Supply Chain Management (SCM) is a strategic technique used by businesses across the globe to improve performance. Both manufacturing and service organizations utilize operational performance as an evaluation metric. Implementing SCM effectively is crucial for firms to achieve their performance and growth objectives.
Learn industry best practices on how to Increase Supply Chain Performance below.
The flow of items, information, and money are the three most important factors of supply chain management. The efficiency and profitability of an enterprise are directly proportional to the quality of management of these resources. To Improve the efficiency and productivity of every step in the supply chain it is important to think about the following factors:
· Strategy
· Planning
· Organization
· Management
· Control Activities
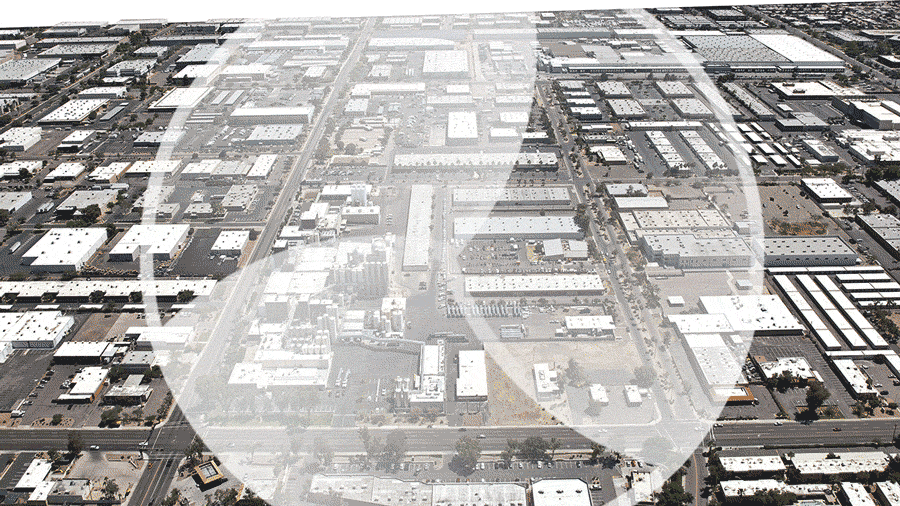
An Example of Simulation-Based Multiechelon Inventory Optimization
Managing the inventory across multiple facilities arrayed in multiple echelons can be a huge challenge for any company. The complexity arises from the interactions among the echelons, with demands at the lower levels bubbling up and any shortages at the higher levels cascading down.
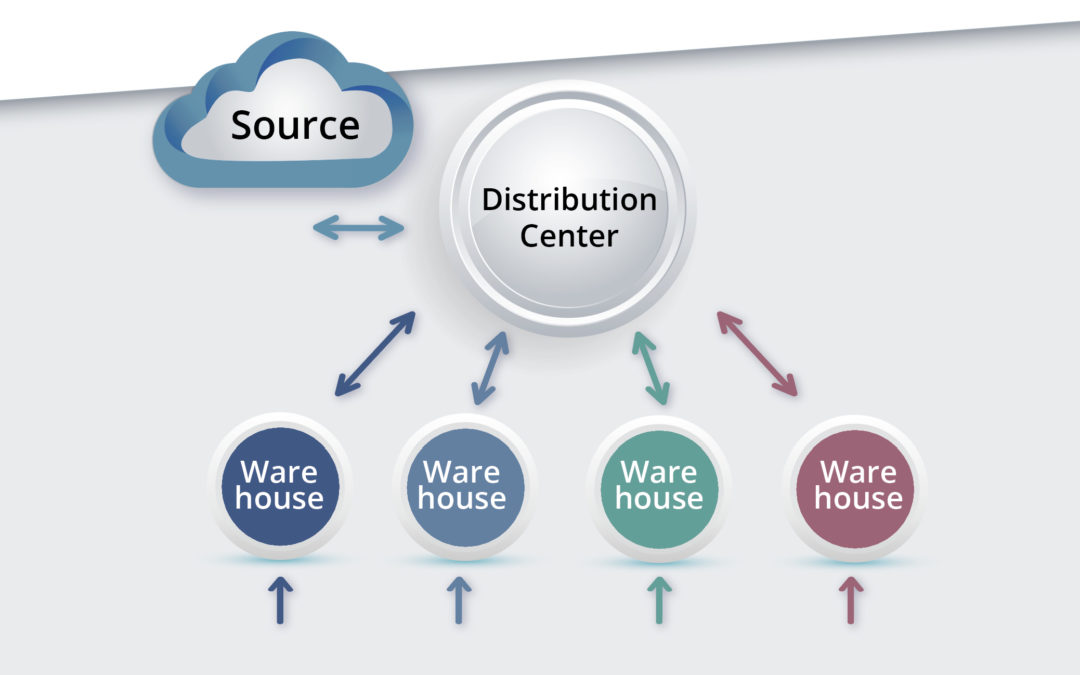
Fact and Fantasy in Multiechelon Inventory Optimization
For most small-to-medium manufacturers and distributors, single-level or single-echelon inventory optimization is at the cutting edge of logistics practice. Multi-echelon inventory optimization (“MEIO”) involves playing the game at an even higher level and is therefore much less common.
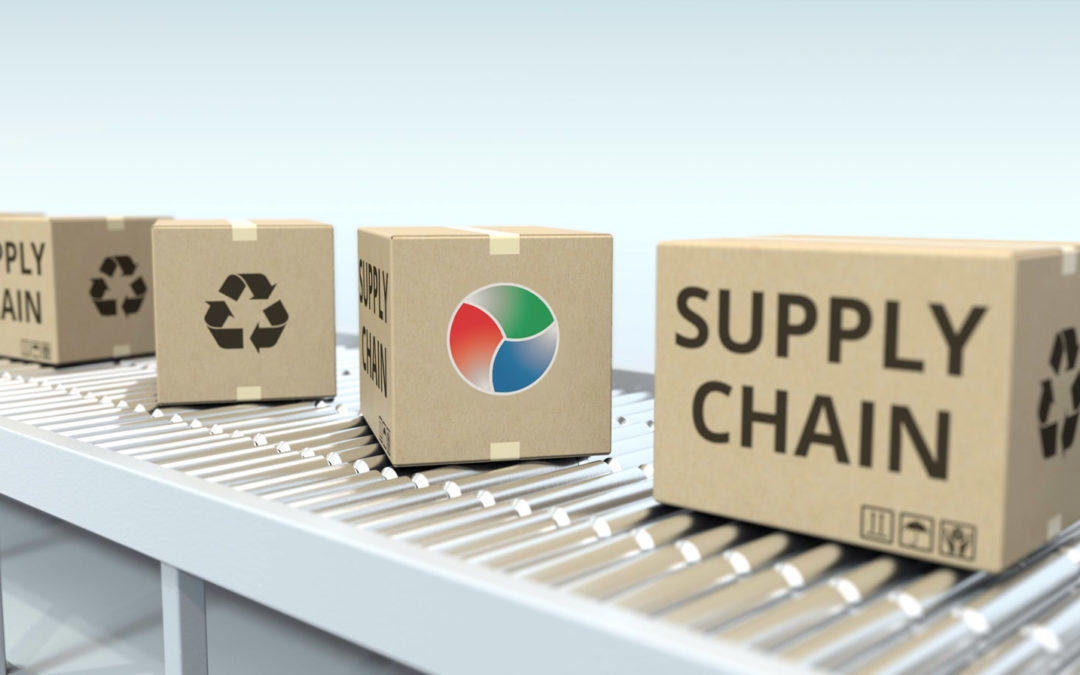
Assessing How Suppliers Influence Your Inventory Costs
Software for inventory optimization is most often used to crank out the analytical results you need to run your day-to-day business, such as Reorder Points (also known as Mins) and Order Quantities. This specialized software helps you find the sweet spot that balances inventory costs against item availability during routine operations.
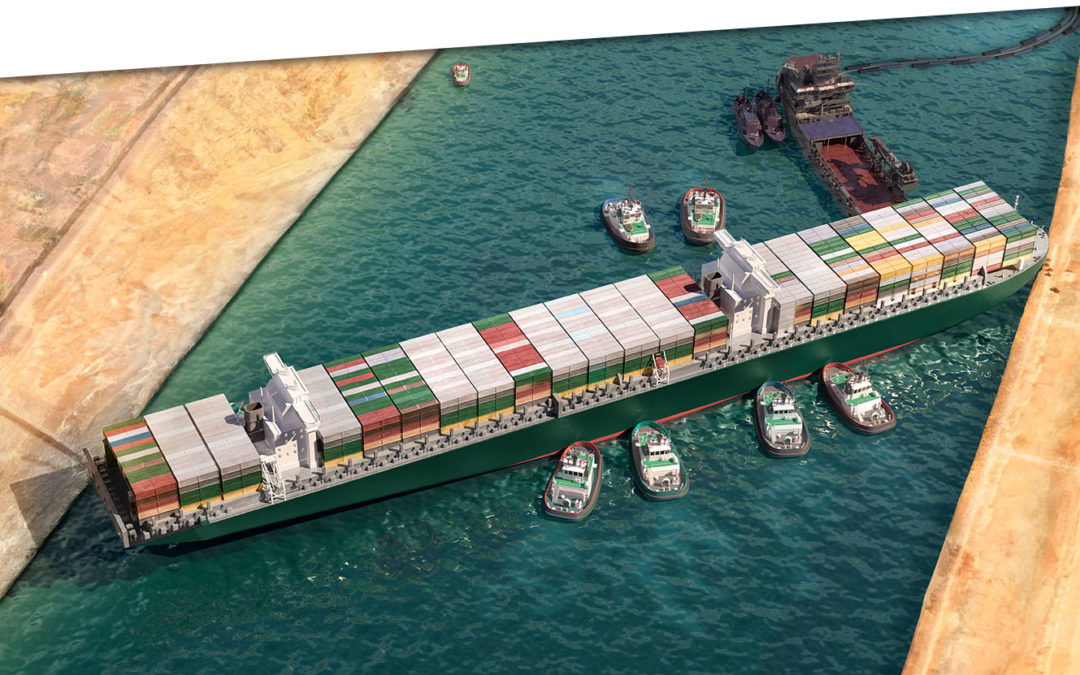
Redefine Exceptions and Fine Tune Planning to Address Uncertainty
In a perfect world, Just in Time (JIT) would be the appropriate solution for inventory management. But as the saying goes “everyone has a plan until they get punched in the mouth.” One enormous punch in the mouth for the global supply chain was Suez Canal Blockage that held up $9.6B in trade costing an estimated $6.7M per minute.
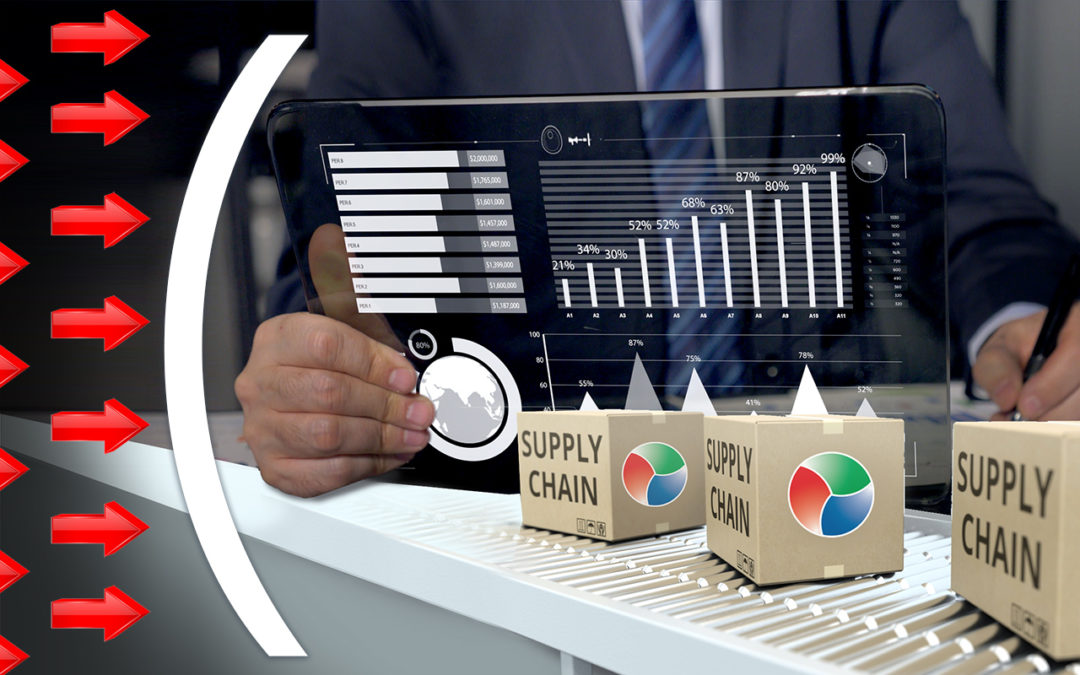
Gaming Out Your Logistical Response to the Corona Virus
This short note is about one way your business can develop a plan to adjust to one of the likely fallouts from the virus: sudden increases in the time it takes to get inventory replenishment from suppliers. Supply chains around the world are being disrupted. If this happens to you, how can you react in a systematic way?
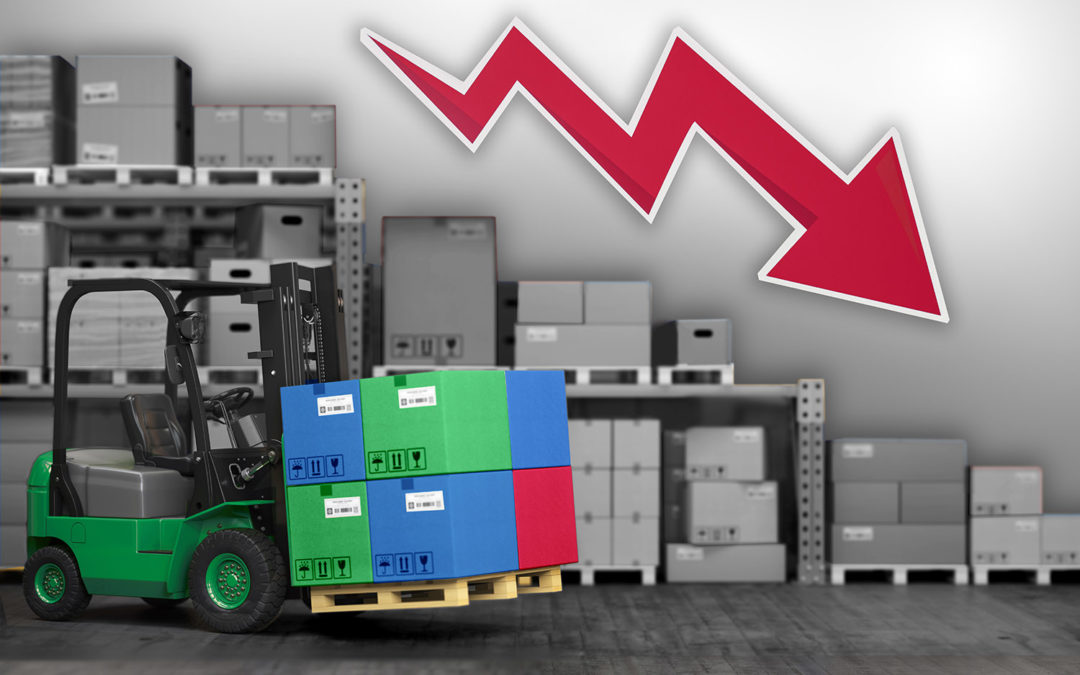
If there is a recession, you should …
Continuously update your inventory control parameters: reorder points, order quantities, safety stocks, mins, maxes, lead times. Beyond that, you should be updating your inventory strategies.
Problem
What is my inventory position today, on any item? Where are we stocking out and how often? What are my delivery times? Why did we ship late? Do we have too much inventory in one location, not enough in another? What are my real supplier lead times? These are obvious, daily questions, and the answers can reveal underlying root causes that when resolved will improve supply chain performance. But these answers are elusive, often because data is locked up in your ERP and only accessible via limited reporting views or spreadsheets. Creating these reports manually using Excel requires data imports, reformatting, and distribution to key stakeholders, wasting countless hours of valuable planning time. This means that getting updated information, when you need it, is not always possible. Not having access to these answers means that problems reveal themselves only after it is too late, and opportunities for improving the inventory planning process are overlooked, further contributing to poor performance.
Solution
Smart Operational Analytics (SOA™) is a native web reporting solution available on Smart’s Inventory Planning and Optimization Platform, Smart IP&O. It provides a fast, easily understood, current perspective on the state of your inventory, its performance against critical metrics, actual supplier lead times, opportunities to rebalance stocks across facilities, and helps you uncover root causes of operational inefficiencies. SOA automatically refreshes as often as you’d like providing all stakeholders immediate, up-to-date reporting on your operations and performance. You’ll have constant visibility of inventory levels, orders, shipments, and supplier performance to ensure you’ll always be in tune with the state of your operations and resolve issues before they become problems. Enhance visibility. Improve responsiveness. Increase your bottom line.
Register to Watch the Demo
Smart Operational Analytics
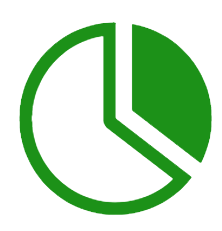
Inventory Analytics
Quantify inventory value
Inventory segmentation
Inventory classification
Trend metrics over time
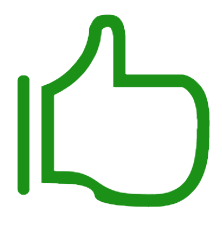
Operational Performance
Measure service level performance
Measure fill rate performance
Calculate turns, holding & ordering costs
Trend metrics over time
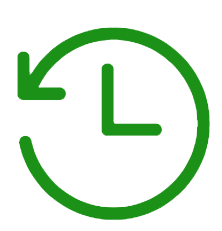
Supplier Insights
Measure supplier performance
Compare supplier lead times
Rank suppliers across available metrics
Trend metrics over time
Who is Operational Analytics for?
Smart Operational Analytics is for executives, planners, and operations professionals who seek to:
- Measure inventory costs and performance in real time.
- Assess and compare Supplier performance.
- Identify root causes of stockouts, excess inventory, and late deliveries.
- share KPI’s such as service levels, turns, costs, and more across the organization.
What questions can Operational Analytics answer?
- What does my inventory look like? By value, count, classification?
- Is my inventory trending up, down, or the same?
- How much of my inventory is overstocked, understocked, or acceptable?
- Can inventory be transferred from overstocked locations to under stocked locations?
- Can existing supplier orders be cancelled or deferred?
- What are my current turns, service levels, and fill rates and how do they trend over time?
- How many out of stock events occurred this week, this month, this quarter?
- How are my suppliers performing, how do they compare?
- What is my supplier lead time and how has it changed over time?
Inventory and supplier reporting for your enterprise
Smart Operational Analytics empowers you to:
- Benchmark service performance and inventory costs.
- Benchmark supplier performance.
- Assess and Classify Inventory by class, stage, and more.
- Share metrics with the organization.