Business policies utilize predictive analytics and regression analysis to manage inventory effectively, avoiding excesses and shortages while optimizing costs and responsiveness. The implementation of these policies involves advanced statistical methods and technologies to enhance accuracy, reduce errors, and adapt to market changes, thereby maintaining operational efficiency and competitiveness.
Check out industry best practices below on how to optimize your inventory to cut costs, meet demand, and streamline your supply chain.
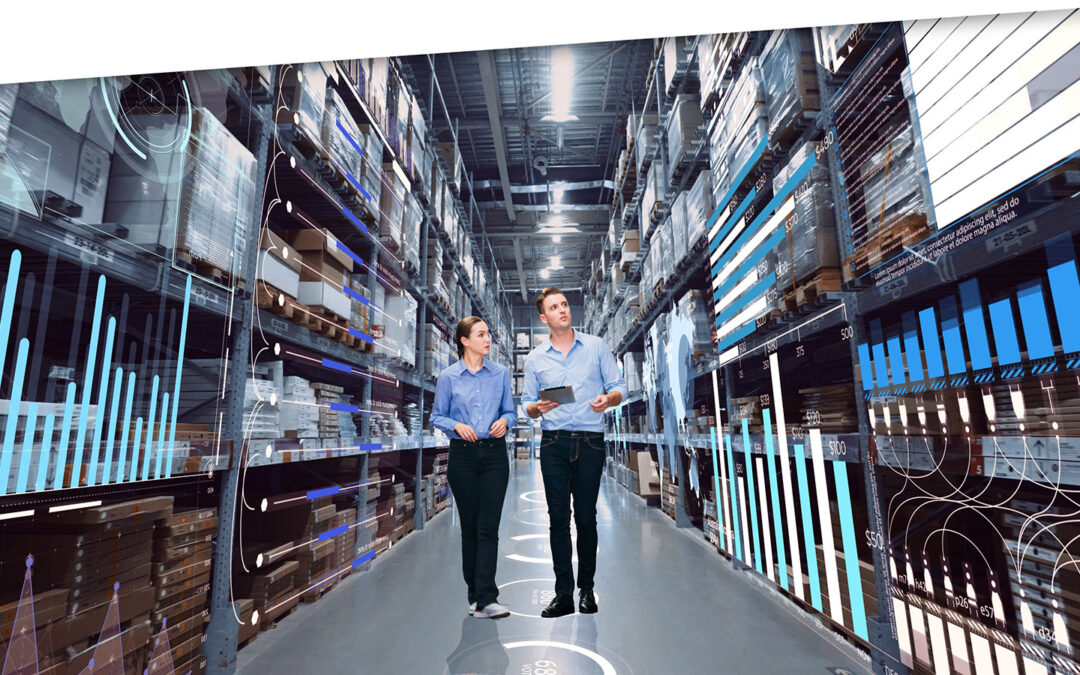
Make AI-Driven Inventory Optimization an Ally for Your Organization
In this blog, we will explore how organizations can achieve exceptional efficiency and accuracy with AI-driven inventory optimization. Traditional inventory management methods often fall short due to their reactive nature and reliance on manual processes. Maintaining optimal inventory levels is fundamental for meeting customer demand while minimizing costs. The introduction of AI-driven inventory optimization can significantly reduce the burden of manual processes, providing relief to supply chain managers from tedious tasks.
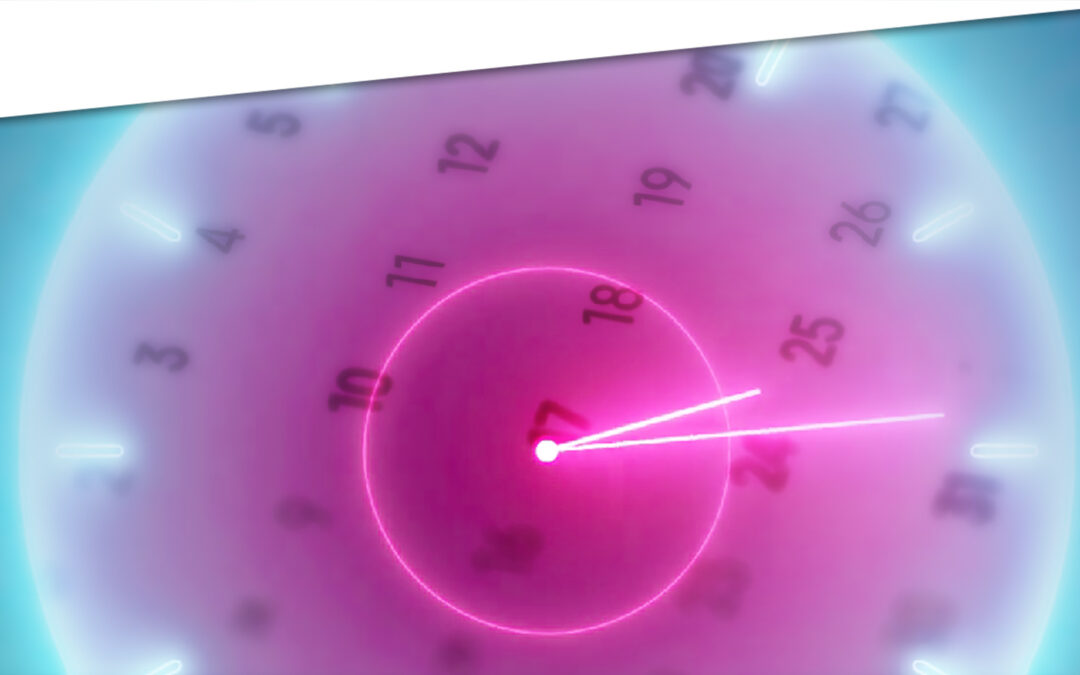
Daily Demand Scenarios
In this Videoblog, we will explain how time series forecasting has emerged as a pivotal tool, particularly at the daily level, which Smart Software has been pioneering since its inception over forty years ago. The evolution of business practices from annual to more refined temporal increments like monthly and now daily data analysis illustrates a significant shift in operational strategies.
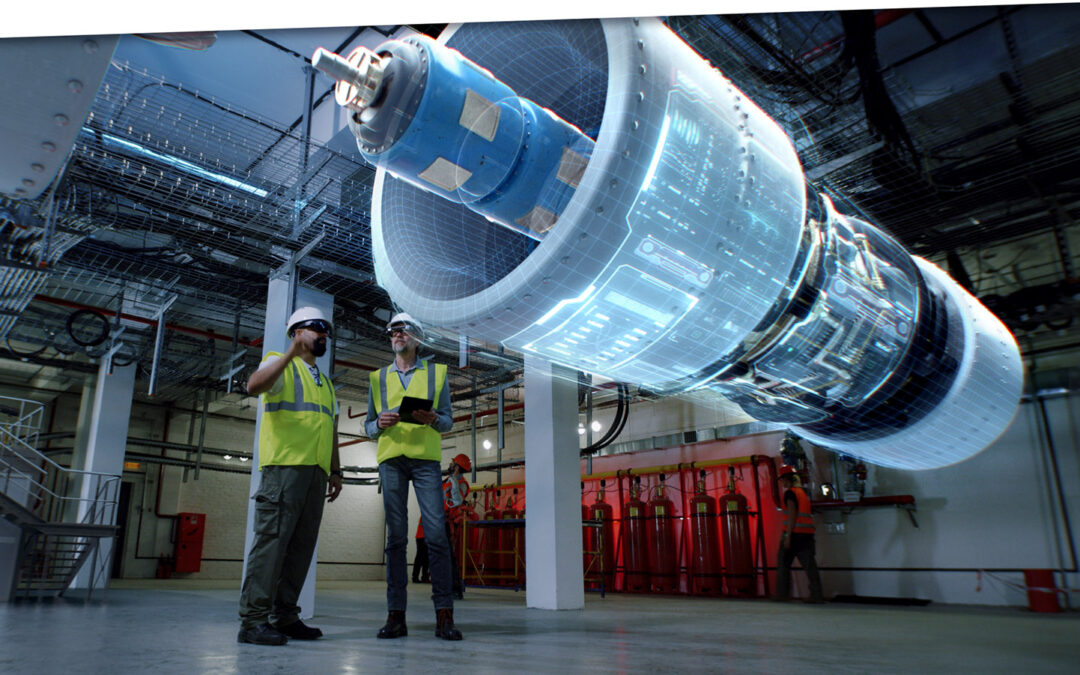
Constructive Play with Digital Twins
Those of you who track hot topics will be familiar with the term “digital twin.” Those who have been too busy with work may want to read on and catch up. While there are several definitions of digital twin, here’s one that works well: A digital twin is a dynamic virtual copy of a physical asset, process, system, or environment that looks like and behaves identically to its real-world counterpart. A digital twin ingests data and replicates processes so you can predict possible performance outcomes and issues that the real-world product might undergo.
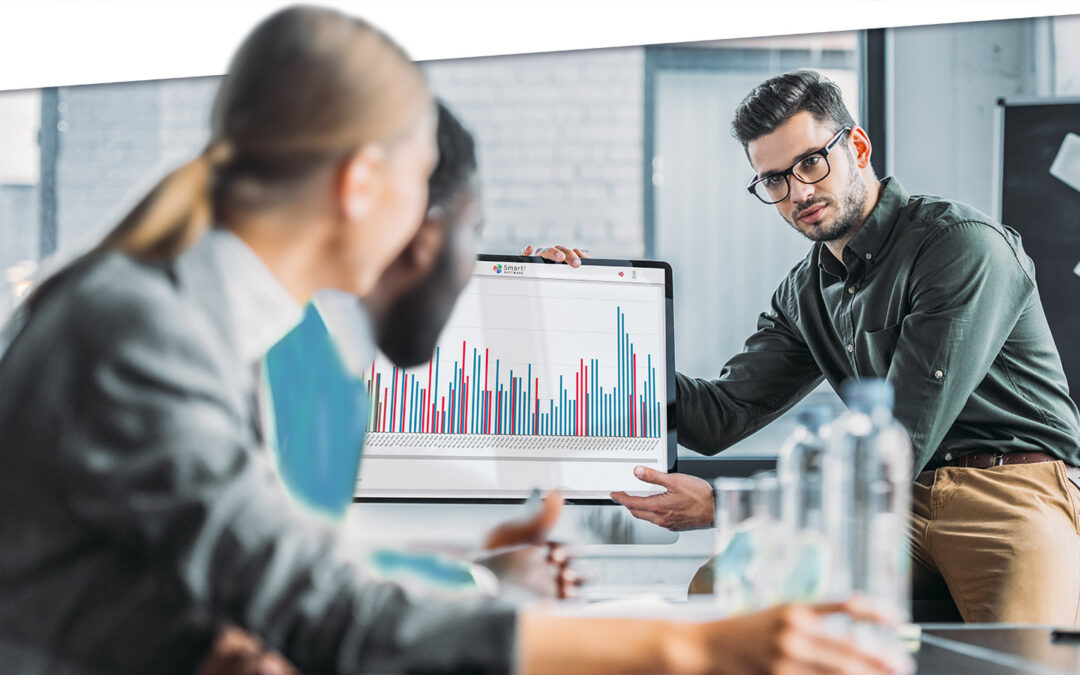
Direct to the Brain of the Boss – Inventory Analytics and Reporting
In this blog, the spotlight is cast on the software that creates reports for management, the silent hero that translates the beauty of furious calculations into actionable reports. Watch as the calculations, intricately guided by planners utilizing our software, seamlessly converge into Smart Operational Analytics (SOA) reports, dividing five key areas: inventory analysis, inventory performance, inventory trending, supplier performance, and demand anomalies.
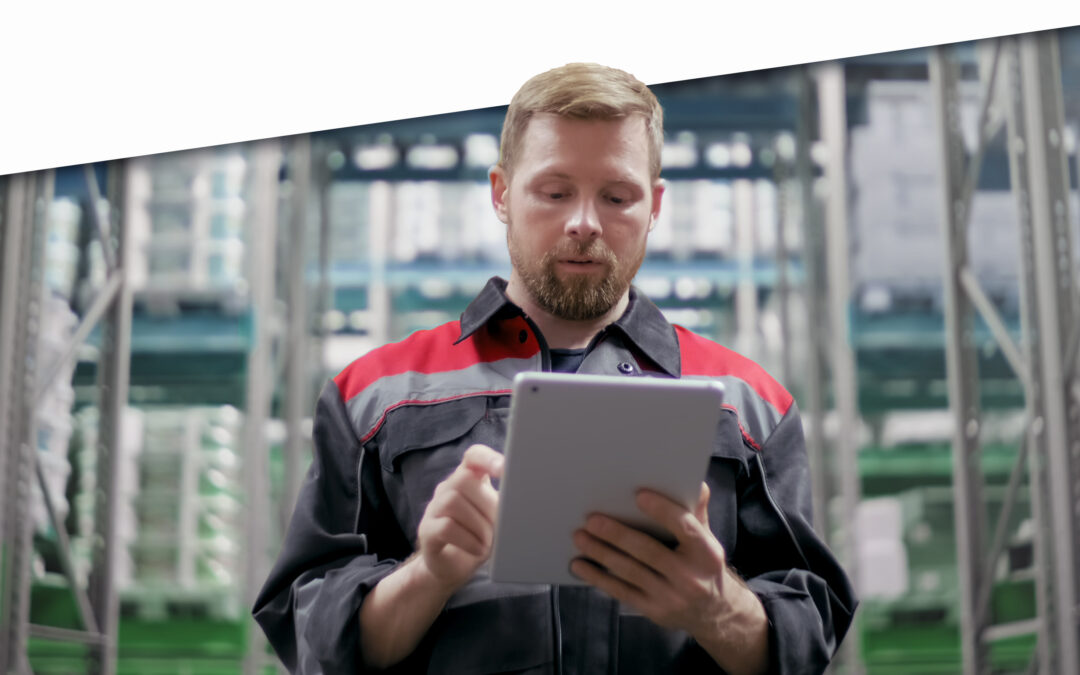
How Are We Doing? KPI’s and KPP’s
Dealing with the day-to-day of inventory management can keep you busy. But you know you have to get your head up now and then to see where you’re heading. For that, your inventory software should show you metrics – and not just one, but a full set of metrics or KPI’s – Key Performance Indicators.
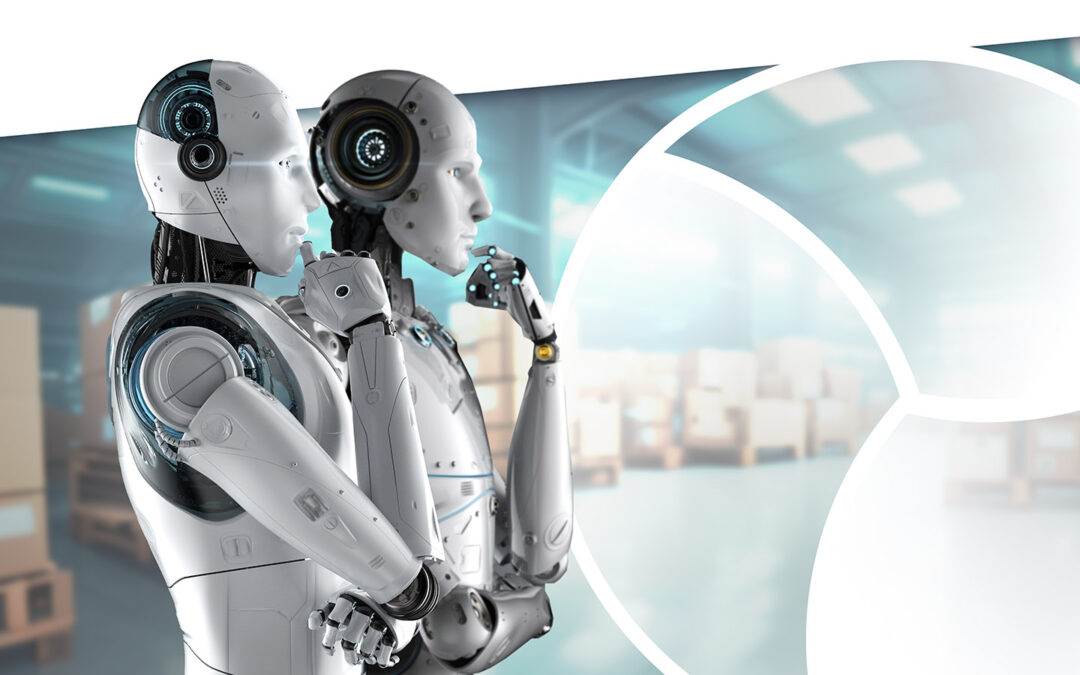
Confused about AI and Machine Learning?
Are you confused about what is AI and what is machine learning? Are you unsure why knowing more will help you with your job in inventory planning? Don’t despair. You’ll be ok, and we’ll show you how some of whatever-it-is can be useful.
Problem
What is my inventory position today, on any item? Where are we stocking out and how often? What are my delivery times? Why did we ship late? Do we have too much inventory in one location, not enough in another? What are my real supplier lead times? These are obvious, daily questions, and the answers can reveal underlying root causes that when resolved will improve supply chain performance. But these answers are elusive, often because data is locked up in your ERP and only accessible via limited reporting views or spreadsheets. Creating these reports manually using Excel requires data imports, reformatting, and distribution to key stakeholders, wasting countless hours of valuable planning time. This means that getting updated information, when you need it, is not always possible. Not having access to these answers means that problems reveal themselves only after it is too late, and opportunities for improving the inventory planning process are overlooked, further contributing to poor performance.
Solution
Smart Operational Analytics (SOA™) is a native web reporting solution available on Smart’s Inventory Planning and Optimization Platform, Smart IP&O. It provides a fast, easily understood, current perspective on the state of your inventory, its performance against critical metrics, actual supplier lead times, opportunities to rebalance stocks across facilities, and helps you uncover root causes of operational inefficiencies. SOA automatically refreshes as often as you’d like providing all stakeholders immediate, up-to-date reporting on your operations and performance. You’ll have constant visibility of inventory levels, orders, shipments, and supplier performance to ensure you’ll always be in tune with the state of your operations and resolve issues before they become problems. Enhance visibility. Improve responsiveness. Increase your bottom line.
Register to Watch the Demo
Smart Operational Analytics
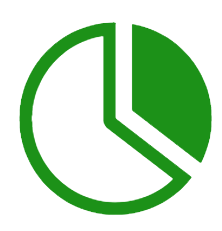
Inventory Analytics
Quantify inventory value
Inventory segmentation
Inventory classification
Trend metrics over time
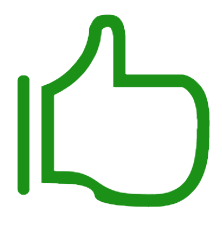
Operational Performance
Measure service level performance
Measure fill rate performance
Calculate turns, holding & ordering costs
Trend metrics over time
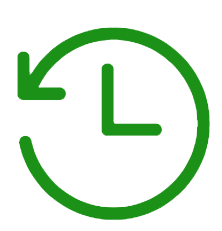
Supplier Insights
Measure supplier performance
Compare supplier lead times
Rank suppliers across available metrics
Trend metrics over time
Who is Operational Analytics for?
Smart Operational Analytics is for executives, planners, and operations professionals who seek to:
- Measure inventory costs and performance in real time.
- Assess and compare Supplier performance.
- Identify root causes of stockouts, excess inventory, and late deliveries.
- share KPI’s such as service levels, turns, costs, and more across the organization.
What questions can Operational Analytics answer?
- What does my inventory look like? By value, count, classification?
- Is my inventory trending up, down, or the same?
- How much of my inventory is overstocked, understocked, or acceptable?
- Can inventory be transferred from overstocked locations to under stocked locations?
- Can existing supplier orders be cancelled or deferred?
- What are my current turns, service levels, and fill rates and how do they trend over time?
- How many out of stock events occurred this week, this month, this quarter?
- How are my suppliers performing, how do they compare?
- What is my supplier lead time and how has it changed over time?
Inventory and supplier reporting for your enterprise
Smart Operational Analytics empowers you to:
- Benchmark service performance and inventory costs.
- Benchmark supplier performance.
- Assess and Classify Inventory by class, stage, and more.
- Share metrics with the organization.