Inventory management has developed its own set of key words and key phrases.
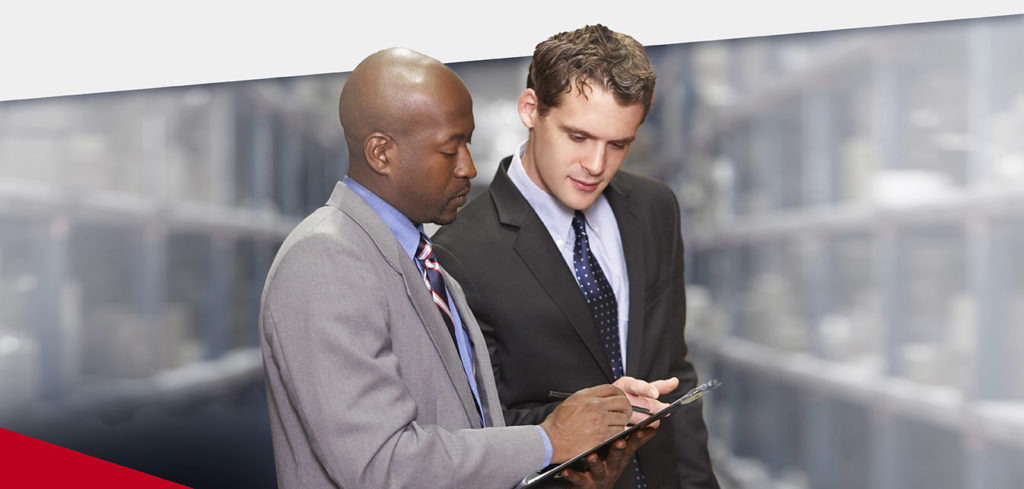
Dictionary
We find that practitioners are not always sure about the meanings of these words, which can impede effective business communication, particularly when implementing inventory optimization and forecasting software. Sometimes two companies (supplier and customer, supply chain software vendor and customer, etc.) use the same word but apply different meanings to it. This post aims to clarify some basic definitions.
Inventory optimization and forecasting Dictionary
Backorder Policy
A prescription of what to do when there is a stockout. Under a backorder policy, any units demanded but not provided immediately are provided later, when available.
Fill Rate
An item availability metric that measures the fraction of items demanded that are supplied immediate from stock on hand. Expressed as a percentage: A 90% fill rate means that 90% of the units demanded, on average, are immediately available. Fill rate differs from service level in that it takes account of how large a stockout is, not just how often a stockout happens. Accordingly, fill rate and service level can be very different numbers. What’s the difference between fill rate and service level?
Lead Time
Lead time is the interval between inventory realizing that you need more stock, i.e., detecting that inventory has dropped to or below the reorder point or min, and its arrival back in stock. The lead time might be composed of several intervals: the time to sense the problem, the time to request purchasing to get more, the time until purchasing actually cuts a purchase order, the time for the vendor to deliver, and then the time to restock. The shorter the lead time, the more lean and agile your operation. You can use SmartForecasts to do “what if” analysis, examining the gains to be made from reducing lead times.
Min level of inventory
The level of inventory which, when reached or breached, triggers replenishment. Identical to the reorder point R. The Min is comprised of the cycle stock (expected lead time demand) and safety stock (to protect against demand and supply variability).
Order Quantity
A fixed number of units to order when the reorder point has been reached or breached
Order Quantity Minimum
Order quantities are often negotiated with suppliers rather than simply calculated from an item’s demand history. Some suppliers require that any order be at least of a certain size. If you would like to order 7 but your supplier has an order quantity minimum of 10, you are stuck ordering 10.
Rule of Thumb
A way to determine inventory requirements based on an easy-to-understand rule such as “order 10 days’ worth of supply every time inventory falls to 5 days of supply.”
Safety Time
The amount of days added to the lead time to accommodate for increases in supplier lead time. By increasing safety time, orders will be triggered sooner thereby minimizing the risk of stockouts.
Cycle Stock
The portion of inventory that is expected to cover the lead time demand. In an inventory control system, the reorder point is comprised of the cycle stock and the safety stock. The more safety stock, the lower the risk of stocking out.
Inventory Forecasting
An inventory management process that predicts future inventory levels, costs, and service level performance.
Lead Time Demand
Lead time demand is a random quantity totaling all the demands that arrive during the lead time. SmartForecasts’ key analytical computation is estimation of the probability distribution of lead time demand. From this flow assessments of service level, fill rate, and reorder point (min).
Loss Policy
A prescription of what to do when there is a stockout. Under a loss policy, any units demanded but not provided immediately are considered lost: either the customer gets those units elsewhere or just doesn’t get them at all.
Make/Procure to Order
An item is produced or ordered from a supplier when ordered by the customer. Inventory is not automatically replenished with Make to Order items.
Max level of inventory
The “order-up-to” level in min/max systems. The actual order quantity is random in the min/max system: How much is ordered depends on the current gap between available inventory and the max.
Order Quantity Multiple
As with order quantities, order multiples are often imposed by suppliers, who may insist that order quantities be an even multiple of some basic unit. For instance, if a supplier only provides six packs, you cannot order either 5 or 7 units; instead, you must order 6 or 12
Order Up to Policy
Represents a replenishment policy driven by the Order Up to Level and a fixed replenishment frequency. For example, every two weeks (the replenishment frequency)
Safety Stock
The amount of inventory added to the average lead time demand to accommodate random increases in demand, thereby minimizing the risk of stockouts, with their attendant lost sales or backorders. The safety stock is strongly influenced by the volatility of demand. In an inventory system, a replenishment order is triggered when the supply of inventory is forecasted to hit the safety stock level. The order is placed at the Reorder Point.
Economic Order Quantity (EOQ)
A classic but not always useful estimate of the “best” order quantity. The EOQ takes account of three factors: the average level of demand, the cost of holding inventory, and the cost of making a replenishment order. SmartForecasts provides alternative order quantity recommendations based on additional factors: the long-run stability of the system (i.e., you have to order at least enough to keep your head above water) and any supplier-imposed order minimums and multiples.
Inventory Optimization
An inventory management process that yields an inventory with the lowest possible cost and maximum possible service. Inventory Forecasting methods that employ traditional rule of thumb policy or service level targeting are not sufficient to optimize inventory since the choice of service level is arbitrary and will not yield the maximum overall service for the lowest total cost.
Lot for Lot Policy
Otherwise known as “sell one, buy one.” Represents a replenishment policy driven by a reorder point or min and a replenishment quantity that is equal to what was consumed. The replenishment frequency parallels the demand frequency as an order is placed to replenish each time inventory is consumed.
Min/Max Inventory Policy
Represents a replenishment policy driven by the Min and the Max. When supply breaches the Min, an order is placed up to the Max. With Min/Max policy, the order quantity will vary depending on the gap between supply and max
Q,R or R,Q Policy
Represents a replenishment policy driven by the reorder point (R) and the reorder quantity (Q). With a Q,R policy, the replenishment quantity is always the same.
Reorder Point
The level of inventory which, when reached or breached, triggers replenishment. Also the same as the min in min/max systems. Example: If reorder point is 7, any inventory level from 7 on down will trigger a replenishment order. The Reorder Point or ROP is comprised of the the cycle stock and safety stock.
Service Level
An item availability metric that measures the ability to avoid stocking out during a replenishment lead time. Expressed as a percentage: A 90% service level implies a 10% chance of stockout. What’s the difference between fill rate and service level? In inventory forecasting, safety stock and reorder point levels can be planned with a user defined service level target.
Article Archives
Smart Software is excited to announce that we are joining Epicor, a global leader of industry-specific enterprise software. The acquisition brings together two companies tightly aligned in helping organizations get to the right insights at the right time and take action to maximize business performance.
In joining Epicor, Smart Software customers will benefit from significant scale, development, and investment in our inventory planning and optimization solutions, over time giving you even more capabilities and product options. In acquiring Smart Software, Epicor is complementing and strengthening its portfolio of best-in-class ERP solutions, helping makers, movers, and sellers worldwide streamline and simplify their supply chains to gain a competitive advantage. As your strategic business partner, our top priority as we integrate the organizations in the coming months is to continue to provide you with the highest level of service and support you expect.
For more information on the news, please visit the Epicor Newsroom
Smart Software is pleased to announce the award of US Patent 11,656,887. “System And Method to Simulate Demand and Optimize Control Parameters for a Technology Platform.”
The patent directs “technical solutions for analyzing historical demand data of resources in a technology platform to facilitate management of an automated process in the platform.” One important application is optimization of parts inventories.
Smart Software named a Microsoft Co-sell-ready partner as a leading demand planning and inventory optimization solutions provider. Microsoft customers leverage Smart’s web-native platform for Inventory Planning and Optimization (Smart IP&O) to develop consensus forecasts, manage demand, and optimize stocking policies.
We are so grateful to announce Smart Software’s 40th anniversary. Forty years of Innovation for Demand Forecasting, Inventory Planning, and Supply Chain Analytics. Smart, Hartunian, and Willemain was incorporated in June 1981 by Charles Smart, Thomas Willemain, and Nelson Hartunian, our visionary founders.
Supply and Demand Chain Executive 2020 Online Magazine features an article about inventory optimization at BC Transit, entitled “Optimizing Parts Management at BC Transit.” Eric Nelson, Director for Supply Services at BC Transit explains how Smart IP&O has helped ensure that they have the right part in the right place at the right time to equip their entire service network with 35 repair locations.
Don’t Be a Victim of your Forecast Models – Special Section in Foresight Magazine. In this feature section, Tom Willemain provokes a good deal of thought about the role of statistical models in supply chain forecasting, a field that he believes lags far behind finance in embracing algorithms over gut instinct. Download Special Section on Forecast Modeling in Spring 2019 Issue of Foresight Magazine
Right-Sizing Inventory with Demand Forecasting,” interview with Chief Material Officer at Metro-North Railroad.
Supply & Demand Chain Executive — June 26
See “Four Steps to Service Level-Driven Inventory Planning” in SupplyChain Management Review.
SupplyChain Management Review — April 12, 2015
Minnesota’s Metro Transit adopts service-level driven method of inventory planning from Smart Software.
Mass Transit Magazine — February 2015
Video Interview with SupplyChainBrain, “Service Level-Driven Demand Planning”
SupplyChainBrain — June 30, 2014
Conquering Supply Chain Variability at Rev-A-Shelf,” in Supply & Demand Chain Executive Online
Supply & Demand Chain Executive — April 9, 2014
Now You See It, Now You Don’t Inventory,” New technologies to address intermittent demand, in Aviation Week Online
Aviation Week — April 7, 2014
Webinar Replay: Agile Demand Forecasting, the Rev-A-Shelf Experience.
SmartSoftware Inc. — January 2014
Feature Article: MCI’s Parts Planning Excels with Smart Software” in BusRide Maintenance Magazine
BusRide Maintenance Magazine — September 2013
Webinar replay: CFO View of Demand Forecasting, with Bud Schultz, NKK Switches. Originally broadcast 9/26/2013.
SmartSoftware Inc. — September 2013
Featured Review: “Smart Software for Service-level Driven Forecasting” by Technology Evaluation Centers.
Technology Evaluation Centers — May 2013
Feature Article: “Forecasting – It’s More than Inventory Management,” in Supply & Demand Chain Executive.
Supply & Demand Chain Executive — February 2013
Feature Article: “Small Operational Changes Bring Big Cost-Cutting Results for Transit Agencies” in APTA Passenger Transport Magazine
APTA Passenger Transport Magazine — June 2012
Feature Article: “Meeting the Service Parts Inventory Planning Challenge” in BUSride Maintenance Magazine
BUSride Maintenance Magazine — April 2012
SmartForecasts Review: “Smarter Inventory Management: Forecasting public transportation needs with the complete software package” in APICS Magazine
APICS magazine — January/February 2012
Transit Talk Blog: “How to Discover Hidden Cost Savings in Your Transit Operations”
Mass Transit Magazine — September, 2011
Cover Story: A Northeast Commuter Railroad Struggles to Optimize Its Spare Parts Inventory
SupplyChainBrain — May/June 2011
“Prestolite Charges up Its Inventory Management”
When retirements drained its planning expertise and a bad mix of too much inventory put a strain on cash flow, the company brought in a new forecasting tool to power its planning process. S&DCE Aug/Sep 2010
“How to Survive the Economic Crunch”
Current economic conditions are challenging everyone’s business. This is especially true for companies in the manufacturing and distribution sectors that have a large percentage of their supply chain resources tied up in inventory. With credit tight, these companies are looking for ways to preserve as much cash as possible. Because inventory is cash sitting on the shelves, a prime way to reduce costs and increase cash flows is to improve the forecasting and planning of inventory requirements. SDCExec.com May 2009
“Smooth Ride: Forecasting solution improves product deployment and reduces transportation costs”
See how Prevost Parts, a division of Canadian bus manufacturer Prevost Car, has used SmartForecasts to improve inventory allocation and distribution effectiveness in the North American aftermarket for its 25,000 motorcoach and urban bus parts. Learn about Prevost Parts’ evaluation criteria in selecting SmartForecasts over five other applications considered, and the importance of Smart’s unique intermittent demand forecasting capability in solving Prevost’s forecasting and safety stock estimation problems. APICS May 2005
“Prevost Parts increases replacement part availability and reduces inventory through improved demand forecasting” by Alex Daudelin.
Read an article about how Prevost Parts, the parts division of Canadian bus manufacturer Prevost Car, uses SmartForecasts to more effectively distribute replacement parts for the North American motorcoach and transit bus markets. Learn why the company selected SmartForecasts over SAP’s demand planning application and now expects both a 25% increase in forecast accuracy and close to a 20% reduction in inventory stocking levels. Geston Logistique March 2004
“The Right Tools” by Charles Smart, president of Smart Software.
Learn how the right statistical forecasting tools combined with collaborative inputs from management, salespeople and customers can greatly improve forecast accuracy and streamline a company’s demand planning process. APICS May 2003
“Forecasting-As Important as Ever” by Charles Smart, president of Smart Software.
Read why demand forecasting is still essential in this new manufacturing age. APICS Nov/Dec 2001
“A better crystal ball” by Charles Smart, president of Smart Software.
Read a Web-exclusive article about how forecasting applications are adapting to shorter product life cycles and build-to-order trends. manufacturingsystems.com Nov 2001
“Bootstrap Your Way to Better Forecasts” by Charles Smart, president of Smart Software.
Learn about Smart Software’s new forecasting method to address the multi-million dollar problem of planning intermittent, slow-moving demand. Midrange Enterprise Jan 2001
Contact Us Today for More Information
If you request a demo, one of our specialists will show you how Smart can help, using your own inventory data!