Inventory Planning from the Perspective of a Physicist
In a perfect world, Just in Time (JIT) would be the appropriate solution for inventory management. If you can exactly predict what you need and where you need it and your suppliers can get what you need without delay, then you do not need to maintain much inventory locally. But as the saying goes from famous pugilist Mike Tyson, “everyone has a plan until they get punched in the mouth.” And the latest punch in the mouth for the global supply chain was last week’s Suez Canal Blockage that held up $9.6B in trade costing an estimated $6.7M per minute[1]. Disruptions from these and similar events should be modeled and accounted for in your planning.
The assumption that you can exactly predict the future was apparent in Isaac Newton’s laws. Since the 1920’s with the introduction of quantum physics, uncertainty became fundamental to our understanding of nature. Uncertainty is built into fundamental reality. So too should it be built into Supply and Demand Planning processes. Yet too often, black swan events such as the Suez Canal blockage are often thought of as anomalies and as a result, discounted when planning. It is not enough to look back in hindsight and proclaim that it should have been expected. Something needs to be done about addressing the occurrence of other such events in the future and planning stocking levels accordingly.
We must move beyond the “thin tailed distribution” thinking where extreme outcomes are discounted and plan for “fat tails.” So how do we execute a real-world JIT plan when it comes to planning inventory? To do this, the first step is to estimate the realistic lead time to obtain an item. However, estimation is difficult due to lead time uncertainty. Using actual supplier lead times in your company database and external data, you can develop a distribution of possible future lead times and demands within those lead times. Probabilistic forecasting will allow you to account for disruptions and unusual events by not limiting your estimates to what has been observed solely on your own short-term demand and lead time data. You’ll be able to generate possible outcomes with associated probabilities for each occurrence.
Once you have an estimate of the lead time and demand distribution, you can then specify the service level you need to have for that part. Using solutions such as Smart Inventory Optimization (SIO), you will be able confidently stock based on the targeted stock-out risk with minimal inventory carrying cost. You may also consider letting the solution prescribe optimal service level targets by assessing the costs of additional inventory vs. cost of stockout.
Finally, as I have already noted, we need to accept that we can never eliminate all uncertainty. As a physicist, I have always been intrigued by the fact that, even at the most basic levels of reality as we understand it today, there is still uncertainty. Albert Einstein believed in certainty (determinism) in physical law. If he were an inventory manager, he might have argued for JIT because he believed physical laws should allow perfect predictability. He famously said, “God does not play with dice.” Or could it be possible that the universe we exist in was a “black swan” event in a prior “multi-verse” that produced a particular kind of universe that allowed us to exist.
In inventory planning, as in science, we cannot escape the reality of uncertainty and the impact of unusual events. We must plan accordingly.
[1] https://www.bbc.com/news/business-56559073#:~:text=Looking%20at%20the%20bigger%20picture,0.2%20to%200.4%20percentage%20points.
Related Posts
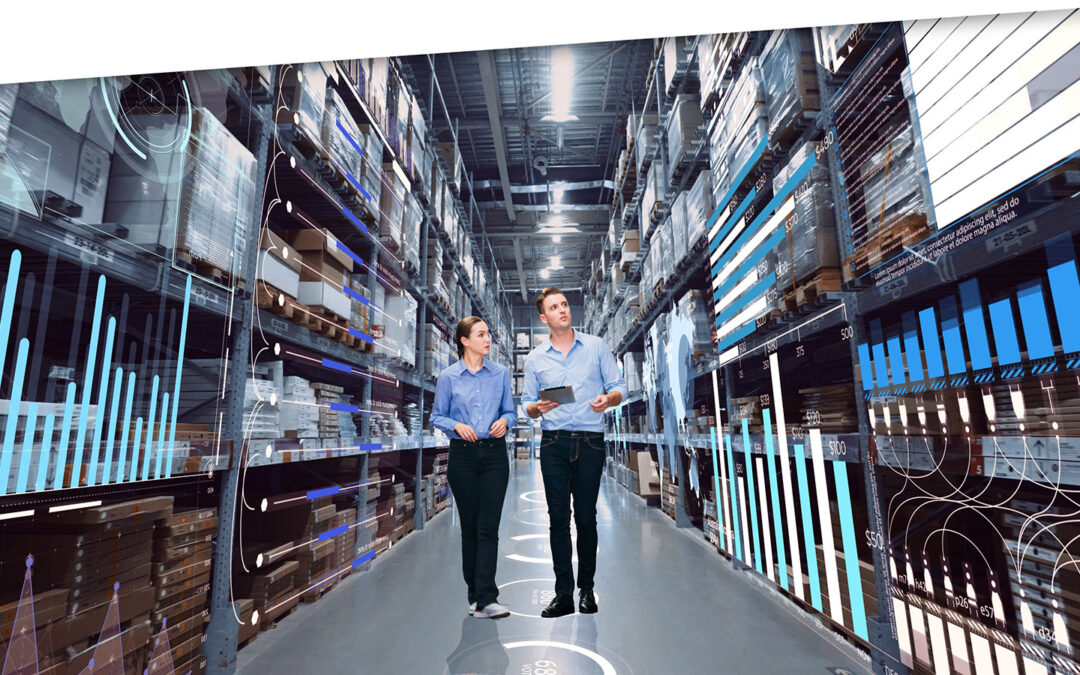
Make AI-Driven Inventory Optimization an Ally for Your Organization
In this blog, we will explore how organizations can achieve exceptional efficiency and accuracy with AI-driven inventory optimization. Traditional inventory management methods often fall short due to their reactive nature and reliance on manual processes. Maintaining optimal inventory levels is fundamental for meeting customer demand while minimizing costs. The introduction of AI-driven inventory optimization can significantly reduce the burden of manual processes, providing relief to supply chain managers from tedious tasks.
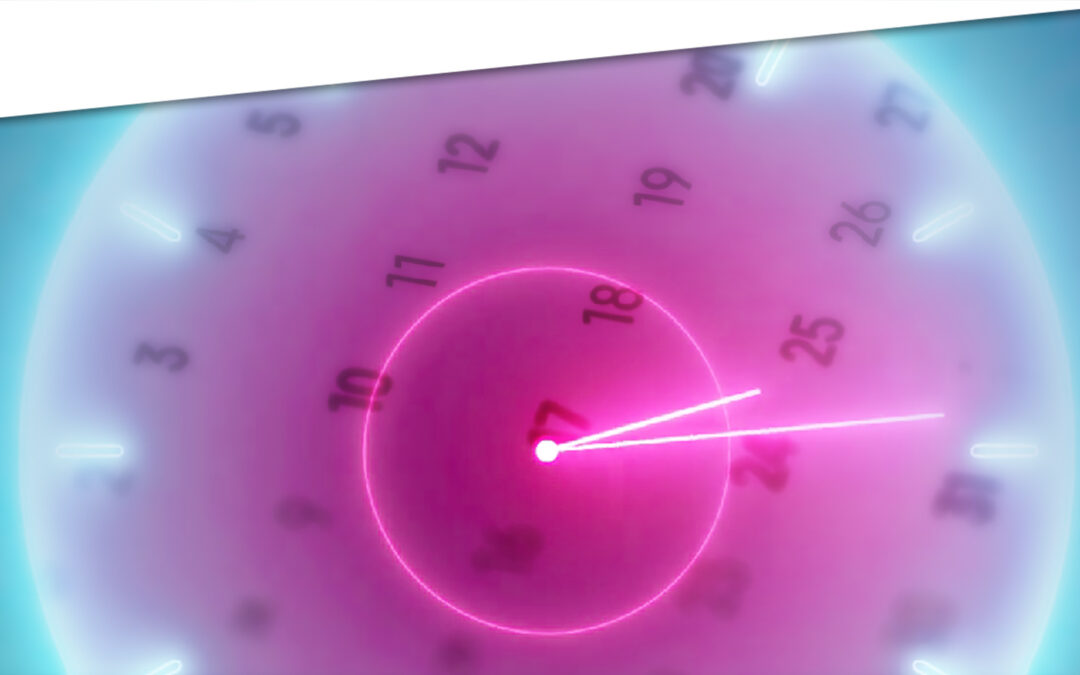
Daily Demand Scenarios
In this Videoblog, we will explain how time series forecasting has emerged as a pivotal tool, particularly at the daily level, which Smart Software has been pioneering since its inception over forty years ago. The evolution of business practices from annual to more refined temporal increments like monthly and now daily data analysis illustrates a significant shift in operational strategies.
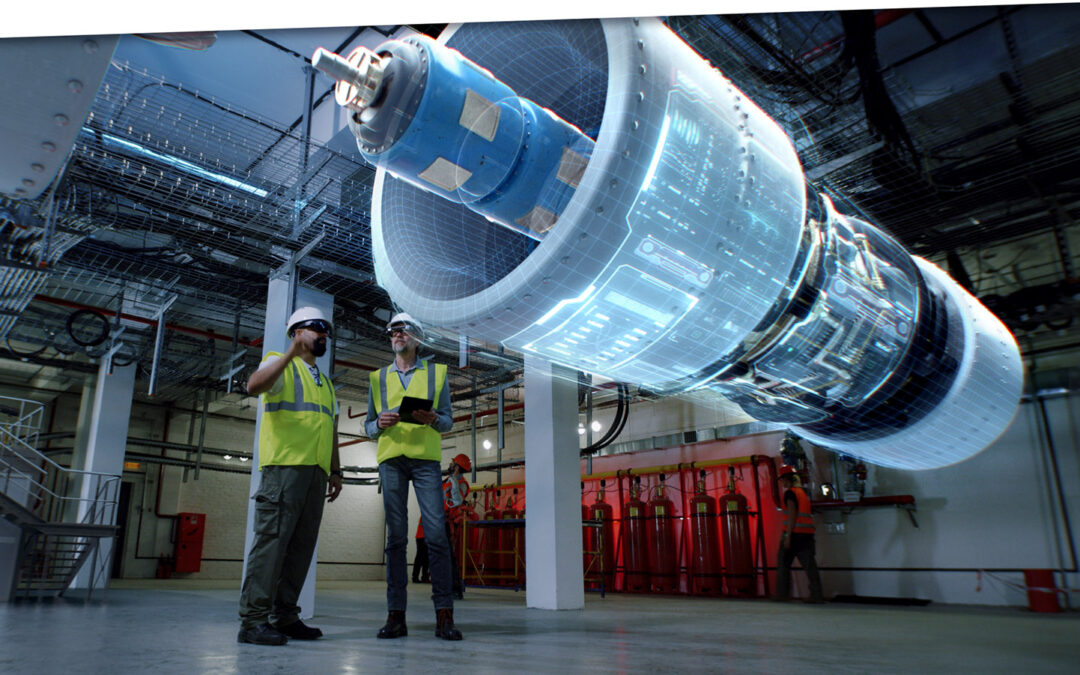
Constructive Play with Digital Twins
Those of you who track hot topics will be familiar with the term “digital twin.” Those who have been too busy with work may want to read on and catch up. While there are several definitions of digital twin, here’s one that works well: A digital twin is a dynamic virtual copy of a physical asset, process, system, or environment that looks like and behaves identically to its real-world counterpart. A digital twin ingests data and replicates processes so you can predict possible performance outcomes and issues that the real-world product might undergo.