Stop buying everything, from paper clips to software? No. You should get a little bit smart about how you are going to ride it out.
Even in normal times, good inventory hygiene suggests that you continuously update your inventory control parameters: reorder points, order quantities, safety stocks, mins, maxes, lead times. Beyond that, you should be updating your inventory strategies, such as adjusting the target service levels or fill rates for every item you hold. That’s the “should.”
But in normal times, it’s easy enough to let those adjustments slide and focus on other things. Then, when the first whiff of recession is in the air, you might get panicky and jump into action in a way that makes it harder to survive the down times. You may look decisive by essentially freezing in place or even shutting some things down, but you risk looking decisive now and foolish later.
Better to take stock of your entire current inventory operation and do that tuning before things get really bad. It is common enough for inventory parameters like reorder points to be set at their current levels by somebody long gone at some time in the distant past for some reason that nobody remembers. Over time, conditions change but the system fails to adapt. So the start of a possible recession is an apt time to run your inventory optimization software to tune up your operations.
You may find that you can remove enough sludge in your current system to offset some or all of the bad news. For instance, your suppliers might be filling orders faster than your software thinks, so you can reduce inventories without risking more stockouts by recalculating reorder points. If you feel you must reduce stocks and ask your customers to accept lower fill rates, you should use your inventory optimization software to identify the best items to put on the chopping block, rather than, say, adjusting every item’s fill rate down by 5%. If you have thousands or tens of thousands of inventory items, that kind of laser-focused adjustment may not be humanly possible without good software support. But with good software support, it’s doable and useful.
Before you hit the panic button, be sure to squeeze all the inefficiency out of your current operations. If, as is common, you have good software but your people are using only a fraction of its capabilities, fix that and get more out of the investment. If you don’t have modern inventory optimization, make a counter-cyclical decision and get some.
If you want to read more about demand planning, forecasting and find new business opportunities in economic recession, read this Journal of Business Forecasting article from the Institute of Business Forecasting (IBF) here or keep reading our new articles
Related Posts
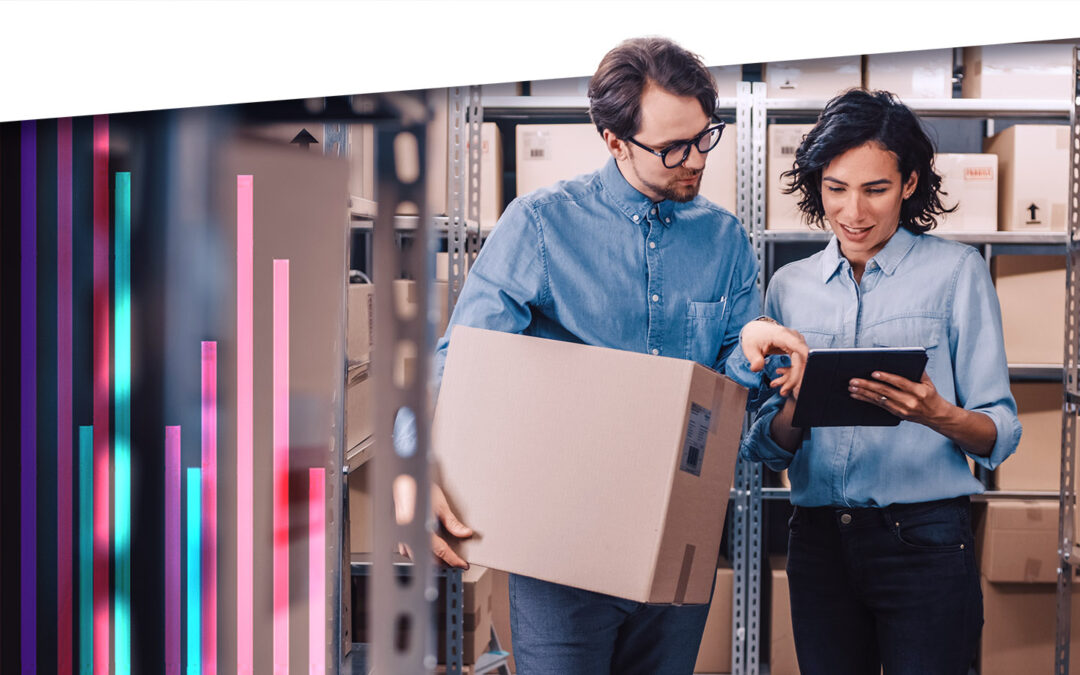
Forecast-Based Inventory Management for Better Planning
Forecast-based inventory management, or MRP (Material Requirements Planning) logic, is a forward-planning method that helps businesses meet demand without overstocking or understocking. By anticipating demand and adjusting inventory levels, it maintains a balance between meeting customer needs and minimizing excess inventory costs. This approach optimizes operations, reduces waste, and enhances customer satisfaction.
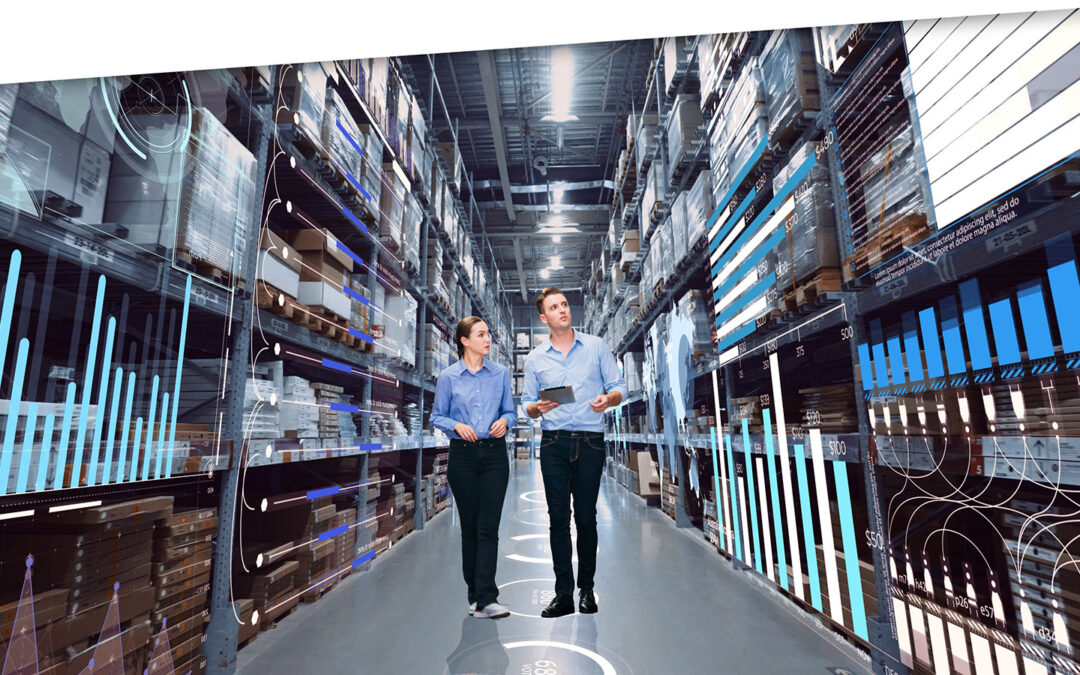
Make AI-Driven Inventory Optimization an Ally for Your Organization
In this blog, we will explore how organizations can achieve exceptional efficiency and accuracy with AI-driven inventory optimization. Traditional inventory management methods often fall short due to their reactive nature and reliance on manual processes. Maintaining optimal inventory levels is fundamental for meeting customer demand while minimizing costs. The introduction of AI-driven inventory optimization can significantly reduce the burden of manual processes, providing relief to supply chain managers from tedious tasks.
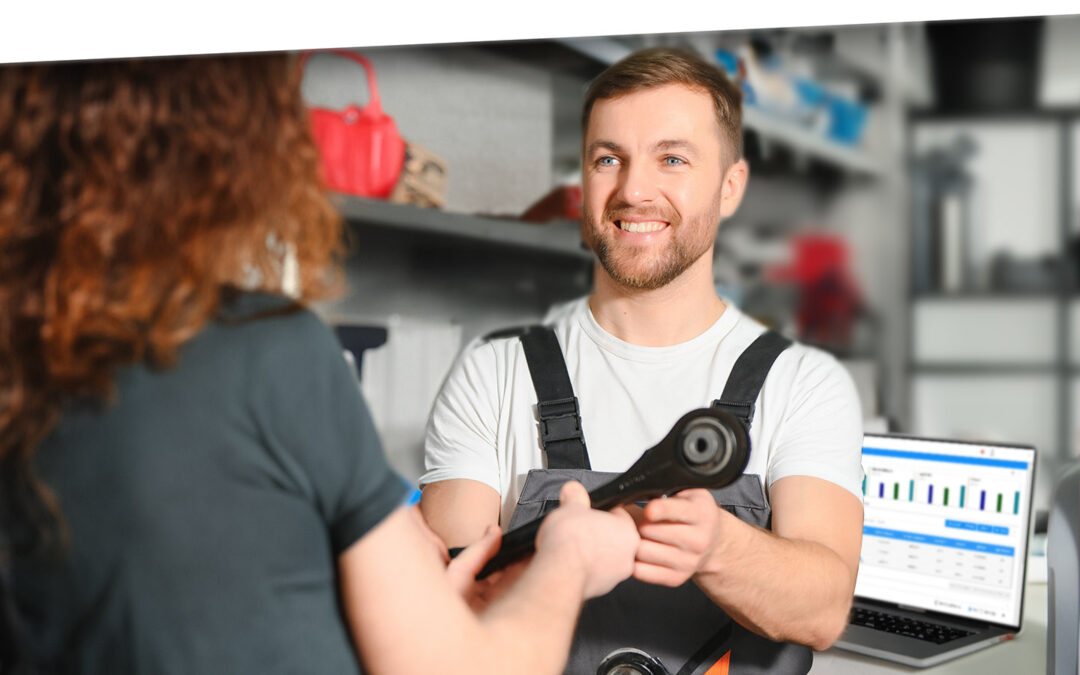
The Importance of Clear Service Level Definitions in Inventory Management
Inventory optimization software that supports what-if analysis will expose the tradeoff of stockouts vs. excess costs of varying service level targets. But first it is important to identify how “service levels” is interpreted, measured, and reported. This will avoid miscommunication and the false sense of security that can develop when less stringent definitions are used. Clearly defining how service level is calculated puts all stakeholders on the same page. This facilitates better decision-making.