Inventory managers have the problem of handling tens or even hundreds of thousands of products, each with unique properties, demanding sophisticated and time-consuming calculations. The proactive management of big inventories becomes unfeasible in the absence of a systematic approach and effective analytic tools.
Without inventory optimization, businesses run the risk of overpaying and underperforming. Manufacturers, distributors, and MRO inventory managers frequently err on the side of caution when setting stocking levels to prevent expensive shortages. Establishing the ideal stock levels for manufacturers, distributors, and MRO should be a science, not an art.
Learn industry best practices on how to optimize inventory to save on costs, meet demand, and streamline your supply chain below.
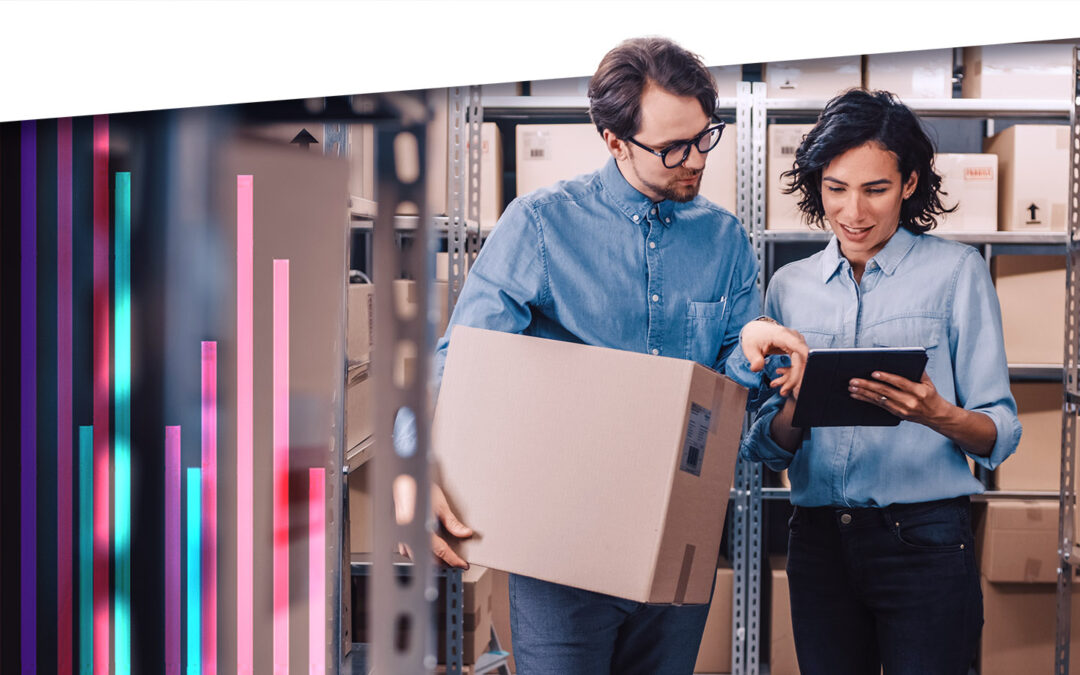
Forecast-Based Inventory Management for Better Planning
Forecast-based inventory management, or MRP (Material Requirements Planning) logic, is a forward-planning method that helps businesses meet demand without overstocking or understocking. By anticipating demand and adjusting inventory levels, it maintains a balance between meeting customer needs and minimizing excess inventory costs. This approach optimizes operations, reduces waste, and enhances customer satisfaction.
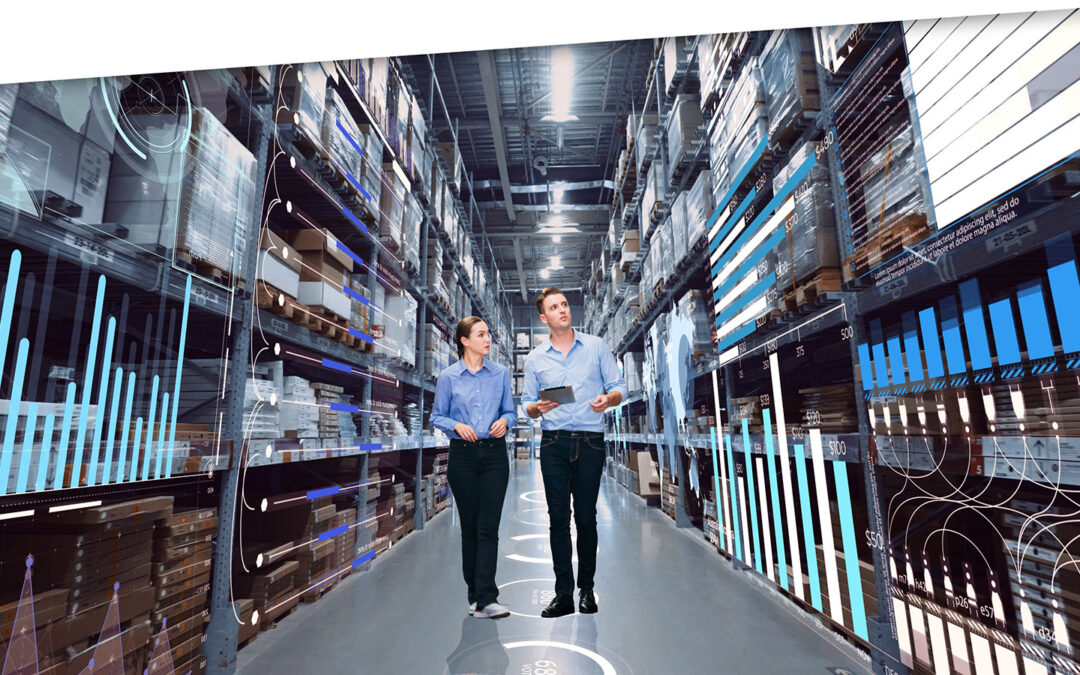
Make AI-Driven Inventory Optimization an Ally for Your Organization
In this blog, we will explore how organizations can achieve exceptional efficiency and accuracy with AI-driven inventory optimization. Traditional inventory management methods often fall short due to their reactive nature and reliance on manual processes. Maintaining optimal inventory levels is fundamental for meeting customer demand while minimizing costs. The introduction of AI-driven inventory optimization can significantly reduce the burden of manual processes, providing relief to supply chain managers from tedious tasks.
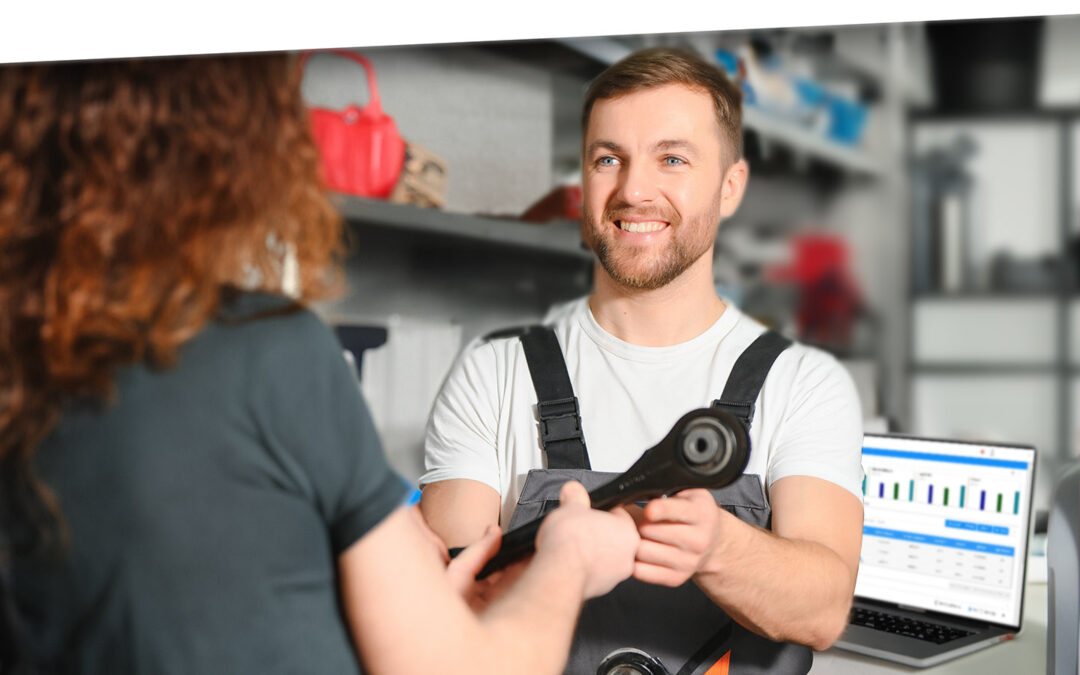
The Importance of Clear Service Level Definitions in Inventory Management
Inventory optimization software that supports what-if analysis will expose the tradeoff of stockouts vs. excess costs of varying service level targets. But first it is important to identify how “service levels” is interpreted, measured, and reported. This will avoid miscommunication and the false sense of security that can develop when less stringent definitions are used. Clearly defining how service level is calculated puts all stakeholders on the same page. This facilitates better decision-making.
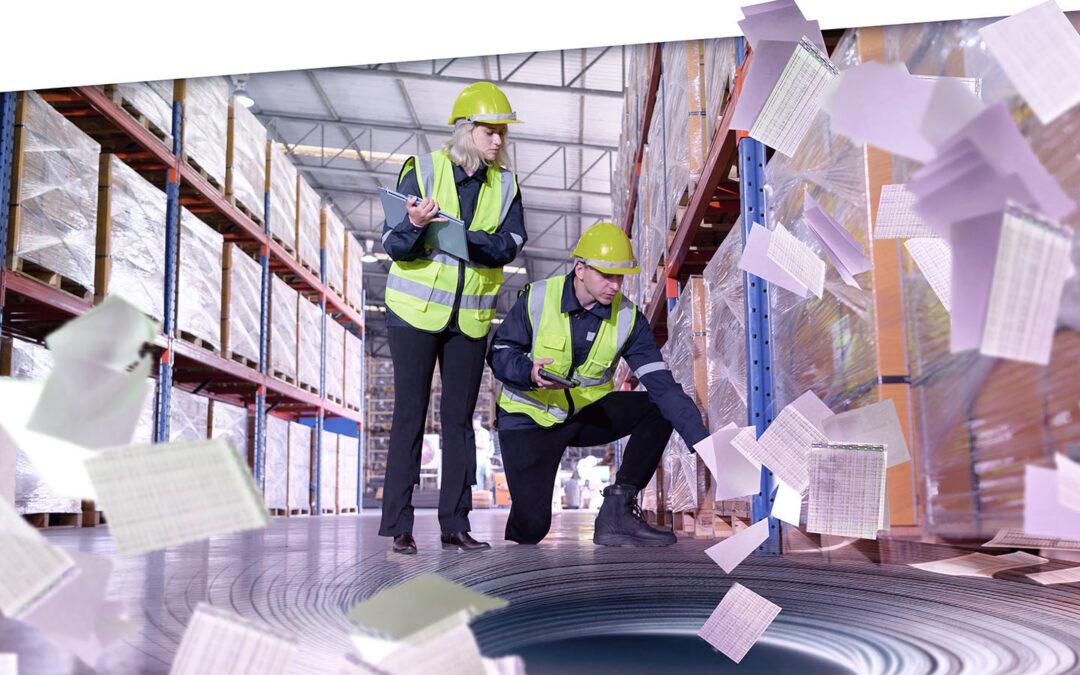
The Cost of Spreadsheet Planning
Companies that depend on spreadsheets for demand planning, forecasting, and inventory management are often constrained by the spreadsheet’s inherent limitations. This post examines the drawbacks of traditional inventory management approaches caused by spreadsheets and their associated costs, contrasting these with the significant benefits gained from embracing state-of-the-art planning technologies.
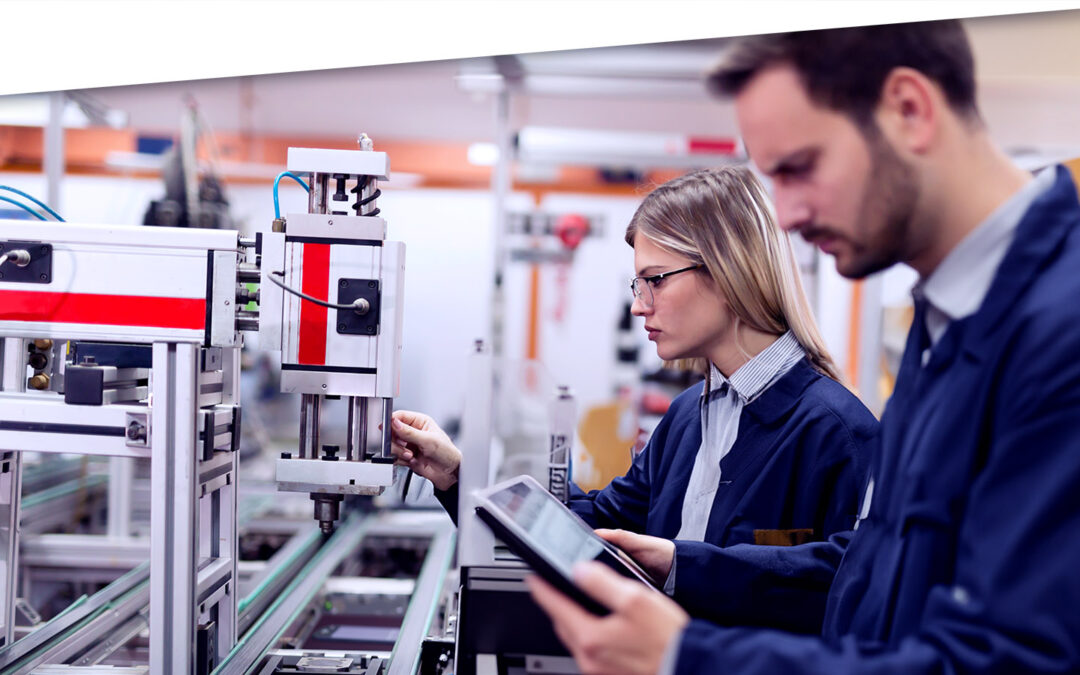
Leveraging Epicor Kinetic Planning BOMs with Smart IP&O to Forecast Accurately
In this blog, we explore how leveraging Epicor Kinetic Planning BOMs with Smart IP&O can transform your approach to forecasting in a highly configurable manufacturing environment. Discover how Smart, a cutting-edge AI-driven demand planning and inventory optimization solution, can simplify the complexities of predicting finished goods demand, especially when dealing with interchangeable components. Learn how Planning BOMs and advanced forecasting techniques enable businesses to anticipate customer needs more accurately, ensuring operational efficiency and staying ahead in a competitive market.
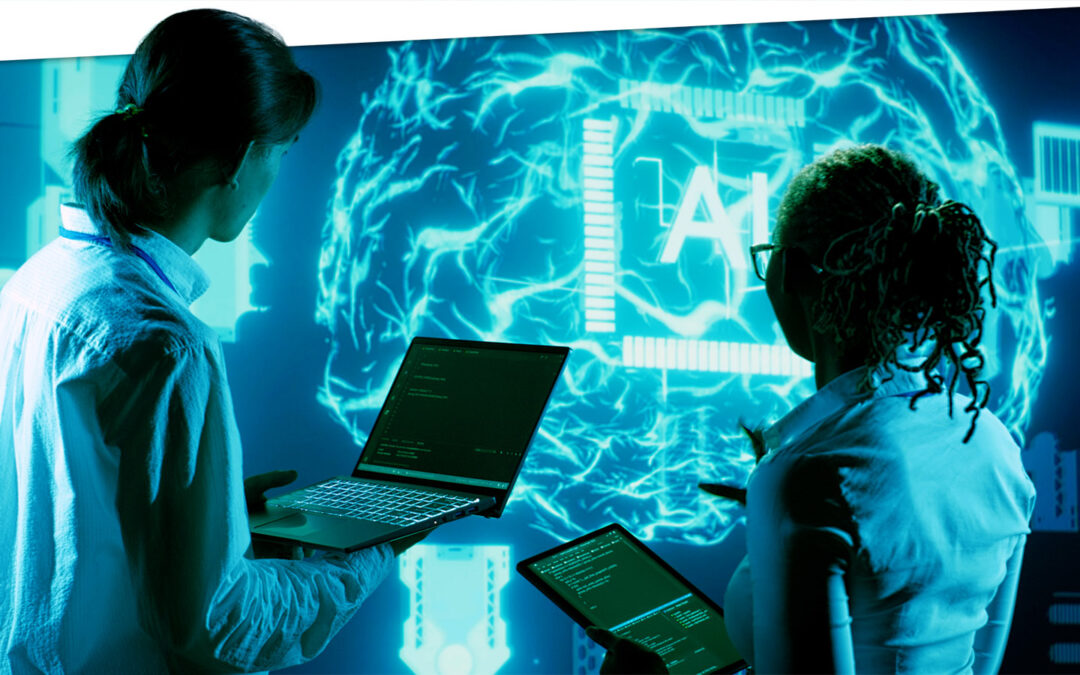
The Next Frontier in Supply Chain Analytics
We believe the leading edge of supply chain analytics to be the development of digital twins of inventory systems. These twins take the form of discrete event models that use Monte Carlo simulation to generate and optimize over the full range of operational risks. We also assert that we and our colleagues at Smart Software have played an outsized role in forging that leading edge.
Problem
Keeping inventory investments in check while maintaining high customer service levels is a constant balancing act. Without proper controls, excess inventory grows throughout your supply chain, locking up vital working capital that constrains your company’s growth. Every day, the ERP system makes purchase order suggestions and manufacturing orders based on planning drivers such as safety stock, reorder points, and Min/Max levels. Ensuring that these inputs are understood and continually optimized will generate substantially better returns on your inventory assets. Unfortunately, many organizations rely on rule of thumb logic, institutional knowledge, and “one-size-fits all” forecasting logic that assigns all items within a particular group the same service level target. These approaches yield suboptimal policies that cause inventory costs to balloon and service performance to suffer. Compounding the problem is the sheer volume of data – thousands of items stocked at multiple locations means planners don’t have the bandwidth to proactively review these inventory drivers on a regular basis. This results in outdated reorder points, safety stocks, order quantities, and Min/Max settings that further contribute to the problem.
Solution
Smart Inventory Optimization (SIO™) is available on Smart’s Inventory Planning and Optimization Platform, Smart IP&O. It delivers inventory policy decision support and the means to share, collaborate, and track the impact of your inventory planning policy. This can help realize millions in savings by improving customer service and reducing excess stock. You can forecast metrics such as service level, fill rate, holding costs, ordering costs, and stock out costs. Users can identify overstocks and understocks, adjust stocking policies when demand changes, share proposed policies with other stakeholders, collect feedback, and establish a consensus inventory plan. And unlike traditional inventory planning systems that rely on rule of thumb approaches or require the user to arbitrarily set suboptimal service level targets, Smart Inventory Optimization prescribes the optimal service levels for you. Users can optionally assign service level constraints to ensure the optimization engine respects business rules. SIO provides the required inventory planning parameters for a variety of replenishment policies such as Reorder Point/Order Quantity, Min/Max, Safety Stock Planning, and Order Up to levels.
Register to Watch the Demo
With Smart Inventory Optimization you can:
- Identify where you are overstocked and understocked.
- Modify planning parameters based on your business rules, service targets, and inventory budget.
- Leverage the optimization logic in SIO to prescribe planning parameters and service levels for you.
- Compare proposed policies to the benchmark.
- Collaborate and develop a consensus inventory plan.
- Automatically generate revised planning parameters as demand and other inputs change.
Smart Inventory Optimization
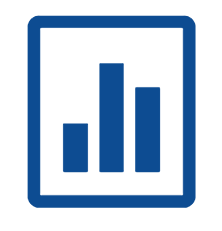
Optimal Inventory Levels
Reduce excess stock
Improve service levels
Minimize buyer transactions
Maximize return on assets

Organizational Consensus
Balance service levels
Identify stockout risk
Identify overstocks
No finger-pointing
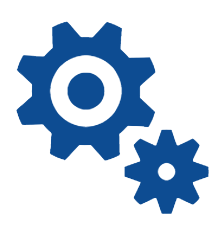
Operational Connectivity
Align process with strategic objectives
Empower team to “make it so”
Optimize as conditions change
Pass results to ERP
Who is Inventory Optimization for?
Smart Inventory Optimization is for executives and business savvy planners who seek to:
- Yield maximum returns from inventory assets.
- Address the problem of highly variable or intermittent demand.
- Broker the service vs. cost tradeoffs between different departments.
- Develop a repeatable and efficient inventory planning process.
- Empower the team to ensure operational plan is aligned with strategic plan.
What questions can Inventory Optimization answer?
- What is the best service level achievable with the inventory budget?
- What service levels will yield the maximum return?
- If lead times increased, what would it cost to maintain service?
- If I reduce inventory, what will the impact on service be?
- If order quantity increases, what will the impact on service and costs be?
- What is the order quantity that balances holding and ordering costs?
Inventory forecasting for the inventory executive
Smart Inventory Optimization empowers you to:
- Predict service performance and inventory costs.
- Assess business impact of “what-if” inventory policies.
- Align inventory policy with corporate strategy.
- Establish an operational framework that guides the planning team.
- Reduce inventory and improve service.