A fundamental aspect of supply chain management is accurate demand forecasting. Some product items have an intermittent demand pattern that makes them all but impossible to forecast with traditional, smoothing-based forecasting methods. We address the problem of forecasting intermittent demand (or irregular demand), i.e. random demand with a large proportion of zero values. This pattern is characteristic of demand for companies that manage large inventories of service and spare parts in industries such as aviation, aerospace, automotive, high tech, and electronics, as well as in MRO (Maintenance, Repair and Overhaul).
Accurate forecasting of demand is important in inventory control, but the intermittent nature of demand makes forecasting especially difficult for service parts planning. Similar problems arise when an organization manufactures slow-moving items and requires sales forecasts for planning purposes. Because forecasts of intermittent and lumpy demand have been so unreliable, most companies forecast inventory requirements relying primarily on subjective business knowledge, forecast only a fraction of their higher volume inventory, use simple “rule of thumb” estimates, or traditional statistical forecasting that incorrectly assumes a particular type demand distribution for inventory control.
Learn industry best practices on how to improve intermittent demand forecasting and create supply chain efficiencies in the articles below.

Future-Proofing Utilities: Advanced Analytics for Supply Chain Optimization
Utilities in the electrical, natural gas, urban water, and telecommunications fields are all asset-intensive and reliant on physical infrastructure that must be properly maintained, updated, and upgraded over time. Maximizing asset uptime and the reliability of physical infrastructure demands effective inventory management, spare parts forecasting, and supplier management. A utility that executes these processes effectively will outperform its peers, provide better returns for its investors and higher service levels for its customers, while reducing its environmental impact.

Centering Act: Spare Parts Timing, Pricing, and Reliability
In this article, we’ll walk you through the process of crafting a spare parts inventory plan that prioritizes availability metrics such as service levels and fill rates while ensuring cost efficiency. We’ll focus on an approach to inventory planning called Service Level-Driven Inventory Optimization. Next, we’ll discuss how to determine what parts you should include in your inventory and those that might not be necessary. Lastly, we’ll explore ways to enhance your service-level-driven inventory plan consistently.

Why MRO Businesses Need Add-on Service Parts Planning & Inventory Software
MRO organizations exist in a wide range of industries, including public transit, electrical utilities, wastewater, hydro power, aviation, and mining. To get their work done, MRO professionals use Enterprise Asset Management (EAM) and Enterprise Resource Planning (ERP) systems. These systems are designed to do a lot of jobs. Given their features, cost, and extensive implementation requirements, there is an assumption that EAM and ERP systems can do it all. In this post, we summarize the need for add-on software that addresses specialized analytics for inventory optimization, forecasting, and service parts planning.

5 Steps to Improve the Financial Impact of Spare Parts Planning
In today’s competitive business landscape, companies are constantly seeking ways to improve their operational efficiency and drive increased revenue. Optimizing service parts management is an often-overlooked aspect that can have a significant financial impact. Companies can improve overall efficiency and generate significant financial returns by effectively managing spare parts inventory. This article will explore the economic implications of optimized service parts management and how investing in Inventory Optimization and Demand Planning Software can provide a competitive advantage.
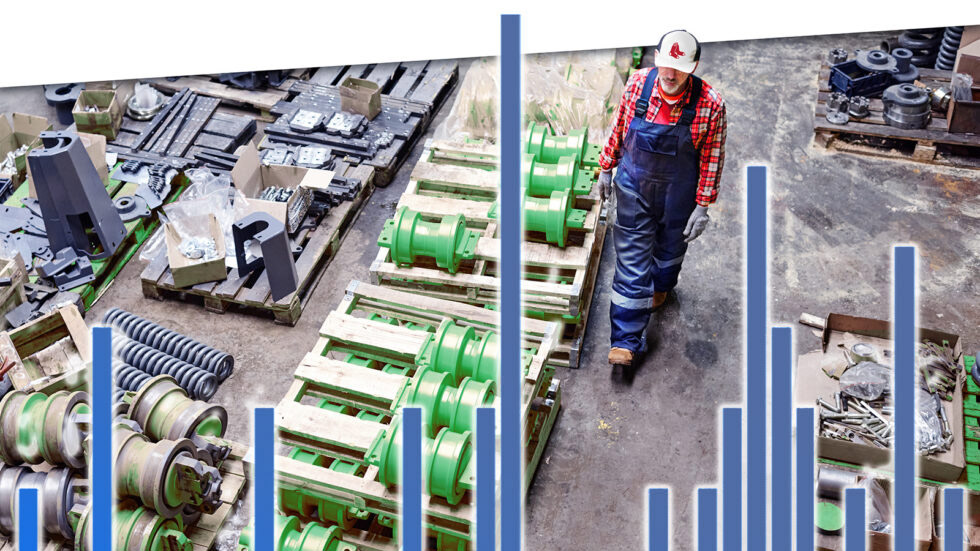
The Forecast Matters, but Maybe Not the Way You Think
True or false: The forecast doesn’t matter to spare parts inventory management. At first glance, this statement seems obviously false. After all, forecasts are crucial for planning stock levels, right? It depends on what you mean by a “forecast”. If you mean an old-school single-number forecast (“demand for item CX218b will be 3 units next week and 6 units the week after”), then no. If you broaden the meaning of forecast to include a probability distribution taking account of uncertainties in both demand and supply, then yes.
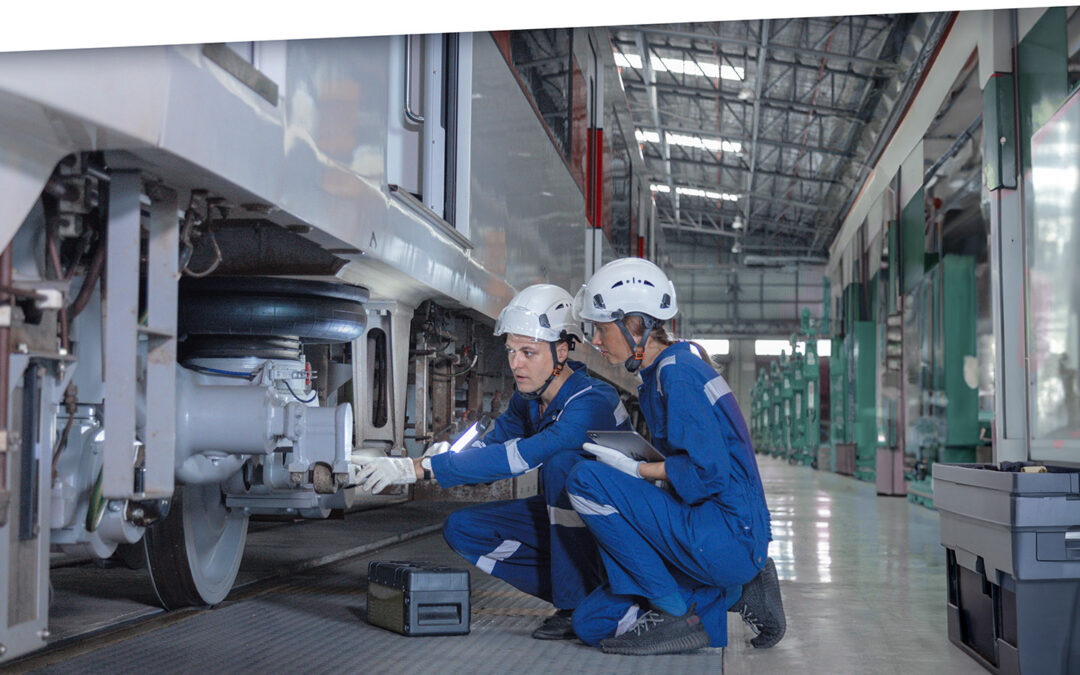
Why MRO Businesses Should Care About Excess Inventory
Do MRO companies genuinely prioritize reducing excess spare parts inventory? From an organizational standpoint, our experience suggests not necessarily. Boardroom discussions typically revolve around expanding fleets, acquiring new customers, meeting service level agreements (SLAs), modernizing infrastructure, and maximizing uptime. In industries where assets supported by spare parts cost hundreds of millions or generate significant revenue (e.g., mining or oil & gas), the value of the inventory just doesn’t raise any eyebrows, and organizations tend to overlook massive amounts of excessive inventory.
The Problem
Some product items have an intermittent demand pattern that makes them all but impossible to forecast with traditional, smoothing-based forecasting methods. Items with intermittent demand – also known as lumpy, volatile, variable or unpredictable demand – have many zero or low volume values interspersed with random spikes of demand that are often many times larger than the average. This problem is especially prevalent in companies that manage large inventories of service and spare parts in industries such as aviation, aerospace, automotive, high tech, and electronics, as well as in MRO (Maintenance, Repair and Overhaul).
Intermittent demand
In these businesses, as much as 80% of the parts and product items may have intermittent or lumpy demand. Intermittent demand makes it difficult to accurately estimate the safety stock and service level inventory requirements needed for successful supply chain planning. Because forecasts of intermittent and lumpy demand have been so unreliable, most companies forecast inventory requirements relying primarily on subjective business knowledge, forecast only a fraction of their higher volume inventory, use simple “rule of thumb” estimates, or traditional statistical forecasting that incorrectly assumes a particular type demand distribution for inventory control. The result is that billions of dollars are wasted every year because of either excess inventory costs or poor customer service due to stock-outs.
Intermittent demand – also known as lumpy, volatile, variable or unpredictable demand.
The Smart Solution
SmartForecasts and Smart Inventory Optimization use a unique empirical probabilistic forecasting approach that results in accurate forecasts of inventory requirements where demand is intermittent. The solution works particularly well whenever demand does not conform to a simple normal distribution. Our patented, APICS award-winning “bootstrapping” technology rapidly generates tens of thousands of possible scenarios of future demand sequences and cumulative demand values over an item’s lead time. These scenarios are statistically similar to the item’s observed data, and they capture the relevant details of intermittent demand without relying on the assumptions commonly made about the nature of demand distributions by traditional forecasting methods. The result is a highly accurate forecast of the entire distribution of cumulative demand over an item’s full lead time. With the information these demand distributions provide, you can easily plan your company’s safety stock and service level inventory requirements for thousands of intermittently demanded items with nearly 100% accuracy.
The Benefits
Companies using our powerful intermittent demand forecasting and planning solution typically reduce standing inventory by 20% in the first year, increase parts availability 10-20%, and reduce the need for and associated costs of emergency transshipment to close gaps in their supply chain. Repair and service parts inventories are truly optimized, leading to more efficient operations, improvements in customer service, and significantly less cash tied up in inventory.
White Paper: Smart Software Gen2
In this white paper, we introduce “Gen2”, our next generation of probabilistic modeling technology that powers the Smart IP&O Platform. We recount the evolution of Smart Software’s forecasting methods and we detail how Gen2 substantially expands the capabilities that have made Gen1 so useful to so many companies. Finally, we will also give a high-level view of the probability math behind Gen2 . Fill in this form and we'll email you the paper.