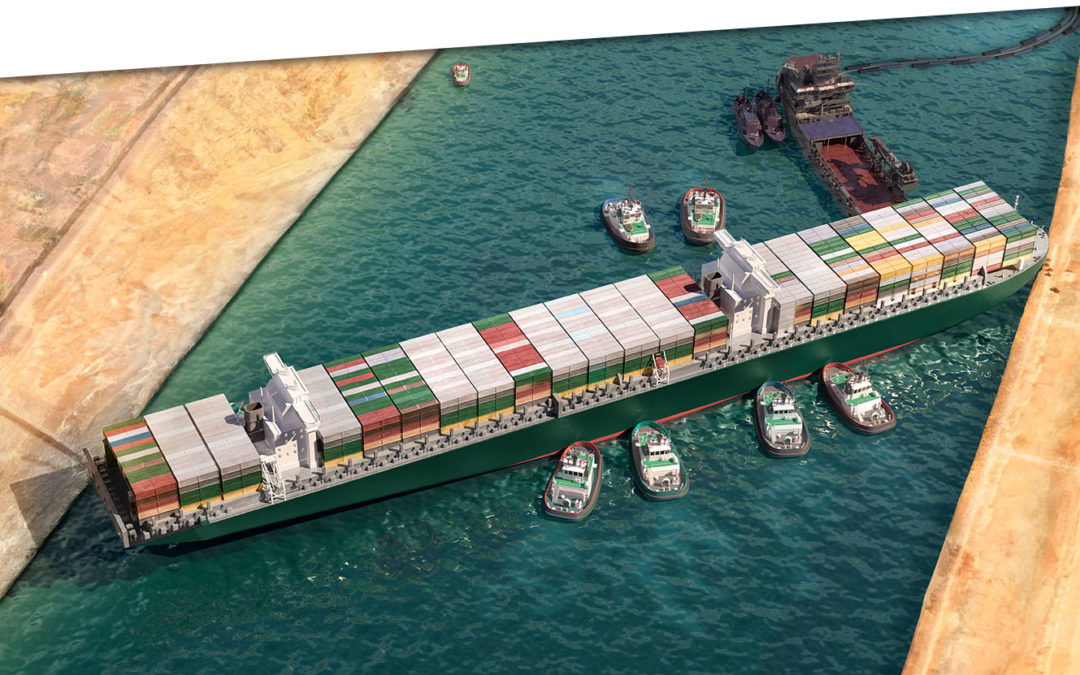
Redefine Exceptions and Fine Tune Planning to Address Uncertainty
In a perfect world, Just in Time (JIT) would be the appropriate solution for inventory management. But as the saying goes “everyone has a plan until they get punched in the mouth.” One enormous punch in the mouth for the global supply chain was Suez Canal Blockage that held up $9.6B in trade costing an estimated $6.7M per minute.
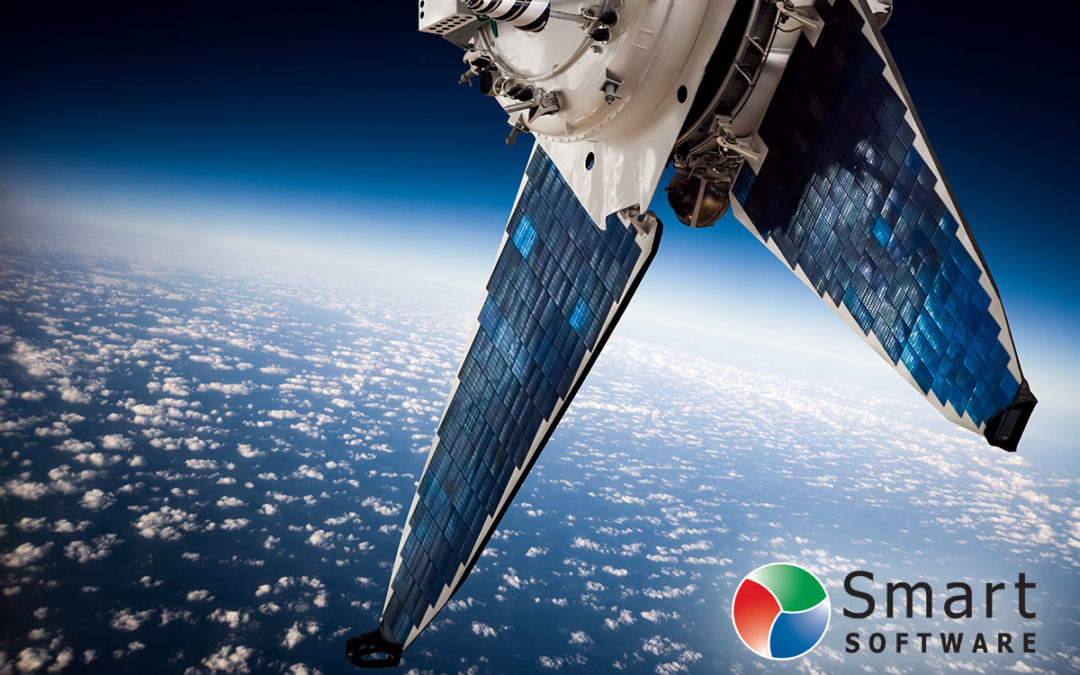
Engineering to Order at Kratos Space – Making Parts Availability a Strategic Advantage
The Kratos Space group within National Security technology innovator Kratos Defense & Security Solutions, Inc., produces COTS s software and component products for space communications – Making Parts Availability a Strategic Advantage
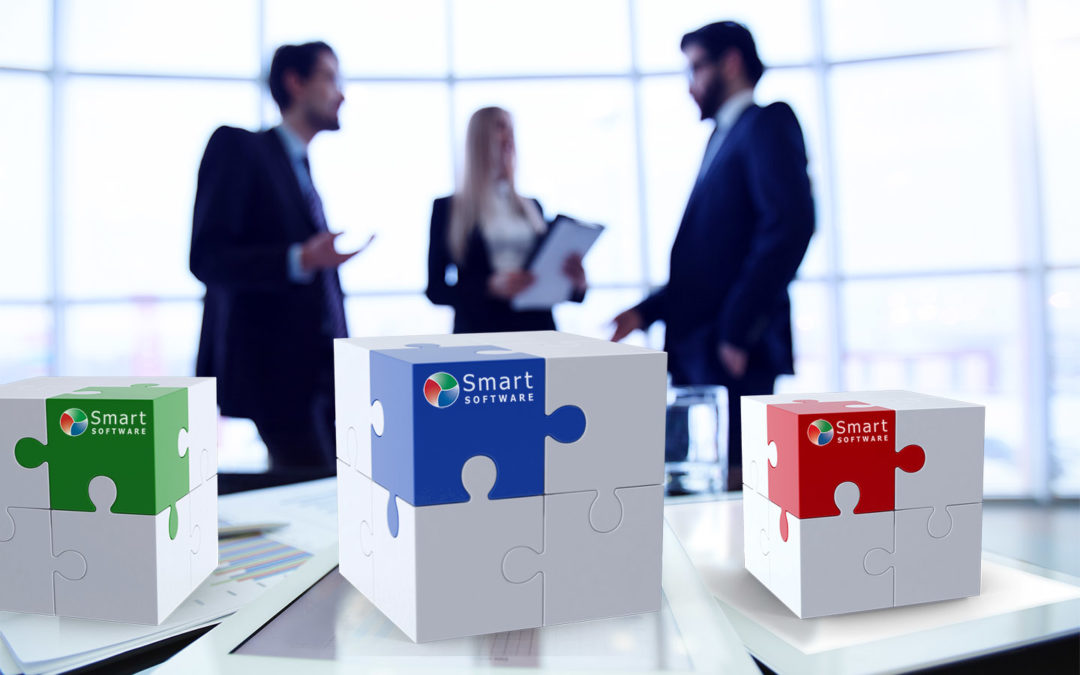
Ten Tips that Avoid Data Problems in Software Implementation
Once a customer is ready to implement software for demand planning and/or inventory optimization, they need to connect the analytics software to their corporate data stream.This provides information on item demand and supplier lead times, among other things. We extract the rest of the data from the ERP system itself, which provides metadata such as each item’s location, unit cost, and product group.
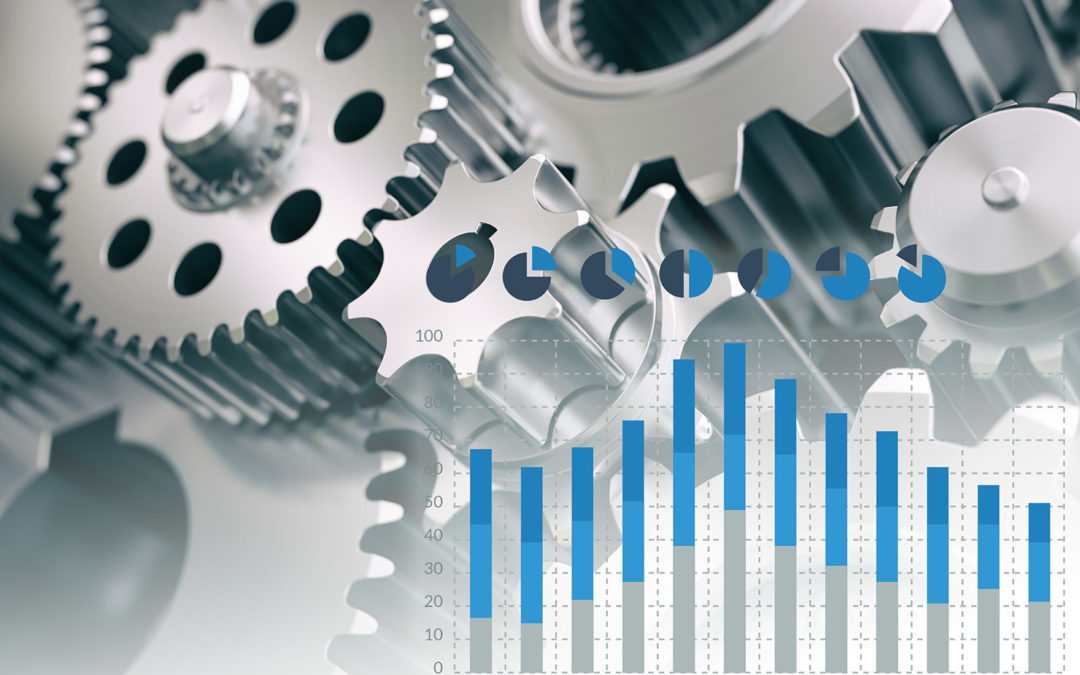
MAX-MIN OR ROP – ROQ
This guest blog details the differences between Min-Max and Reorder Point- Order Quantity replenishment logic and why it is important. It is authored by Phillip Slater, Founder of SparePartsKNowHow.com the leading educational resource for spare parts management. Mr. Slater is a global leader and consultant on materials management and specifically, engineering spare parts inventory management and optimization.
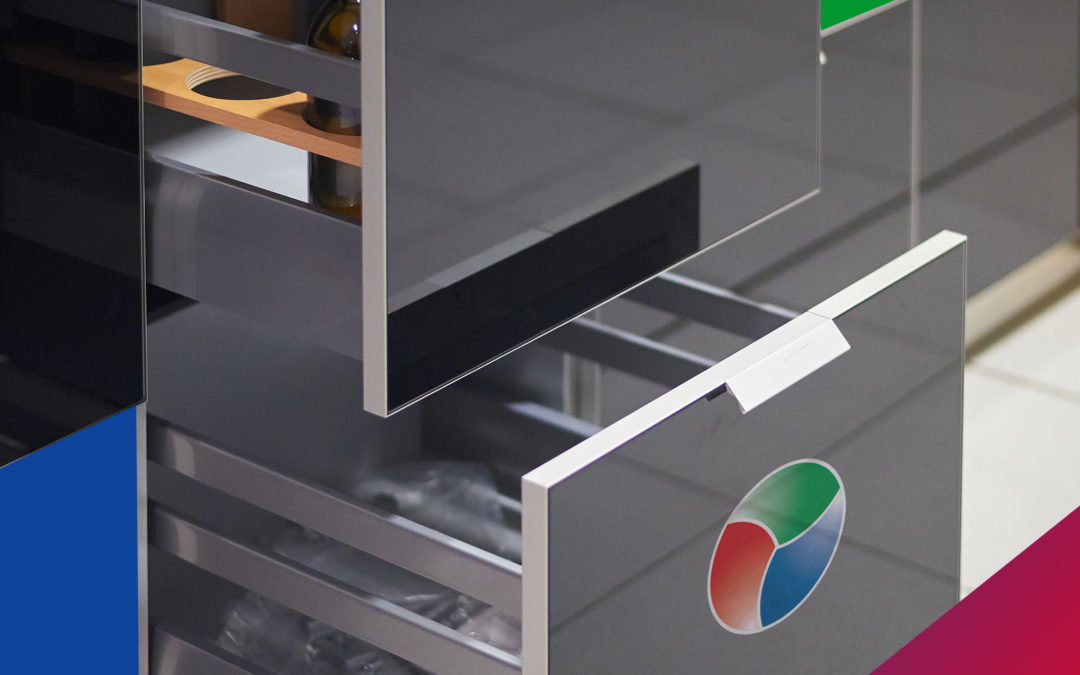
Handling Extreme Supply Chain Variability at Rev-A-Shelf
Does your extended supply chain suffer from extreme seasonal variability? Does this situation challenge your ability to meet service level commitments to your customers? I have grappled with this at Rev-A-Shelf, addressing unusual conditions created by Chinese New Year and other global events, and would like to share the experience and a few things I learned along the way.
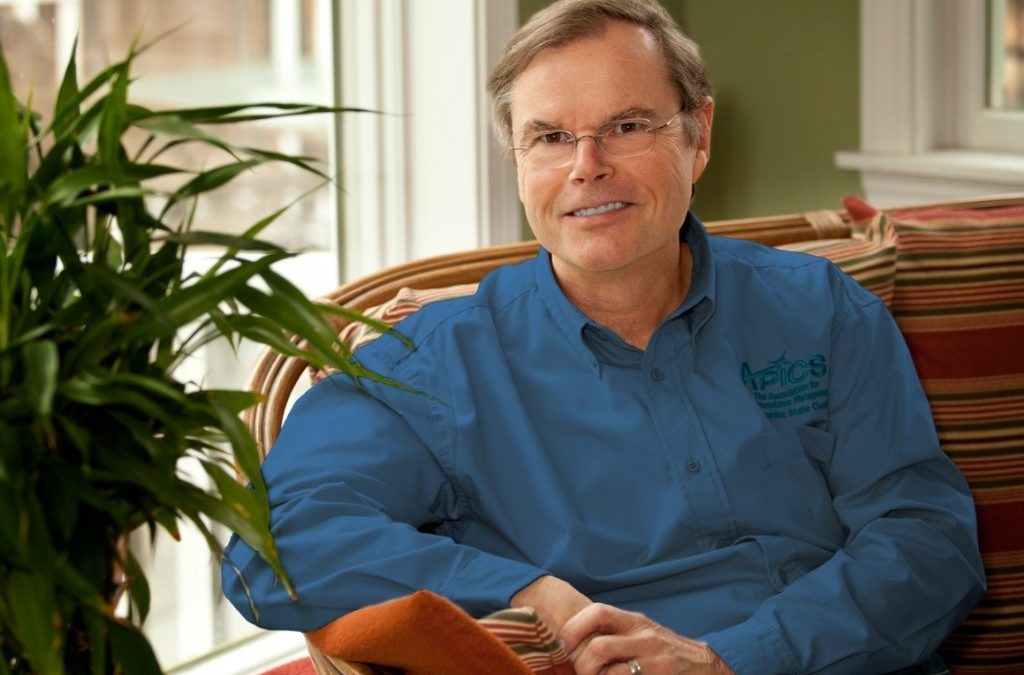
Truth in Forecasting—Practical Advice at Year’s End
At year’s end, we are often caught up in thinking and planning for the coming year. Did 2013 turn out the way you expected? Will 2014 be dramatically different? Are there other factors—things we are planning to do; things we think our competitors might do; outside forces like changing taste, demographics or economics—that might change the course of business in the coming year?
Problem
Keeping inventory investments in check while maintaining high customer service levels is a constant balancing act. Without proper controls, excess inventory grows throughout your supply chain, locking up vital working capital that constrains your company’s growth. Every day, the ERP system makes purchase order suggestions and manufacturing orders based on planning drivers such as safety stock, reorder points, and Min/Max levels. Ensuring that these inputs are understood and continually optimized will generate substantially better returns on your inventory assets. Unfortunately, many organizations rely on rule of thumb logic, institutional knowledge, and “one-size-fits all” forecasting logic that assigns all items within a particular group the same service level target. These approaches yield suboptimal policies that cause inventory costs to balloon and service performance to suffer. Compounding the problem is the sheer volume of data – thousands of items stocked at multiple locations means planners don’t have the bandwidth to proactively review these inventory drivers on a regular basis. This results in outdated reorder points, safety stocks, order quantities, and Min/Max settings that further contribute to the problem.
Solution
Smart Inventory Optimization (SIO™) is available on Smart’s Inventory Planning and Optimization Platform, Smart IP&O. It delivers inventory policy decision support and the means to share, collaborate, and track the impact of your inventory planning policy. This can help realize millions in savings by improving customer service and reducing excess stock. You can forecast metrics such as service level, fill rate, holding costs, ordering costs, and stock out costs. Users can identify overstocks and understocks, adjust stocking policies when demand changes, share proposed policies with other stakeholders, collect feedback, and establish a consensus inventory plan. And unlike traditional inventory planning systems that rely on rule of thumb approaches or require the user to arbitrarily set suboptimal service level targets, Smart Inventory Optimization prescribes the optimal service levels for you. Users can optionally assign service level constraints to ensure the optimization engine respects business rules. SIO provides the required inventory planning parameters for a variety of replenishment policies such as Reorder Point/Order Quantity, Min/Max, Safety Stock Planning, and Order Up to levels.
Register to Watch the Demo
With Smart Inventory Optimization you can:
- Identify where you are overstocked and understocked.
- Modify planning parameters based on your business rules, service targets, and inventory budget.
- Leverage the optimization logic in SIO to prescribe planning parameters and service levels for you.
- Compare proposed policies to the benchmark.
- Collaborate and develop a consensus inventory plan.
- Automatically generate revised planning parameters as demand and other inputs change.