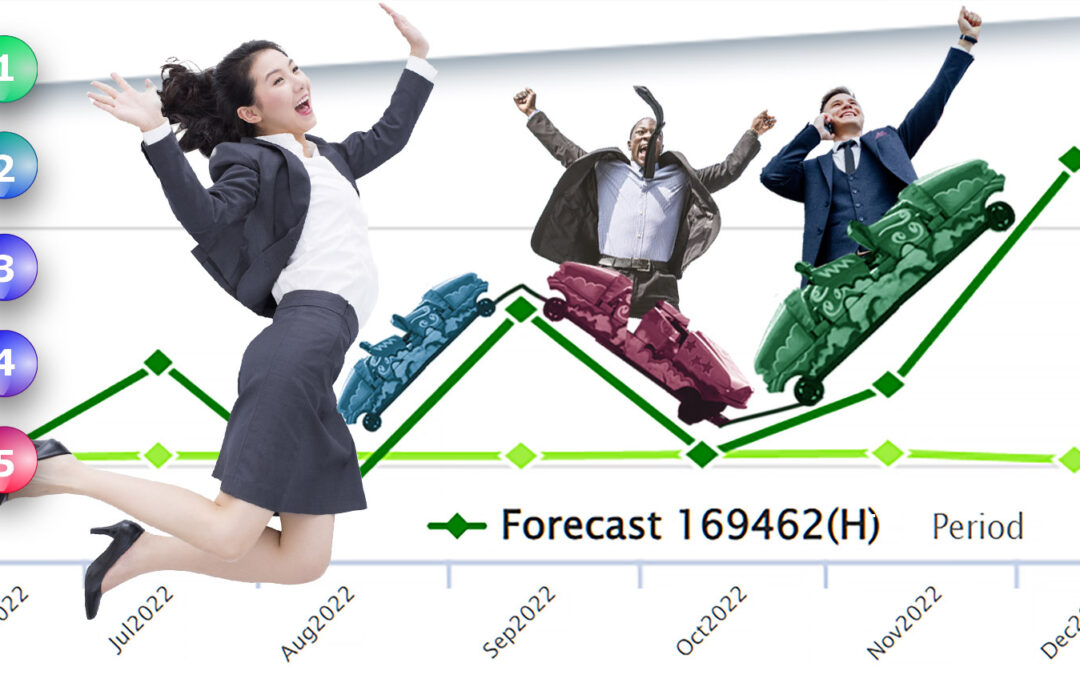
Top Five Tips for New Demand Planners and Forecasters
Good forecasting can make a big difference to your company’s performance, whether you are forecasting to support sales, marketing, production, inventory, or finance. This blog is aimed primarily at those fortunate individuals who are about to start this adventure. Welcome to the field!
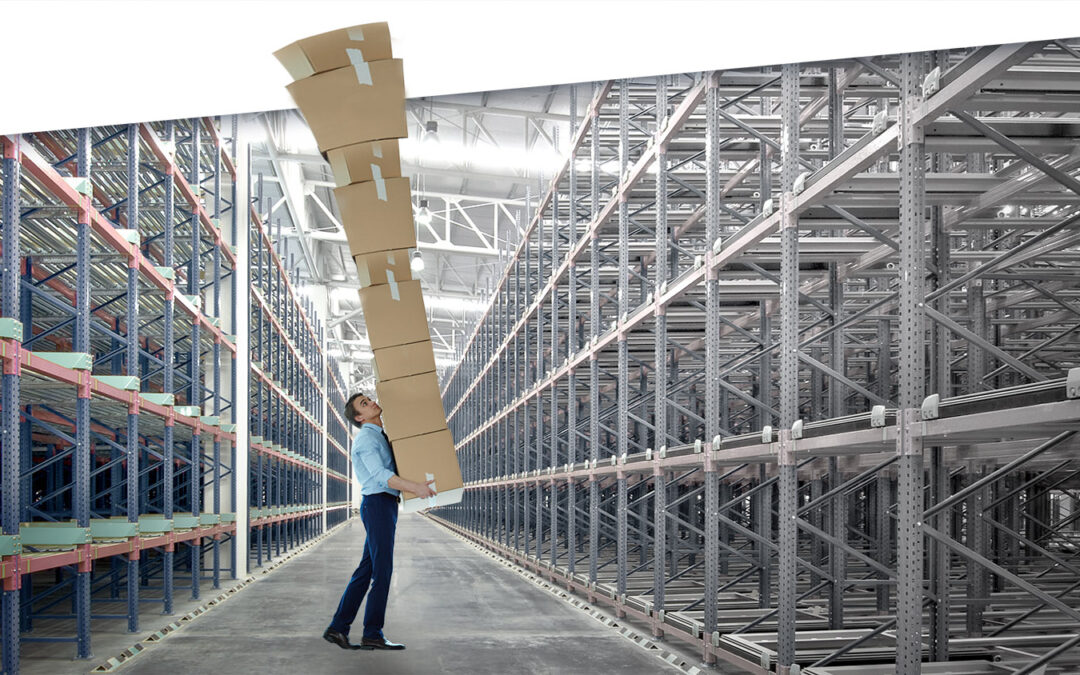
The Supply Chain Blame Game: Top 3 Excuses for Inventory Shortage and Excess
The supply chain has become the blame game for almost any industrial or retail problem. Shortages on lead time variability, bad forecasts, and problems with bad data are facts of life, yet inventory-carrying organizations are often caught by surprise when any of these difficulties arise. So, again, who is to blame for the supply chain chaos? Keep reading this blog and we will try to show you how to prevent product shortages and overstocking.
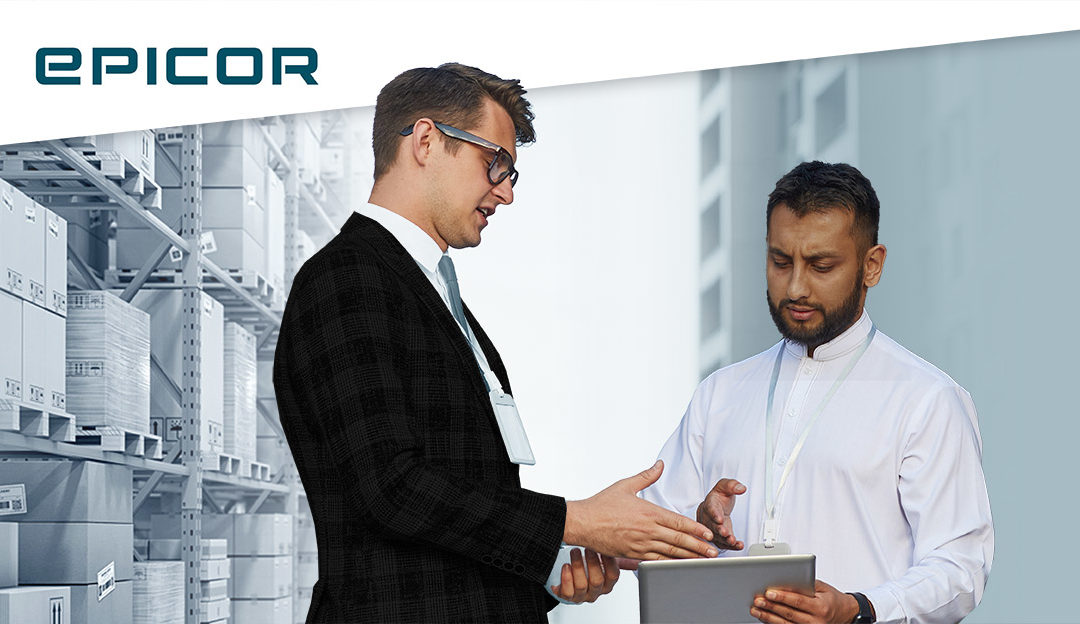
Extend Epicor Kinetic’s Forecasting & Min/Max Planning with Smart IP&O
Epicor Kinetic can manage replenishment by suggesting what to order and when via reorder point-based inventory policies. The problem is that the ERP system requires that the user either manually specify these reorder points, or use a rudimentary “rule of thumb” approach based on daily averages. In this article, we will review the inventory ordering functionality in Epicor Kinetic, explain its limitations, and summarize how to reduce inventory, and minimize stockouts by providing the robust predictive functionality that is missing in Epicor.
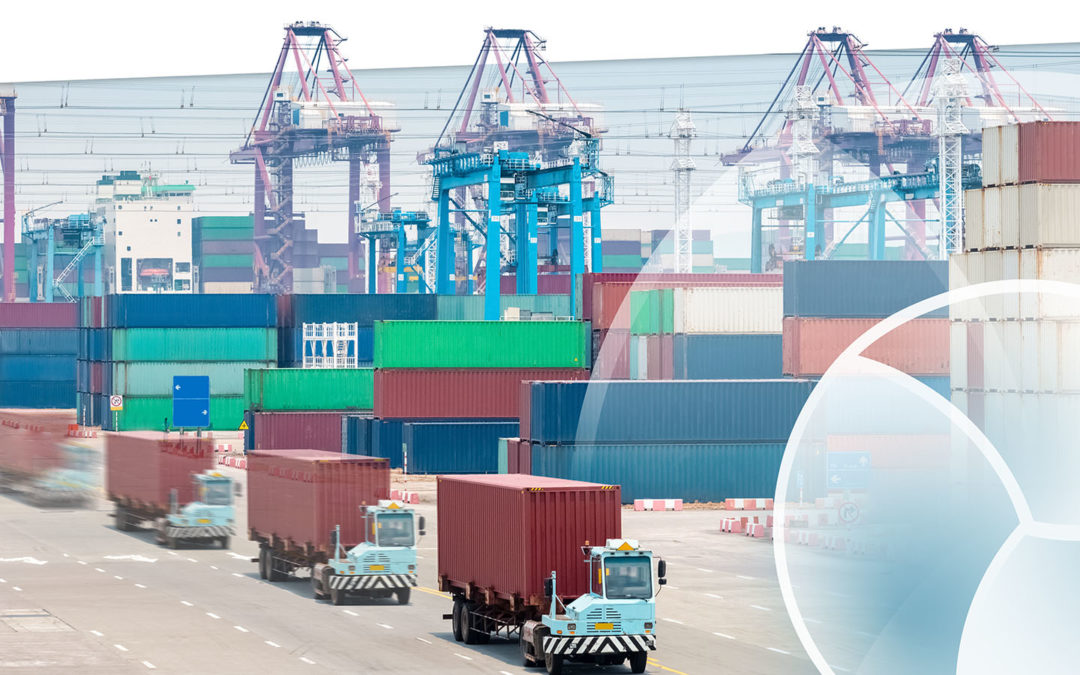
Demand Planning with Blanket Orders
Our customers are great teachers who have always helped us bridge the gap between textbook theory and practical application. Our latest bit of schooling concerns how to effectively incorporate “blanket orders” into the demand planning process.
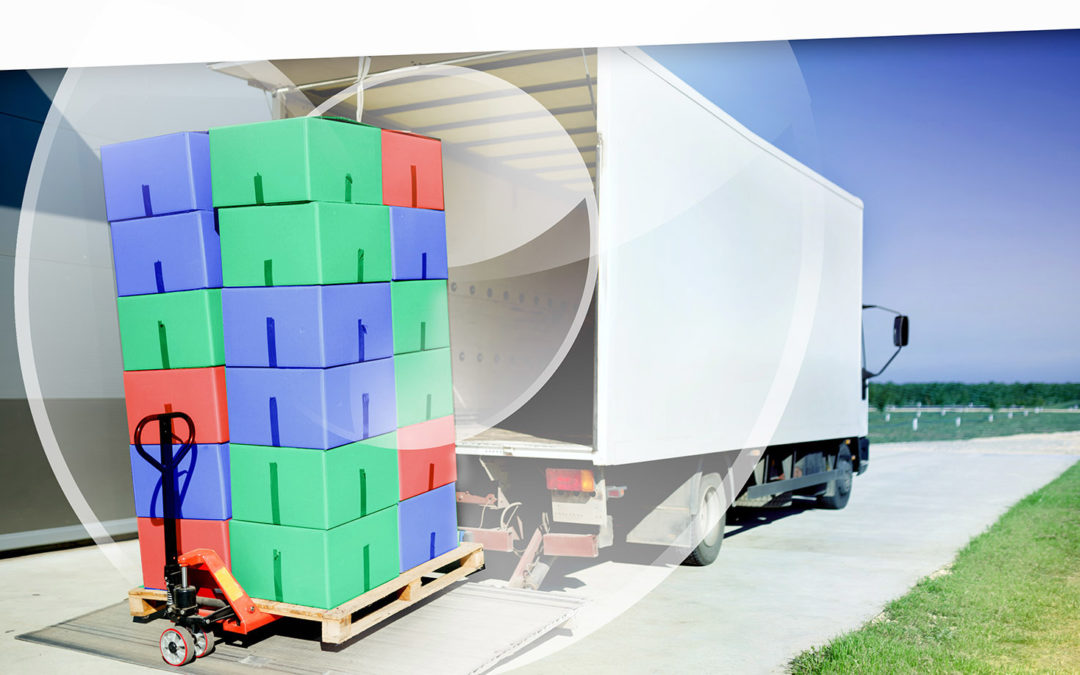
Optimizing Inventory around Suppliers´ Minimum Order Quantities
Recently, we had an interesting conversation with an inventory manager and the VP Finance. We were discussing the benefits of being able to automatically optimize both reorder points and order quantities. The VP Finance was concerned that given their large supplier required minimum order quantities, they would not be able to benefit. He said his suppliers held all the power, forcing him to accept massive minimum order quantities and tying his hands. While he felt bad about this, he saw a silver lining: He didn’t have to do any planning. He would accept a large inventory investment, but his customer service levels would the exceptional. Perhaps the large inventory investment was assumed to be the cost of doing business.
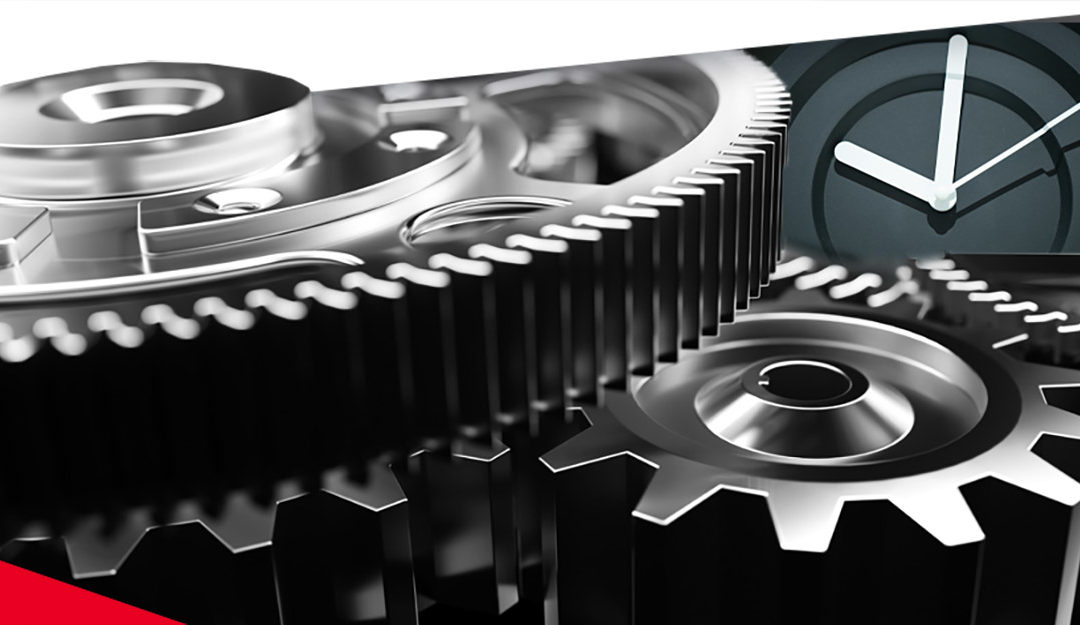
A Beginner’s Guide to Downtime and What to Do about It
If you manufacture things for sale, you need machines to make those things. If your machines are up and running, you have a fighting chance to make money. If your machines are down, you lose opportunities to make money.
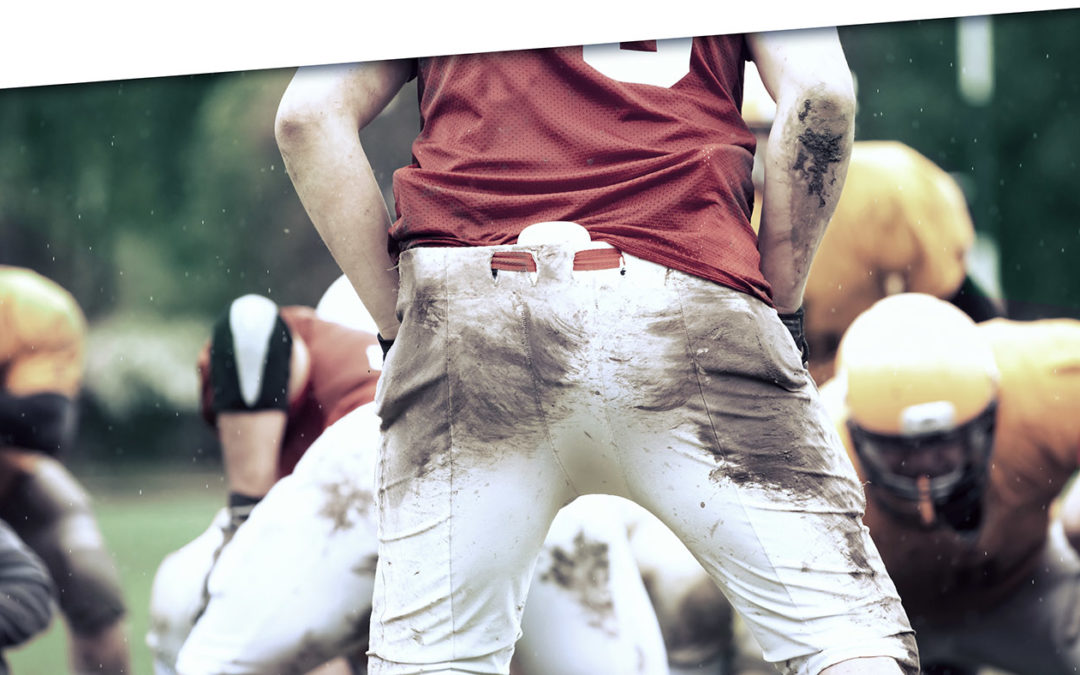
Call an Audible to Proactively Counter Supply Chain Noise
You know the situation: You work out the best way to manage each inventory item by computing the proper reorder points and replenishment targets, then average demand increases or decreases, or demand volatility changes, or suppliers’ lead times change, or your own costs change.
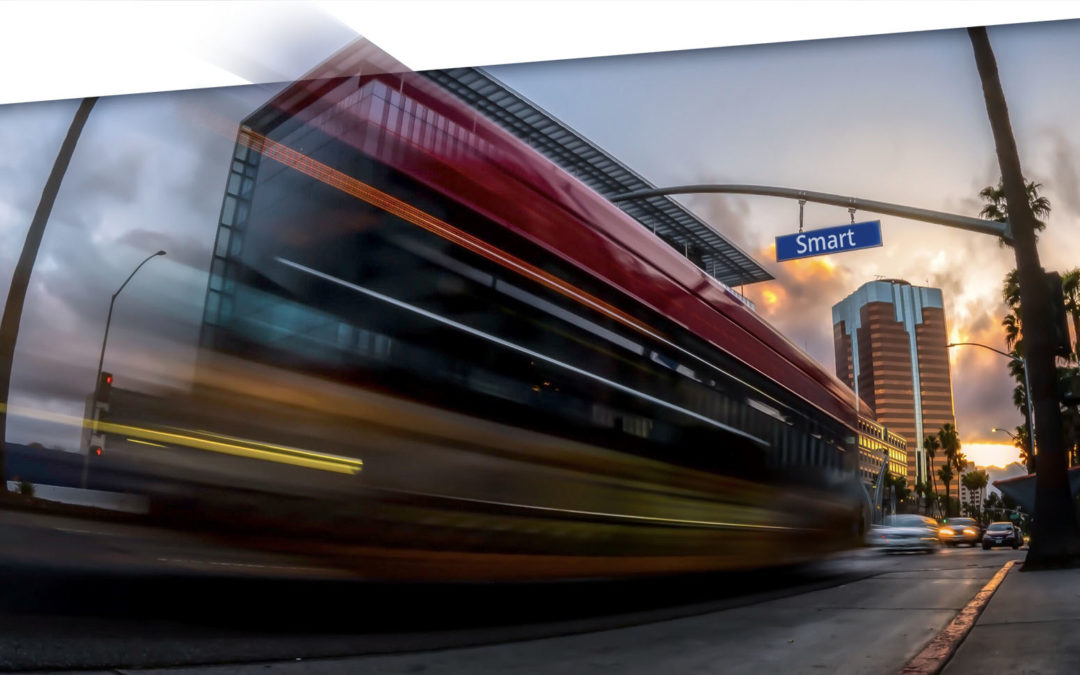
Thoughts on Spare Parts Planning for Public Transit
The Covid19 pandemic has placed unusual stress on public transit agencies. This stress forces agencies to look again at their processes and equipment. This blog focuses on bus systems and their practices for spare parts planning and management. However, there are lessons here for other types of public transit, including rail and light rail
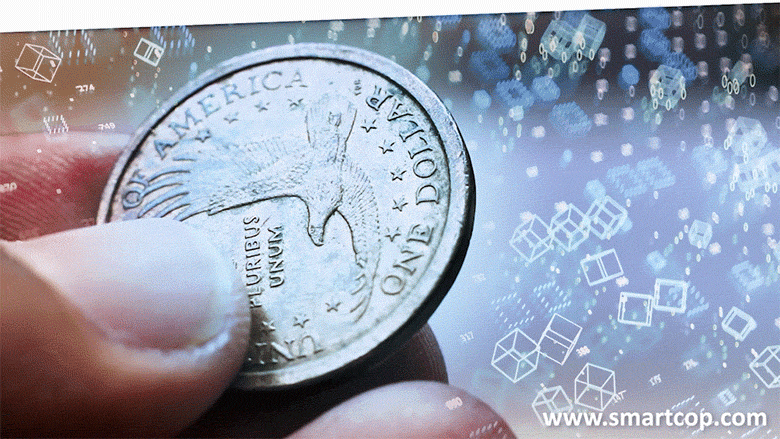
A Primer on Probabilistic Forecasting
If you keep up with the news about supply chain analytics, you are more frequently encountering the phrase “probabilistic forecasting.” Probabilistic forecasts have the ability to simulate future values that aren’t anchored to the past. If this phrase is puzzling, read on.
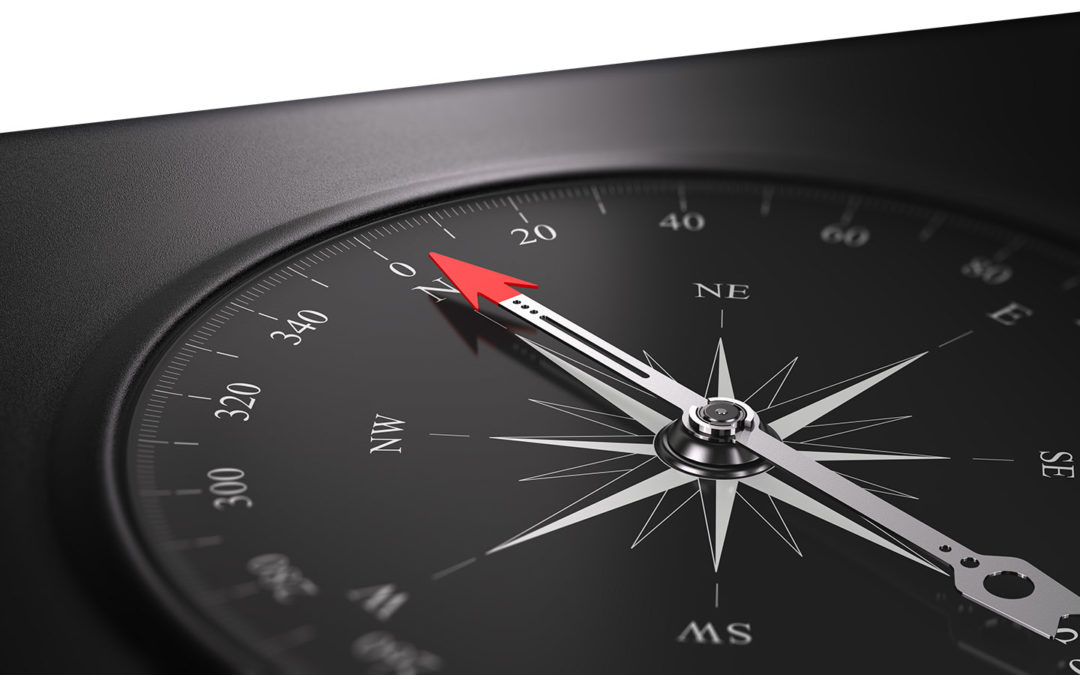
Stay the course
We’ve found that a few things help new customers exploit the power of advanced analytics for forecasting and inventory optimization. One is having a champion among management, an executive sponsor, who can vouch for the commercial importance of a successful implementation while ensuring the users are supported with continuing education.
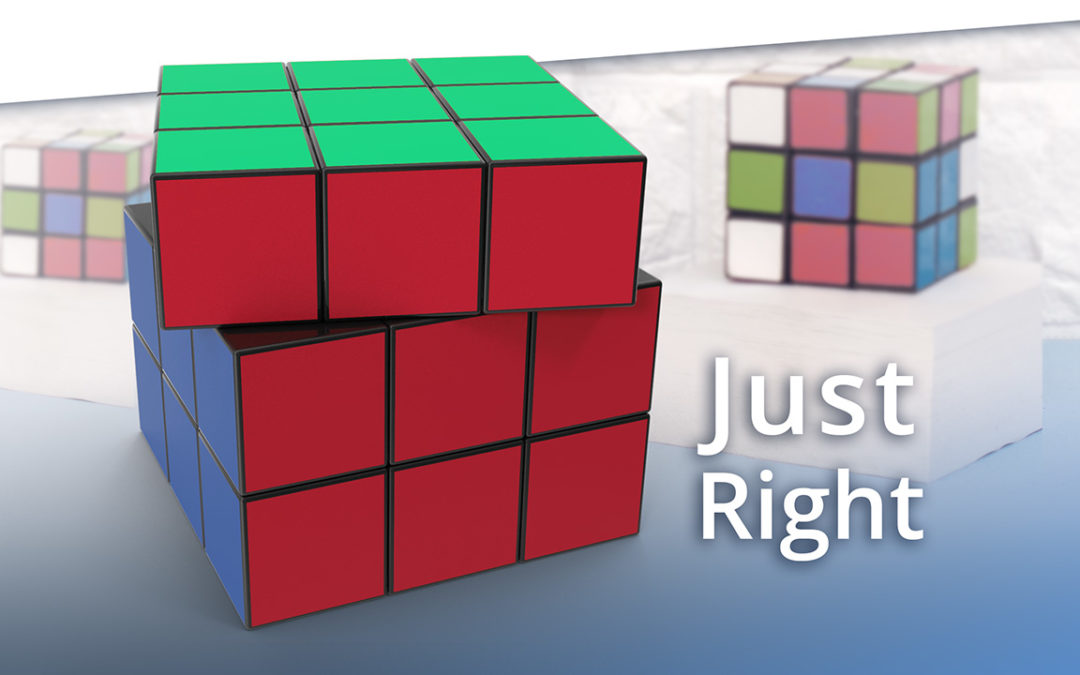
Goldilocks Inventory Levels
You may remember the story of Goldilocks from your long-ago youth. Sometimes the porridge was too hot, sometimes it was too cold, but just once it was just right. Now that we are adults, we can translate that fairy tale into a professional principle for inventory planning: There can be too little or too much inventory, and there is some Goldilocks level that is “just right.” This blog is about finding that sweet spot.
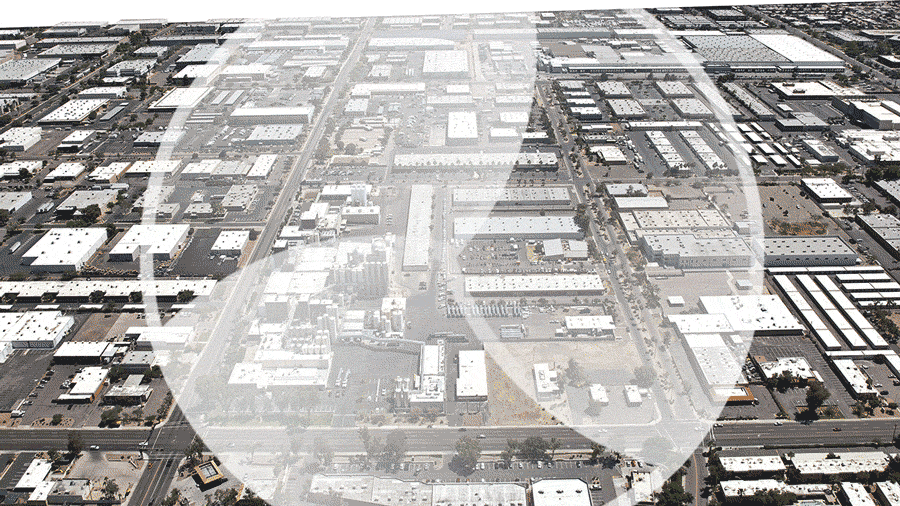
An Example of Simulation-Based Multiechelon Inventory Optimization
Managing the inventory across multiple facilities arrayed in multiple echelons can be a huge challenge for any company. The complexity arises from the interactions among the echelons, with demands at the lower levels bubbling up and any shortages at the higher levels cascading down.
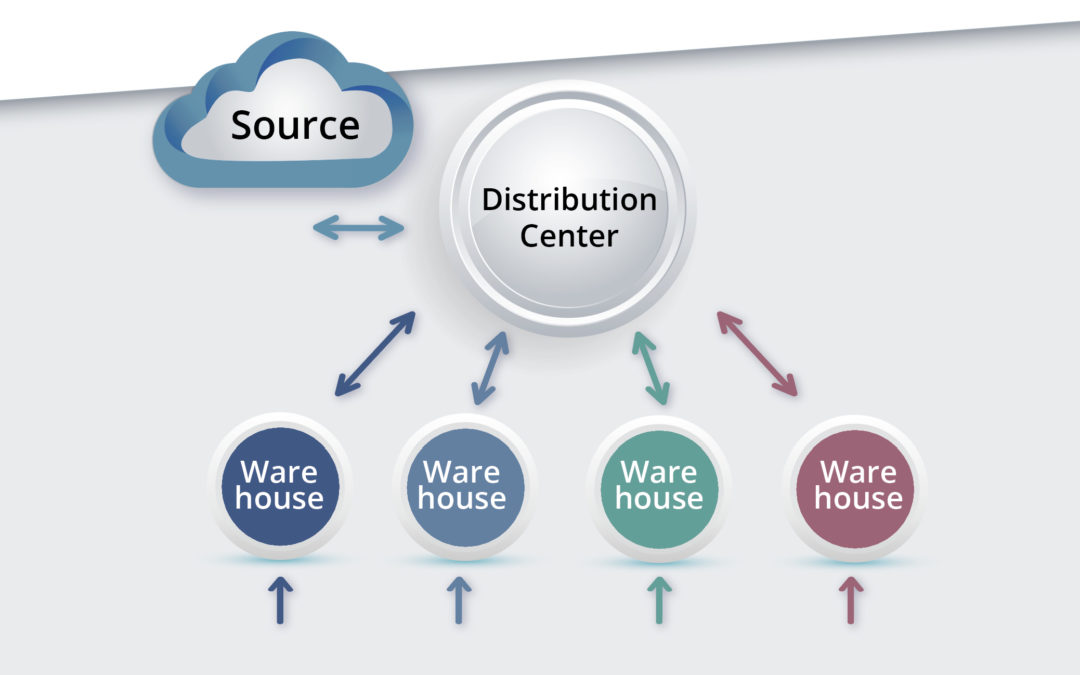
Fact and Fantasy in Multiechelon Inventory Optimization
For most small-to-medium manufacturers and distributors, single-level or single-echelon inventory optimization is at the cutting edge of logistics practice. Multi-echelon inventory optimization (“MEIO”) involves playing the game at an even higher level and is therefore much less common.
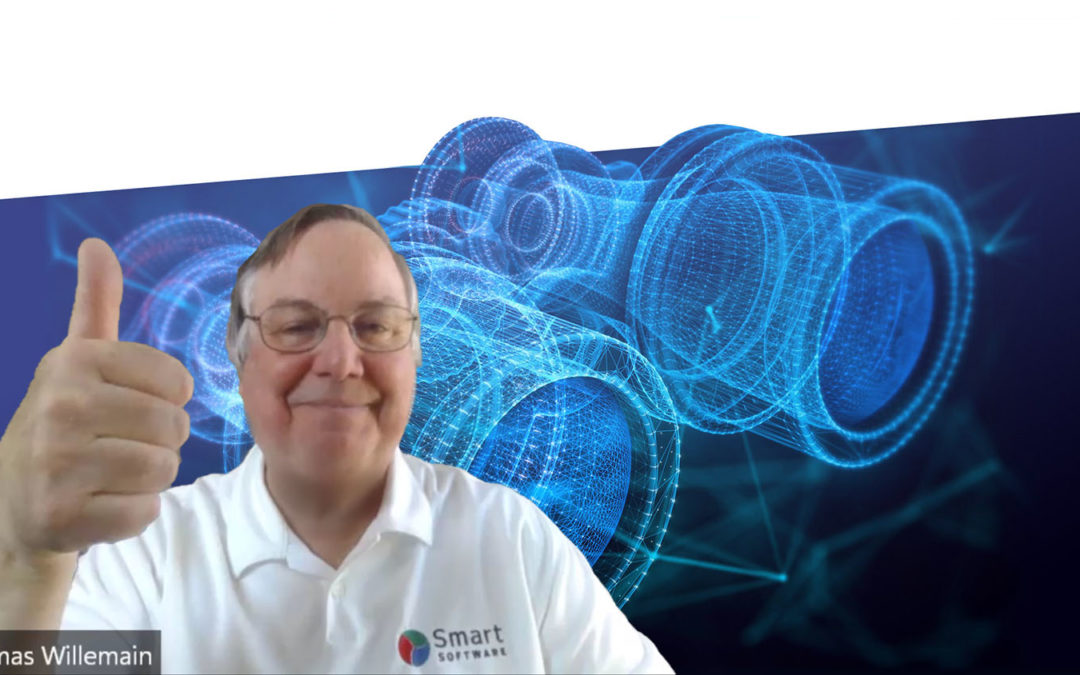
Improve Forecast Accuracy by Managing Error
In this video, Dr. Thomas Willemain, co-Founder and SVP Research, talks about improving Forecast Accuracy by Managing Error. This video is the first in our series on effective methods to Improve Forecast Accuracy. We begin by looking at how forecast error causes pain and the consequential cost related to it. Then we will explain the three most common mistakes to avoid that can help us increase revenue and prevent excess inventory.

Inventory Planning Becomes More Interesting
Just-In-Time (JIT) ensures that a manufacturer produces only the necessary amount, and many companies ignore the risks inherent in reducing inventories. Combined with increased globalization and new risks of supply interruption, stock-outs have abounded. So how can you execute a real-world plan for JIT inventory amidst all this risk and uncertainty? The foundation of your response is your corporate data. Uncertainty has two sources: supply and demand. You need the facts for both.