Improve Forecast Accuracy, Eliminate Excess Inventory, & Maximize Service Levels
In this video, Dr. Thomas Willemain, co-Founder and SVP Research, talks about improving Forecast Accuracy by Managing Error. This video is the first in our series on effective methods to Improve Forecast Accuracy. We begin by looking at how forecast error causes pain and the consequential cost related to it. Then we will explain the three most common mistakes to avoid that can help us increase revenue and prevent excess inventory. Tom concludes by reviewing the methods to improve Forecast Accuracy, the importance of measuring forecast error, and the technological opportunities to improve it.
Forecast error can be consequential
Consider one item of many
- Product X costs $100 to make and nets $50 profit per unit.
- Sales of Product X will turn out to be 1,000/month over the next 12 months.
- Consider one item of many
What is the cost of forecast error?
- If the forecast is 10% high, end the year with $120,000 of excess inventory.
- 100 extra/month x 12 months x $100/unit
- If the forecast is 10% low, miss out on $60,000 of profit.
- 100 too few/month x 12 months x $50/unit
Three mistakes to avoid
1. Ignoring error.
- Unprofessional, dereliction of duty.
- Wishing will not make it so.
- Treat accuracy assessment as data science, not a blame game.
2. Tolerating more error than necessary.
- Statistical forecasting methods can improve accuracy at scale.
- Improving data inputs can help.
- Collecting and analyzing forecast error metrics can identify weak spots.
3. Wasting time and money going too far trying to eliminate error.
- Some product/market combinations are inherently more difficult to forecast. After a point, let them be (but be alert for new specialized forecasting methods).
- Sometimes steps meant to reduce error can backfire (e.g., adjustment).
RECENT POSTS
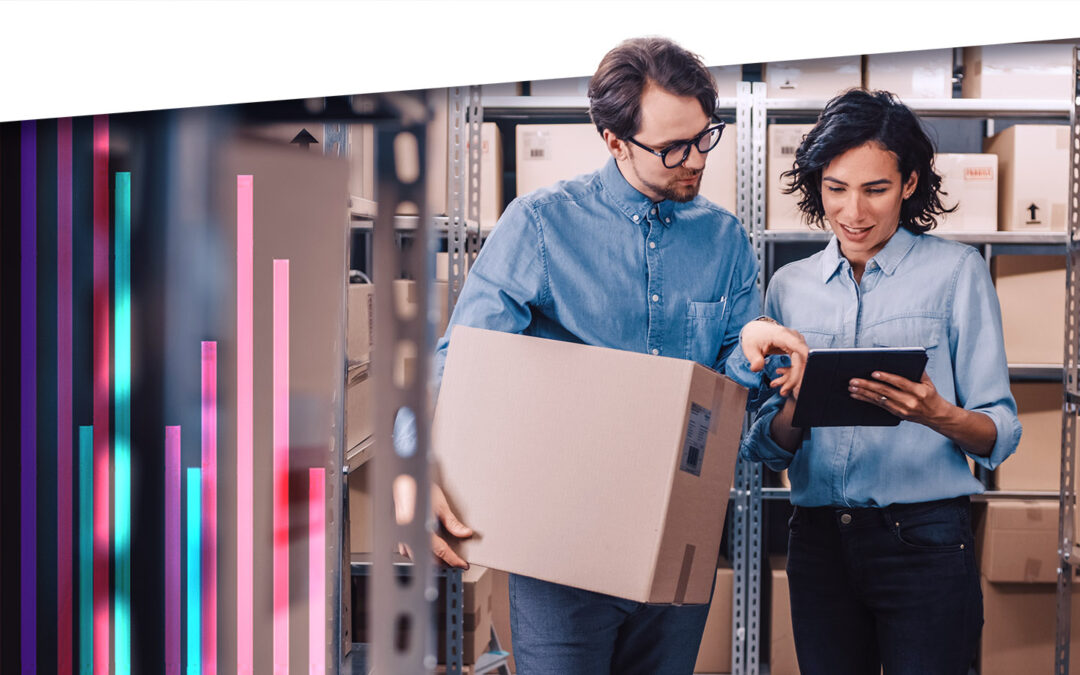
Forecast-Based Inventory Management for Better Planning
Forecast-based inventory management, or MRP (Material Requirements Planning) logic, is a forward-planning method that helps businesses meet demand without overstocking or understocking. By anticipating demand and adjusting inventory levels, it maintains a balance between meeting customer needs and minimizing excess inventory costs. This approach optimizes operations, reduces waste, and enhances customer satisfaction.
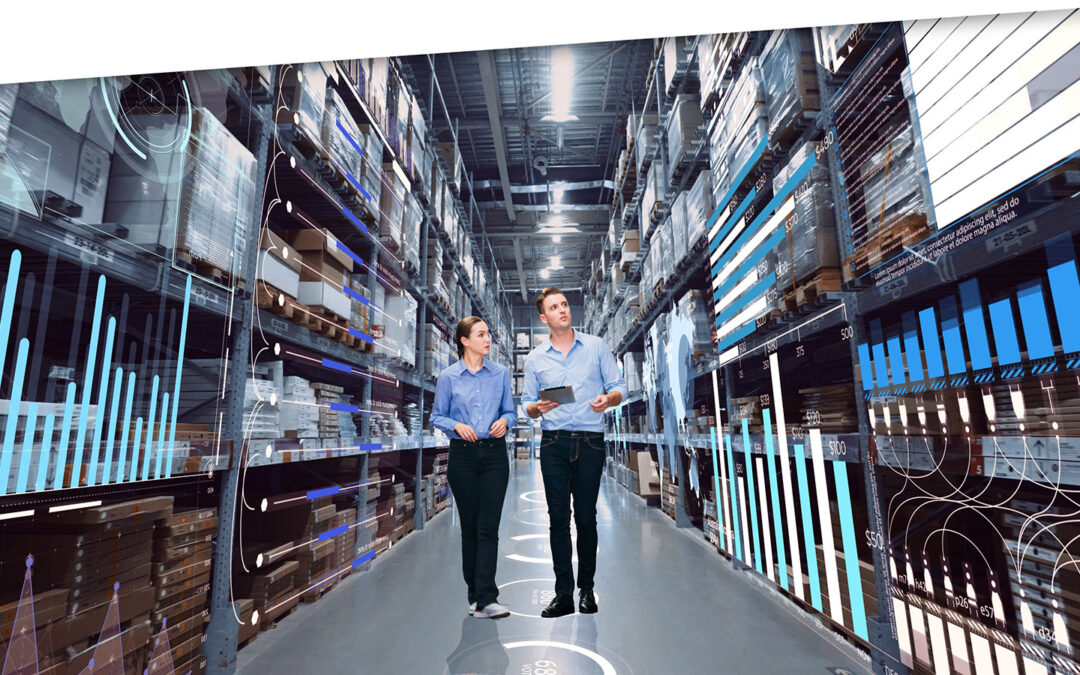
Make AI-Driven Inventory Optimization an Ally for Your Organization
In this blog, we will explore how organizations can achieve exceptional efficiency and accuracy with AI-driven inventory optimization. Traditional inventory management methods often fall short due to their reactive nature and reliance on manual processes. Maintaining optimal inventory levels is fundamental for meeting customer demand while minimizing costs. The introduction of AI-driven inventory optimization can significantly reduce the burden of manual processes, providing relief to supply chain managers from tedious tasks.
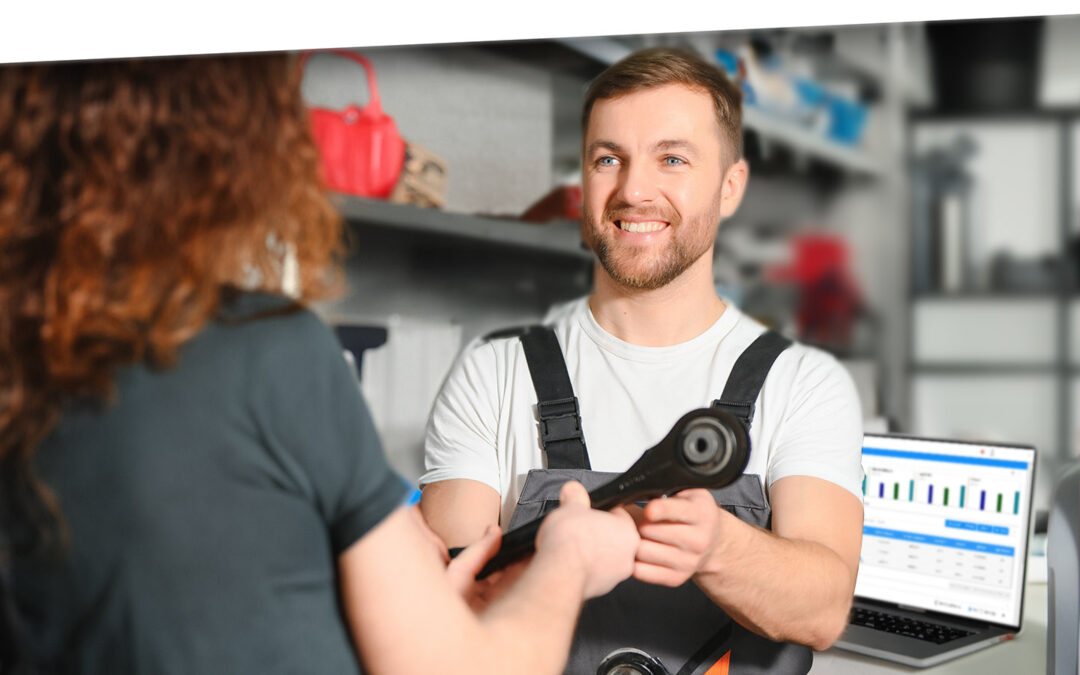
The Importance of Clear Service Level Definitions in Inventory Management
Inventory optimization software that supports what-if analysis will expose the tradeoff of stockouts vs. excess costs of varying service level targets. But first it is important to identify how “service levels” is interpreted, measured, and reported. This will avoid miscommunication and the false sense of security that can develop when less stringent definitions are used. Clearly defining how service level is calculated puts all stakeholders on the same page. This facilitates better decision-making.