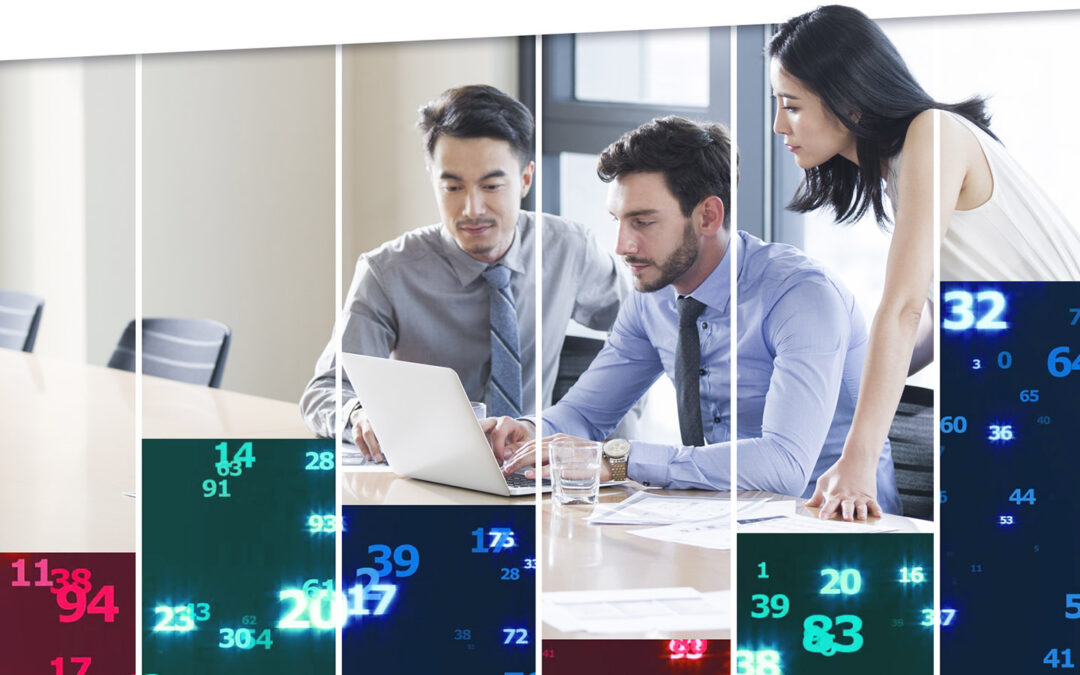
Creating and Exploiting Probabilistic Forecasting Scenarios
Probabilistic scenarios are sequences of data points generated to represent potential real-world situations. Unlike scenarios in war games or other simulations, these are synthetic time series used as inputs to system models or as intuition-builders for decision-makers.
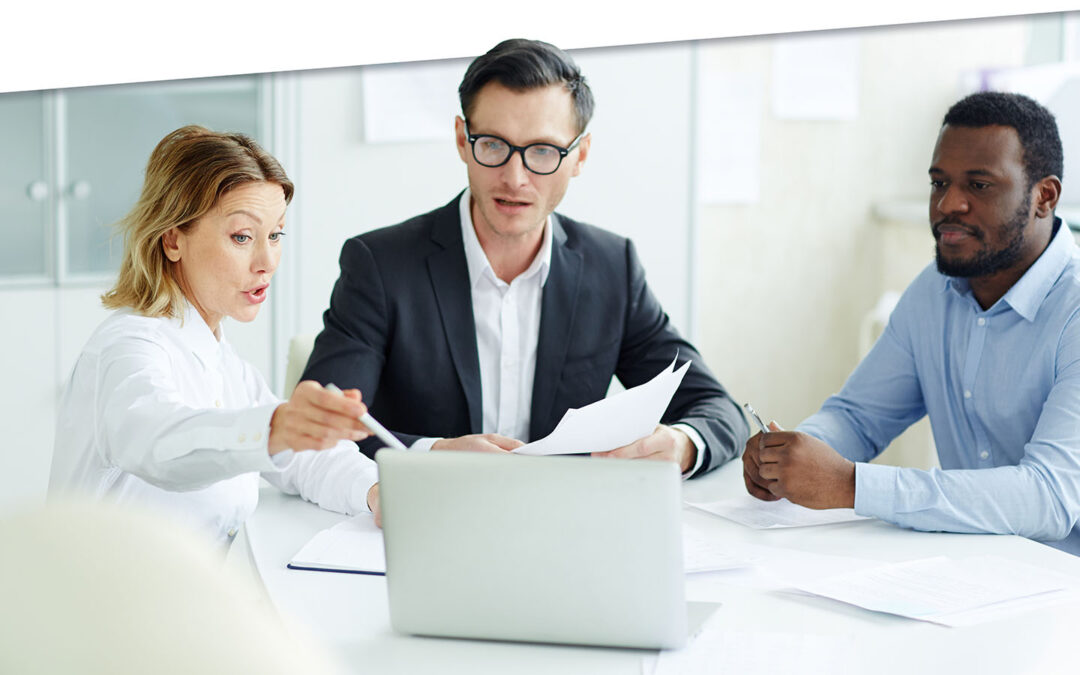
A Rough Map of Forecasting-Related Terms
People new to the jobs of “demand planner” or “supply planner” are likely to have questions about the various forecasting terms and methods used in their jobs. This note may help by explaining these terms and showing how they relate.
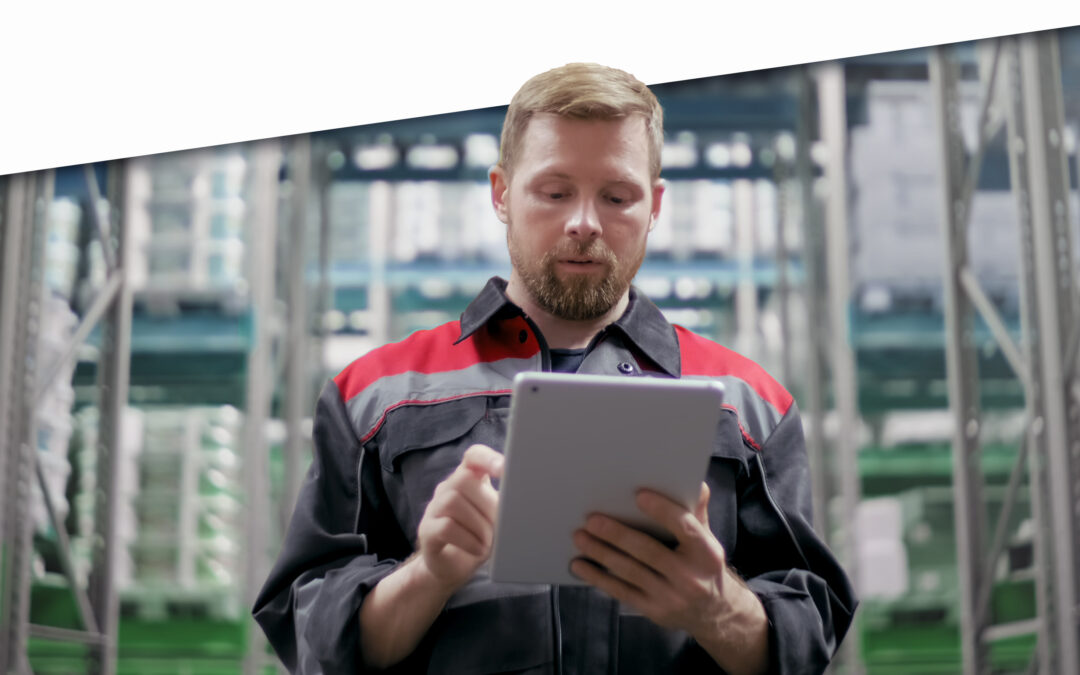
How Are We Doing? KPI’s and KPP’s
Dealing with the day-to-day of inventory management can keep you busy. But you know you have to get your head up now and then to see where you’re heading. For that, your inventory software should show you metrics – and not just one, but a full set of metrics or KPI’s – Key Performance Indicators.

What is Inventory Planning? A Brief Dictionary of Inventory-Related Terms
People involved in the supply chain are likely to have questions about various inventory terms and methods used in their jobs. This note may help by explaining these terms and showing how they relate.
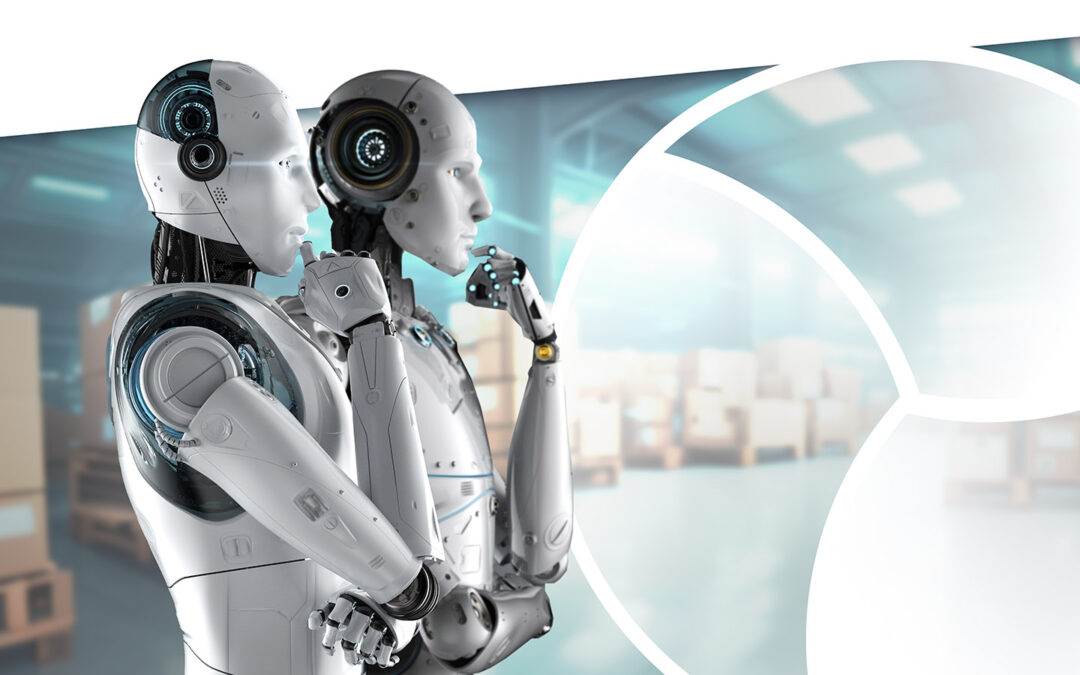
Confused about AI and Machine Learning?
Are you confused about what is AI and what is machine learning? Are you unsure why knowing more will help you with your job in inventory planning? Don’t despair. You’ll be ok, and we’ll show you how some of whatever-it-is can be useful.
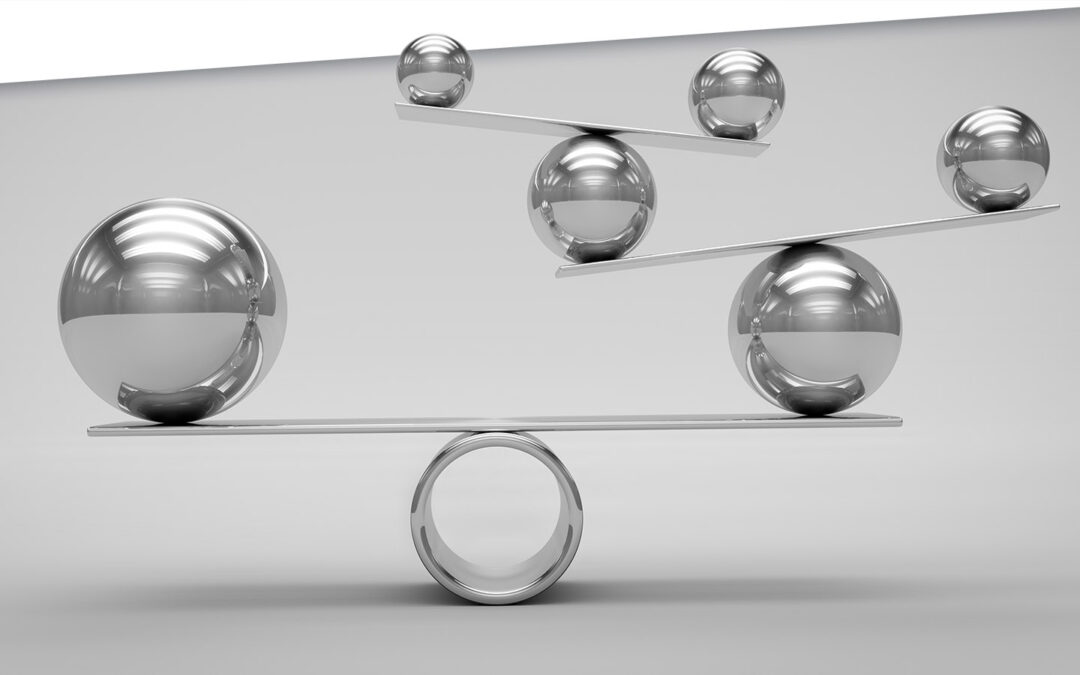
How to Forecast Inventory Requirements
Forecasting inventory requirements is a specialized variant of forecasting that focuses on the high end of the range of possible future demand. Traditional methods often rely on bell-shaped demand curves, but this isn’t always accurate. In this article, we delve into the complexities of this practice, especially when dealing with intermittent demand.
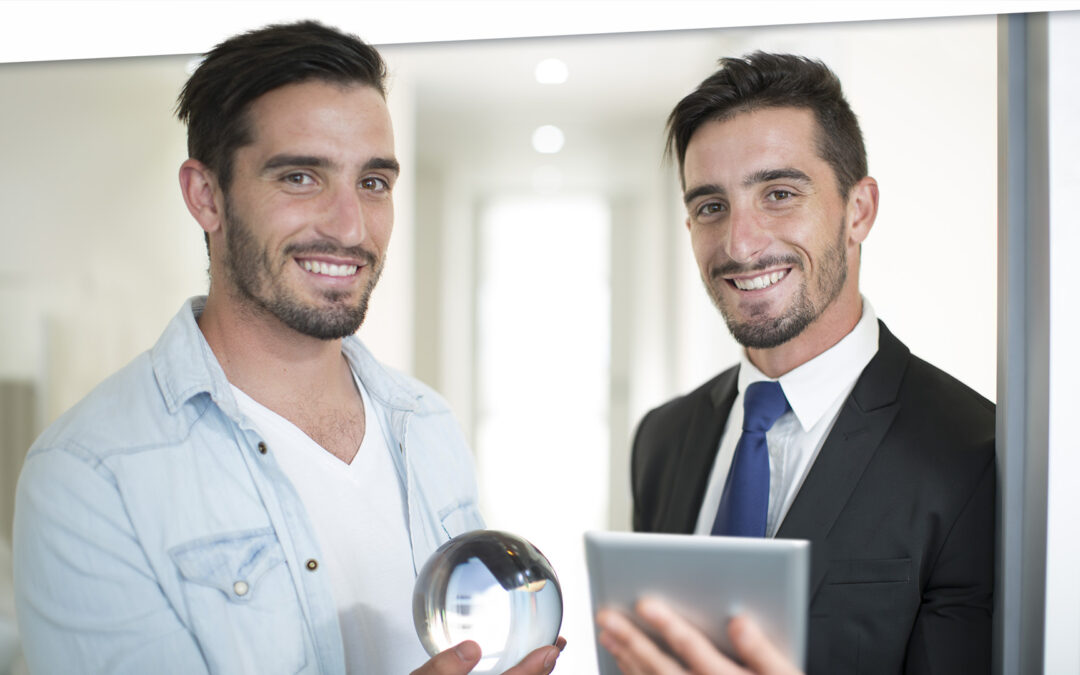
Six Demand Planning Best Practices You Should Think Twice About
Every field, including forecasting, accumulates folk wisdom that eventually starts masquerading as “best practices.” These best practices are often wise, at least in part, but they often lack context and may not be appropriate for certain customers, industries, or business situations. There is often a catch, a “Yes, but”. This note is about six usually true forecasting precepts that nevertheless do have their caveats.
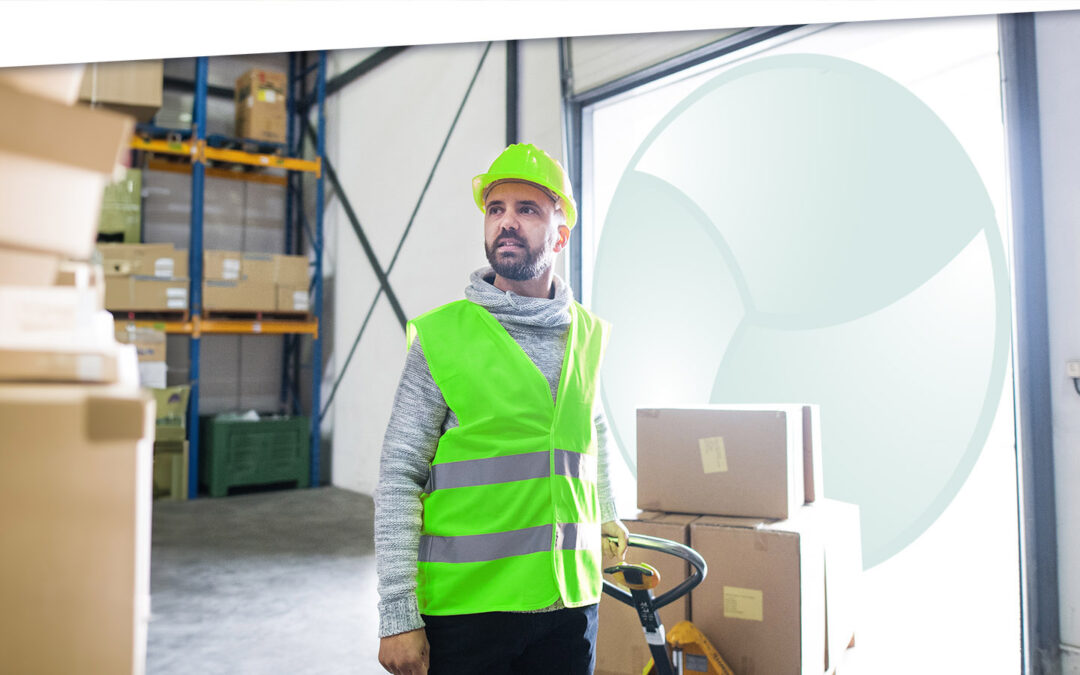
Explaining What “Service Level” Means in Your Inventory Optimization Software
Navigating the intricacies of stocking recommendations can often lead to questions about their accuracy and significance. A recent inquiry from one of our customers prompted an insightful discussion on the nuances of service levels and reorder points. During a team meeting, we identified unusual gaps between our Smart-suggested reorder points (ROP) at a 99% service level and the customer’s current ROP. In this post, we unravel the concept of a “99% service level” and its implications for inventory optimization, shedding light on how timing and immediate stock availability play pivotal roles in meeting customer expectations and remaining competitive in diverse industries.
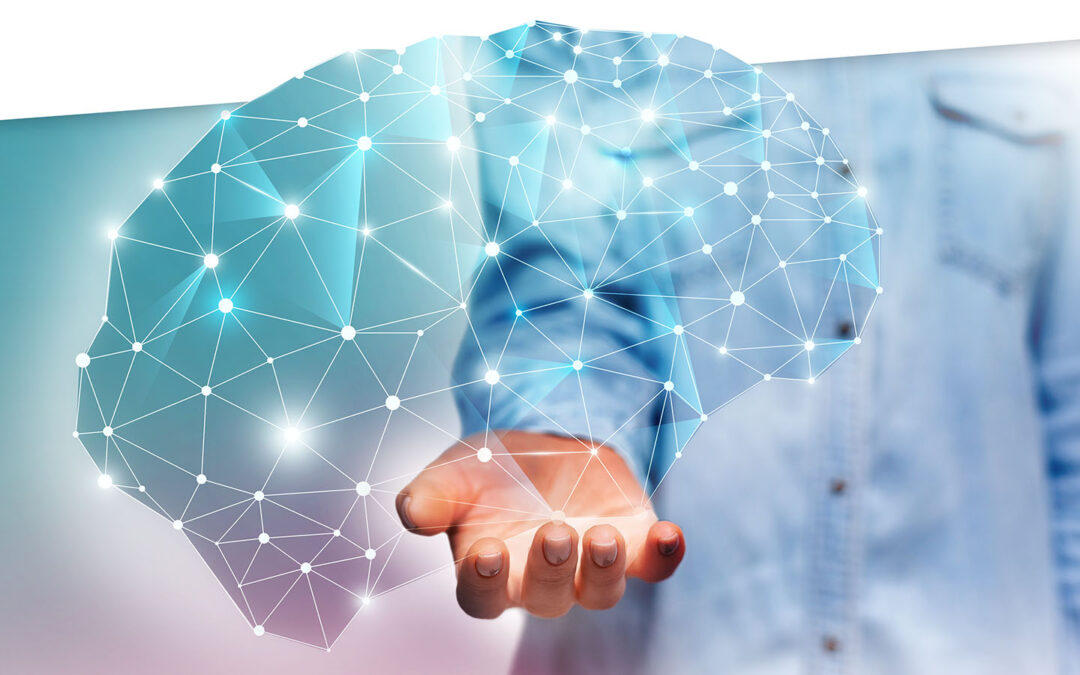
The Automatic Forecasting Feature
Automatic forecasting is the most popular and most used feature of SmartForecasts and Smart Demand Planner. Creating Automatic forecasts is easy. But, the simplicity of Automatic Forecasting masks a powerful interaction of a number of highly effective methods of forecasting. In this blog, we discuss some of the theory behind this core feature. We focus on Automatic forecasting, in part because of its popularity and in part because many other forecasting methods produce similar outputs. Knowledge of Automatic forecasting immediately carries over to Simple Moving Average, Linear Moving Average, Single Exponential Smoothing, Double Exponential Smoothing, Winters’ Exponential Smoothing, and Promo forecasting.
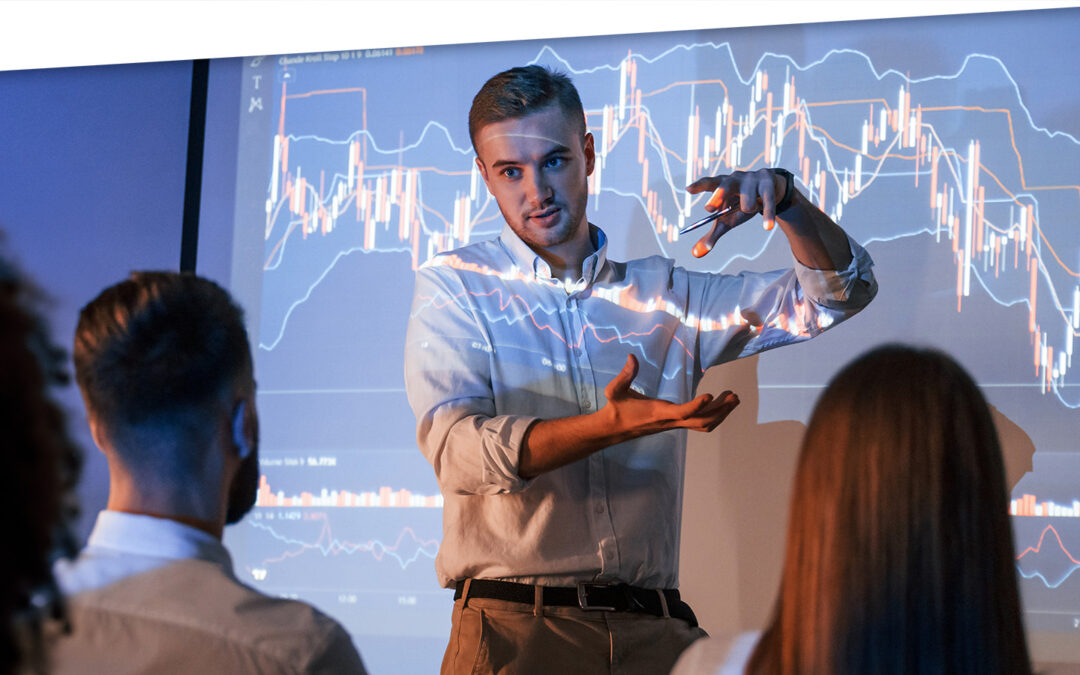
The Objectives in Forecasting
A forecast is a prediction about the value of a time series variable at some time in the future. For instance, one might want to estimate next month’s sales or demand for a product item. A time series is a sequence of numbers recorded at equally spaced time intervals; for example, unit sales recorded every month. The objectives you pursue when you forecast depend on the nature of your job and your business. Every forecast is uncertain; in fact, there is a range of possible values for any variable you forecast. Values near the middle of this range have a higher likelihood of actually occurring, while values at the extremes of the range are less likely to occur.
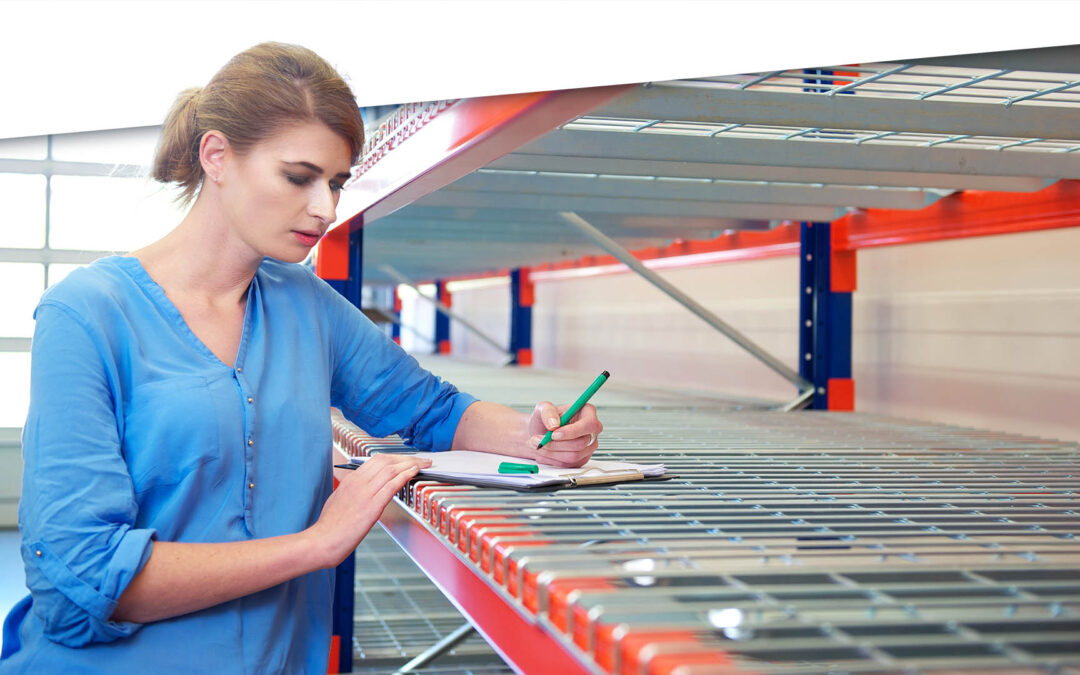
Don’t blame shortages on problematic lead times.
Lead time delays and supply variability are supply chain facts of life, yet inventory-carrying organizations are often caught by surprise when a supplier is late. An effective inventory planning process embraces this fact of life and develops policies that effectively account for this uncertainty. Sure, there will be times when lead time delays come out of nowhere and cause a shortage. But most often, the shortages result from:
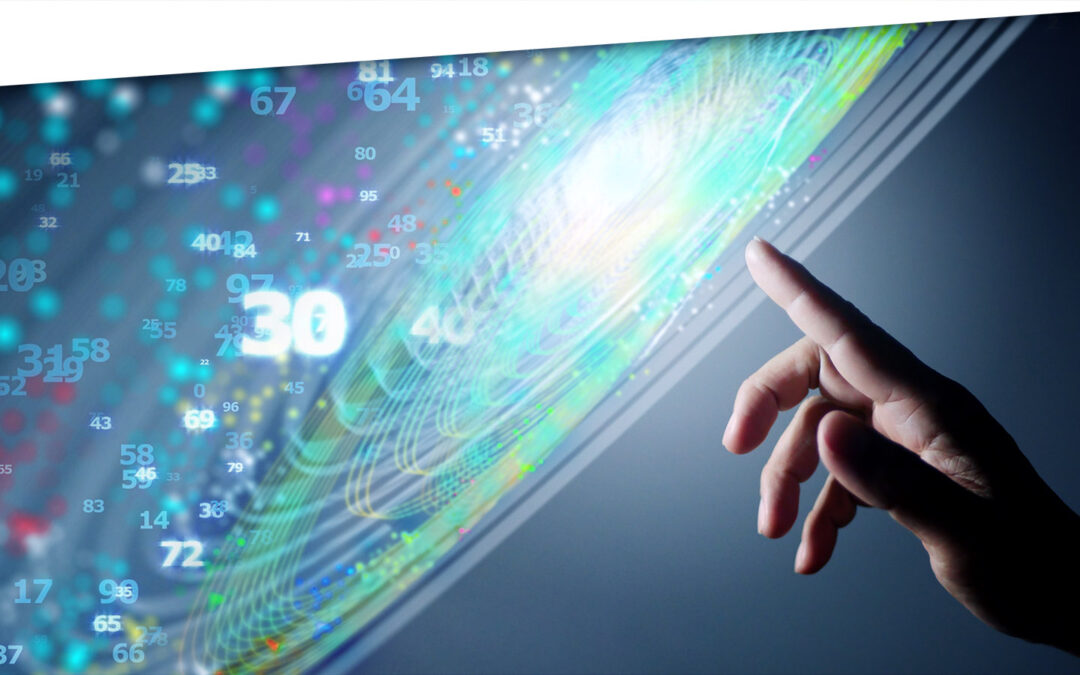
A Gentle Introduction to Two Advanced Techniques: Statistical Bootstrapping and Monte Carlo Simulation
Smart Software’s advanced supply chain analytics exploits multiple advanced methods. Two of the most important are “statistical bootstrapping” and “Monte Carlo simulation”. Since both involve lots of random numbers flying around, folks sometimes get confused about which is which and what they are good for. Hence, this note. Bottom line up front: Statistical bootstrapping generates demand scenarios for forecasting. Monte Carlo simulation uses the scenarios for inventory optimization.
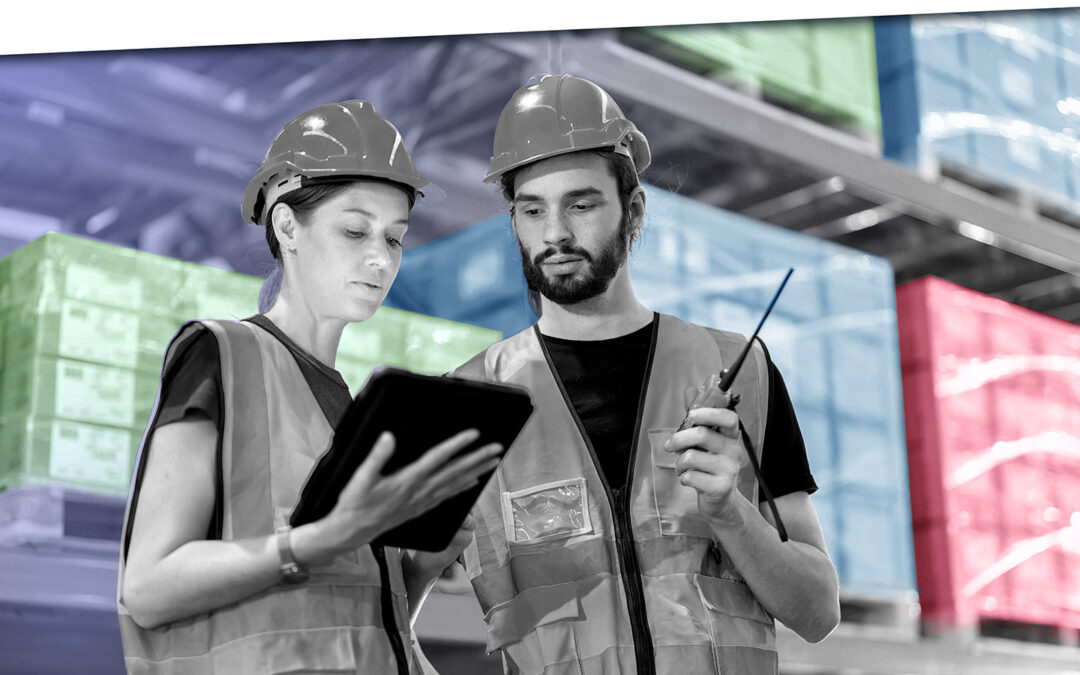
How does your ERP system treat safety stock?
Is safety stock regarded as emergency spares or as a day-to-day buffer against spikes in demand? Knowing the difference and configuring your ERP properly will greatly benefit your bottom line. It is critical to understand how your ERP configurations will impact treatment of safety stock and replenishment orders/production job suggestions. Doing so ensures that unintended mistakes that cause inventory bloat and shortages can be avoided.

Bottom Line Strategies for Spare Parts Planning
Managing spare parts presents numerous challenges, such as unexpected breakdowns, changing schedules, and inconsistent demand patterns. Traditional forecasting methods and manual approaches are ineffective in dealing with these complexities. To overcome these challenges, this blog outlines key strategies that prioritize service levels, utilize probabilistic methods to calculate reorder points, regularly adjust stocking policies, and implement a dedicated planning process to avoid excessive inventory. Explore these strategies to optimize spare parts inventory and improve operational efficiency.
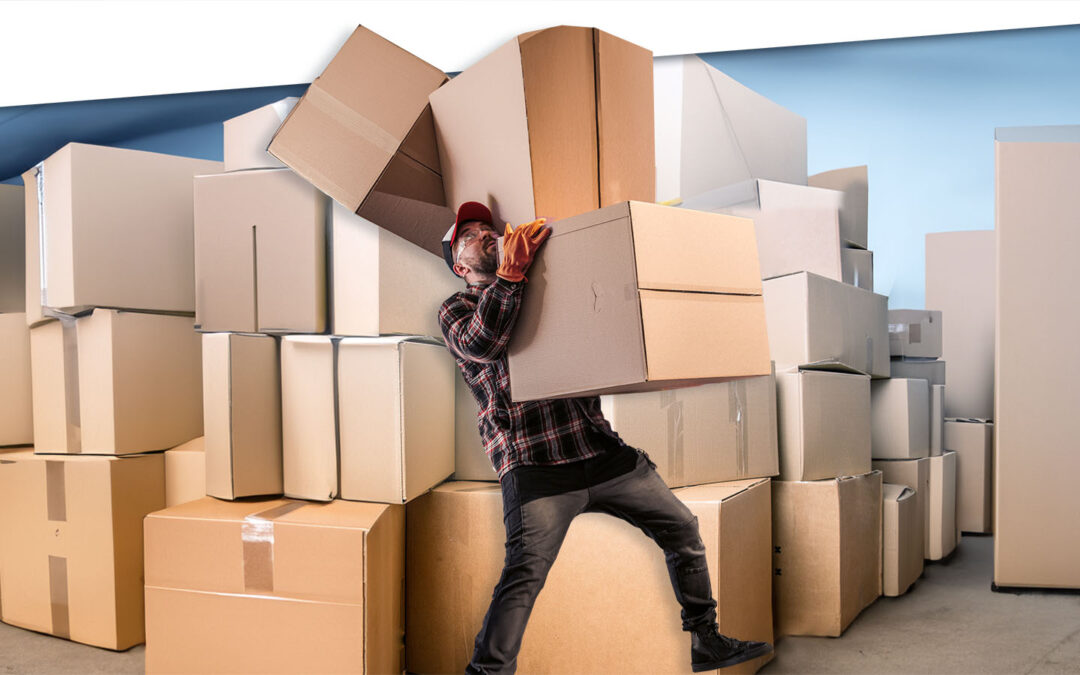
Top 4 Moves When You Suspect Software is Inflating Inventory
Discover the key strategies to tackle inventory inflation caused by software in your supply chain. We often are asked, “Why is the software driving up the inventory?” The answer is that Software isn’t driving it in either direction – the inputs are driving it, and those inputs are controlled by the users (or admins). Here are four things you can do to get results you expect.