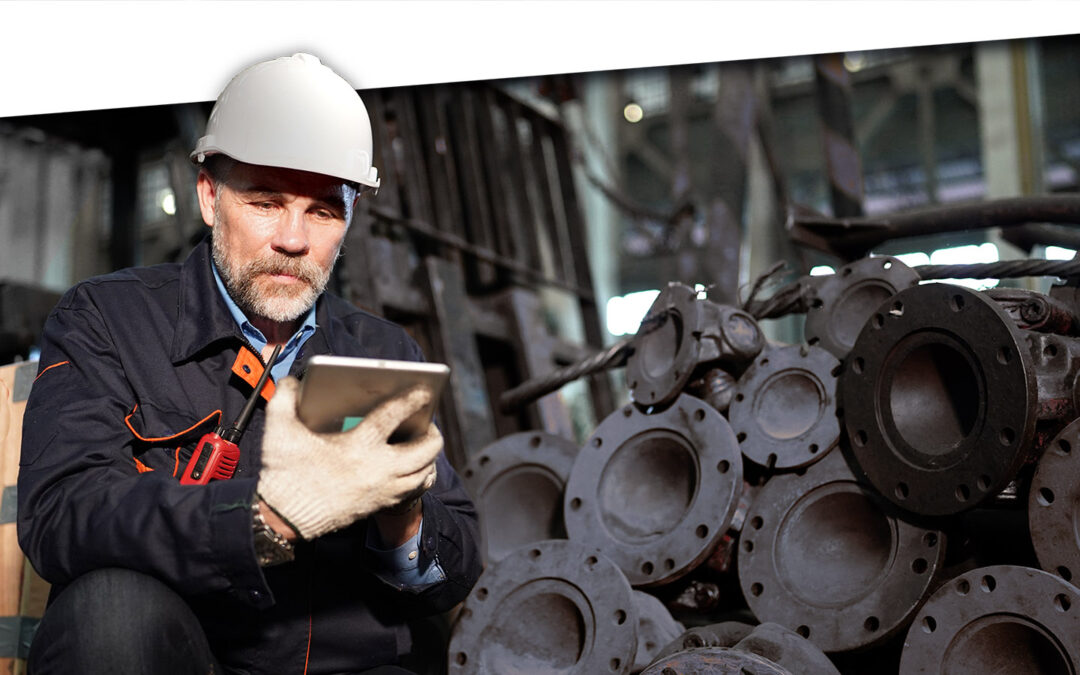
6 Do’s and Don’ts for Spare Parts Planning
Managing spare parts inventories can feel impossible. You don’t know what will break and when. Feedback from mechanical departments and maintenance teams is often inaccurate. Planned maintenance schedules are often shifted around, making them anything but “planned.” Usage (i.e., demand) patterns are most often extremely intermittent, i.e., demand jumps randomly between zero and something else, often a surprisingly big number.
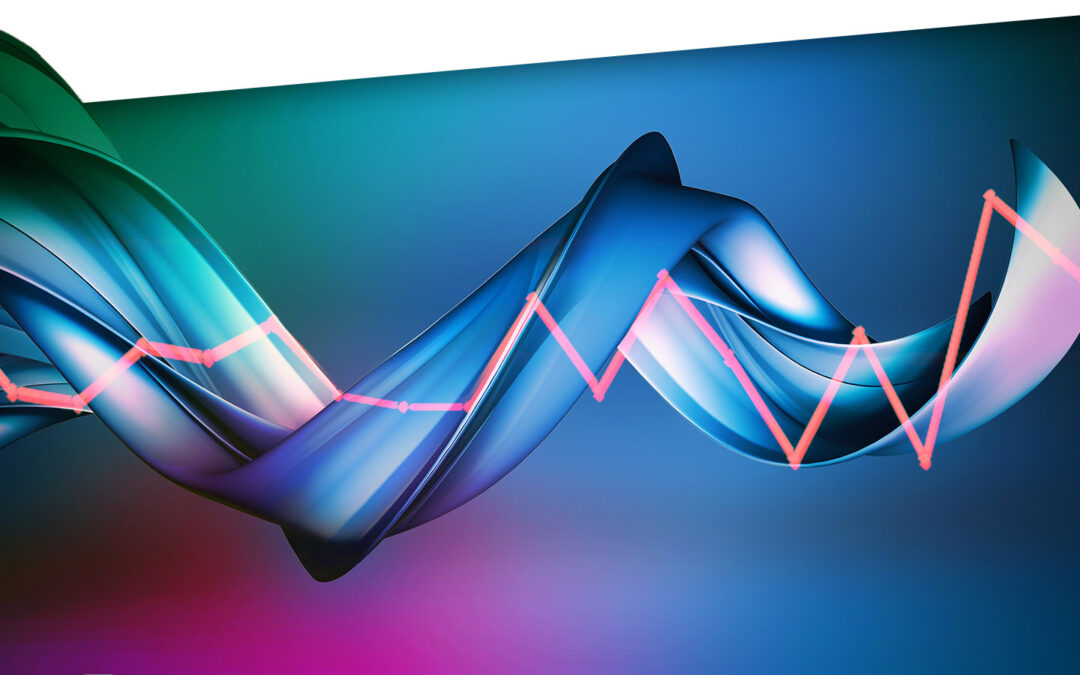
Do your statistical forecasts suffer from the wiggle effect?
What is the wiggle effect? It’s when your statistical forecast incorrectly predicts the ups and downs observed in your demand history when there really isn’t a pattern. It’s important to make sure your forecasts don’t wiggle unless there is a real pattern. Here is a transcript from a recent customer where this issue was discussed:
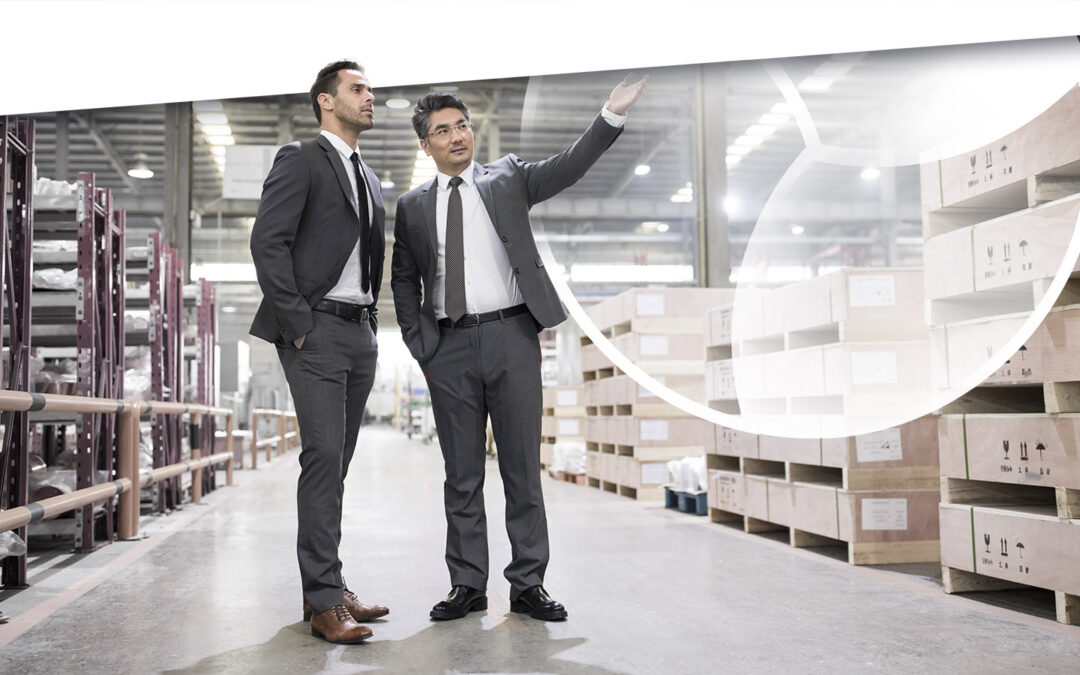
Extend Microsoft 365 F&SC and AX with Smart IP&O
Microsoft Dynamics 365 F&SC and AX can manage replenishment by suggesting what to order and when via reorder point-based inventory policies. A challenge that customers face is that efforts to maintain these levels are very detailed oriented and that the ERP system requires that the user manually specify these reorder points and/or forecasts. In this article, we will review the inventory ordering functionality in AX / D365 F&SC, explain its limitations, and summarize how to reduce inventory, minimize and controlle stockouts.
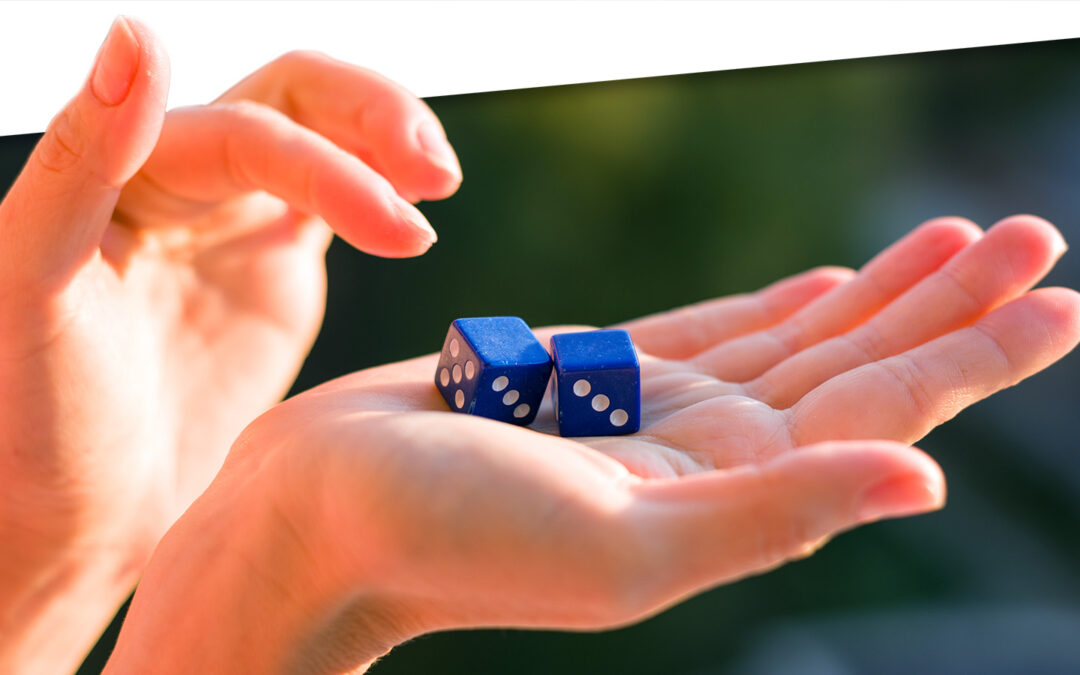
How to Handle Statistical Forecasts of Zero
A statistical forecast of zero can cause lots of confusion for forecasters, especially when the historical demand is non-zero. Sure, it’s obvious that demand is trending downward, but should it trend to zero?

Probabilistic Forecasting for Intermittent Demand
The New Forecasting Technology derives from Probabilistic Forecasting, a statistical method that accurately forecasts both average product demand per period and customer service level inventory requirements.
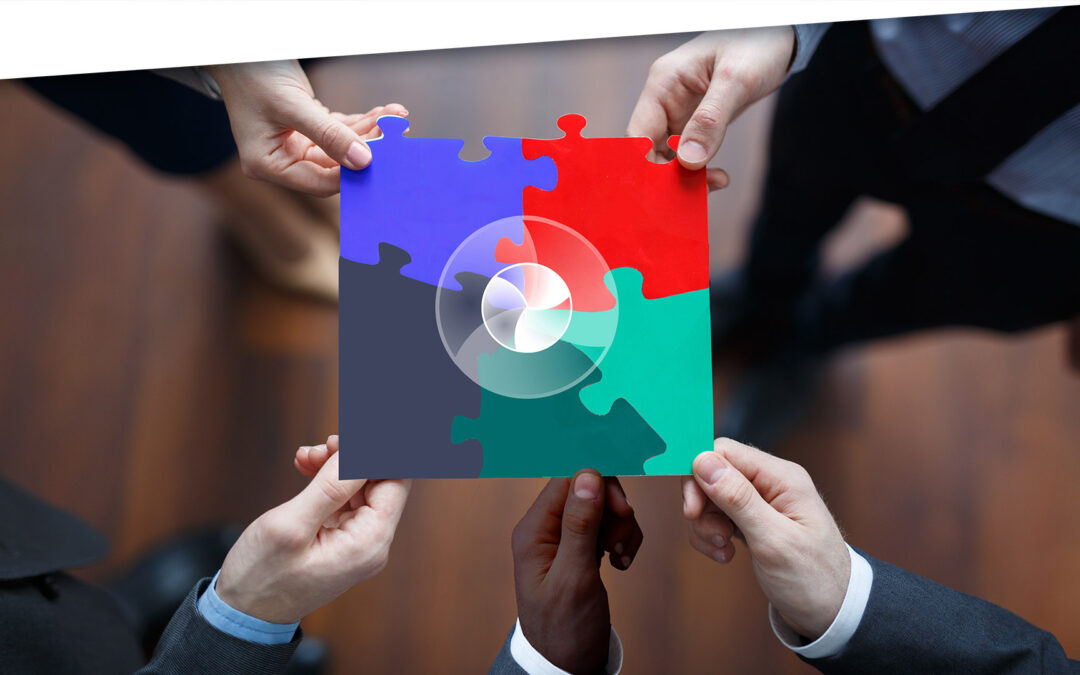
Beyond the forecast – Collaboration and Consensus Planning
The whole point of demand forecasting is to establish the best possible view of future demand. This requires that we draw upon the best data and inputs we can get, leverage statistics to capture underlying patterns, put our heads together to apply overrides based on business knowledge, and agree on a consensus demand plan that serves as cornerstone to the company’s overall demand plan.
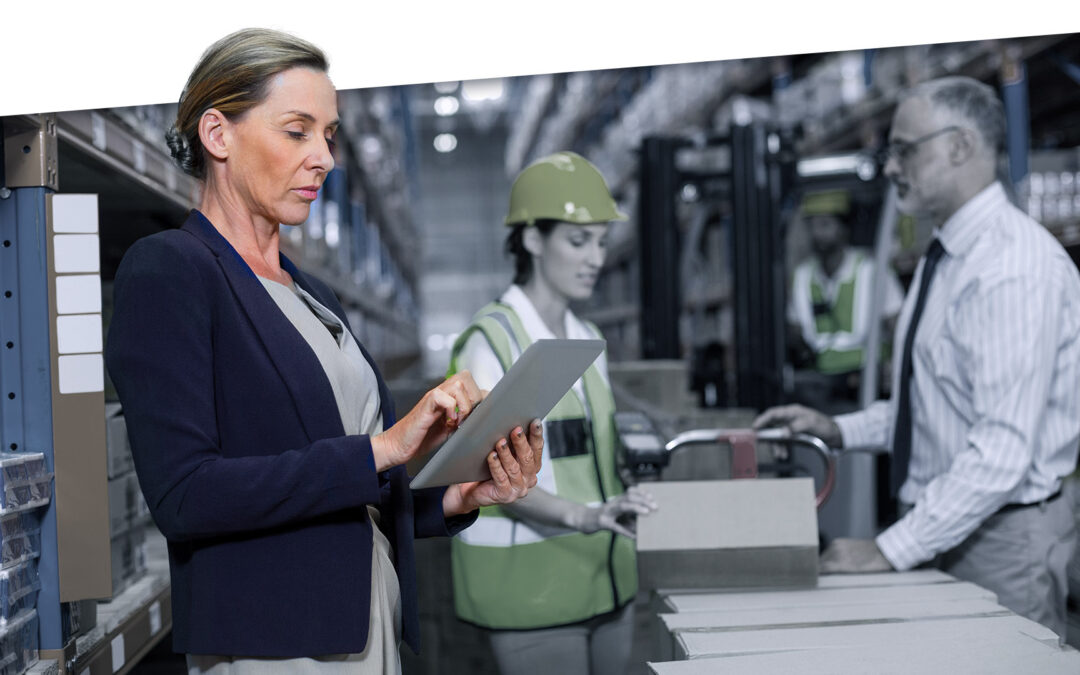
Why Days of Supply Targets Don’t Work when Computing Safety Stocks
CFOs tell us they need to spend less on inventory without impacting sales. One way to do that is to move away from using targeted day of supply rules to determine reorder points and safety stock buffers. Here is how a target days of supply/coverage approach works:
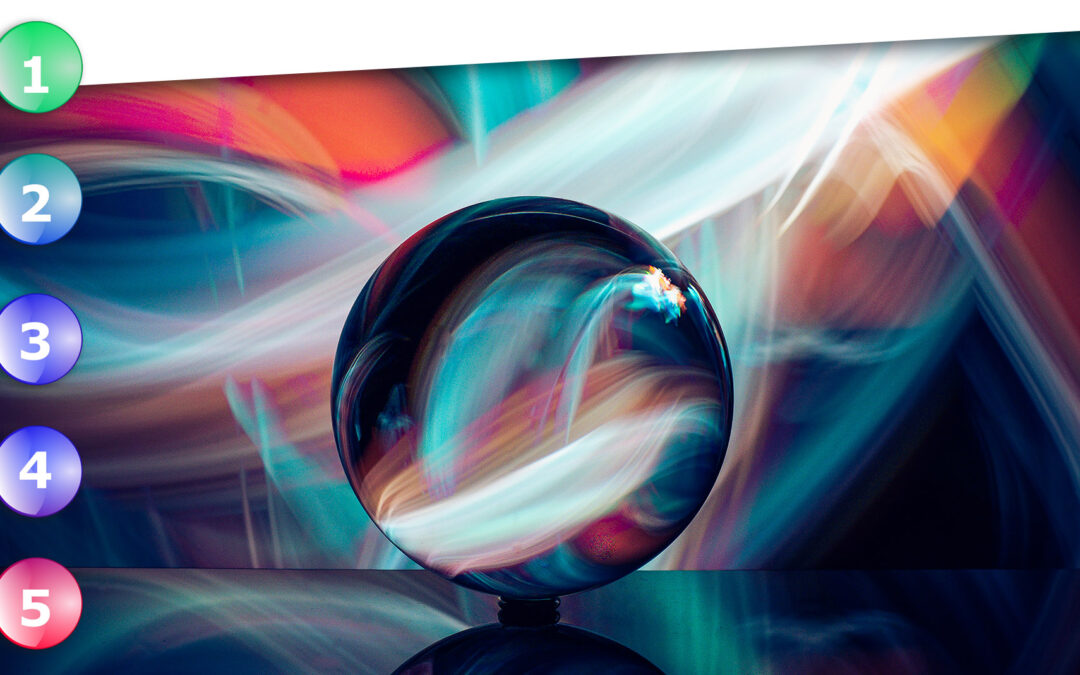
5 Tips for Creating Smart Forecasts
Many companies use the term “smart forecasting” or “smart forecasts” without firm justification. Let’s distinguish between the Smart brand and being smart about the way you do your forecasting work. Demand forecasting is a critical part of the demand planning and S&OP process. Here are 5 tips that will help you execute your forecasts intelligently.
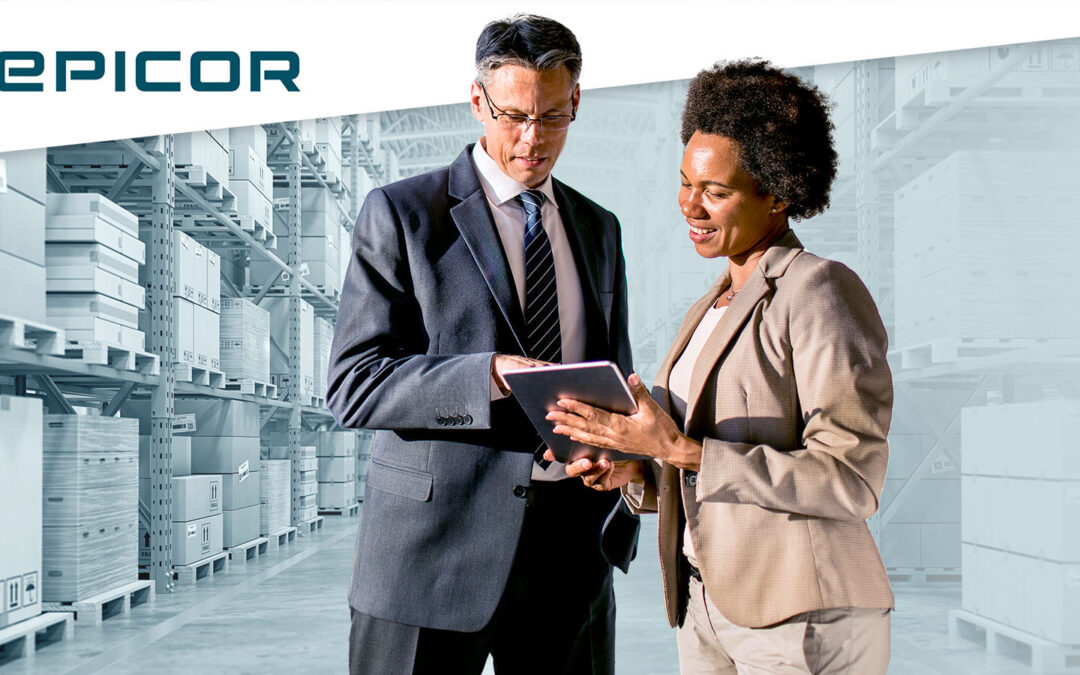
Extend Epicor Prophet 21 with Smart IP&O’s Forecasting & Dynamic Reorder Point Planning
Smart Inventory Planning & Optimization (Smart IP&O) can help with inventory ordering functionality in Epicor P21, reduce inventory, minimize stockouts and restore your organization’s trust by providing robust predictive analytics, consensus-based forecasting, and what-if scenario planning.
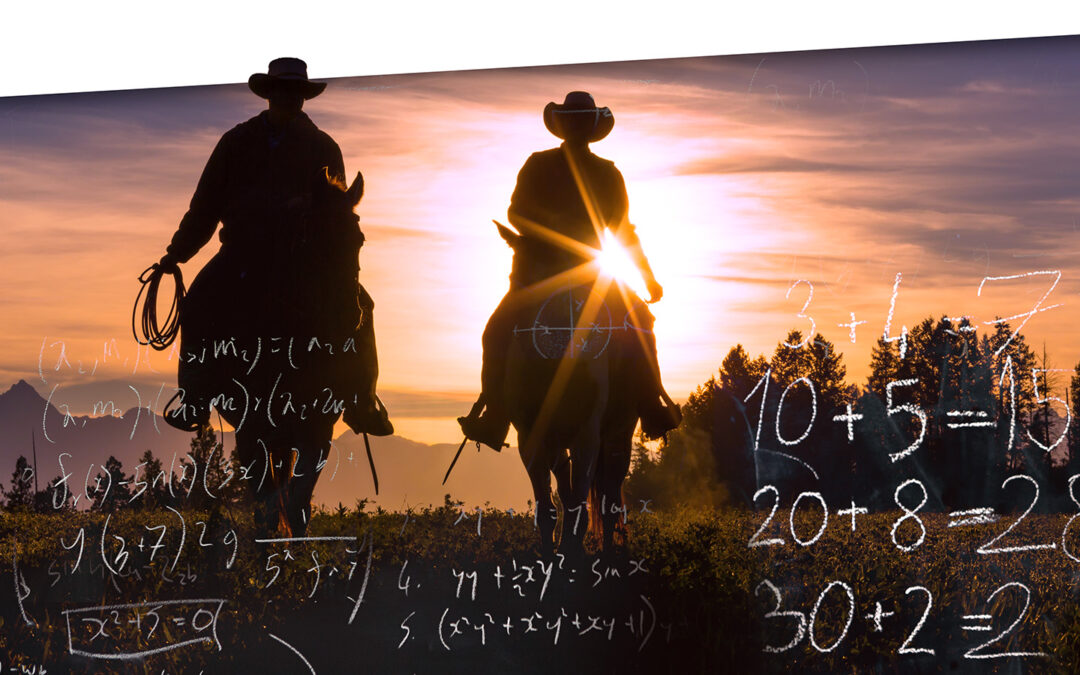
Supply Chain Math: Don’t Bring a Knife to a Gunfight
Math and the supply chain go hand and hand. As supply chains grow, increasing complexity will drive companies to look for ways to manage large-scale decision-making. Math is a fact of life for anyone in inventory management and demand forecasting who is hoping to remain competitive in the modern world. Read our article to learn more.
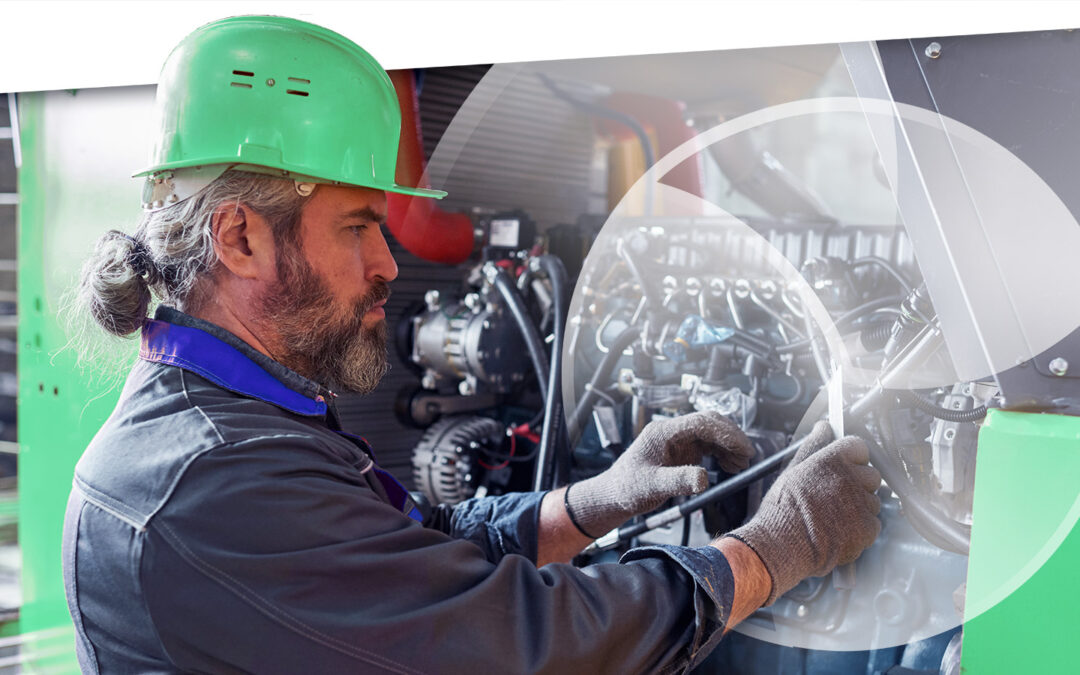
Service Parts Planning: Planning for consumable parts vs. Repairable Parts
When deciding on the right stocking parameters for spare and replacement parts, it is important to distinguish between consumable and repairable servoce parts. These differences are often overlooked by inventory planning software and can result in incorrect estimates of what to stock. Different approaches are required when planning for consumables vs. repairable service parts.
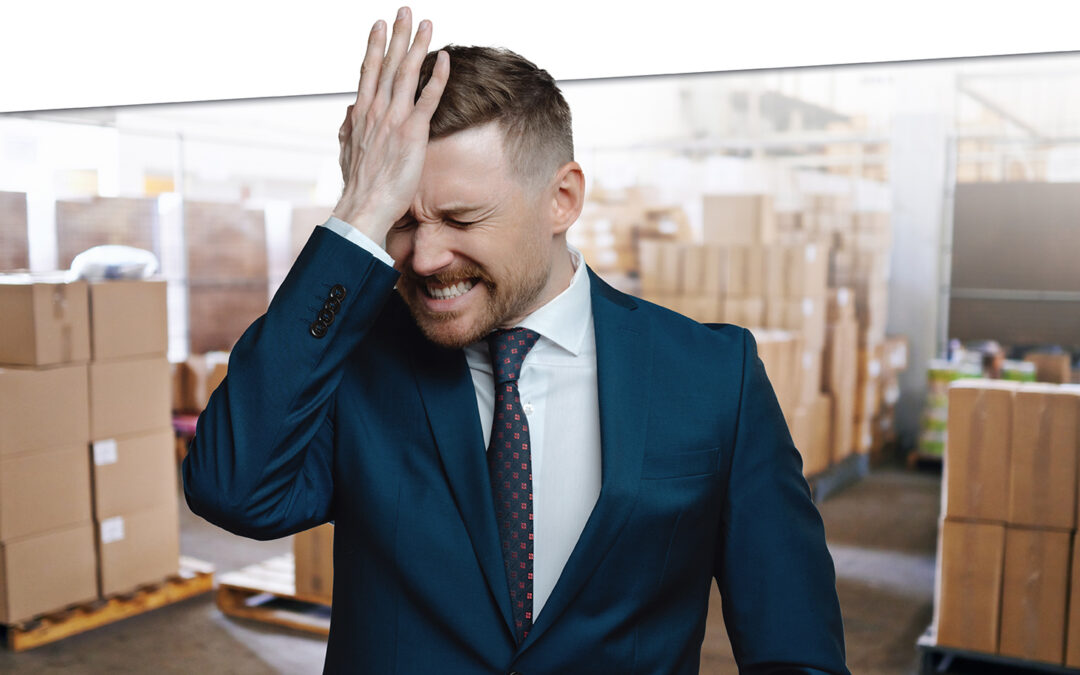
Four Common Mistakes when Planning Replenishment Targets
How often do you recalibrate your stocking policies? Why? Learn how to avoid key mistakes when planning replenishment targets by automating the process, recalibrating parts, using targeting forecasting methods, and reviewing exceptions.
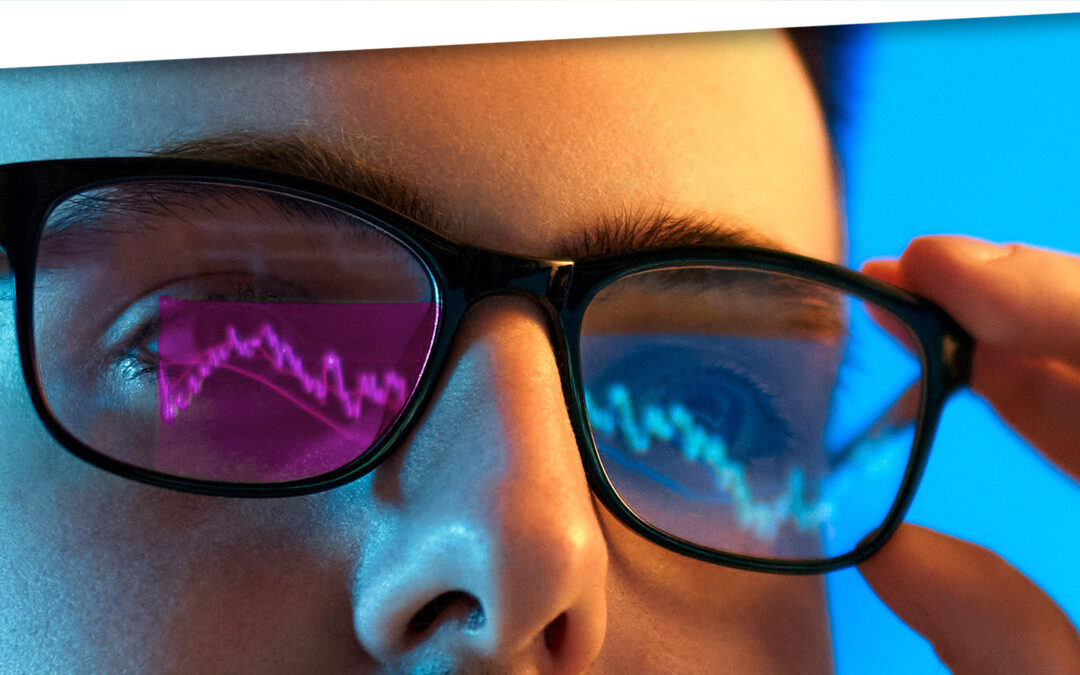
Managing Inventory amid Regime Change
If you hear the phrase “regime change” on the news, you immediately think of some fraught geopolitical event. Statisticians use the phrase differently, in a way that has high relevance for demand planning and inventory optimization. This blog is about “regime change” in the statistical sense, meaning a major change in the character of the demand for an inventory item.
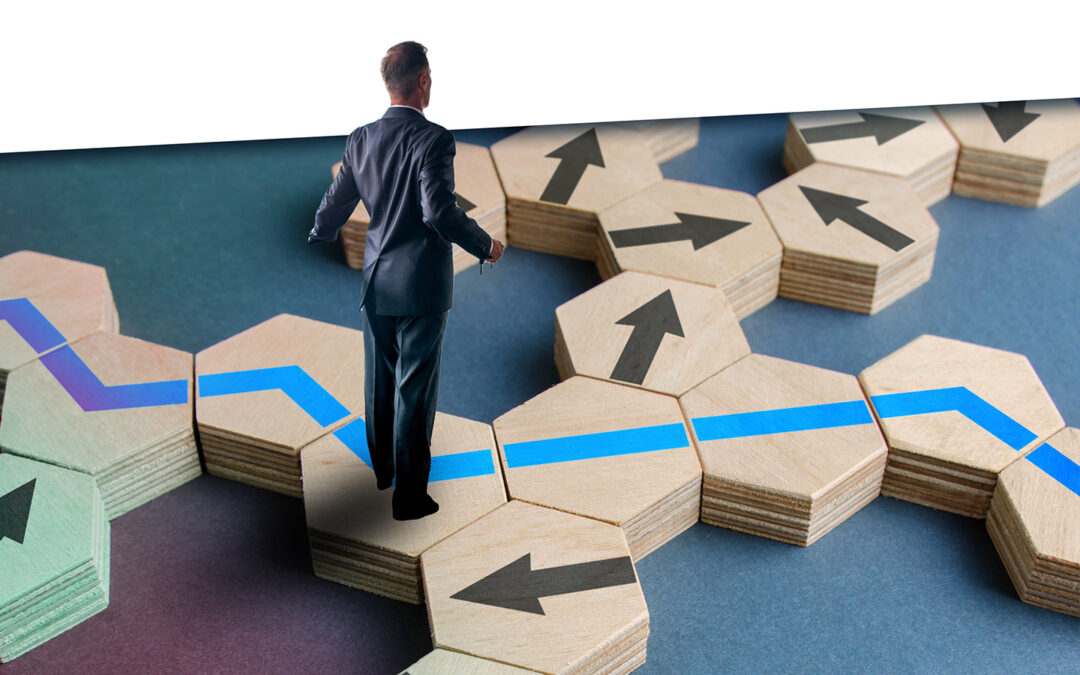
Scenario-based Forecasting vs. Equations
Traditionally, software has served as a delivery vehicle for equations. This is fine, as far as it goes. But we at Smart Software think you would do better by trading in your equations for scenarios. Learn why Scenario-based planning helps planners better manage risk and create better outcomes.
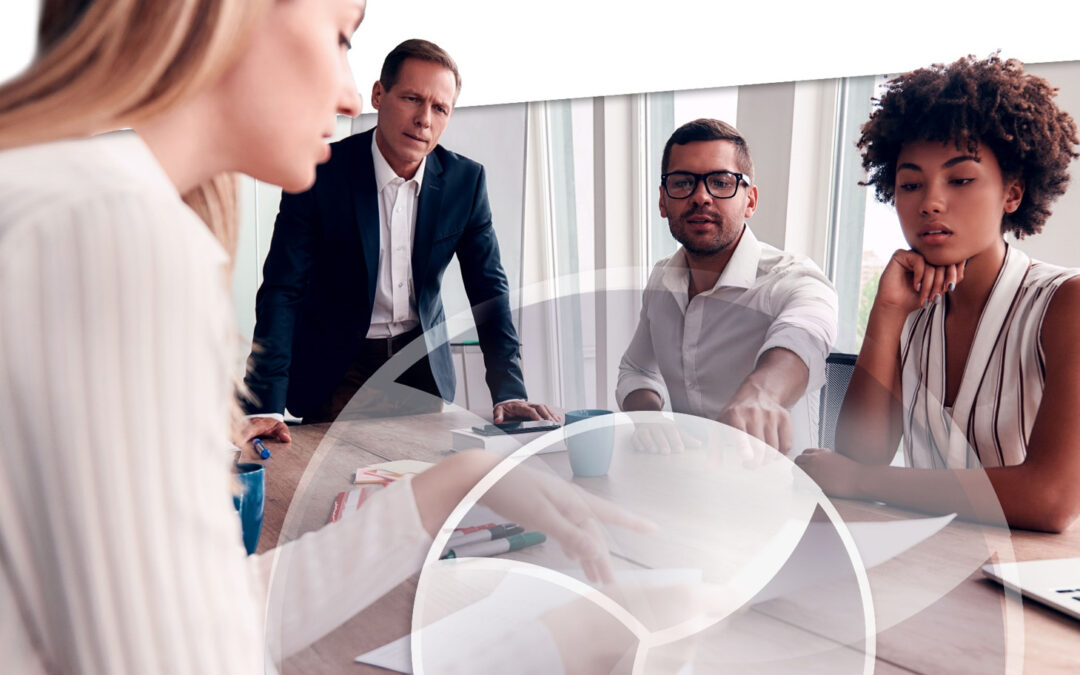
Extend Microsoft 365 BC and NAV with Smart IP&O
Microsoft 365 BC and NAV can manage replenishment by suggesting what to order and when via reorder point-based inventory policies. The problem is that the ERP system requires that the user manually specify these reorder points and/or forecasts. In this article, we will review the inventory ordering functionality in Microsoft BC & NAV, explain its limitations, and summarize how to reduce inventory, and minimize stockouts by providing the robust predictive functionality that is missing in Dynamics 365.