Smart Inventory Optimization™ is a collaborative inventory planning and optimization solution available on Smart’s Inventory Planning and Optimization Platform, Smart IP&O. It delivers inventory policy decision support and the means to share, collaborate, and track the impact of your inventory planning policy. This can help realize millions in savings by improving customer service and reducing excess stock. You can forecast metrics such as service level, fill rate, holding costs, ordering costs, and stock out costs. Users can identify overstocks and understocks, adjust stocking policies when demand changes, share proposed policies with other stakeholders, collect feedback, and establish a consensus inventory plan.
Smart Inventory Optimization Overview and Features
Inventory Planning
SIO embraces a fundamentally different approach to inventory planning than traditional forecasting, inventory planning and order management systems. Rather than simply suggesting what should be ordered and stocked to meet an arbitrary service level, SIO predicts service performance, costs, and other key performance predictions associated with the current and proposed policies.
Smart Optimization
When using the optimization feature, SIO projects holding cost, stock out cost and ordering cost for each item and prescribes the optimal planning parameters that achieve the least-cost service level for each item. The planning parameters being optimized are either reorder point/order quantity or Min/Max.
Optimal Policies
SIO will prescribe optimal service level targets that are projected to yield the lowest total cost, accounting for stock out costs, holding costs and ordering costs. The optimal policy is automatically compared to the current policy. Users can conduct what if analysis that modifies the policy according to business rules, such as service level targets. Below we’ve described the core functionality.
Predictive Exceptions
SIO’s Exception Management features identify which items are predicted to have significant changes in service level and/or inventory value. It also alerts to which items aren’t being ordered in the ERP or order management system according to the consensus plan. Exception lists are produced automatically, making it easy for you to review any problematic items and decide how to manage them moving forward.
Demand Groups
SIO classifies items into nine groups based on volume and frequency of usage/demand. Administrators can establish thresholds that define high, medium and low volume and frequency. The nine-cell Demand Groups table shows the counts of items, projected average service levels and projected average inventory values as well as the marginal totals. By selecting the symbol within each cell, you can jump to a display of the workbench for that subset.
Probabilistic Forecasting
SIO’s patented probability forecasting engine automatically generates tens of thousands of demand simulations per item and compares these simulations to the inventory policy. This stress tests the policy over thousands of realistic demand scenarios. Calculations are performed automatically as part of the daily import process. Users aren’t required to learn functionality to run the simulations—it’s baked into the process. Each time new transactional data are provided, the metrics are recalculated based on up-to-date information on demand, lead times and costs. As these variables change, so will the metrics. The following figure illustrates the kind of scenario analysis done in SIO.
Scenario Analysis
In order to make the right inventory decisions, businesses need to simulate the impact of proposed policy changes. SIO’s planning workbench offers the ability to compare multiple inventory policy scenarios. Four different types of scenarios are utilized: Live, What If, Named and Goal.
Collaboration and Consensus
All Named, Live, and Goal policies can be shared with other users on the platform. Alerts within SIO indicate when a policy has been shared among users. Recipients can import a shared policy into their workbench and assess it for themselves. Collaborative functionality within SIO is important for organizations with multiple planners responsible for their subset of items, locations, suppliers, etc. It lets each planner generate and share policies that they judge will best balance service versus cost.
Multiple Replenishment Methods
SIO is designed to generate planning parameters that can be used in any ERP replenishment policy. Results that can be exported include Min/Max, Reorder Point/Order Quantity, Safety Stock and Lead Time Demand Forecast.
Mass Apply
The Mass Apply radial will auto-apply numerical values entered into headers to all What If entries for the group. Mass Apply can be used to specify identical driver values for all items in a filtered group.
Patented Intermittent Demand Forecasting
Gives you the most accurate way to forecast sales when product demand is irregular and has a large proportion of zero values. This pattern is typical of spare parts and big-ticket items.
The Goal Scenario
The Goal scenario represents the consensus inventory plan and may only be produced by forecast lead users. It contains the item-specific inventory planning parameters that will be saved to the ERP system. To convert a Named scenario into the Goal scenario, follow these steps. First, copy that scenario to What If by selecting the encircled ↑ icon to the right of the scenario. Second, select Apply to All Items and Recalculate. Now, the What If scenario is equal to the Named Scenario intended for the goal. Finally, click Make Goal, which converts the What If scenario into the Goal scenario..
What If Analysis
What If scenarios can be run at the summary and item levels. Users can try out What If scenarios at the summary level by changing the service level average, ceiling or floors from the Drivers tab. Users can also prescribe the same target service level for all items by entering the desired value for the ceiling and floor. Users can conduct What If scenarios on individual items by doing so in the designated item section.
Optimization Function
The Optimization function provides an option to calculate planning parameters automatically for each item. Optimization computes the operating cost and service level associated with each choice of drivers (e.g., Min and Max). Then it searches through the possible choices of drivers to identify the least cost item-specific driver values subject to a limit on the Minimum acceptable service level.
Projected Metrics
Projected metrics forecast how a specified inventory policy will perform in the future.SIO reports on a variety of projected metrics, including service levels, fill rates, turns, stock-out costs, holding costs, ordering costs, and inventory value.
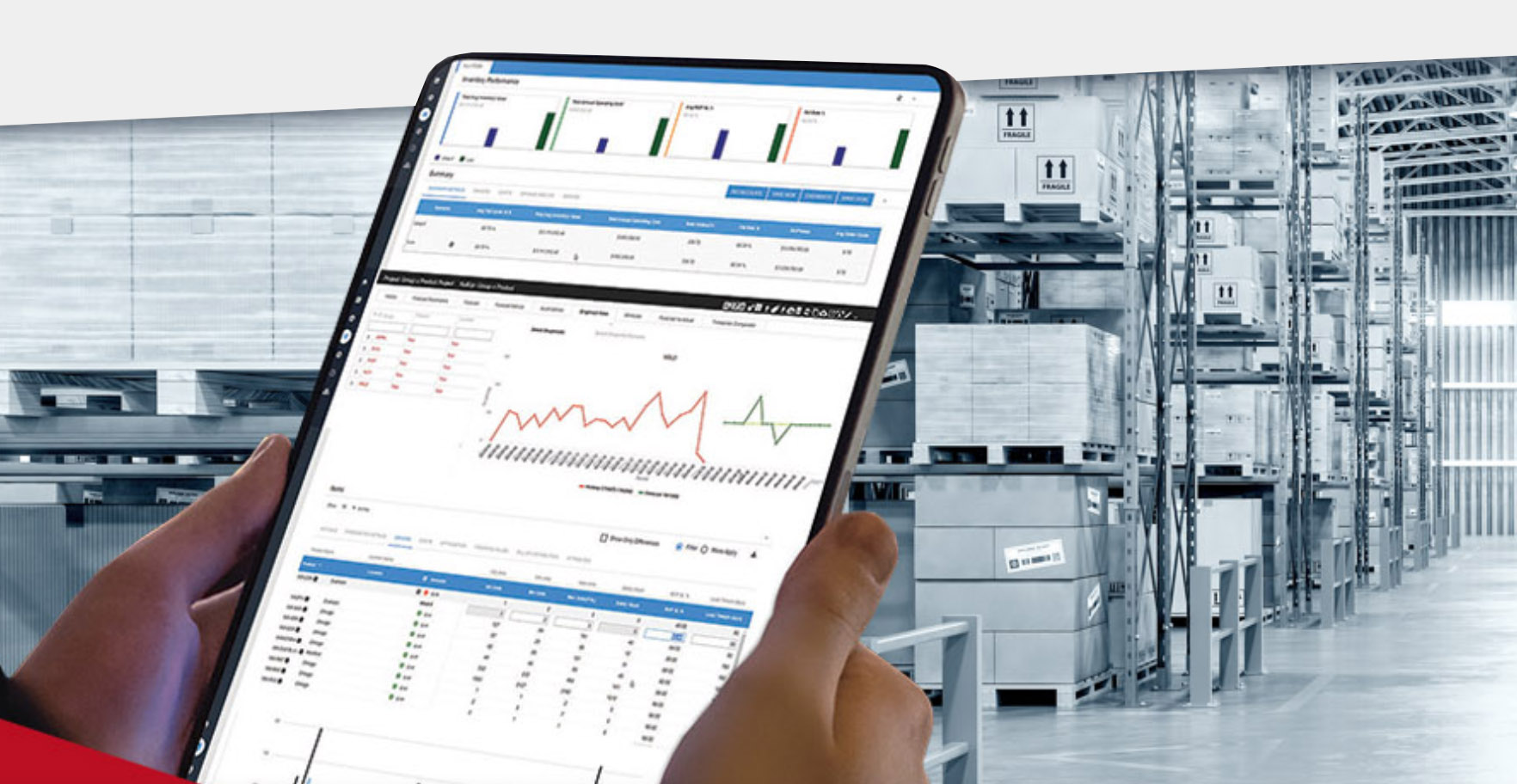
The impact of improved Demand & Inventory Planning
Optimizing Inventory Levels means savings realized on one subset of items can be reallocated in order to carry a broader portfolio of “in stock” items allowing revenues to be captured that would otherwise be lost sales. A leading distributor was able to stock a broader portfolio of parts with savings used from inventory reductions and increased part availability by 18%
Less critical Items that are forecasted to achieve 99%+ services levels represent opportunities to reduce inventory. By targeting lower service levels on less critical items, inventory will “right size” over time to the new equilibrium decreasing holding costs and value of inventory on hand. A major public transit system reduced inventory by more than $4,000,000 while improving service levels.
Customers Using our Demand and Inventory Forecasting Software
Contact Us Today for More Information
If you request a demo, one of our specialists will show you how Smart can help, using your own inventory data!