Inventory managers have the problem of handling tens or even hundreds of thousands of products, each with unique properties, demanding sophisticated and time-consuming calculations. The proactive management of big inventories becomes unfeasible in the absence of a systematic approach and effective analytic tools.
Without inventory optimization, businesses run the risk of overpaying and underperforming. Manufacturers, distributors, and MRO inventory managers frequently err on the side of caution when setting stocking levels to prevent expensive shortages. Establishing the ideal stock levels for manufacturers, distributors, and MRO should be a science, not an art.
Learn industry best practices on how to optimize inventory to save on costs, meet demand, and streamline your supply chain below.

Managing Spare Parts Inventory: Best Practices
In this blog, we’ll explore several effective strategies for managing spare parts inventory, emphasizing the importance of optimizing stock levels, maintaining service levels, and using smart tools to aid in decision-making. Managing spare parts inventory is a critical component for businesses that depend on equipment uptime and service reliability. Unlike regular inventory items, spare parts often have unpredictable demand patterns, making them more challenging to manage effectively. An efficient spare parts inventory management system helps prevent stockouts that can lead to operational downtime and costly delays while also avoiding overstocking that unnecessarily ties up capital and increases holding costs.

12 Causes of Overstocking and Practical Solutions
Managing inventory effectively is critical for maintaining a healthy balance sheet and ensuring that resources are optimally allocated. Here is an in-depth exploration of the main causes of overstocking, their implications, and possible solutions.

FAQ: Mastering Smart IP&O for Better Inventory Management.
Effective supply chain and inventory management are essential for achieving operational efficiency and customer satisfaction. This blog provides clear and concise answers to some basic and other common questions from our Smart IP&O customers, offering practical insights to overcome typical challenges and enhance your inventory management practices. Focusing on these key areas, we help you transform complex inventory issues into strategic, manageable actions that reduce costs and improve overall performance with Smart IP&O.

Innovating the OEM Aftermarket with AI-Driven Inventory Optimization
The aftermarket sector provides OEMs with a decisive advantage by offering a steady revenue stream and fostering customer loyalty through the reliable and timely delivery of service parts. However, managing inventory and forecasting demand in the aftermarket is fraught with challenges, including unpredictable demand patterns, vast product ranges, and the necessity for quick turnarounds. Traditional methods often fall short due to the complexity and variability of demand in the aftermarket. The latest technologies can analyze large datasets to predict future demand more accurately and optimize inventory levels, leading to better service and lower costs.
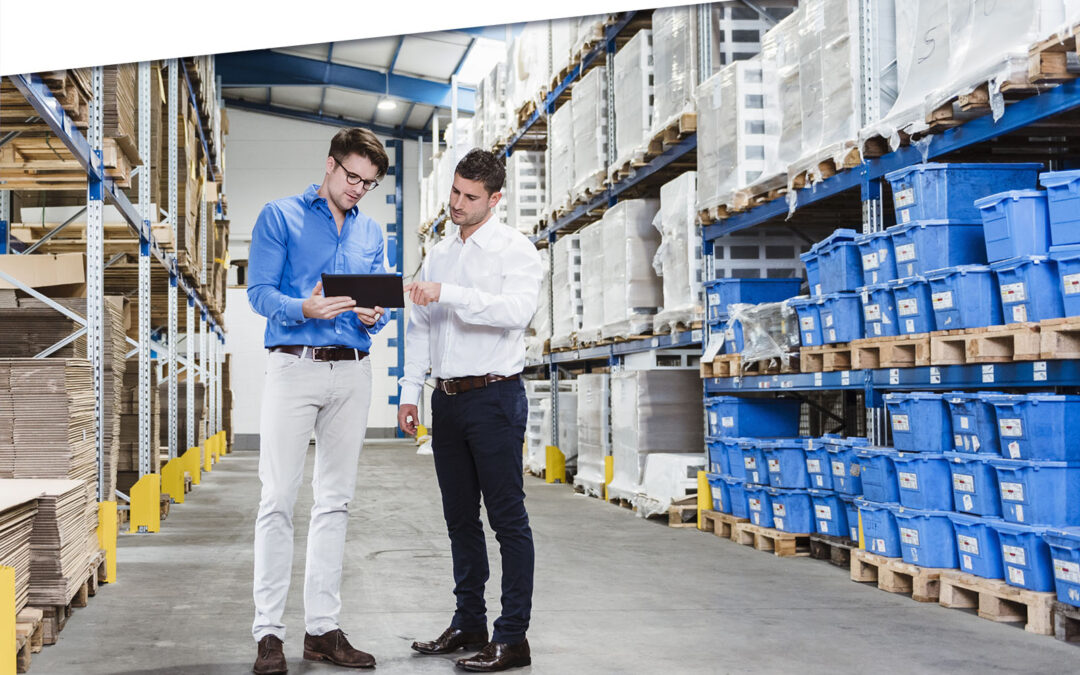
Forecast-Based Inventory Management for Better Planning
Forecast-based inventory management, or MRP (Material Requirements Planning) logic, is a forward-planning method that helps businesses meet demand without overstocking or understocking. By anticipating demand and adjusting inventory levels, it maintains a balance between meeting customer needs and minimizing excess inventory costs. This approach optimizes operations, reduces waste, and enhances customer satisfaction.
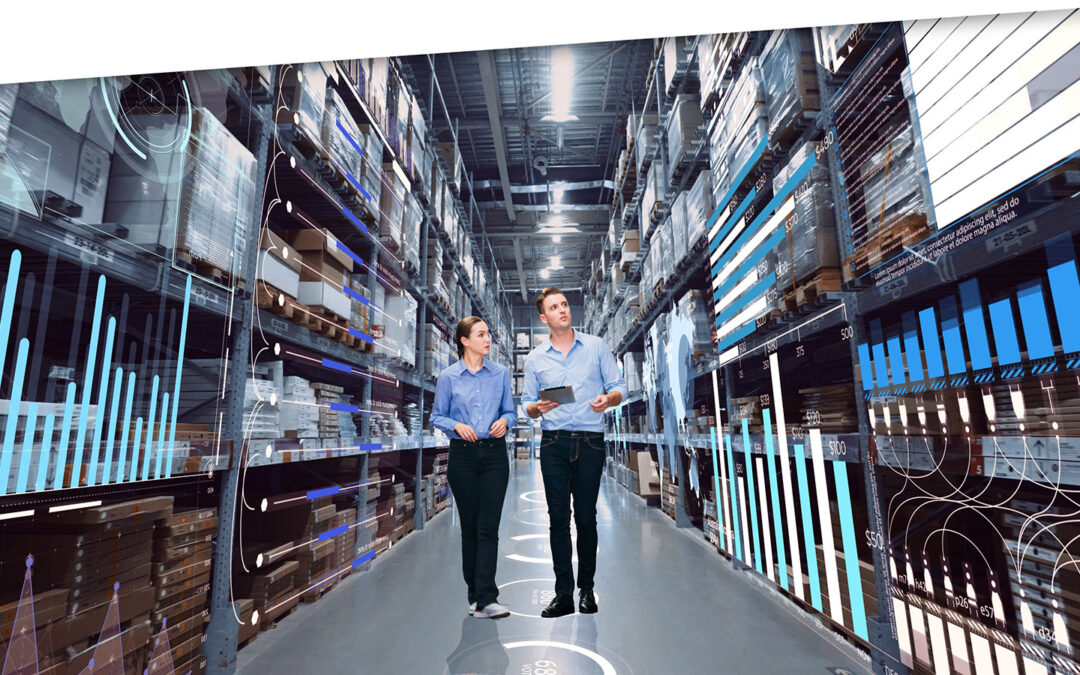
Make AI-Driven Inventory Optimization an Ally for Your Organization
In this blog, we will explore how organizations can achieve exceptional efficiency and accuracy with AI-driven inventory optimization. Traditional inventory management methods often fall short due to their reactive nature and reliance on manual processes. Maintaining optimal inventory levels is fundamental for meeting customer demand while minimizing costs. The introduction of AI-driven inventory optimization can significantly reduce the burden of manual processes, providing relief to supply chain managers from tedious tasks.
Problem
Keeping inventory investments in check while maintaining high customer service levels is a constant balancing act. Without proper controls, excess inventory grows throughout your supply chain, locking up vital working capital that constrains your company’s growth. Every day, the ERP system makes purchase order suggestions and manufacturing orders based on planning drivers such as safety stock, reorder points, and Min/Max levels. Ensuring that these inputs are understood and continually optimized will generate substantially better returns on your inventory assets. Unfortunately, many organizations rely on rule of thumb logic, institutional knowledge, and “one-size-fits all” forecasting logic that assigns all items within a particular group the same service level target. These approaches yield suboptimal policies that cause inventory costs to balloon and service performance to suffer. Compounding the problem is the sheer volume of data – thousands of items stocked at multiple locations means planners don’t have the bandwidth to proactively review these inventory drivers on a regular basis. This results in outdated reorder points, safety stocks, order quantities, and Min/Max settings that further contribute to the problem.
Solution
Smart Inventory Optimization (SIO™) is available on Smart’s Inventory Planning and Optimization Platform, Smart IP&O. It delivers inventory policy decision support and the means to share, collaborate, and track the impact of your inventory planning policy. This can help realize millions in savings by improving customer service and reducing excess stock. You can forecast metrics such as service level, fill rate, holding costs, ordering costs, and stock out costs. Users can identify overstocks and understocks, adjust stocking policies when demand changes, share proposed policies with other stakeholders, collect feedback, and establish a consensus inventory plan. And unlike traditional inventory planning systems that rely on rule of thumb approaches or require the user to arbitrarily set suboptimal service level targets, Smart Inventory Optimization prescribes the optimal service levels for you. Users can optionally assign service level constraints to ensure the optimization engine respects business rules. SIO provides the required inventory planning parameters for a variety of replenishment policies such as Reorder Point/Order Quantity, Min/Max, Safety Stock Planning, and Order Up to levels.
Register to Watch the Demo
With Smart Inventory Optimization you can:
- Identify where you are overstocked and understocked.
- Modify planning parameters based on your business rules, service targets, and inventory budget.
- Leverage the optimization logic in SIO to prescribe planning parameters and service levels for you.
- Compare proposed policies to the benchmark.
- Collaborate and develop a consensus inventory plan.
- Automatically generate revised planning parameters as demand and other inputs change.
Smart Inventory Optimization
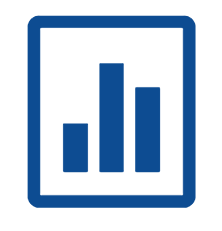
Optimal Inventory Levels
Reduce excess stock
Improve service levels
Minimize buyer transactions
Maximize return on assets

Organizational Consensus
Balance service levels
Identify stockout risk
Identify overstocks
No finger-pointing
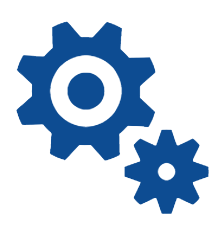
Operational Connectivity
Align process with strategic objectives
Empower team to “make it so”
Optimize as conditions change
Pass results to ERP
Who is Inventory Optimization for?
Smart Inventory Optimization is for executives and business savvy planners who seek to:
- Yield maximum returns from inventory assets.
- Address the problem of highly variable or intermittent demand.
- Broker the service vs. cost tradeoffs between different departments.
- Develop a repeatable and efficient inventory planning process.
- Empower the team to ensure operational plan is aligned with strategic plan.
What questions can Inventory Optimization answer?
- What is the best service level achievable with the inventory budget?
- What service levels will yield the maximum return?
- If lead times increased, what would it cost to maintain service?
- If I reduce inventory, what will the impact on service be?
- If order quantity increases, what will the impact on service and costs be?
- What is the order quantity that balances holding and ordering costs?
Inventory forecasting for the inventory executive
Smart Inventory Optimization empowers you to:
- Predict service performance and inventory costs.
- Assess business impact of “what-if” inventory policies.
- Align inventory policy with corporate strategy.
- Establish an operational framework that guides the planning team.
- Reduce inventory and improve service.