Business policies utilize predictive analytics and regression analysis to manage inventory effectively, avoiding excesses and shortages while optimizing costs and responsiveness. The implementation of these policies involves advanced statistical methods and technologies to enhance accuracy, reduce errors, and adapt to market changes, thereby maintaining operational efficiency and competitiveness.
Check out industry best practices below on how to optimize your inventory to cut costs, meet demand, and streamline your supply chain.
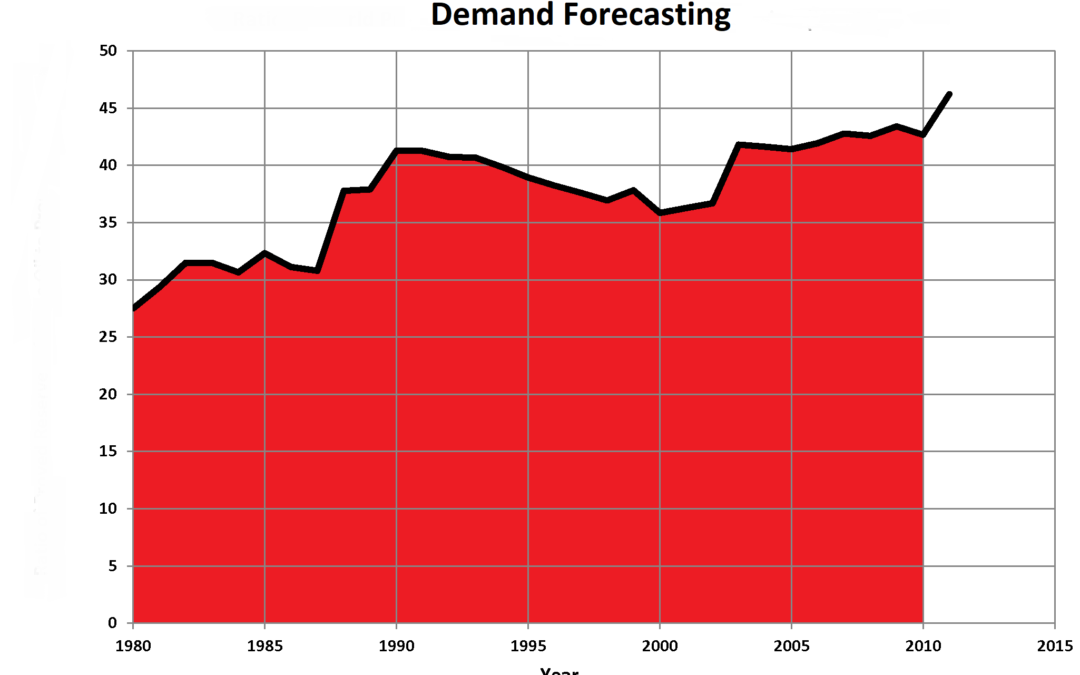
Demand Forecasting in a “Build to Order” Company
We often come into contact with potential customers who claim that they cannot use a forecasting system since they are a “build-to-order” manufacturing operation. I find this a puzzling perspective, because whatever these organizations build requires lower level raw materials or intermediate goods. If those lower level inputs are not available when an order for the finished good is received, the order cannot be built. Consequently, the order could be canceled and the associated revenue lost.
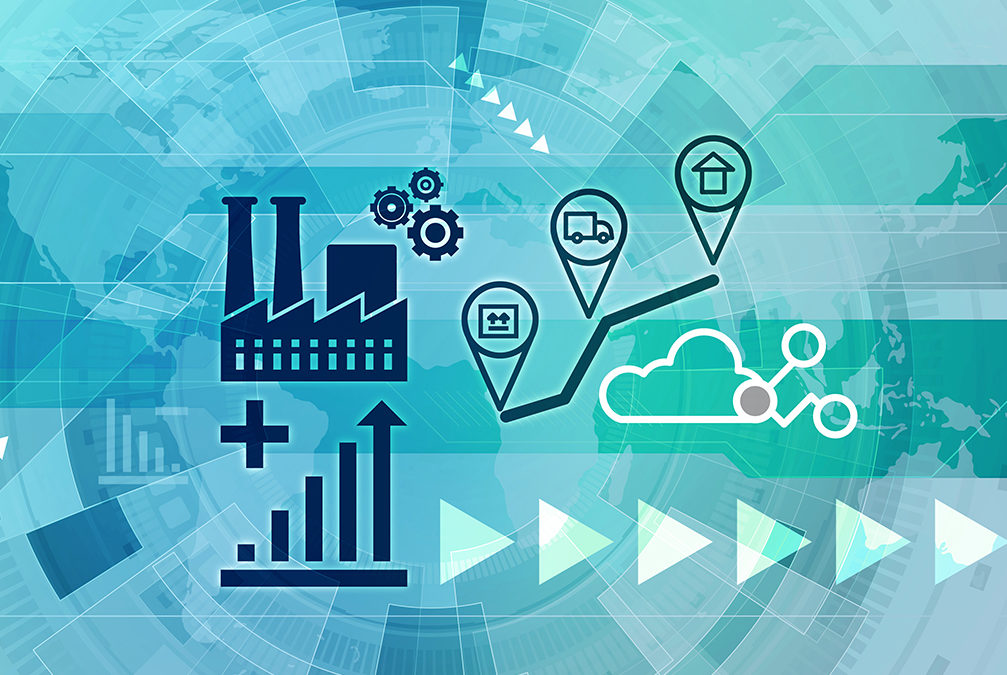
3 Types of Supply Chain Analytics
The three types of supply chain analytics are “descriptive”, “predictive”, and “prescriptive.” Each plays a different role in helping you manage your inventory. Modern supply chain software lets you exploit all three helping you to reduce inventory costs, improve on time delivery and service levels, while running a more efficient supply chain.
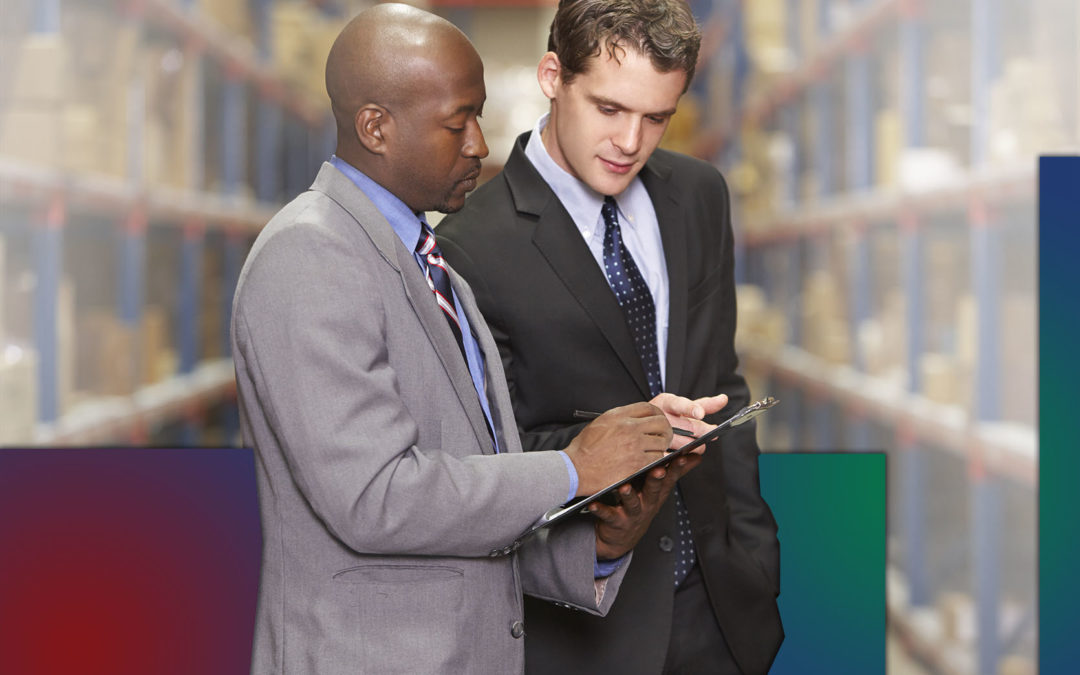
Too Much or Too Little Inventory?
Do you know which items have too much or too little inventory? What if you knew? How would you go about cutting overstocks while still ensuring a competitive service level? Would you be able to reduce stockouts without incurring a prohibitively expensive inventory increase? How would these changes impact service levels, costs and turns—for individual items, groups of items and overall?
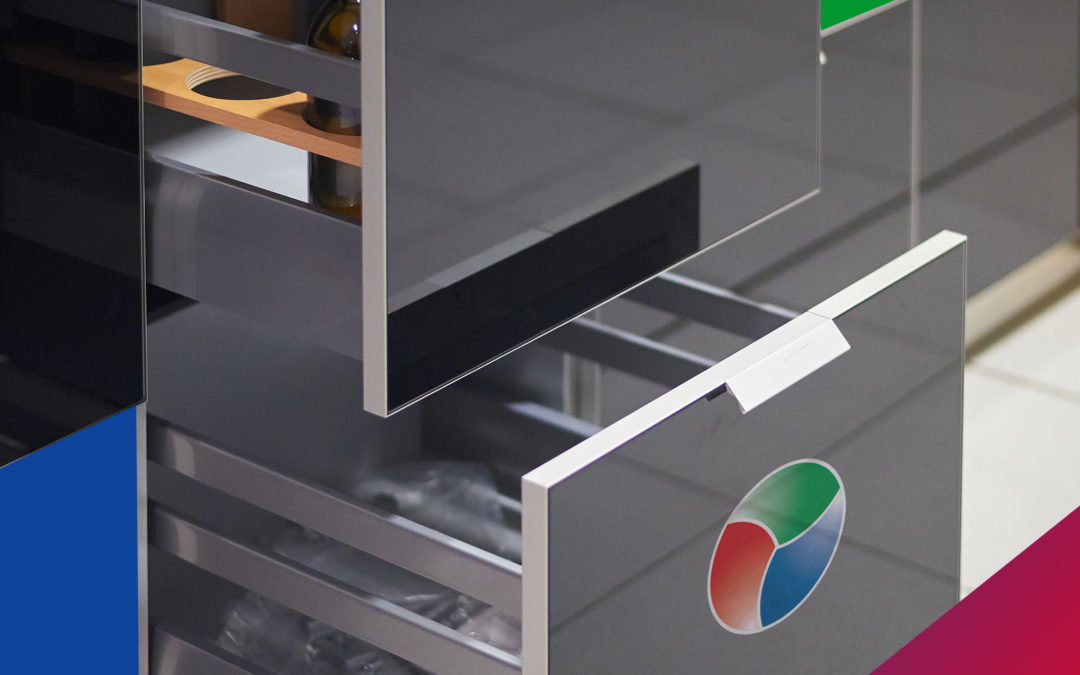
Handling Extreme Supply Chain Variability at Rev-A-Shelf
Does your extended supply chain suffer from extreme seasonal variability? Does this situation challenge your ability to meet service level commitments to your customers? I have grappled with this at Rev-A-Shelf, addressing unusual conditions created by Chinese New Year and other global events, and would like to share the experience and a few things I learned along the way.
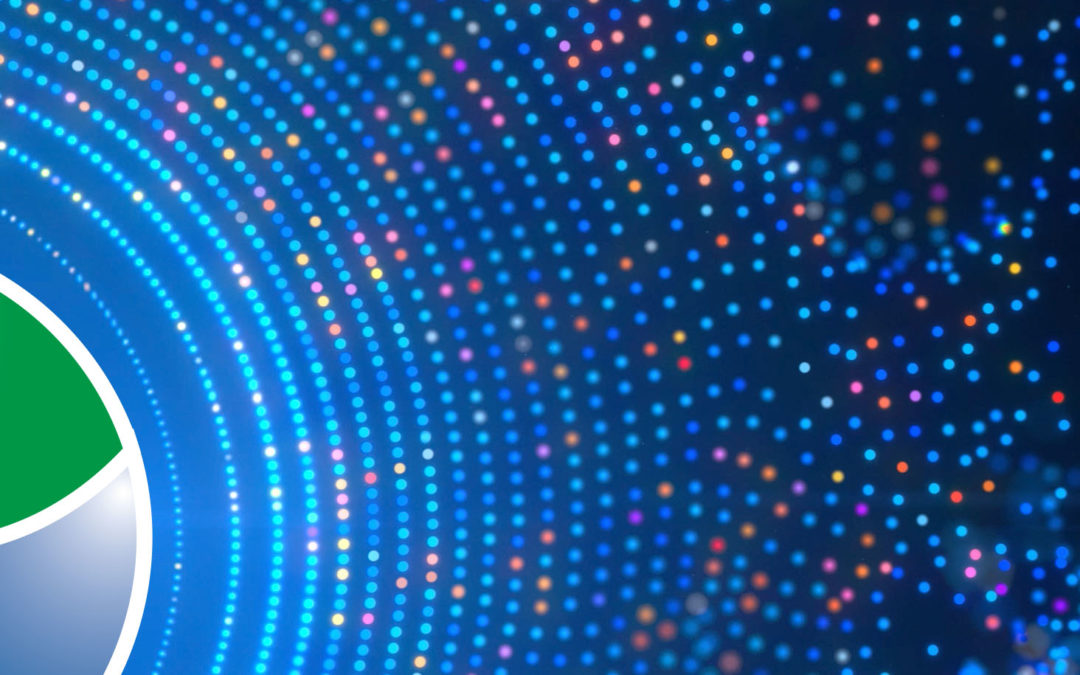
Recommended Reading: Cloud Software Helps Overcome Budget Constraints
Smart Software recently announced a Software as a Service (SaaS) option for SmartForecasts—SFCloud™. Premises-based perpetual licenses will continue to be the preferred software implementation method for many organizations, but there are many reasons why demand for cloud-based solutions is taking off. A vintage post by Bill Richardson at ApplicantStack Team Blog summarizes key benefits of the SaaS model.
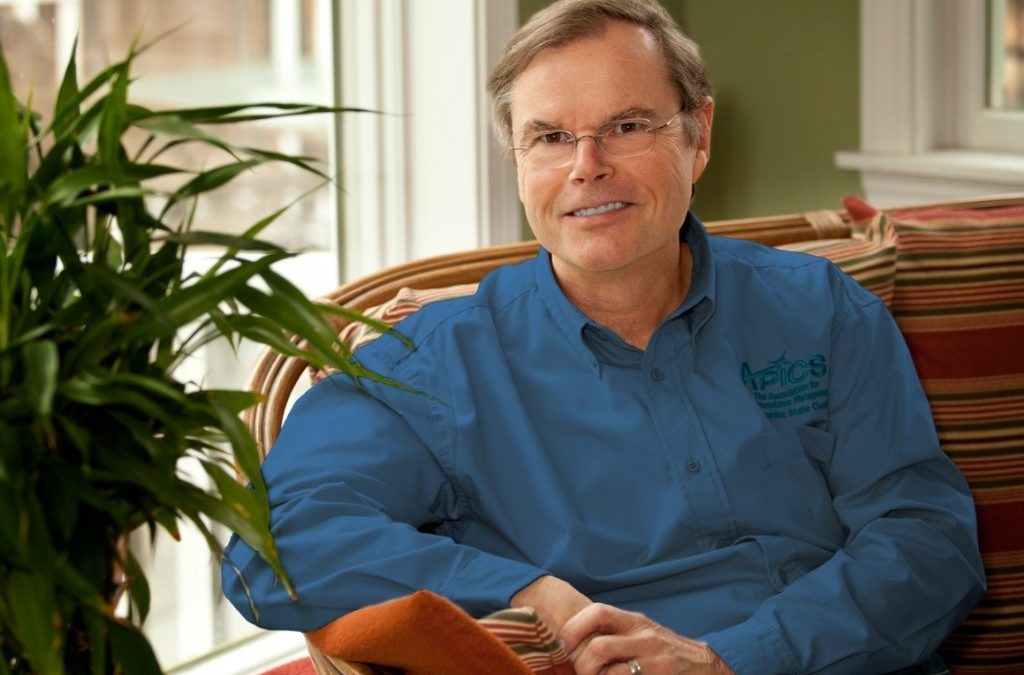
Truth in Forecasting—Practical Advice at Year’s End
At year’s end, we are often caught up in thinking and planning for the coming year. Did 2013 turn out the way you expected? Will 2014 be dramatically different? Are there other factors—things we are planning to do; things we think our competitors might do; outside forces like changing taste, demographics or economics—that might change the course of business in the coming year?
Problem
What is my inventory position today, on any item? Where are we stocking out and how often? What are my delivery times? Why did we ship late? Do we have too much inventory in one location, not enough in another? What are my real supplier lead times? These are obvious, daily questions, and the answers can reveal underlying root causes that when resolved will improve supply chain performance. But these answers are elusive, often because data is locked up in your ERP and only accessible via limited reporting views or spreadsheets. Creating these reports manually using Excel requires data imports, reformatting, and distribution to key stakeholders, wasting countless hours of valuable planning time. This means that getting updated information, when you need it, is not always possible. Not having access to these answers means that problems reveal themselves only after it is too late, and opportunities for improving the inventory planning process are overlooked, further contributing to poor performance.
Solution
Smart Operational Analytics (SOA™) is a native web reporting solution available on Smart’s Inventory Planning and Optimization Platform, Smart IP&O. It provides a fast, easily understood, current perspective on the state of your inventory, its performance against critical metrics, actual supplier lead times, opportunities to rebalance stocks across facilities, and helps you uncover root causes of operational inefficiencies. SOA automatically refreshes as often as you’d like providing all stakeholders immediate, up-to-date reporting on your operations and performance. You’ll have constant visibility of inventory levels, orders, shipments, and supplier performance to ensure you’ll always be in tune with the state of your operations and resolve issues before they become problems. Enhance visibility. Improve responsiveness. Increase your bottom line.
Register to Watch the Demo
Smart Operational Analytics
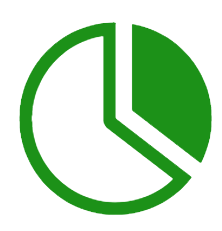
Inventory Analytics
Quantify inventory value
Inventory segmentation
Inventory classification
Trend metrics over time
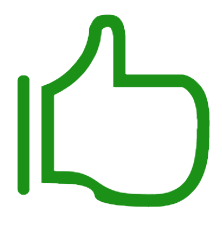
Operational Performance
Measure service level performance
Measure fill rate performance
Calculate turns, holding & ordering costs
Trend metrics over time
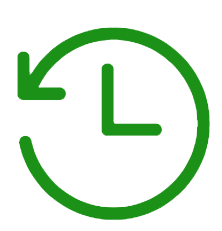
Supplier Insights
Measure supplier performance
Compare supplier lead times
Rank suppliers across available metrics
Trend metrics over time
Who is Operational Analytics for?
Smart Operational Analytics is for executives, planners, and operations professionals who seek to:
- Measure inventory costs and performance in real time.
- Assess and compare Supplier performance.
- Identify root causes of stockouts, excess inventory, and late deliveries.
- share KPI’s such as service levels, turns, costs, and more across the organization.
What questions can Operational Analytics answer?
- What does my inventory look like? By value, count, classification?
- Is my inventory trending up, down, or the same?
- How much of my inventory is overstocked, understocked, or acceptable?
- Can inventory be transferred from overstocked locations to under stocked locations?
- Can existing supplier orders be cancelled or deferred?
- What are my current turns, service levels, and fill rates and how do they trend over time?
- How many out of stock events occurred this week, this month, this quarter?
- How are my suppliers performing, how do they compare?
- What is my supplier lead time and how has it changed over time?
Inventory and supplier reporting for your enterprise
Smart Operational Analytics empowers you to:
- Benchmark service performance and inventory costs.
- Benchmark supplier performance.
- Assess and Classify Inventory by class, stage, and more.
- Share metrics with the organization.