Service level is a key performance indicator for companies that put a premium on satisfying customer demand. Service level is defined as the probability of surviving a replenishment lead time without stocking out.
Inventory management best practice begins with setting service level targets, then calculates reorder points (also called Mins) to achieve those targets. These calculations should account for variability in both demand and replenishment lead time. There are many software systems available for doing these calculations. If everything works out, the achieved service level ends up very close to the target service level. Unfortunately, there is often a painful gap between the two.
One reason for the gap is unrealistic models of demand. In many cases, software for calculating reorder points uses textbook formulas based on mathematical assumptions that make analysis simple at the expense of realism. Many “Inventory 101” textbooks use formulas that assume demand has a Normal distribution (a.k.a. the “bell-shaped curve”) for finished goods and the Poisson distribution for spare parts. Fortunately, there are now inventory optimization and forecasting systems that process the actual demand histories of the inventory items using probabilistic forecasting. These solutions calculate an accurate estimate of the distribution – not some idealized version. To learn more check out this past blog on probabilistic forecasting:
But there is a second source of error in textbooks that operates invisibly in many inventory software package: “undershoot”.
Calculations of reorder points almost always assume that stockouts arise when the total demand during a replenishment interval exceeds the reorder point. For example, assume that demand averages 1 unit per day. If lead time is 5 days, then on average lead time demand is 5 units. Setting the reorder point at 5 units would yield a laughable service level somewhere in the vicinity of 50%. Adding safety stock to the calculation might result in a reorder point of, say, 11 units, which might correspond to a service level of 95%. Another way to say this is, starting at a reorder point of 11 units, there should be a 95% chance of surviving the 5 day lead time without experiencing cumulative demand of more than 11 units. Theoretically!
What’s missing from this analysis is the undershoot phenomenon. Undershoot means that the lead time begins not at the reorder point but below it. Undershoot happens every time the demand that breached the reorder point took the stock down below (not down to) the reorder point. The figure below shows replenishment cycles with and without undershoot. Undershoot picks your pocket before you even begin to roll the dice. It deludes the inventory professional into thinking his or her reorder points are sufficient to achieve their targets, whereas actual performance will not make the grade.
There is only one situation in which undershoot is not a worry: when demand is always either zero or one unit. In that case, undershoot is impossible. But in all other cases, undershoot is sure to happen to some extent, and it can seriously undercut the service level actually achieved by a given choice of reorder point. Our analyses show that the conditions most vulnerable to undershoot involve highly intermittent and skewed demand with very short lead times – the very conditions being made most common by market trends.
What can be done to protect yourself from the effect of undershoot on reorder point calculations? Use inventory optimization and forecasting software that isn’t tied to the old textbook assumptions and instead automatically accounts for undershoot when calculating the service level produced by any choice of reorder point.
To see Smart Software’s Inventory Optimization solution in action, register to see a recorded demo below:
Related Posts
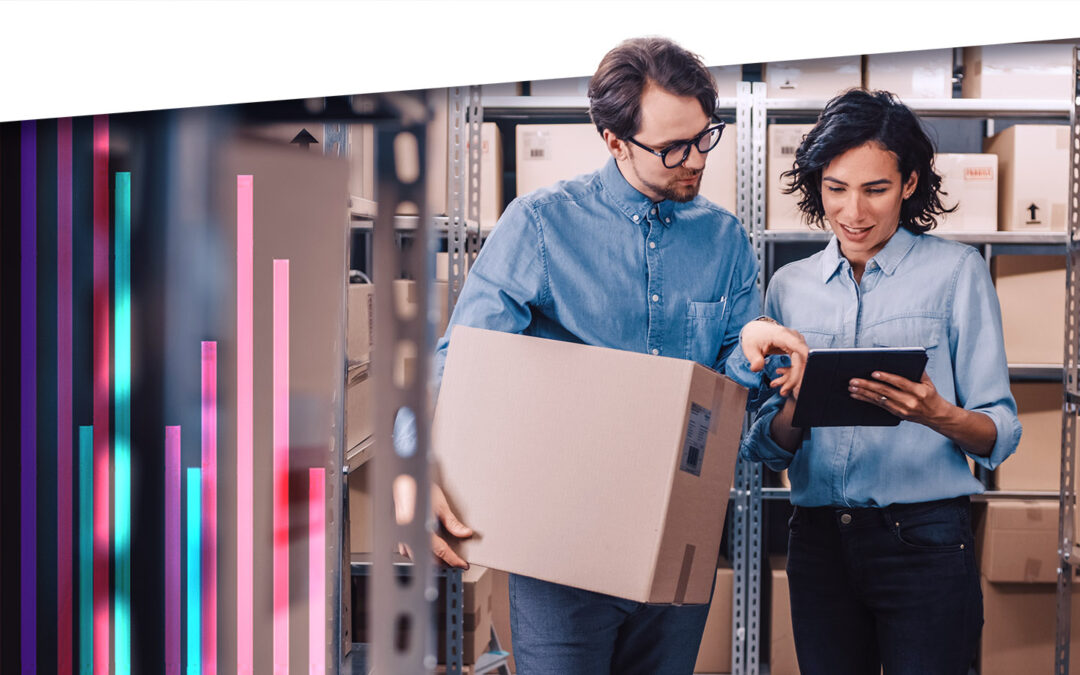
Forecast-Based Inventory Management for Better Planning
Forecast-based inventory management, or MRP (Material Requirements Planning) logic, is a forward-planning method that helps businesses meet demand without overstocking or understocking. By anticipating demand and adjusting inventory levels, it maintains a balance between meeting customer needs and minimizing excess inventory costs. This approach optimizes operations, reduces waste, and enhances customer satisfaction.
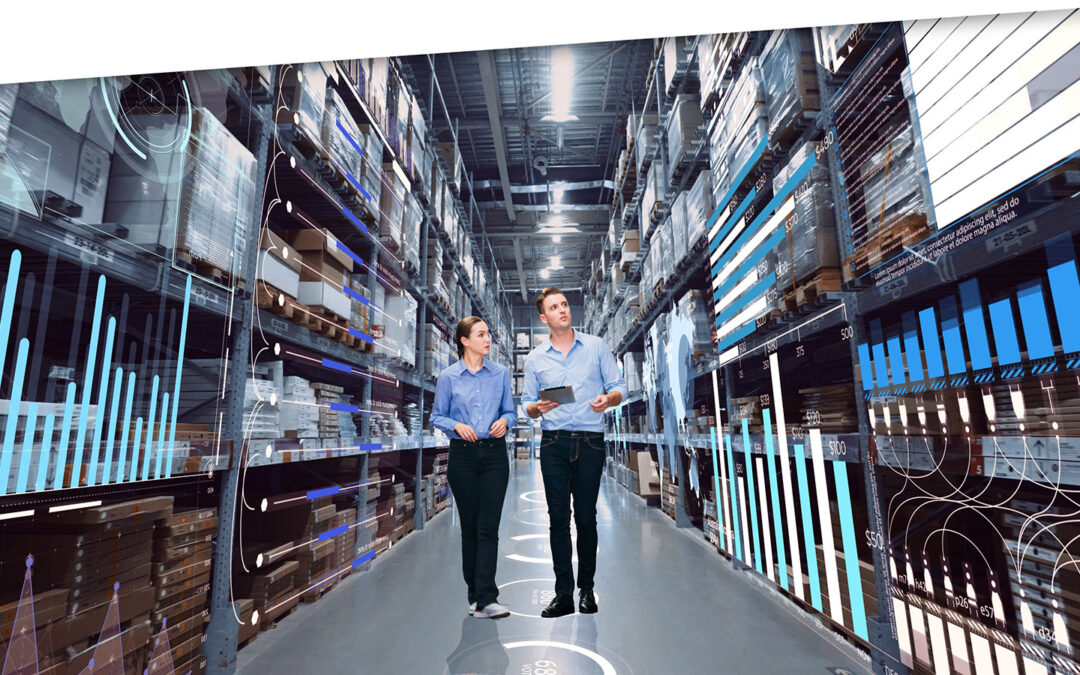
Make AI-Driven Inventory Optimization an Ally for Your Organization
In this blog, we will explore how organizations can achieve exceptional efficiency and accuracy with AI-driven inventory optimization. Traditional inventory management methods often fall short due to their reactive nature and reliance on manual processes. Maintaining optimal inventory levels is fundamental for meeting customer demand while minimizing costs. The introduction of AI-driven inventory optimization can significantly reduce the burden of manual processes, providing relief to supply chain managers from tedious tasks.
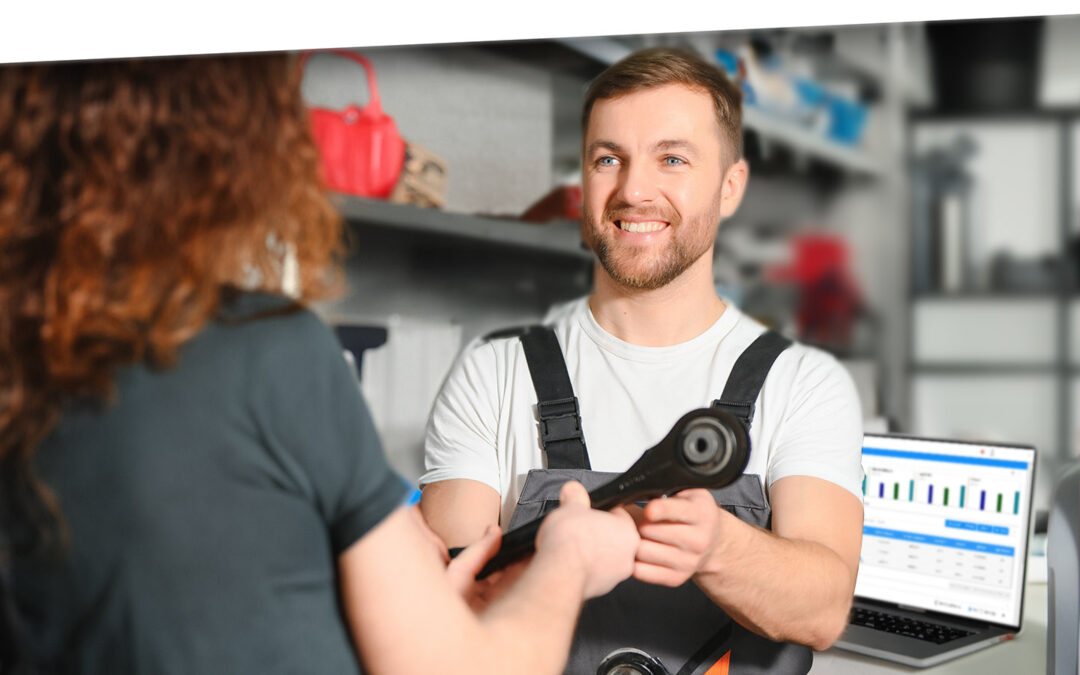
The Importance of Clear Service Level Definitions in Inventory Management
Inventory optimization software that supports what-if analysis will expose the tradeoff of stockouts vs. excess costs of varying service level targets. But first it is important to identify how “service levels” is interpreted, measured, and reported. This will avoid miscommunication and the false sense of security that can develop when less stringent definitions are used. Clearly defining how service level is calculated puts all stakeholders on the same page. This facilitates better decision-making.