You can’t properly manage your inventory levels, let alone optimize them, if you don’t have a handle on exactly how demand forecasts and stocking parameters (such as Min/Max, safety stocks, and reorder points, and order quantities) are determined.
Many organizations cannot specify how policy inputs are calculated or identify situations calling for management overrides to the policy. For example, many people can say they rely on a particular planning method such as Min/Max, reorder point, or forecast with safety stock, but they can’t say exactly how these planning inputs are calculated. More fundamentally, they may not understand what would happen to their KPI’s if they were to change Min,Max, or Safety Stock. They may know that the forecast relies on “averages” or “history” or “sales input”, but specific details about how the final forecast is arrived at are unclear.
Often enough, a company’s inventory planning and forecasting logic was developed by a former employee or vanished consultant and entombed in a spreadsheet. It otherwise may rely on outdated ERP functionality or ERP customization by an IT organization that incorrectly assumed that ERP software can and should do everything. (Read this great and, as they say, “funny because it’s true,” blog by Shaun Snapp about ERP Centric Strategies.) The policy may not have been properly documented, and no one currently on the job can improve it or use it to best advantage.
This unhappy situation leads to another, in which buyers and inventory planners flat out ignore the output from the ERP system, forcing reliance on Microsoft Excel to determine order schedules. Ad hoc methods are developed that impede cohesive responses to operational issues and aren’t visible to the rest of the organization (unless you want your CFO to learn the complex and finicky spreadsheet). These methods often rely on rules of thumb, averaging techniques, or textbook statistics without a full understanding of their shortcomings or applicability. And even when documented, most companies often discover that actual ordering strays from the documented policy. One company we consulted for had on hand inventory levels that were routinely 2 x’s the Max quantity! In other words, there isn’t really a policy at all.
In summary, many current inventory and demand forecast “systems” were developed out of distrust for the previous system’s suggestions but don’t actually improve KPI’s. They also force the organization to rely on a few employees to manage demand forecasting, daily ordering, and inventory replenishment.
And when there is a problem, it is impossible for the executive team to unwind how you got there, because there are too many moving parts. For example, was the excess stock the fault of an inaccurate demand forecast that relied on an averaging method that didn’t account for a declining demand? Or was it due to an outdated lead time setting that was higher than it should’ve been? Or was it due to a forecast override a planner made to account for an order that just never happened? And who gave the feedback to make that override? A customer? Salesperson?
Do you have any of these problems? If so, you are wasting hundreds of thousands to millions of dollars each year in unnecessary shortage costs, holding costs, and ordering costs. What would you be able to do with that extra cash? Imagine the impact that this would have on your business.
This blog details the top 10 questions that you can ask in order to uncover what’s really happening at your company. We detail the typical answers provided when a forecasting/inventory planning policy doesn’t really exist, explain how to interpret these answers, and offer some clear advice on what to do about it.
Related Posts
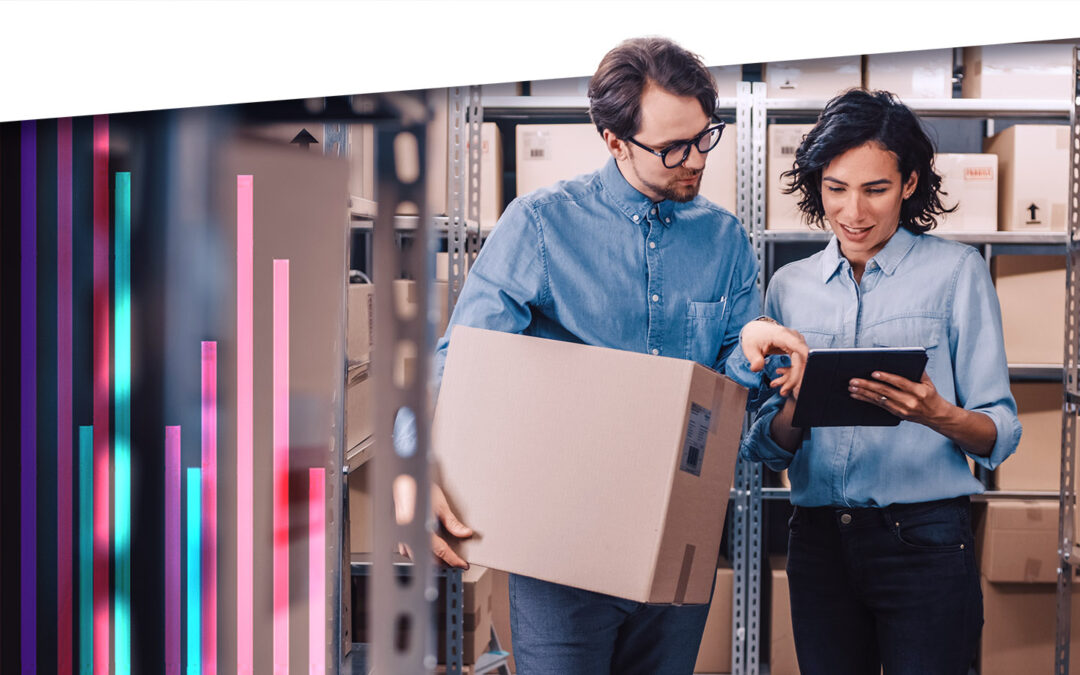
Forecast-Based Inventory Management for Better Planning
Forecast-based inventory management, or MRP (Material Requirements Planning) logic, is a forward-planning method that helps businesses meet demand without overstocking or understocking. By anticipating demand and adjusting inventory levels, it maintains a balance between meeting customer needs and minimizing excess inventory costs. This approach optimizes operations, reduces waste, and enhances customer satisfaction.
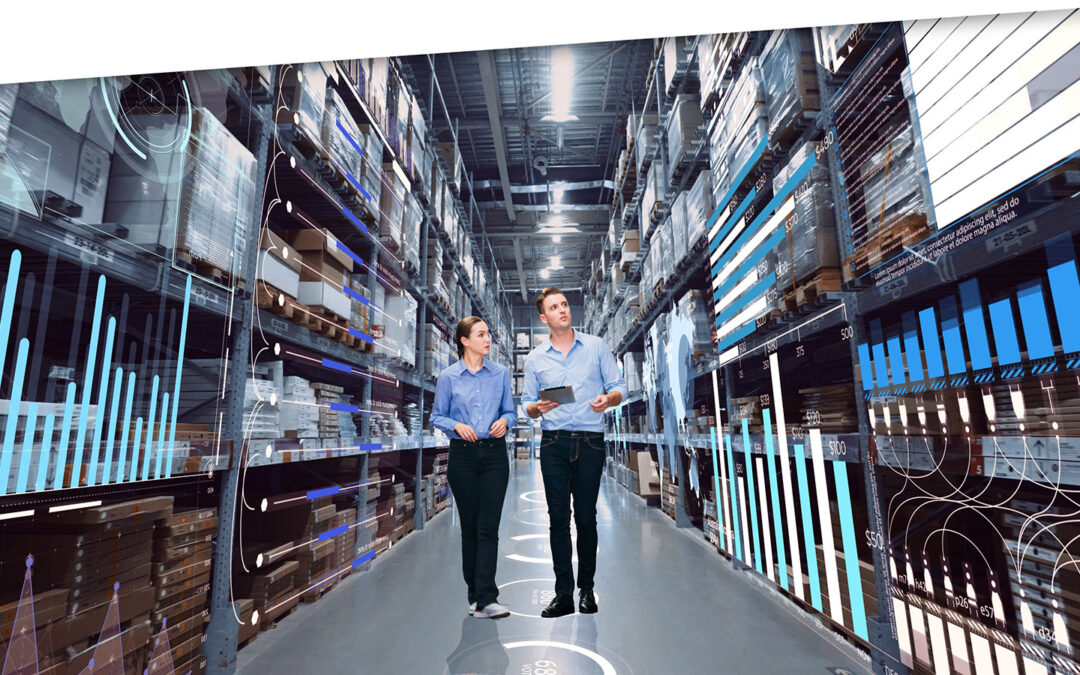
Make AI-Driven Inventory Optimization an Ally for Your Organization
In this blog, we will explore how organizations can achieve exceptional efficiency and accuracy with AI-driven inventory optimization. Traditional inventory management methods often fall short due to their reactive nature and reliance on manual processes. Maintaining optimal inventory levels is fundamental for meeting customer demand while minimizing costs. The introduction of AI-driven inventory optimization can significantly reduce the burden of manual processes, providing relief to supply chain managers from tedious tasks.
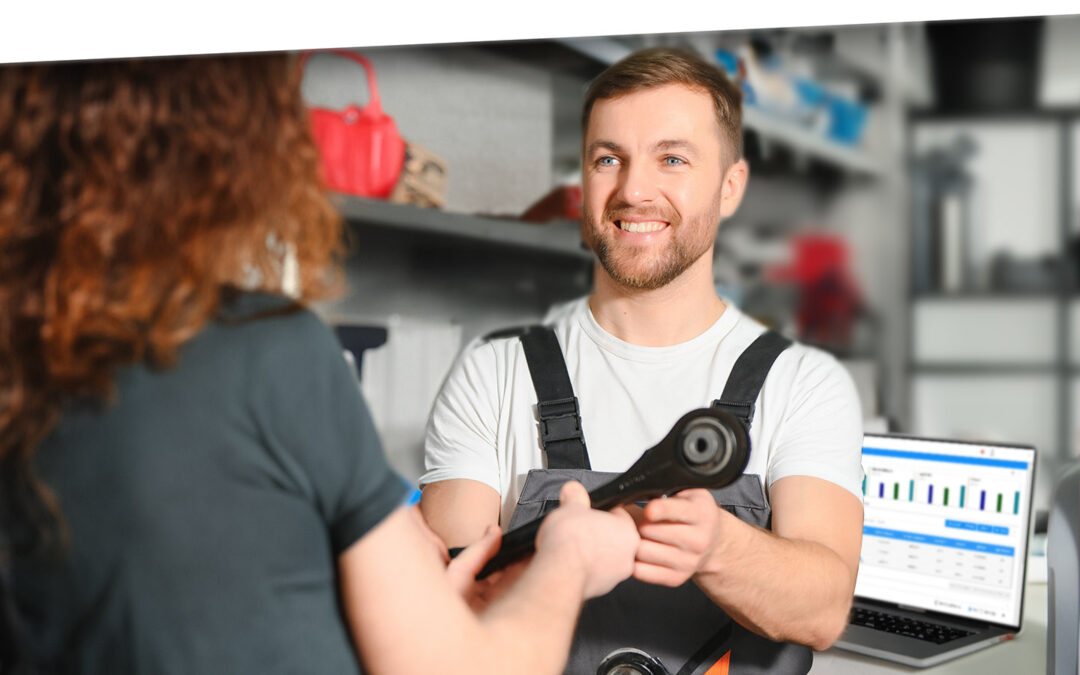
The Importance of Clear Service Level Definitions in Inventory Management
Inventory optimization software that supports what-if analysis will expose the tradeoff of stockouts vs. excess costs of varying service level targets. But first it is important to identify how “service levels” is interpreted, measured, and reported. This will avoid miscommunication and the false sense of security that can develop when less stringent definitions are used. Clearly defining how service level is calculated puts all stakeholders on the same page. This facilitates better decision-making.