In our last blog we posed the question: How can you be sure that you really have a policy for inventory planning and demand forecasting? We explained how an organization’s lack of understanding on the basics (how a forecast is created, how safety stock buffers are determined, and how/why these values are adjusted) contributes to poor forecast accuracy, misallocated inventory, and lack of trust in the whole process.
In this blog, we review 10 specific questions you can ask to uncover what’s really happening at your company. We detail the typical answers provided when a forecasting/inventory planning policy doesn’t really exist, explain how to interpret these answers, and offer some clear advice on what to do about it.
Always start with a simple hypothetical example. Focusing on a specific problem you just experienced is bound to provoke defensive answers that hide the full story. The goal is to uncover the actual approach used to plan inventory and forecasts that has been baked into the mental math or spreadsheets. Here is an example:
Suppose you have 100 units on hand, the lead time to replenish is 3 months, and the average monthly demand is 20 units? When should you order more? How much would you order? How will your answer change if expected receipts of 10 per month were scheduled to arrive? How will your answer change if the item is the item is an A, B, or C item, the cost of the item is high or low, lead time of the item is long or short? Simply put, when you schedule a production job or place a new order with a supplier, why did you do it? What triggered the decision to get more? What planning inputs were considered?
When getting answers to the above question, focus on uncovering answers to the following questions:
1. What is the underlying replenishment approach? This will typically be one of Min/Max, forecast/safety stock, Reorder Point/Order Quantity, Periodic Review/Order Up To or even some odd combination
2. How are the planning parameters, such as demand forecasts, reorder points, or Min/Max, actually calculated? It’s not enough to know that you use Min/Max. You have to know exactly how these values are calculated. Answers such as “We use history” or “We use an average” are not specific enough. You’ll need answers that clearly outline how history is used. For example, “We take an average of the last 6 months, divide that by 30 to get a daily average, and then multiply that by the lead time in days. For ‘A’ items we then multiply the lead time average by 2 and for ‘B’ items we use a multiplier of 1.5.” (While that is not an especially good technical approach, at least it has a clear logic.)
Once you have a policy well-defined, you can identify its weaknesses in order to improve it. But if the answer provided doesn’t get much further past “We use history”, then you don’t have a policy to start with. Answers will often reveal that different planners use history in different ways. Some may only consider the most recent demand, others might stock according to the average of the highest demand periods, etc. In other words, you may find that you actually have multiple ill-conceived “policies”.
3. Are forecasts used to drive replenishment planning and if so, how? Many companies will say they forecast, but their forecasts are calculated and used differently. Is the forecast used to predict what on hand inventory will be in the future, resulting in an order being triggered? Or is it used to derive a reorder point but not to predict when to order (i.e. I predict we’ll sell 10 a week so to help protect against stock out, I’ll order more when on hand gets to 15)? Is it used as a guide for the planner to help subjectively determine when they should order more? Is it used to set up blanket orders with suppliers? Some use it to drive MRP. You’ll need to know these specifics. A thorough answer to this question might look like this: “My forecast is 10 per week and my lead time is 3 weeks so I make my reorder point a multiple of that forecast, typically 2 x lead time demand or 60 unit for important items and I use a smaller multiple for less important items. (Again, not a great technical approach, but clear.)
4. What technique is actually used to generate the forecast? Is it an average, a trending model such as double exponential smoothing, a seasonal model? Does the choice of technique change depend on the type of demand data or when new demand data is available? (Spare parts and high-volume items have very different demand patterns.) How do you go about selecting the forecast model? Is this process automated? How often is the choice of model reconsidered? How often are the model parameters recomputed? What is the process used to reconsider your approach? The answer here documents how the baseline forecasts are produced. Once determined, you can conduct an analysis to identify whether other forecasting methods would improve forecast accuracy. If you aren’t documenting forecast accuracy and conducting “forecast value add” analysis then you aren’t in a position to properly assess whether the forecasts being produced are the best that they can be. You’ll miss out on opportunities to improve the process, increase forecast accuracy, and educate the business on what type of forecast error is normal and should be expected.
5. How do you use safety stock? Notice the question was not “Do you use safety stock?” In this context, and to keep it simple, the term “safety stock” means stock used to buffer inventory against supply and demand variability. All companies use buffering approaches in some way. There are some exceptions though. Maybe you are a job shop manufacturer that procures all parts to order and your customers are completely fine waiting weeks or months for you to source material, manufacture, QA, and ship. Or maybe you are high-volume manufacturer with tons of buying power so your suppliers set up local warehouses that are stocked full and ready to provide inventory to you almost immediately. If these descriptions don’t describe your company, you will definitely have some sort of buffer to protect against demand and supply variability. You may not use the “safety stock” field in your ERP but you are definitely buffering.
Answers might be provided such as “We don’t use safety stock because we forecast.” Unfortunately, a good forecast will have a 50/50 chance of being over/under the actual demand. This means you’ll incur a stock out 50% of the time without a safety stock buffer added to the forecast. Forecasts are only perfect when there is no randomness. Since there is always randomness, you’ll need to buffer if you don’t want to have abysmal service levels.
If the answer isn’t revealed, you can probe a bit more into how the varying replenishment levers are used to add possible buffers which leads to questions 6 & 7.
6. Do you ever increase the lead time or order earlier than you truly need to?
In our hypothetical example, your supplier typically takes 4 weeks to deliver and is pretty consistent. But to protect against stockouts your buyer routinely orders 6 weeks out instead of 4 weeks. The safety stock field in your ERP system might be set to zero because “we don’t use safety stock”, but in reality, the buyer’s ordering approach just added 2 weeks of buffer stock.
7. Do you pad the demand forecast?
In our example, the planner expects to consume 10 units per month but “just in case” enters a forecast of 20 per month. The safety stock field in the MRP system is left blank but the now disguised buffer stock has been smuggled into the demand forecast. This is a mistake that introduces “forecast bias.” Not only will your forecasts be less accurate but if the bias isn’t accounted for and safety stock is added by other departments, you will overstock.
The ad-hoc nature of the above approaches compounds the problems by not considering the actual demand or supply variability of the item. For example, the planner might simply make a rule of thumb that doubles the lead time forecast for important items. One-size doesn’t fit all when it comes to inventory management. This approach will substantially overstock the predictable items while substantially understocking the intermittently demanded items. You can read “Beware of Simple Rules of Thumb for Managing Inventory” to learn more about why this type of approach is so costly.
The ad-hoc nature of the approaches also ignores what happens the company is faced with a huge overstock or stock out. When trying to understand what happened, the stated policies will be examined. In the case of an overstock, the system will show zero safety stock. The business leaders will assume they aren’t carrying any safety stock, scratch their heads, and eventually just blame the forecast, declare “Our business can’t be forecasted” and stumble on. They may even blame the supplier for shipping too early and making them hold more than needed. In the case of a stock out, they will think they aren’t carrying enough and arbitrarily add more stock across many items not realizing there is in fact lots of extra safety stock baked into process. This makes it more likely inventory will need to be written off in the future.
8. What is the exact inventory terminology used? Define what you mean by safety stock, Min, reorder point, EOQ, etc. While there are standard technical definitions it’s possible that something differs, and miscommunication here will be problematic. For example, some companies refer to Min as the amount of inventory needed to satisfy lead time demand while some may define Min as inclusive of both lead time demand and safety stock to buffer against demand variability. Others may mean the minimum order quantity.
9. Is on hand inventory consistent with the policy? When your detective work is done and everything is documented, open your spreadsheet or ERP system and look at the on-hand quantity. It should be more or less in line with your planning parameters (i.e. if Min/Max is 20/40 and typical lead time demand is 10, then you should have roughly 10 to 40 units on hand at any given point in time. Surprisingly, for many companies there is often a huge inconsistency. We have observed situations where the Min/Max setting is 20/40 but the on-hand inventory is 300+. This indicates that whatever policy has been prescribed just isn’t being followed. That’s a bigger problem.
10. What are you going to do next?
Demand forecasting and inventory stocking policy need to be well-defined processes that are understood and accepted by everybody involved. There should be zero mystery.
To do this right, the demand and supply variability must be analyzed and used to compute the proper levels of safety stock. Adding buffers without an implicit understanding of what each additional unit of buffer stock is buying you in terms of service is like arbitrarily throwing a handful of ingredients into a cake recipe. A small change in ingredients can have a huge impact on what comes out of the oven – one bite too sweet but the next too sour. It is the same with inventory management. A little extra here, a little less there, and pretty soon you find yourself with costly excess inventory in some areas, painful shortages in others, no idea how you got there, and with little guidance on how to make things better.
Modern inventory optimization and demand planning software with its advanced analytics and strong basis in forecast analysis can help a good deal with this problem. But even the best software won’t help if it is used inconsistently.
Related Posts
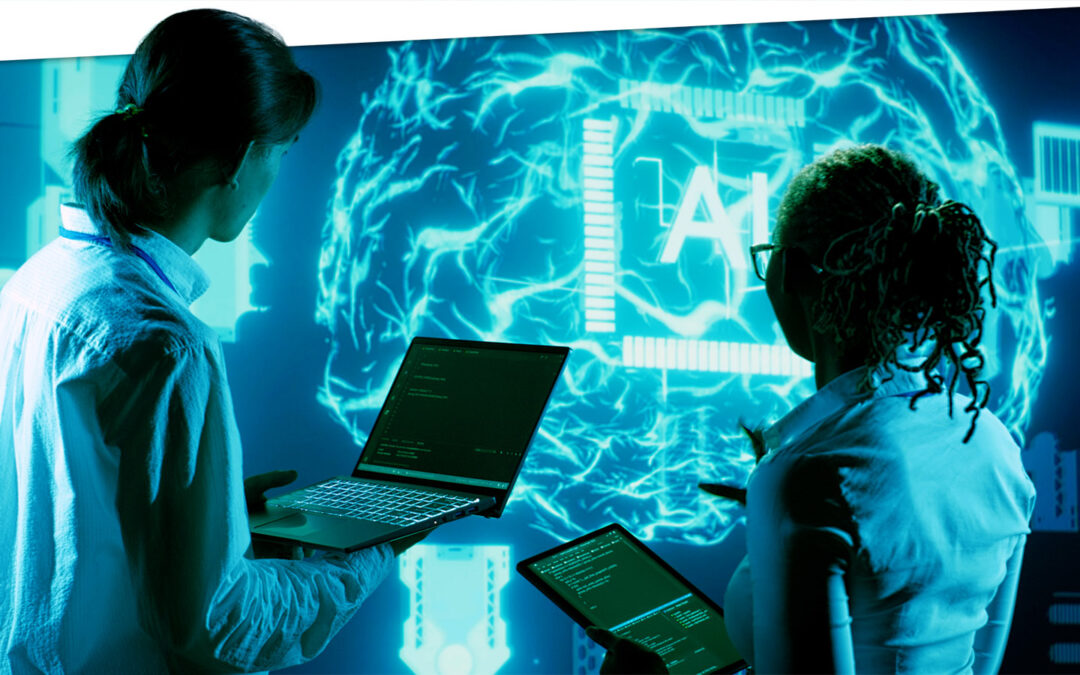
The Next Frontier in Supply Chain Analytics
We believe the leading edge of supply chain analytics to be the development of digital twins of inventory systems. These twins take the form of discrete event models that use Monte Carlo simulation to generate and optimize over the full range of operational risks. We also assert that we and our colleagues at Smart Software have played an outsized role in forging that leading edge.
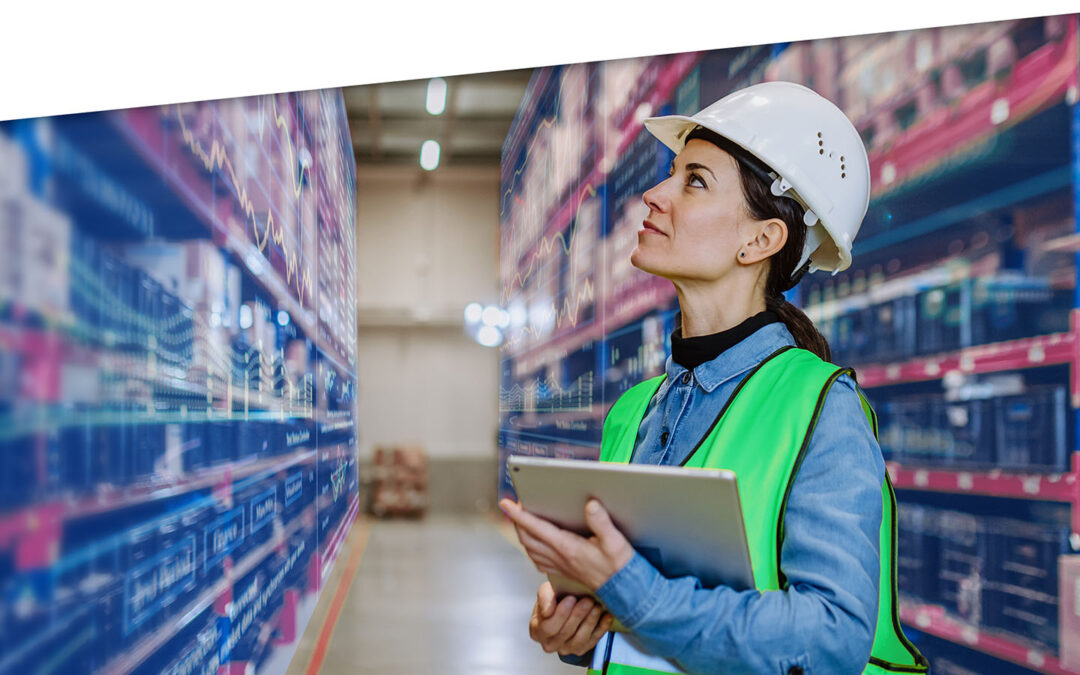
Overcoming Uncertainty with Service and Inventory Optimization Technology
In this blog, we will discuss today’s fast-paced and unpredictable market and the constant challenges businesses face in managing their inventory and service levels efficiently. The main subject of this discussion, rooted in the concept of “Probabilistic Inventory Optimization,” focuses on how modern technology can be leveraged to achieve optimal service and inventory targets amidst uncertainty. This approach not only addresses traditional inventory management issues but also offers a strategic edge in navigating the complexities of demand fluctuations and supply chain disruptions.

Centering Act: Spare Parts Timing, Pricing, and Reliability
In this article, we’ll walk you through the process of crafting a spare parts inventory plan that prioritizes availability metrics such as service levels and fill rates while ensuring cost efficiency. We’ll focus on an approach to inventory planning called Service Level-Driven Inventory Optimization. Next, we’ll discuss how to determine what parts you should include in your inventory and those that might not be necessary. Lastly, we’ll explore ways to enhance your service-level-driven inventory plan consistently.