Contributed to The Smart Forecaster by Dr. Greg Parlier (Colonel, U.S. Army, retired). Details on Dr. Parlier’s background conclude the post.
For over two decades, the General Accounting Office (GAO) has indicated that the Defense Department’s logistics management has been ineffective and wasteful, and that the Services lack strategic plans to improve overall inventory management and supply chain performance.
For the US Army, this problem is directly related to a persistent inability to link inventory investment levels and policies with supply chain effectiveness to achieve combat equipment readiness objectives required for globally deployed forces. This shortcoming has been attributed to numerous complexities associated with managing geographically dispersed, independently operating organizations, further compounded by a lack of visibility, authority and accountability across this vast global enterprise.
Unlike the corporate world, where powerful forces encourage innovation to drive competitiveness and efficiency, the Army is not a revenue generating organization focused on “quarterly earnings” and profitability. Certainly, the Army wants to be an efficient consumer of resources—but unlike the private sector’s focus on profit as a bottom line, the surrogate motivator for the Army is ‘force readiness’. This includes equipment availability and weapon system readiness for current operations in Afghanistan, as well as future capability requirements directed by the National Command Authority.
To sustain that equipment availability, the Army must synchronize disparate organizational components using myriad processes with disconnected legacy management information systems across numerous supply support activities which frequently relocate to support deploying forces.
Today, while still engaged in Afghanistan, the Army is also committed to a comprehensive and ongoing transformation. Central to this effort is recognition that dramatic improvements must be achieved in logistics operations and supply chain management. Owning one of the world’s largest and most complex supply chains, the Army is now investing in historically unprecedented efforts to fully capitalize on the promises offered by new information-based technologies. For example, the “Single Army Logistics Enterprise” is believed to be the most ambitious and expensive Enterprise Resource Planning (ERP) implementation project ever undertaken.
These ERP implementation projects have met with very mixed results. While the evidence suggests that dramatic performance improvements for competitive advantage can be achieved in the commercial sector, this has occurred only where so called “IT solutions” are applied to an underlying foundation of mature, efficient and appropriate business processes.
The reality of most cases in recent years, however, has not been this success. Rather, attempts have been made to “bolt on” a solution (like an ERP system, for example) to existing business processes, in misguided efforts to replicate legacy management practices. Such efforts to automate existing processes have, all too often, simply created chaos. In fact, these attempts have not only failed to achieve anticipated improvements, but have actually resulted in reduced performance.
The general pattern has been: the greater the IT investment and organizational scope, the more likely “failure” occurs, in the form of cost overruns, missed schedules, and even project failure—where the effort has finally been abandoned.
We believe the way to enable a coordinated, comprehensive approach for logistics transformation is by creating an “engine for innovation” to accelerate and sustain continuous performance improvement for Army logistics and supply chain management. We are developing a ‘Center for Innovation in Logistics Systems’ to systematically evaluate major organizational components, conduct root cause analyses, diagnose structural disorders and prescribe integrated solutions. We have now identified several ‘catalysts for innovation’ to reduce supply side variability and demand uncertainty—the proximate causes of the notorious ‘bull whip effect’. These include what we refer to as the ‘readiness equation’, ‘mission-based forecasting’, ‘readiness-based sparing’ and ‘readiness responsive retrograde’.
Our goal is to develop a comprehensive modeling capacity to generate and test these innovation catalysts along with several other initiatives in order to estimate cost effective approaches before they are adopted as policy and implemented in practice. We are looking at performance analysis, organizational design, management information and decision support concepts, enterprise systems engineering and workforce considerations including human capital investment needs.
Examining the ‘catalysts’ in isolation, we have seen significant potential for improvement which could yield hundreds of millions of dollars in savings. When combined into new, integrated management practices, however, the potential magnitude for improvement is truly dramatic—billions of dollars in further savings are likely. More importantly, it becomes possible to relate investment levels to current readiness and future capabilities.
The center is capable of developing ‘management innovation as a strategic technology’ by integrating advanced analytics with transformational strategic planning. By harnessing, focusing and applying the power of analysis, we are promoting both qualitative and quantitative common sense—the compelling analytical arguments for necessary change to pursue a common vision. With this power, we are beginning to educate the Army’s leadership, motivate logistics managers to action and provide a source for innovation the culture can embrace. During our journey, we have certainly adapted and applied much from both academic domains and the corporate sector. They, in turn, might now benefit from what we have been able to learn and achieve as well.
Prior to his retirement, Colonel Parlier was the Army’s senior, most experienced operations research analyst and served as Army Aviation and Missile Command’s (AMCOM) Deputy Commander for Transformation. He is the author of Transforming U.S. Army Supply Chains: Strategies for Management Innovation, describing the analytical framework of a multi-year Army Materiel Command (AMC) research and development project providing operations research insights for use by the Army and Department of Defense.
Related Posts
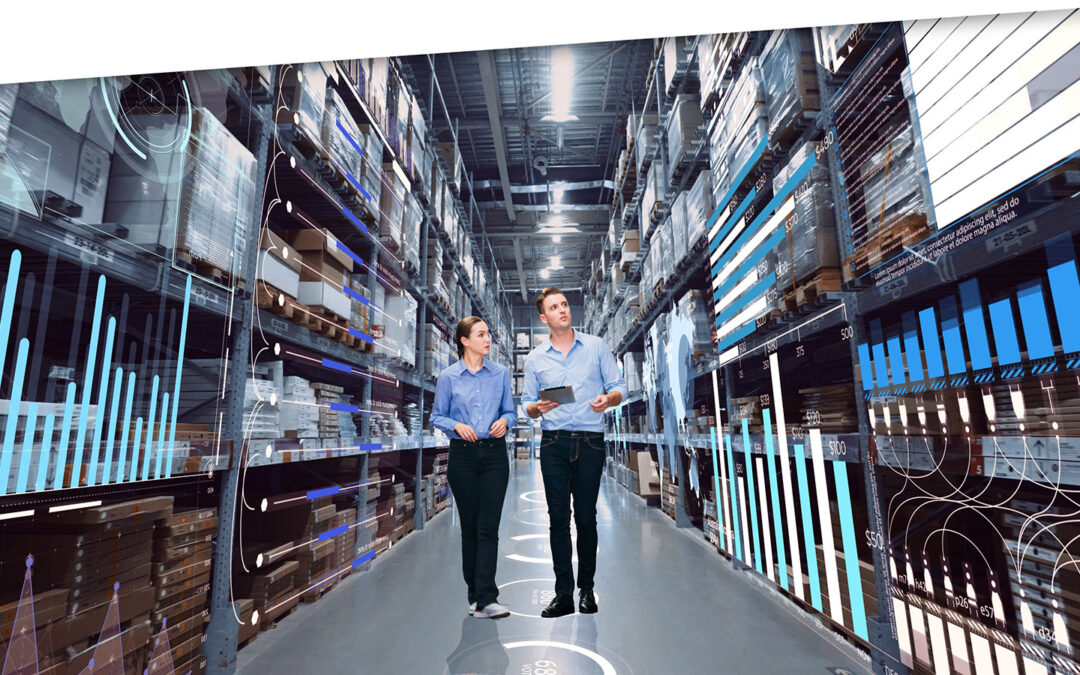
Make AI-Driven Inventory Optimization an Ally for Your Organization
In this blog, we will explore how organizations can achieve exceptional efficiency and accuracy with AI-driven inventory optimization. Traditional inventory management methods often fall short due to their reactive nature and reliance on manual processes. Maintaining optimal inventory levels is fundamental for meeting customer demand while minimizing costs. The introduction of AI-driven inventory optimization can significantly reduce the burden of manual processes, providing relief to supply chain managers from tedious tasks.

Future-Proofing Utilities: Advanced Analytics for Supply Chain Optimization
Utilities in the electrical, natural gas, urban water, and telecommunications fields are all asset-intensive and reliant on physical infrastructure that must be properly maintained, updated, and upgraded over time. Maximizing asset uptime and the reliability of physical infrastructure demands effective inventory management, spare parts forecasting, and supplier management. A utility that executes these processes effectively will outperform its peers, provide better returns for its investors and higher service levels for its customers, while reducing its environmental impact.
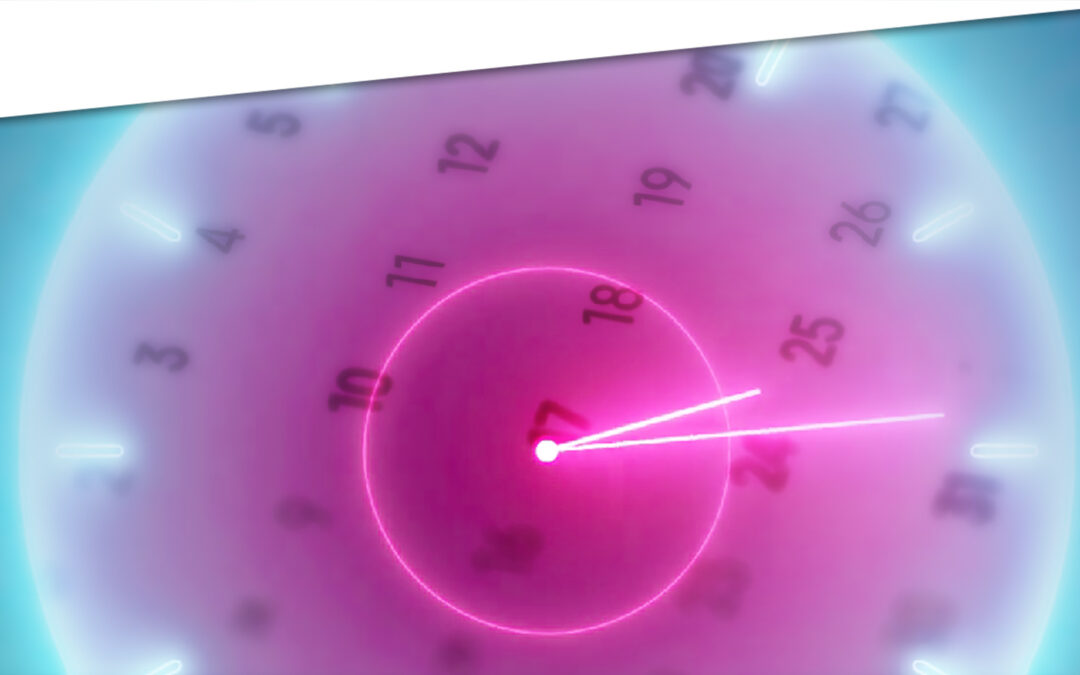
Daily Demand Scenarios
In this Videoblog, we will explain how time series forecasting has emerged as a pivotal tool, particularly at the daily level, which Smart Software has been pioneering since its inception over forty years ago. The evolution of business practices from annual to more refined temporal increments like monthly and now daily data analysis illustrates a significant shift in operational strategies.