Problem
Critical enterprise data is often disparately stored across multiple IT systems and is only accessible via limited reporting views or manually exported spreadsheets. Producing reports that track on-hand inventory, supplier lead times, forecast accuracy, stockouts, and excess & obsolete inventory requires countless hours of manual effort. This means that getting updated information, when you need it, is not always possible. And worst of all, there is no ability to gather automated insights from the vast amounts of data being collected. This means that problems reveal themselves only after it is too late, and opportunities for improvement are overlooked, further contributing to poor performance.
Solution
Smart Operational Analytics (SOA™) is available on Smart’s Inventory Planning and Optimization Platform, Smart IP&O. You can build and deploy any desired custom report or simply take advantage of the standard reports that provide a fast, easily understood, current perspective on the state of your inventory, historical service levels, actual supplier lead times, forecast accuracy, and inventory trends. Already leveraging an alternative BI Studio? Smart IP&O’s curated data model can be easily exposed to Power BI, Domo, Tableau, Grow and other solutions. Smart’s embedded BI and ML studio enables you to build, train, and deploy ML models without writing any code to drive automated prescriptive insights.
Register to Watch the Demo
Smart Operational Analytics
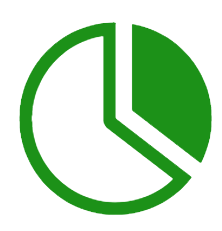
Inventory Analytics
Quantify inventory value
Inventory segmentation
Inventory classification
Trend metrics over time
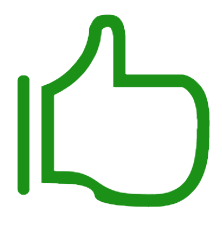
Operational Performance
Measure service level performance
Measure fill rate performance
Calculate turns, holding & ordering costs
Trend metrics over time
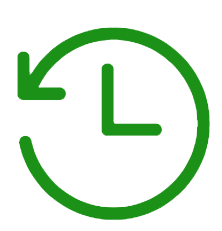
Supplier Insights
Measure supplier performance
Compare supplier lead times
Rank suppliers across available metrics
Trend metrics over time
Who is Operational Analytics for?
Smart Operational Analytics is for executives, planners, and operations professionals who seek to:
- Measure inventory costs and performance in real time.
- Assess and compare Supplier performance.
- Identify root causes of stockouts, excess inventory, and late deliveries.
- share KPI’s such as service levels, turns, costs, and more across the organization.
What questions can Operational Analytics answer?
- What does my inventory look like? By value, count, classification?
- Is my inventory trending up, down, or the same?
- How much of my inventory is overstocked, understocked, or acceptable?
- Can inventory be transferred from overstocked locations to under stocked locations?
- Can existing supplier orders be cancelled or deferred?
- What are my current turns, service levels, and fill rates and how do they trend over time?
- How many out of stock events occurred this week, this month, this quarter?
- How are my suppliers performing, how do they compare?
- What is my supplier lead time and how has it changed over time?
Inventory and supplier reporting for your enterprise
Smart Operational Analytics empowers you to:
- Benchmark service performance and inventory costs.
- Benchmark supplier performance.
- Assess and Classify Inventory by class, stage, and more.
- Share metrics with the organization.