A fundamental aspect of supply chain management is accurate demand forecasting. Some product items have an intermittent demand pattern that makes them all but impossible to forecast with traditional, smoothing-based forecasting methods. We address the problem of forecasting intermittent demand (or irregular demand), i.e. random demand with a large proportion of zero values. This pattern is characteristic of demand for companies that manage large inventories of service and spare parts in industries such as aviation, aerospace, automotive, high tech, and electronics, as well as in MRO (Maintenance, Repair and Overhaul).
Accurate forecasting of demand is important in inventory control, but the intermittent nature of demand makes forecasting especially difficult for service parts planning. Similar problems arise when an organization manufactures slow-moving items and requires sales forecasts for planning purposes. Because forecasts of intermittent and lumpy demand have been so unreliable, most companies forecast inventory requirements relying primarily on subjective business knowledge, forecast only a fraction of their higher volume inventory, use simple “rule of thumb” estimates, or traditional statistical forecasting that incorrectly assumes a particular type demand distribution for inventory control.
Learn industry best practices on how to improve intermittent demand forecasting and create supply chain efficiencies in the articles below.
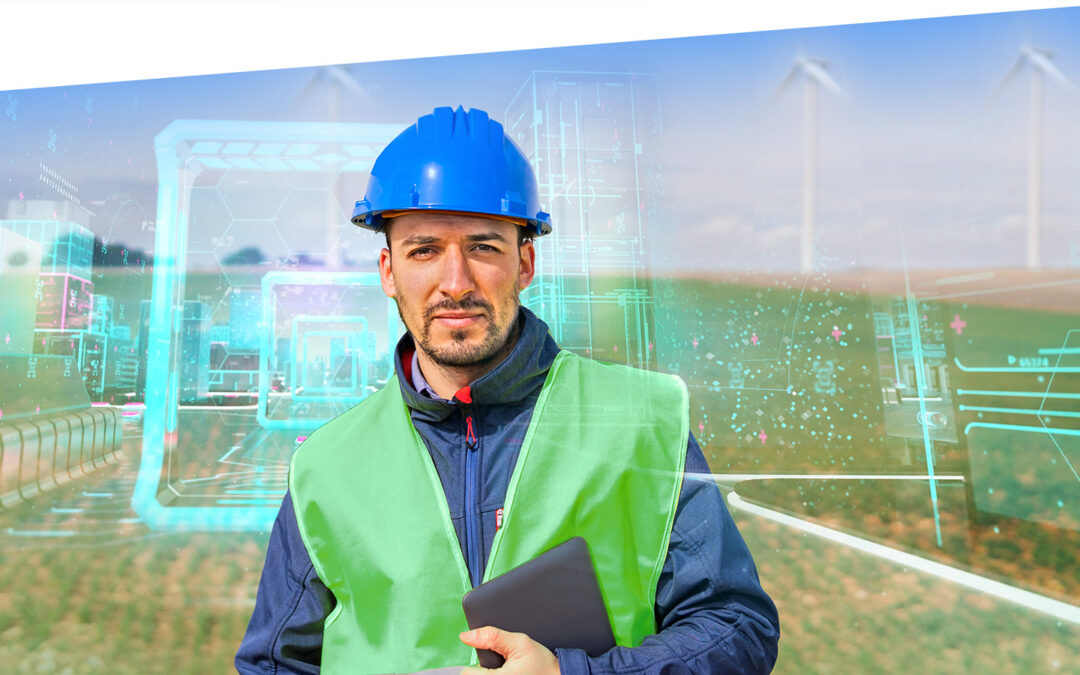
7 Digital Transformations for Utilities that will Boost MRO Performance
Utilities in the electrical, natural gas, urban water, and telecommunications fields are all asset-intensive and reliant on physical infrastructure that must be properly maintained, updated, and upgraded over time. Maximizing asset uptime and the reliability of physical infrastructure demands effective inventory management, spare parts forecasting, and supplier management. A utility that executes these processes effectively will outperform its peers, provide better returns for its investors and higher service levels for its customers, while reducing its environmental impact.
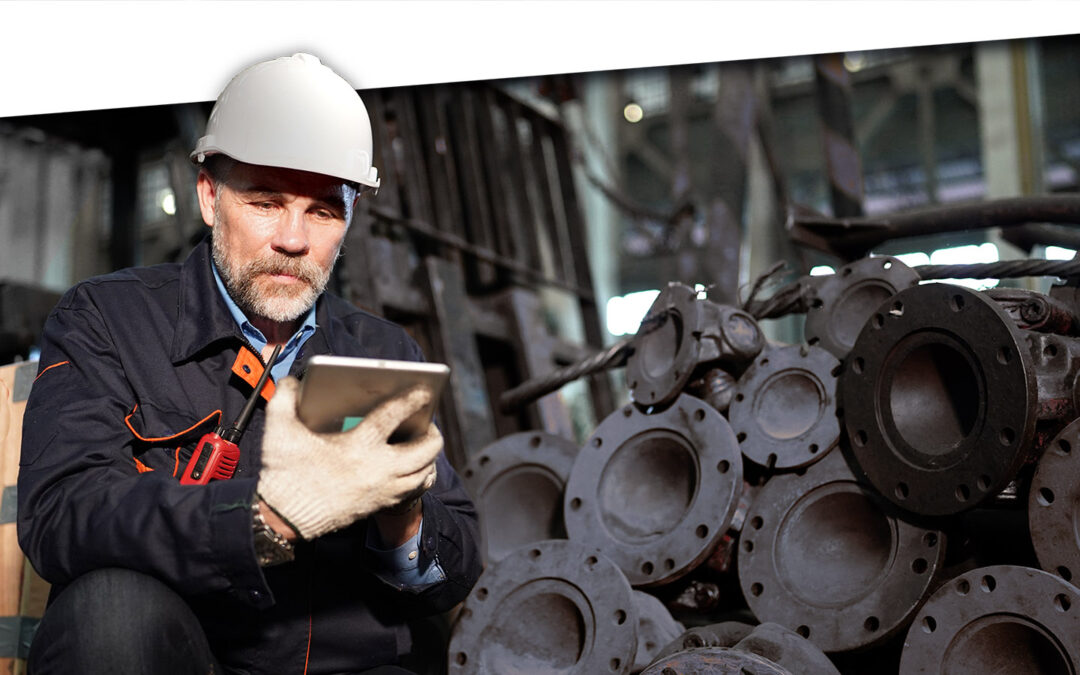
6 Do’s and Don’ts for Spare Parts Planning
Managing spare parts inventories can feel impossible. You don’t know what will break and when. Feedback from mechanical departments and maintenance teams is often inaccurate. Planned maintenance schedules are often shifted around, making them anything but “planned.” Usage (i.e., demand) patterns are most often extremely intermittent, i.e., demand jumps randomly between zero and something else, often a surprisingly big number.

Probabilistic Forecasting for Intermittent Demand
The New Forecasting Technology derives from Probabilistic Forecasting, a statistical method that accurately forecasts both average product demand per period and customer service level inventory requirements.
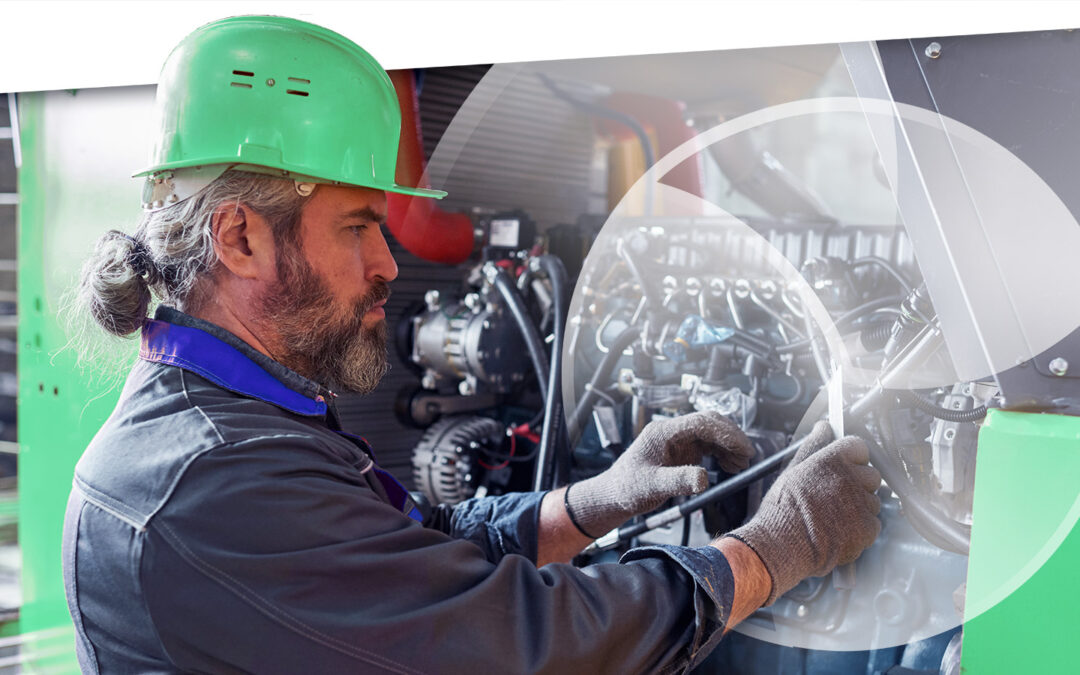
Service Parts Planning: Planning for consumable parts vs. Repairable Parts
When deciding on the right stocking parameters for spare and replacement parts, it is important to distinguish between consumable and repairable servoce parts. These differences are often overlooked by inventory planning software and can result in incorrect estimates of what to stock. Different approaches are required when planning for consumables vs. repairable service parts.
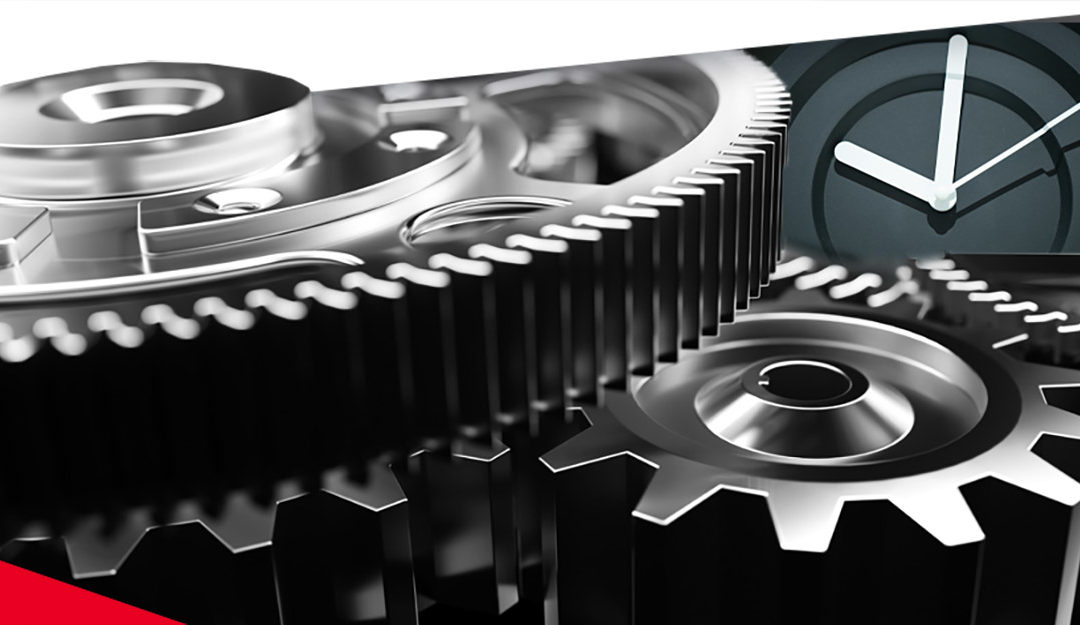
A Beginner’s Guide to Downtime and What to Do about It
If you manufacture things for sale, you need machines to make those things. If your machines are up and running, you have a fighting chance to make money. If your machines are down, you lose opportunities to make money.
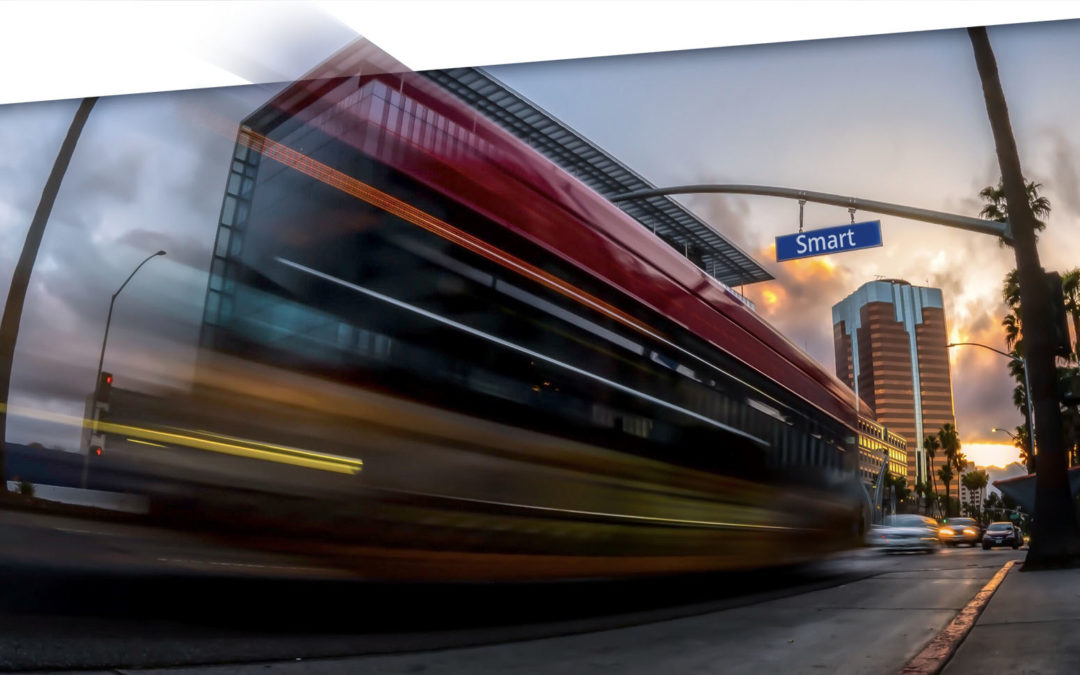
Thoughts on Spare Parts Planning for Public Transit
The Covid19 pandemic has placed unusual stress on public transit agencies. This stress forces agencies to look again at their processes and equipment. This blog focuses on bus systems and their practices for spare parts planning and management. However, there are lessons here for other types of public transit, including rail and light rail
The Problem
Some product items have an intermittent demand pattern that makes them all but impossible to forecast with traditional, smoothing-based forecasting methods. Items with intermittent demand – also known as lumpy, volatile, variable or unpredictable demand – have many zero or low volume values interspersed with random spikes of demand that are often many times larger than the average. This problem is especially prevalent in companies that manage large inventories of service and spare parts in industries such as aviation, aerospace, automotive, high tech, and electronics, as well as in MRO (Maintenance, Repair and Overhaul).
Intermittent demand
In these businesses, as much as 80% of the parts and product items may have intermittent or lumpy demand. Intermittent demand makes it difficult to accurately estimate the safety stock and service level inventory requirements needed for successful supply chain planning. Because forecasts of intermittent and lumpy demand have been so unreliable, most companies forecast inventory requirements relying primarily on subjective business knowledge, forecast only a fraction of their higher volume inventory, use simple “rule of thumb” estimates, or traditional statistical forecasting that incorrectly assumes a particular type demand distribution for inventory control. The result is that billions of dollars are wasted every year because of either excess inventory costs or poor customer service due to stock-outs.
Intermittent demand – also known as lumpy, volatile, variable or unpredictable demand.
The Smart Solution
SmartForecasts and Smart Inventory Optimization use a unique empirical probabilistic forecasting approach that results in accurate forecasts of inventory requirements where demand is intermittent. The solution works particularly well whenever demand does not conform to a simple normal distribution. Our patented, APICS award-winning “bootstrapping” technology rapidly generates tens of thousands of possible scenarios of future demand sequences and cumulative demand values over an item’s lead time. These scenarios are statistically similar to the item’s observed data, and they capture the relevant details of intermittent demand without relying on the assumptions commonly made about the nature of demand distributions by traditional forecasting methods. The result is a highly accurate forecast of the entire distribution of cumulative demand over an item’s full lead time. With the information these demand distributions provide, you can easily plan your company’s safety stock and service level inventory requirements for thousands of intermittently demanded items with nearly 100% accuracy.
The Benefits
Companies using our powerful intermittent demand forecasting and planning solution typically reduce standing inventory by 20% in the first year, increase parts availability 10-20%, and reduce the need for and associated costs of emergency transshipment to close gaps in their supply chain. Repair and service parts inventories are truly optimized, leading to more efficient operations, improvements in customer service, and significantly less cash tied up in inventory.
White Paper: Smart Software Gen2
In this white paper, we introduce “Gen2”, our next generation of probabilistic modeling technology that powers the Smart IP&O Platform. We recount the evolution of Smart Software’s forecasting methods and we detail how Gen2 substantially expands the capabilities that have made Gen1 so useful to so many companies. Finally, we will also give a high-level view of the probability math behind Gen2 . Fill in this form and we'll email you the paper.