A fundamental aspect of supply chain management is accurate demand forecasting. Some product items have an intermittent demand pattern that makes them all but impossible to forecast with traditional, smoothing-based forecasting methods. We address the problem of forecasting intermittent demand (or irregular demand), i.e. random demand with a large proportion of zero values. This pattern is characteristic of demand for companies that manage large inventories of service and spare parts in industries such as aviation, aerospace, automotive, high tech, and electronics, as well as in MRO (Maintenance, Repair and Overhaul).
Accurate forecasting of demand is important in inventory control, but the intermittent nature of demand makes forecasting especially difficult for service parts planning. Similar problems arise when an organization manufactures slow-moving items and requires sales forecasts for planning purposes. Because forecasts of intermittent and lumpy demand have been so unreliable, most companies forecast inventory requirements relying primarily on subjective business knowledge, forecast only a fraction of their higher volume inventory, use simple “rule of thumb” estimates, or traditional statistical forecasting that incorrectly assumes a particular type demand distribution for inventory control.
Learn industry best practices on how to improve intermittent demand forecasting and create supply chain efficiencies in the articles below.
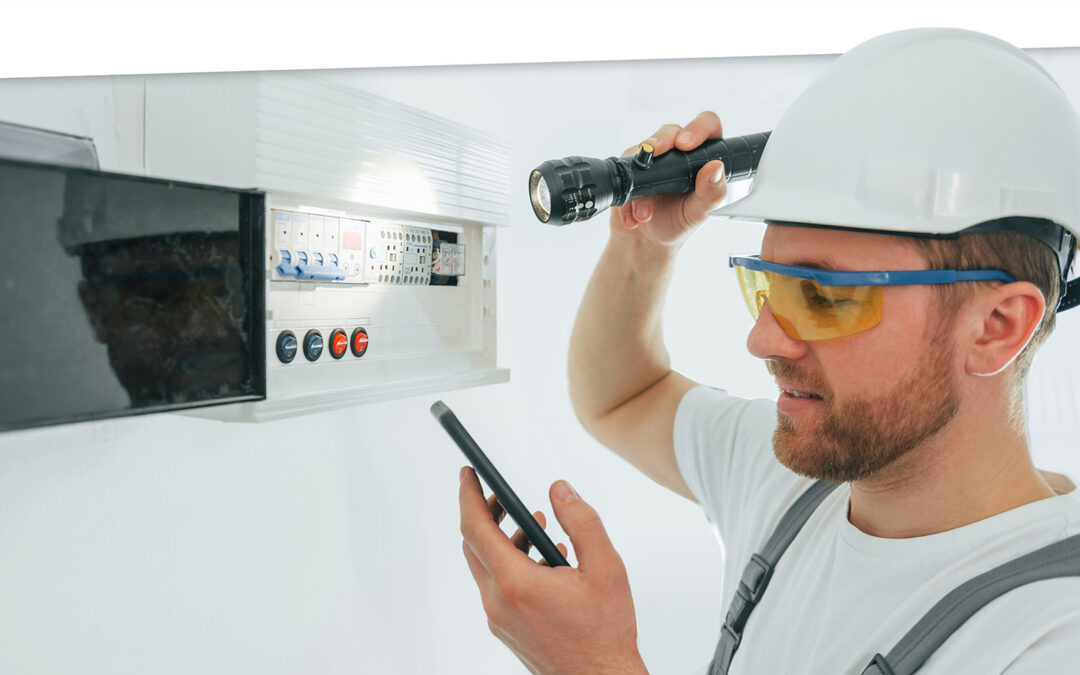
Electric Utilities’ Problems with Spare Parts
Every organization that runs equipment needs spare parts. All of them must cope with issues that are generic no matter what their business. Some of the problems, however, are industry specific. This post discusses one universal problem that manifested in a nuclear plant and one that is especially acute for any electric utility.
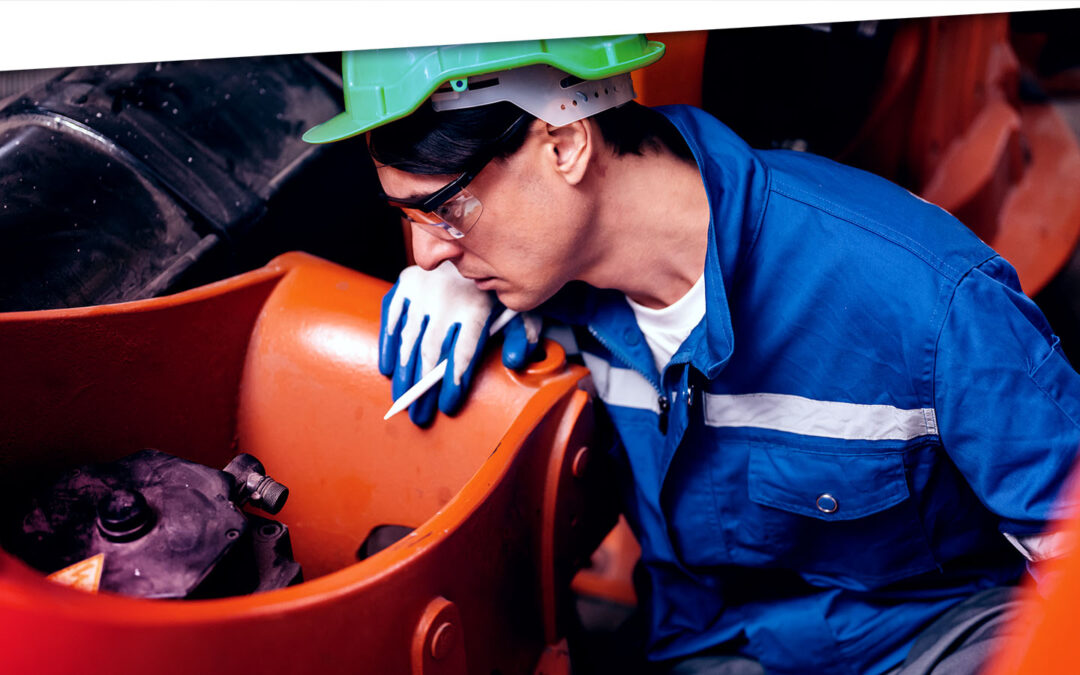
How to Forecast Spare Parts with Low Usage
What do you do when you are forecasting an intermittently demanded item, such as a spare part, with an average demand of less than one unit per month? Most of the time, the demand is zero, but the part is significant in a business sense; it can’t be ignored and must be forecasted to be sure you have adequate stock.
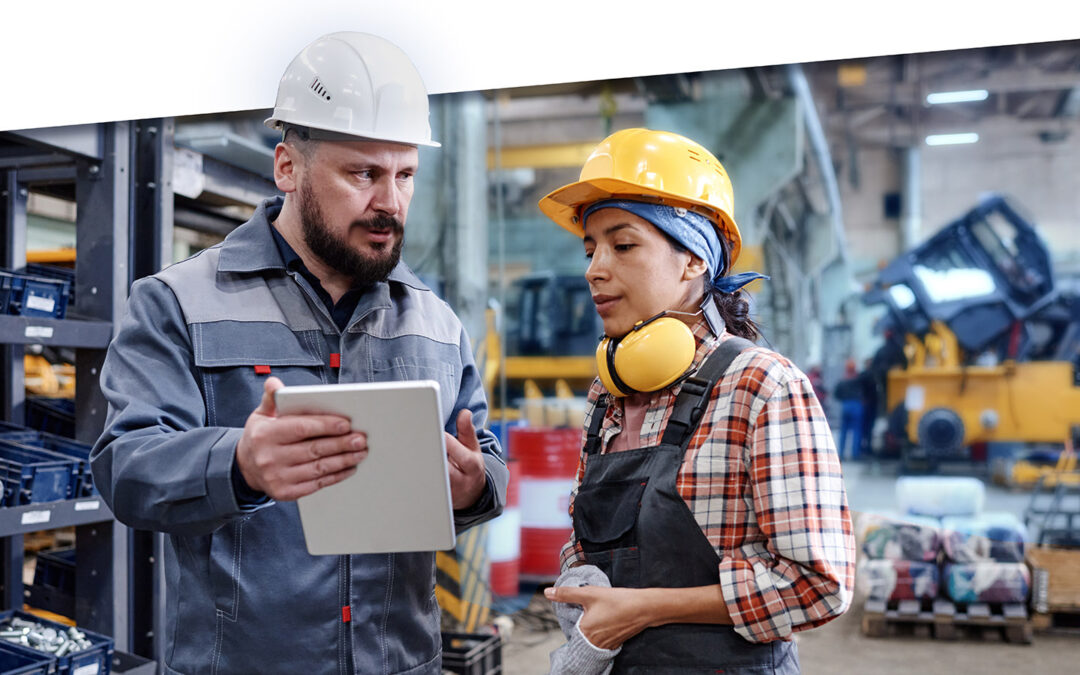
Spare Parts, Replacement Parts, Rotables, and Aftermarket Parts
Those new to the parts planning game are often confused by the many variations in the names of parts. This blog points out distinctions that do or do not have operational significance for someone managing a fleet of spare parts and how those differences impact inventory planning.
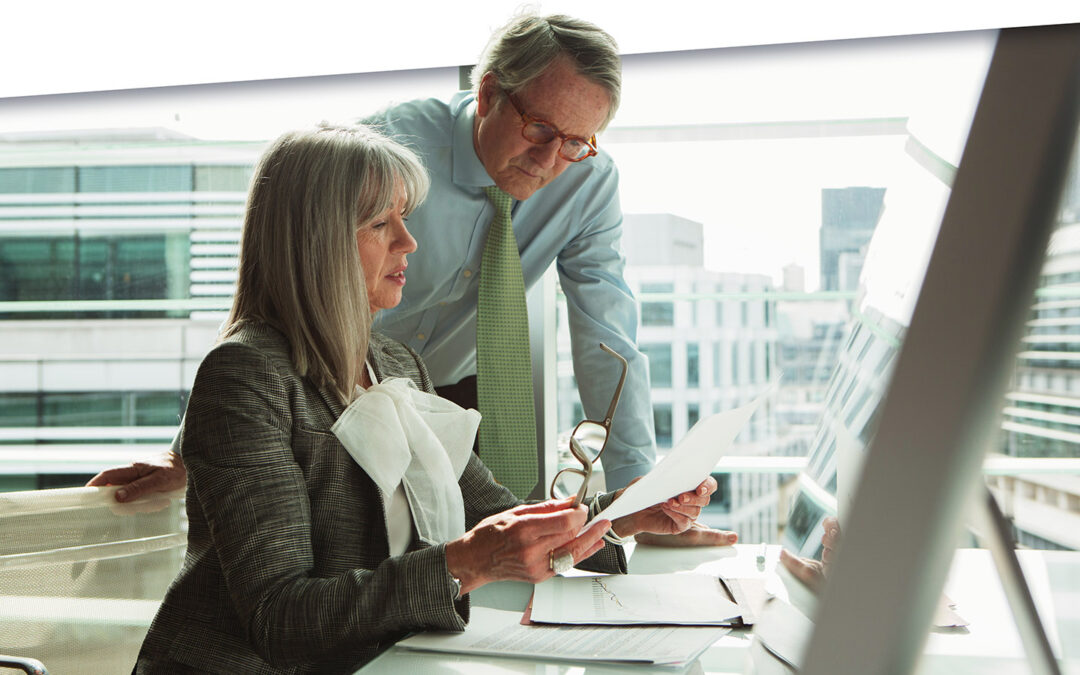
The top 3 reasons why your spreadsheet won’t work for optimizing reorder points on spare parts
We often encounter Excel-based reorder point planning methods. In this post, we’ve detailed an approach that a customer used prior to proceeding with Smart. We describe how their spreadsheet worked, the statistical approaches it relied on, the steps planners went through each planning cycle, and their stated motivations for using (and really liking) this internally developed spreadsheet.
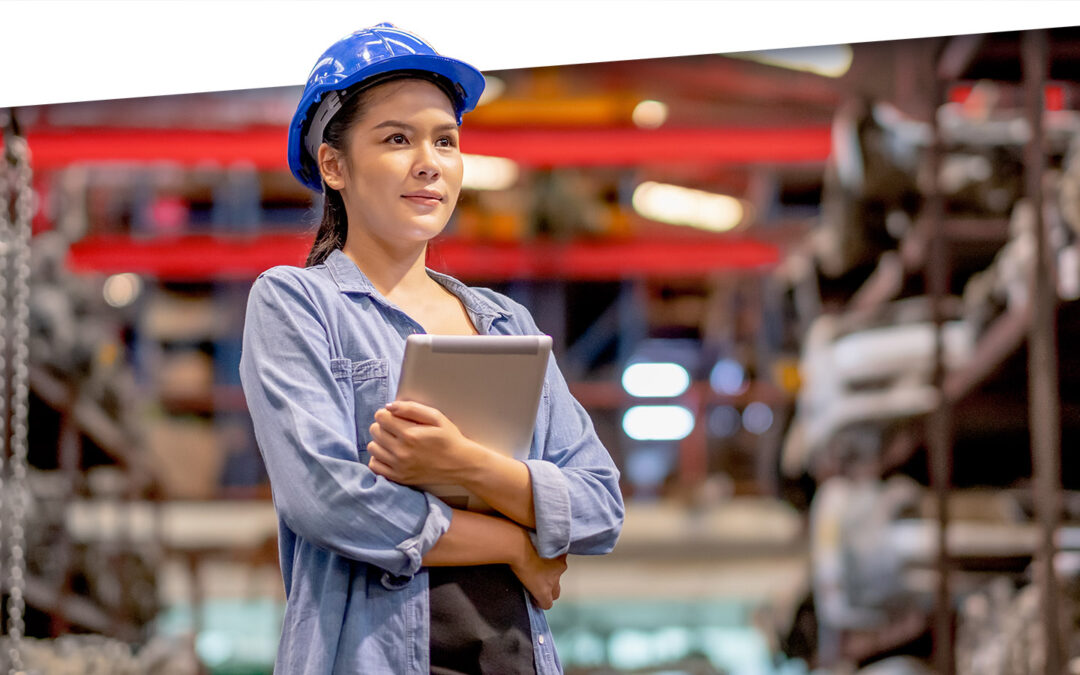
Spare Parts Planning Isn’t as Hard as You Think
When managing service parts, you don’t know what will break and when because part failures are random and sudden. As a result, demand patterns are most often extremely intermittent and lack significant trend or seasonal structure. The number of part-by-location combinations is often in the hundreds of thousands, so it’s not feasible to manually review demand for individual parts. Nevertheless, it is much more straightforward to implement a planning and forecasting system to support spare parts planning than you might think.
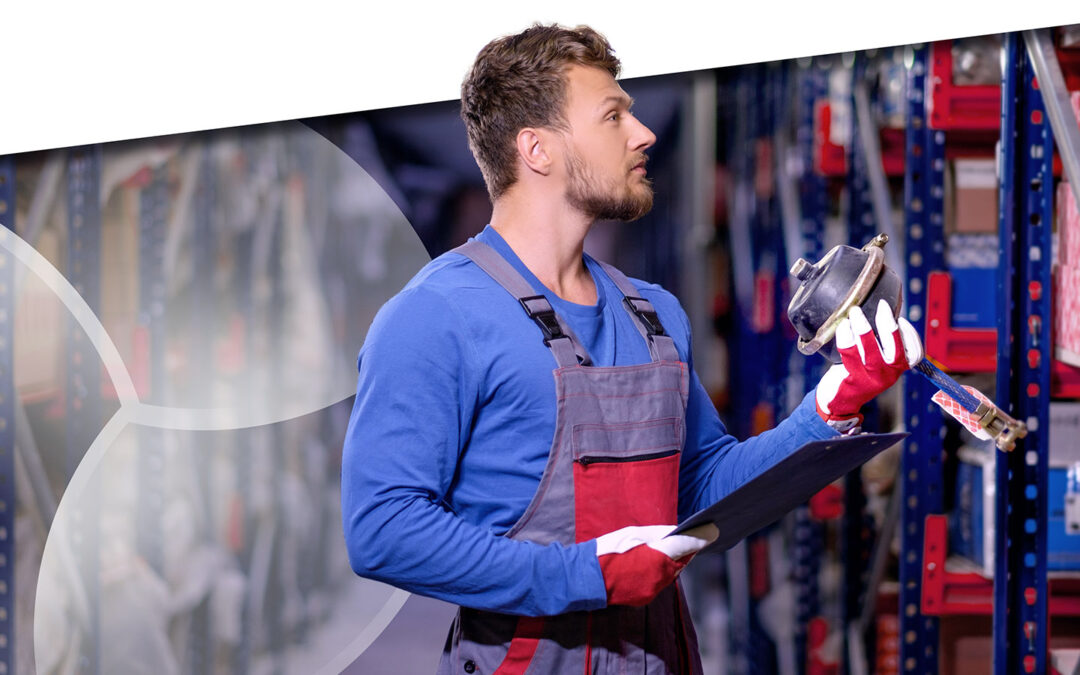
Service-Level-Driven Planning for Service Parts Businesses
Service-Level-Driven Service Parts Planning is a four-step process that extends beyond simplified forecasting and rule-of-thumb safety stocks. It provides service parts planners with data-driven, risk-adjusted decision support.
The Problem
Some product items have an intermittent demand pattern that makes them all but impossible to forecast with traditional, smoothing-based forecasting methods. Items with intermittent demand – also known as lumpy, volatile, variable or unpredictable demand – have many zero or low volume values interspersed with random spikes of demand that are often many times larger than the average. This problem is especially prevalent in companies that manage large inventories of service and spare parts in industries such as aviation, aerospace, automotive, high tech, and electronics, as well as in MRO (Maintenance, Repair and Overhaul).
Intermittent demand
In these businesses, as much as 80% of the parts and product items may have intermittent or lumpy demand. Intermittent demand makes it difficult to accurately estimate the safety stock and service level inventory requirements needed for successful supply chain planning. Because forecasts of intermittent and lumpy demand have been so unreliable, most companies forecast inventory requirements relying primarily on subjective business knowledge, forecast only a fraction of their higher volume inventory, use simple “rule of thumb” estimates, or traditional statistical forecasting that incorrectly assumes a particular type demand distribution for inventory control. The result is that billions of dollars are wasted every year because of either excess inventory costs or poor customer service due to stock-outs.
Intermittent demand – also known as lumpy, volatile, variable or unpredictable demand.
The Smart Solution
SmartForecasts and Smart Inventory Optimization use a unique empirical probabilistic forecasting approach that results in accurate forecasts of inventory requirements where demand is intermittent. The solution works particularly well whenever demand does not conform to a simple normal distribution. Our patented, APICS award-winning “bootstrapping” technology rapidly generates tens of thousands of possible scenarios of future demand sequences and cumulative demand values over an item’s lead time. These scenarios are statistically similar to the item’s observed data, and they capture the relevant details of intermittent demand without relying on the assumptions commonly made about the nature of demand distributions by traditional forecasting methods. The result is a highly accurate forecast of the entire distribution of cumulative demand over an item’s full lead time. With the information these demand distributions provide, you can easily plan your company’s safety stock and service level inventory requirements for thousands of intermittently demanded items with nearly 100% accuracy.
The Benefits
Companies using our powerful intermittent demand forecasting and planning solution typically reduce standing inventory by 20% in the first year, increase parts availability 10-20%, and reduce the need for and associated costs of emergency transshipment to close gaps in their supply chain. Repair and service parts inventories are truly optimized, leading to more efficient operations, improvements in customer service, and significantly less cash tied up in inventory.
White Paper: Smart Software Gen2
In this white paper, we introduce “Gen2”, our next generation of probabilistic modeling technology that powers the Smart IP&O Platform. We recount the evolution of Smart Software’s forecasting methods and we detail how Gen2 substantially expands the capabilities that have made Gen1 so useful to so many companies. Finally, we will also give a high-level view of the probability math behind Gen2 . Fill in this form and we'll email you the paper.