Supply chain management involves planning and implementation. Demand planning, based on a statistical projection, evaluates inventory, marketing, and demand-influencing factors and defines where to distribute products to fulfill the anticipated demand. Usually kicks off the planning side of SCM.
To increase the precision of the demand forecasts utilized in the supply chain, companies invest a lot of time and money in forecasting activities. The objectives of a precise demand plan and a lean supply chain process may be hampered by a bad process design.
Learn industry best practices on how to improve demand planning and create supply chain efficiencies.
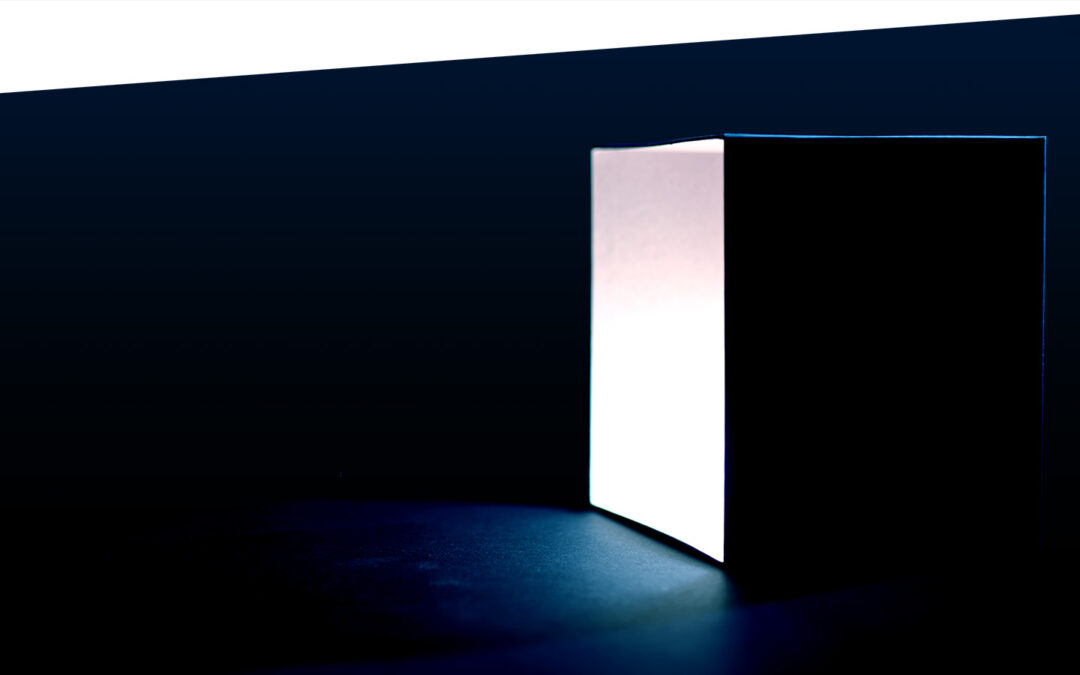
Is your demand planning and forecasting process a black box?
There’s one thing I’m reminded of almost every day at Smart Software that puzzle me: most companies do not understand how forecasts are created, and stocking policies are determined. It’s an organizational black box. Here is an example from a recent sales call:
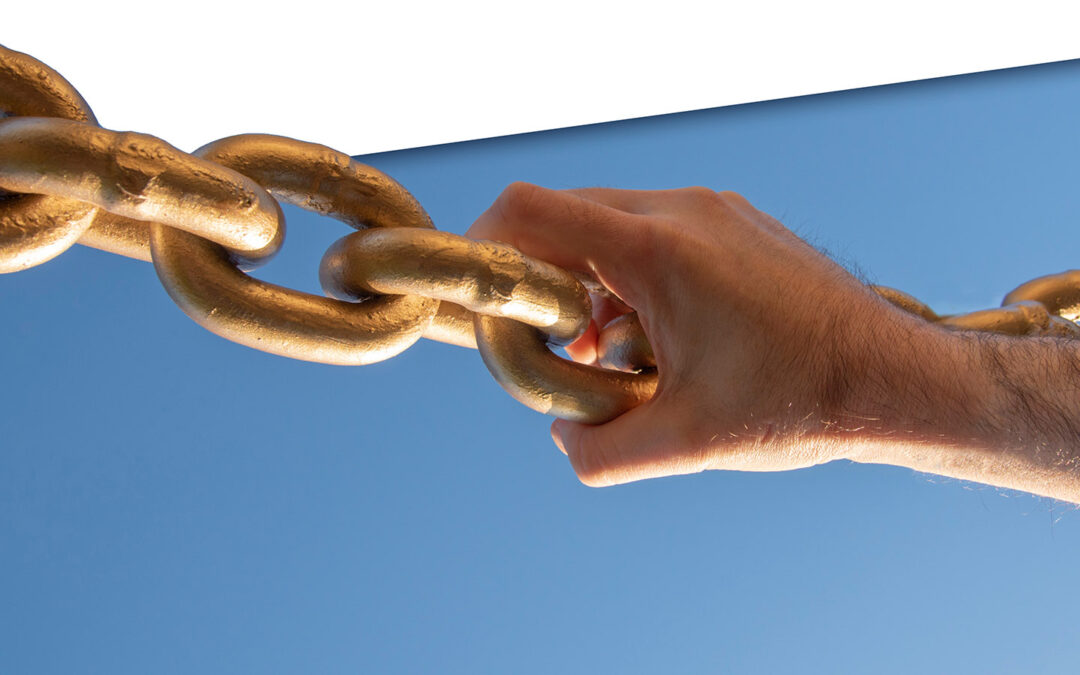
The Role of Trust in the Demand Forecasting Process Part 2: What do you Trust
Regardless of how much effort is poured into training forecasters and developing elaborate forecast support systems, decision-makers will either modify or discard the predictions if they do not trust them.”
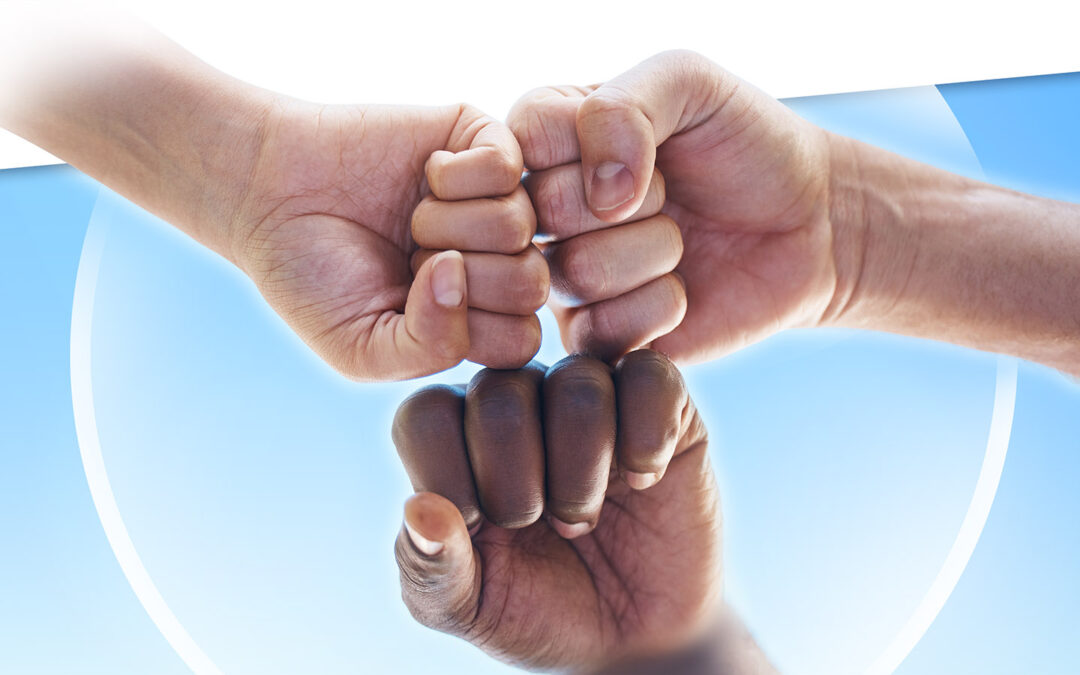
The Role of Trust in the Demand Forecasting Process Part 1: Who do you Trust
Trust is always a two-way street, but let’s stay on the demand forecaster’s side. What characteristics of and actions by forecasters and demand planners build trust in their work? Key to building trust among the users of forecasts are perceptions of forecaster and demand planner competence and objectivity.
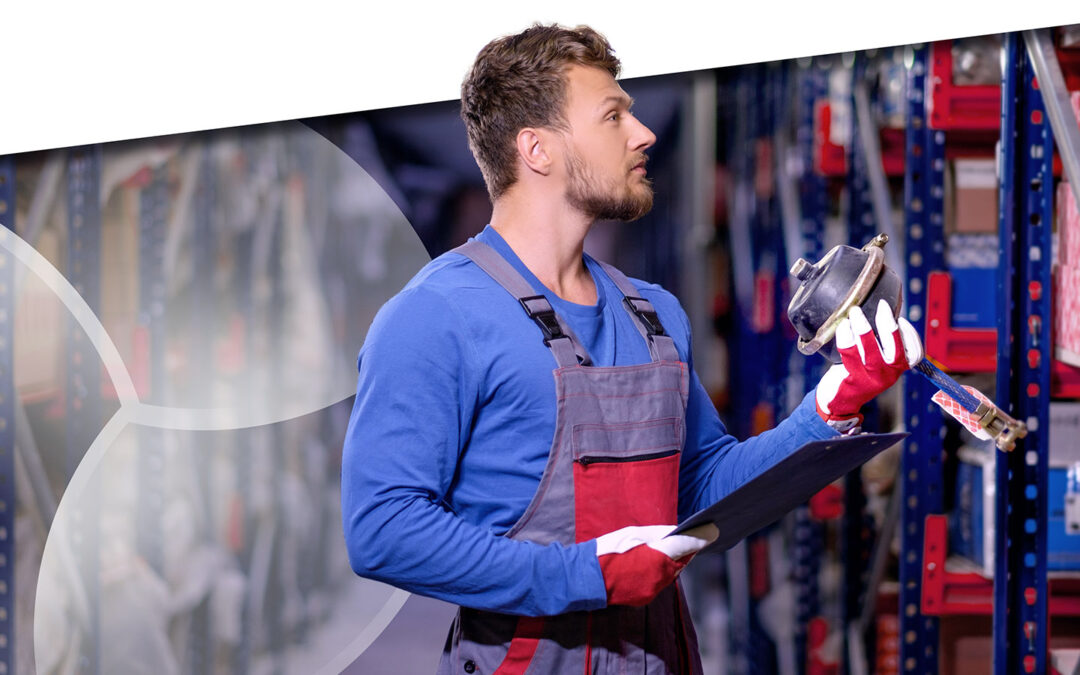
Service-Level-Driven Planning for Service Parts Businesses
Service-Level-Driven Service Parts Planning is a four-step process that extends beyond simplified forecasting and rule-of-thumb safety stocks. It provides service parts planners with data-driven, risk-adjusted decision support.
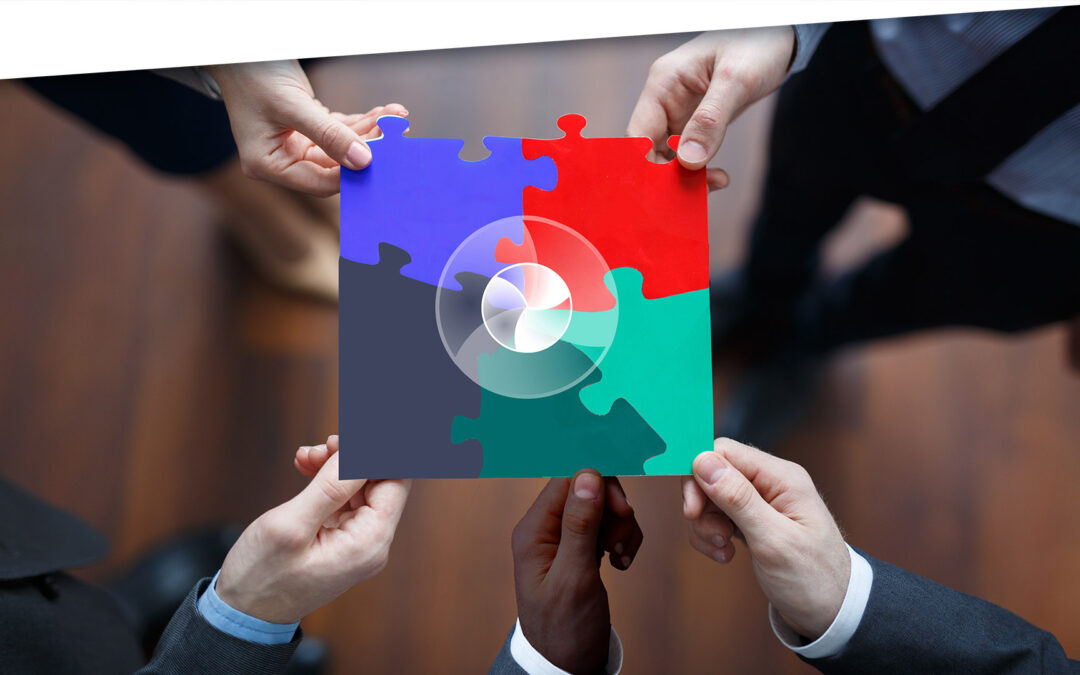
Beyond the forecast – Collaboration and Consensus Planning
The whole point of demand forecasting is to establish the best possible view of future demand. This requires that we draw upon the best data and inputs we can get, leverage statistics to capture underlying patterns, put our heads together to apply overrides based on business knowledge, and agree on a consensus demand plan that serves as cornerstone to the company’s overall demand plan.
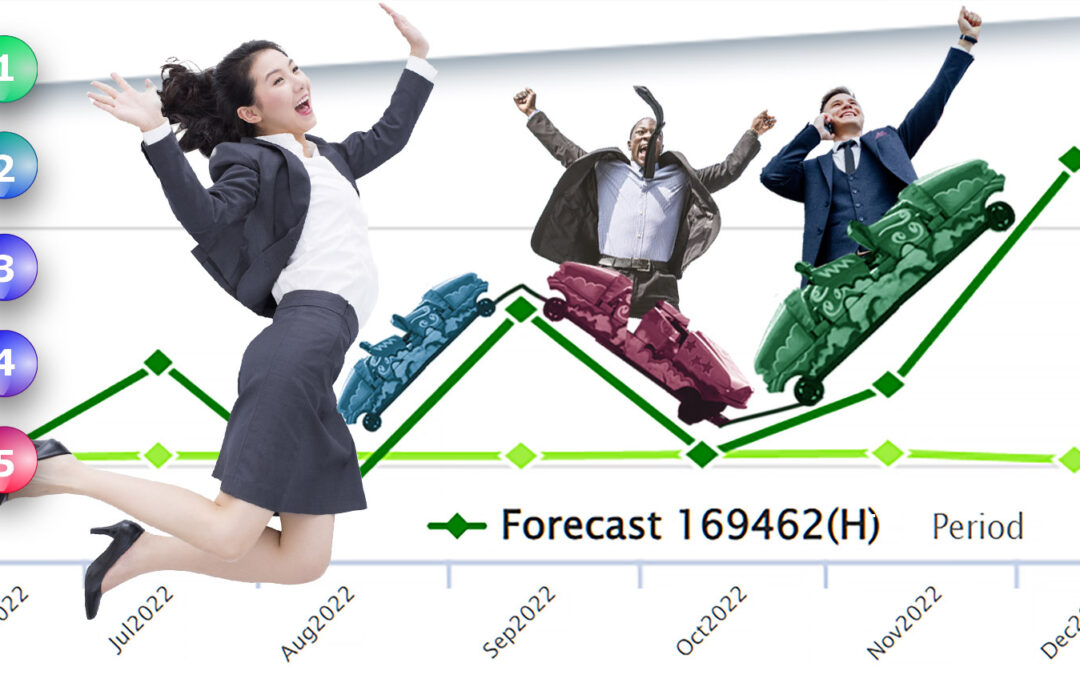
Top Five Tips for New Demand Planners and Forecasters
Good forecasting can make a big difference to your company’s performance, whether you are forecasting to support sales, marketing, production, inventory, or finance. This blog is aimed primarily at those fortunate individuals who are about to start this adventure. Welcome to the field!
Problem
An accurate forecast is a critical supply chain driver, but many organizations have a limited view of what comes next. Forecasts developed by sales teams or customers are often inaccurate and biased toward sales goals or budgets. Forecasts are often provided only at aggregate levels leaving unspecified which items will be at which locations. Planning teams are left to interpret sales figures and convert them into actionable forecasts of the item mix. Incorporating sales feedback, determining which decades old forecast model to use, managing the consensus forecast process, and tracking forecast accuracy are manual processes. They are often managed in complex spreadsheets that are difficult to use, share and scale, and don’t account important features of demand such as seasonality and trend.
Solution
Register to Watch the Demo
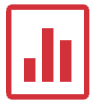
Accurate Demand Forecasts
Capture trend and seasonality
Predict range of future demand
Flag exceptions
Cleanse historical data
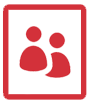
Operational Consensus
Collaborate with key stakeholders
Review at any level of hierarchy
Apply overrides and achieve consensus
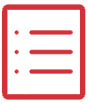
Consistent Repeatable Process
Common system
No spreadsheets
Embed and reuse forecast rules
Monitor accuracy and fine-tune
Who is Smart Demand Planner for?
- Demand Planners.
- Forecast Analysts.
- Material & Inventory Planners.
- Operational Research Professionals.
- Sales Analysts.
- Statistcally Minded Executives.
What questions can Smart Demand Planner answer?
- What is my short and long term demand most likely to be?
- Which areas of the business and products are trending?
- What is the forecast at different levels of my hierarchy (customer, item, family)?
- What is the likely range of future demand?
- Which forecasts need to be reviewed (exception reporting)?
- What is our forecast error (accuracy) for each item, group, overall?
- Are forecast overrides adding value to the process?
What can Smart Demand Planner do?
-
Accurately forecast demand for thousands of items in any unit of measure, powered by the SmartForecasts® engine.
- Capture trends, seasonal, and cyclical patterns at any level.
- Outlier detection and correction to enhance the quality of historical data.
- Identifies “causal” factors such as price and economic data and models their impact on demand.
- Patented Intermittent Demand Planning via APICS award winning “Bootstrapping” technology.
- Create forecasts at any level of the hierarchy – customer, item, product groups, regions.
- Share forecasts with internal and external stakeholders such as sales and suppliers.
- Apply, document, and track forecast overrides.
- Quantify the impact that promotions will have on future demand.
- Apply user defined forecasting methods and rules.