What is to blame for having too much of the stuff you don’t need and not enough of the stuff you do need? Demand and supply variability are often blamed. These problems are significant and seems impossible to overcome leaving many organizations to simply accept misallocated stock as a cost of doing business. However, the real problem it isn’t simply late supplier deliveries and unpredictable demand. These are supply chain planning “facts of life” and it’s how your company addresses them that counts. Watch Greg Hartunian’s vlog to hear his thoughts and what you can do about it.
Smart Inventory Planning and Optimization automatically calculates the stocking policy that yields the best return for your business considering holding costs, ordering costs, and stock outs. To see it in action, register below to watch a 12 minute demonstration.
Related Posts
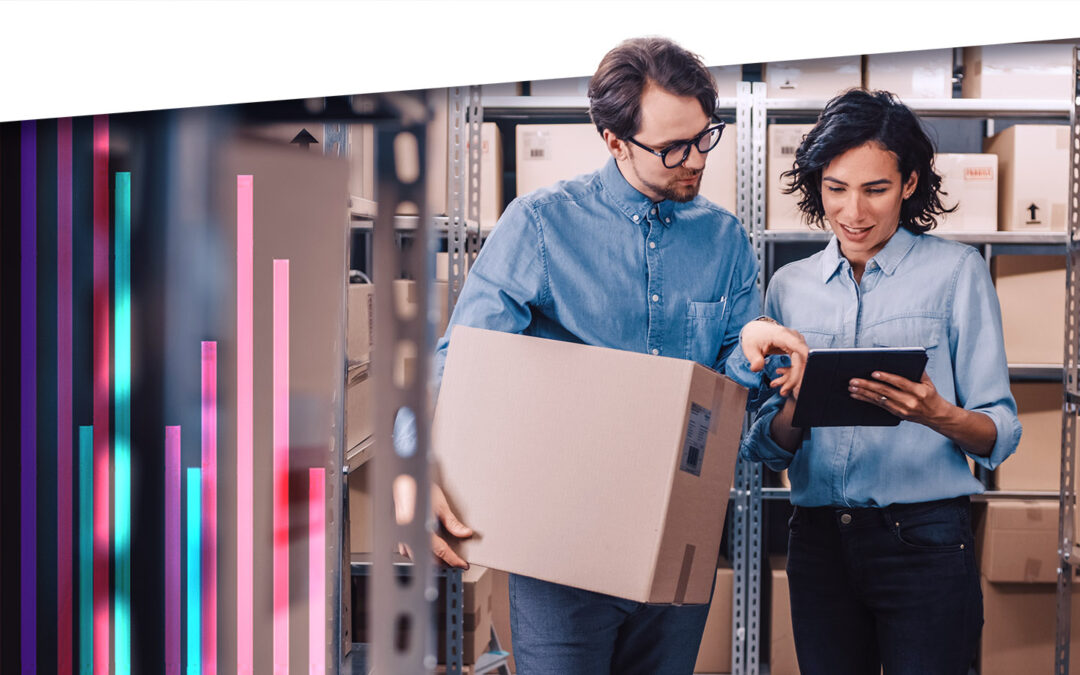
Forecast-Based Inventory Management for Better Planning
Forecast-based inventory management, or MRP (Material Requirements Planning) logic, is a forward-planning method that helps businesses meet demand without overstocking or understocking. By anticipating demand and adjusting inventory levels, it maintains a balance between meeting customer needs and minimizing excess inventory costs. This approach optimizes operations, reduces waste, and enhances customer satisfaction.
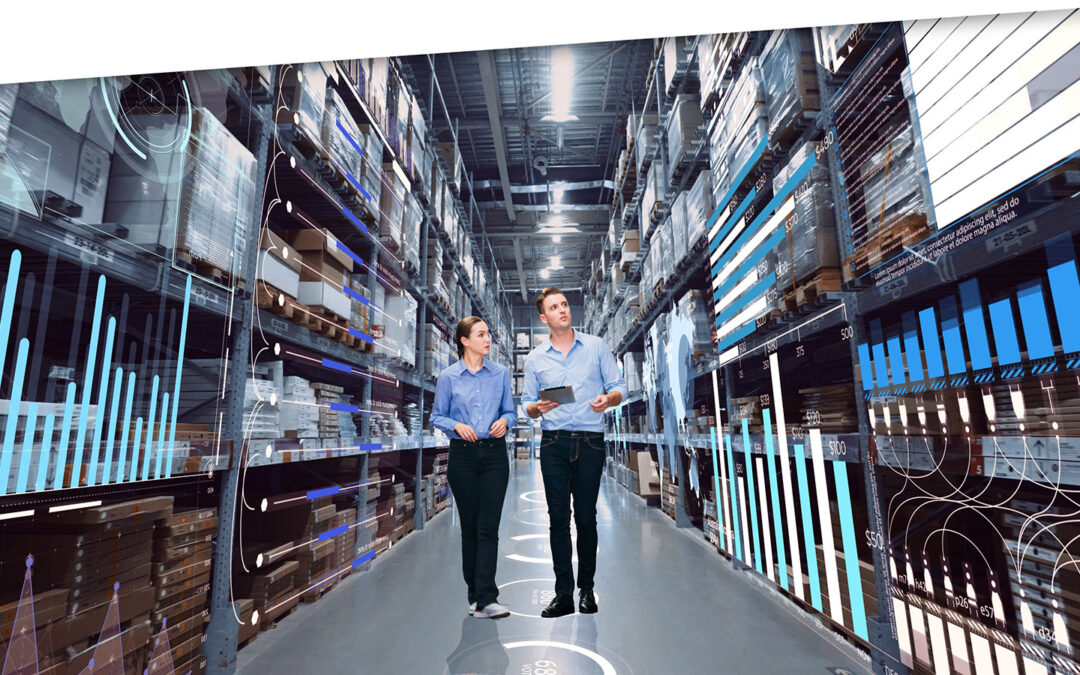
Make AI-Driven Inventory Optimization an Ally for Your Organization
In this blog, we will explore how organizations can achieve exceptional efficiency and accuracy with AI-driven inventory optimization. Traditional inventory management methods often fall short due to their reactive nature and reliance on manual processes. Maintaining optimal inventory levels is fundamental for meeting customer demand while minimizing costs. The introduction of AI-driven inventory optimization can significantly reduce the burden of manual processes, providing relief to supply chain managers from tedious tasks.
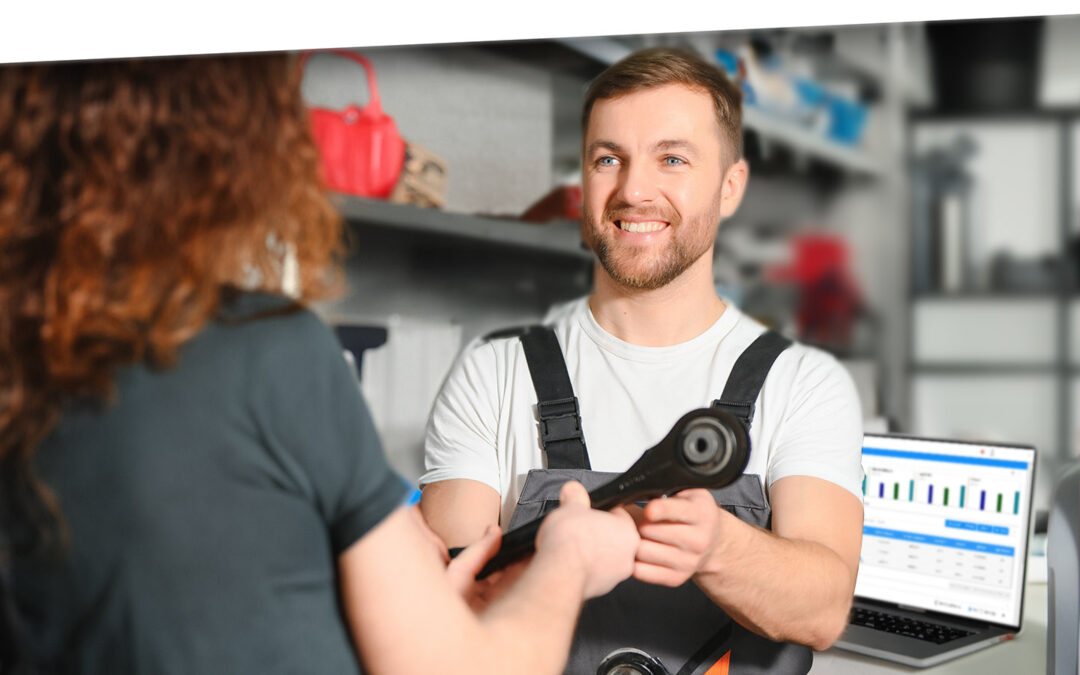
The Importance of Clear Service Level Definitions in Inventory Management
Inventory optimization software that supports what-if analysis will expose the tradeoff of stockouts vs. excess costs of varying service level targets. But first it is important to identify how “service levels” is interpreted, measured, and reported. This will avoid miscommunication and the false sense of security that can develop when less stringent definitions are used. Clearly defining how service level is calculated puts all stakeholders on the same page. This facilitates better decision-making.