Demand planning takes time and effort. It’s worth the effort to the extent that it actually helps you make what you need when you need it.
But the job can be done well or poorly. We see many manufacturers stopping at the first level when they could easily go to the second level. And with a little more effort, they could go all the way to the third level, utilizing probabilistic modeling to convert demand planning results into an inventory optimization process.
The First Level
The first level is making a demand forecast using statistical methods. Figure 1 shows a first level effort: an item’s demand history (red line) and its expected 12-month forecast (green line).
The forecast is bare bones. It only projects expected demand ignoring that demand is volatile and will inevitably create forecast error. (This is another example of an important maxim: “The Average is Not the Answer”). The forecast is as likely to be too high as it is to be too low, and there is no indication of forecast uncertainty accompanying the forecast. This means the planner has no estimate of the risk associated with committing to the forecast. Still, this forecast does provide a rational basis for production planning, personal scheduling, and raw materials purchase. So, it’s much better than guessing.
The Second Level
The second level takes explicit account of forecast uncertainty. Figure 2 shows a second level effort, known as a “percentile forecast”.
Now we see an explicit indication of forecast uncertainty. The cyan line above the green forecast line represents the projected 90th percentile of monthly demand. That is, the demand in each future month has a 90% chance of falling at or below the cyan line. Put another way, there is a 10% chance of demand exceeding the cyan line in each month.
This analysis is much more useful because it supports risk management. If it is important to assure sufficient supply of this item, then it makes sense to produce to the 90th percentile instead of to the expected forecast. After all, it’s a coin flip as to whether the expected forecast will result in enough production to meet monthly demand. This second level forecast is, in effect, a rough substitute for a careful inventory management process.
Figure 2. A percentile forecast, where the cyan line estimates the 90th percentiles of monthly demand.
Going All the Way to the Third Level
Best practice is the Third Level, which uses demand planning as a foundation for completing a second task: explicit inventory optimization. Figure 3 shows the fundamental plot for the efficient management of our finished good, assuming it has a 1 month production lead time.
Figure 3 shows the utilization of probabilistic forecasting and how much draw-down in finished good inventory might take place over a one month production lead time. The uncertainty in demand is apparent in the spread of the possible demand, from a low of 0 to a high of 35, with 15 units being the most likely value. The vertical red line at 22 indicates the “reorder point“ (or “min” or “trigger value”) corresponding to keeping the chance of stocking out while waiting for replenishment to a low 5%. When inventory drops to 22 or below, it is time to order more. The Third Level uses probabilistic demand forecasting with full exposure of forecast uncertainty to efficiently manage the stock of the finished product.
To Sum Up
Forecasting the most likely demand for an item is a useful first step. It gets you halfway to where you want to be. But it provides an incomplete guide to planning because it ignores demand volatility and the forecast uncertainty that it creates. Adding a cushion to the demand forecast gets you further along, because it lessen the risk that a jump in demand will leave you short of product. This cushion can be calculated by probabilistic forecasting approaches that forecasts a high percentile of the distribution of future demand. And if you want to take one step further, you can feed forecasts of the demand distribution over a lead time to calculate reorder points (mins) to ensure that you have an acceptably low level of stock-out risk.
Given what modern forecasting technology can do for you, why would you want to stop halfway to your goal?
Related Posts
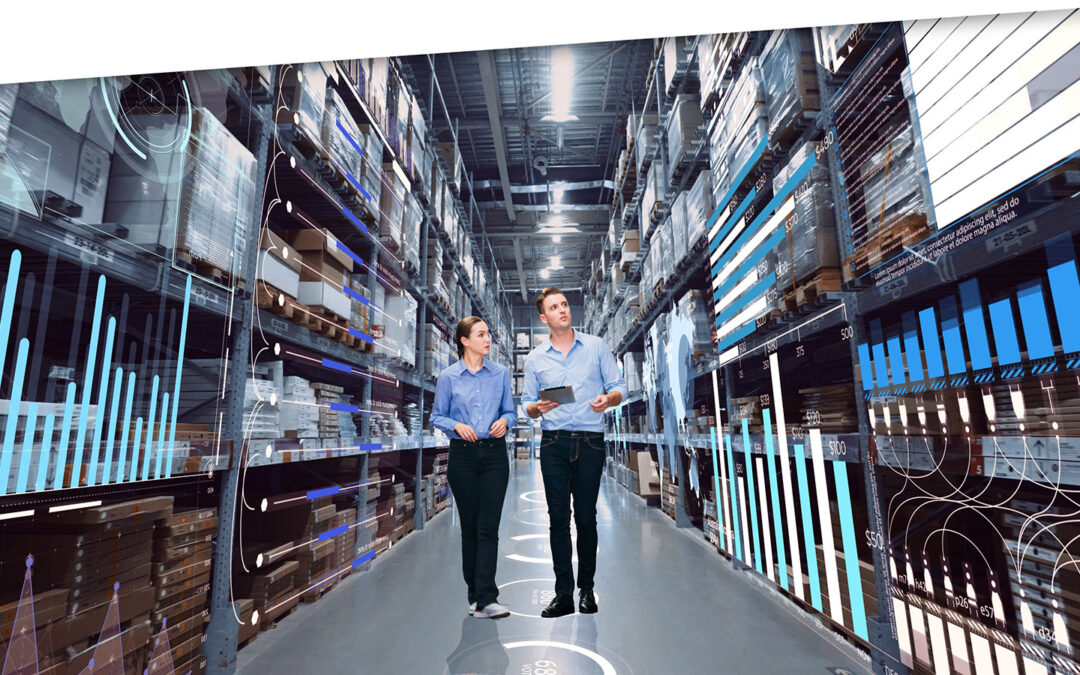
Make AI-Driven Inventory Optimization an Ally for Your Organization
In this blog, we will explore how organizations can achieve exceptional efficiency and accuracy with AI-driven inventory optimization. Traditional inventory management methods often fall short due to their reactive nature and reliance on manual processes. Maintaining optimal inventory levels is fundamental for meeting customer demand while minimizing costs. The introduction of AI-driven inventory optimization can significantly reduce the burden of manual processes, providing relief to supply chain managers from tedious tasks.
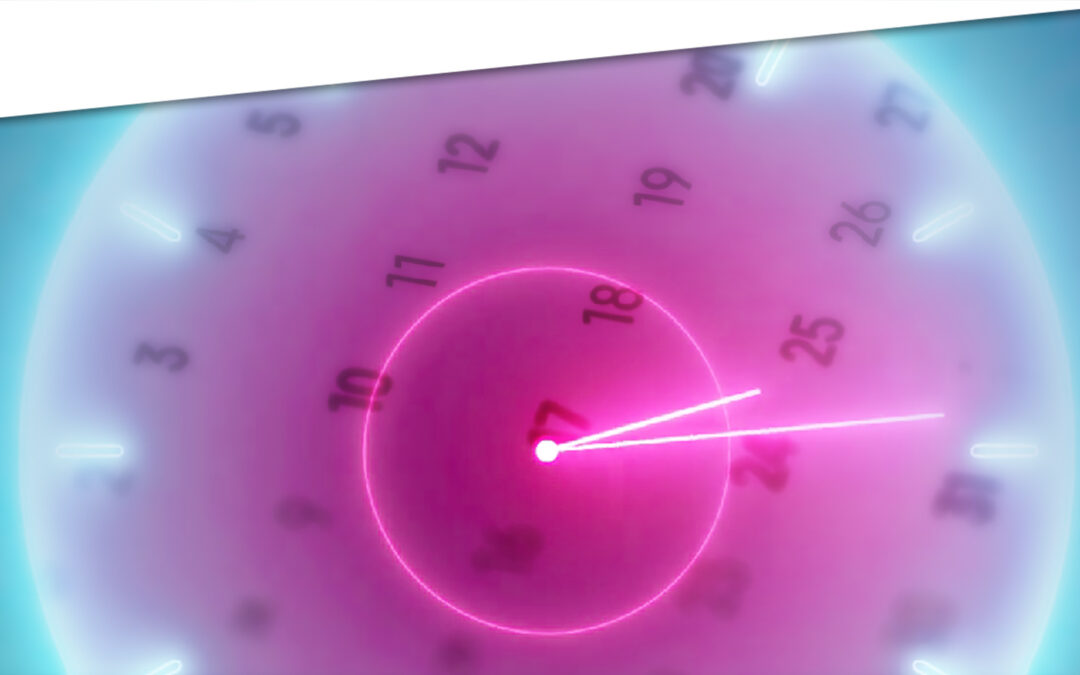
Daily Demand Scenarios
In this Videoblog, we will explain how time series forecasting has emerged as a pivotal tool, particularly at the daily level, which Smart Software has been pioneering since its inception over forty years ago. The evolution of business practices from annual to more refined temporal increments like monthly and now daily data analysis illustrates a significant shift in operational strategies.
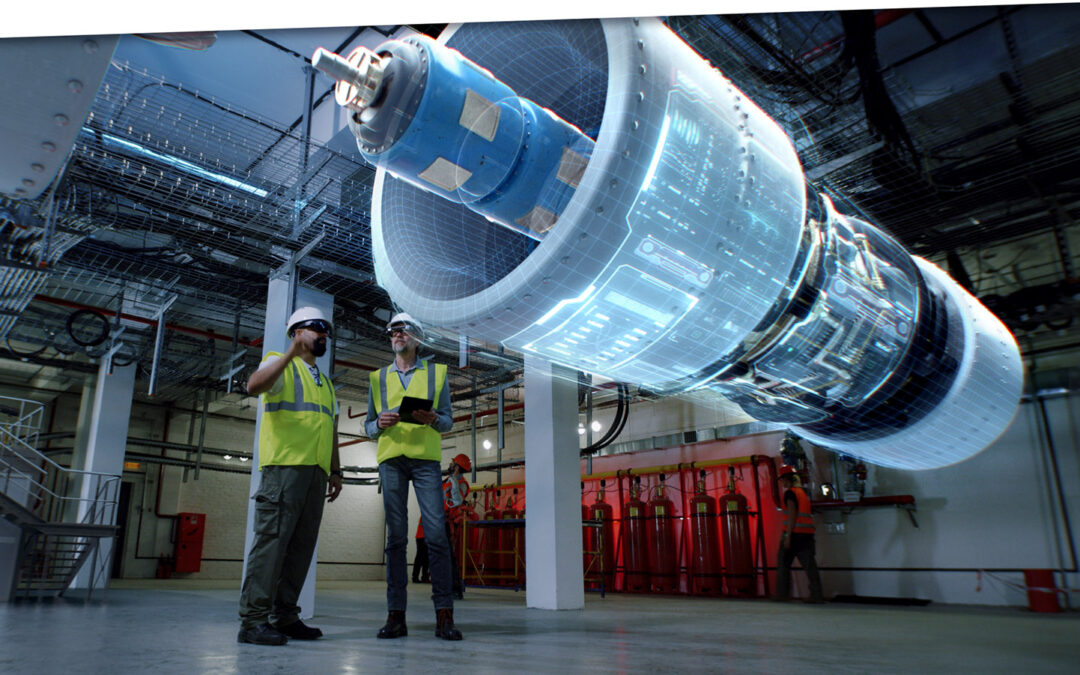
Constructive Play with Digital Twins
Those of you who track hot topics will be familiar with the term “digital twin.” Those who have been too busy with work may want to read on and catch up. While there are several definitions of digital twin, here’s one that works well: A digital twin is a dynamic virtual copy of a physical asset, process, system, or environment that looks like and behaves identically to its real-world counterpart. A digital twin ingests data and replicates processes so you can predict possible performance outcomes and issues that the real-world product might undergo.