What is a Min/Max policy? How do you know is working well for you? Smart IP&O gets Min/Max right!
The Min/Max inventory policy is one of four available Replenishment methods in SIO. When the inventory level drops to or below the Min, a replenishment order is generated. The reorder quantity is the number of units needed to raise the stock up to the Max. How do you know your Min/Max settings are working well and triggering replenishment orders at the right time and for the right quantities? If you are like most companies, setting Min/Max levels is based on rules of thumb or simple averaging techniques that don’t expose the trade off curve between service level and inventory cost. This makes it impossible to predict which items are likely to have overstocks and shortages in the future. In this Video Blog we elaborate on this and describe how Smart Inventory Optimization can help.
Related Posts
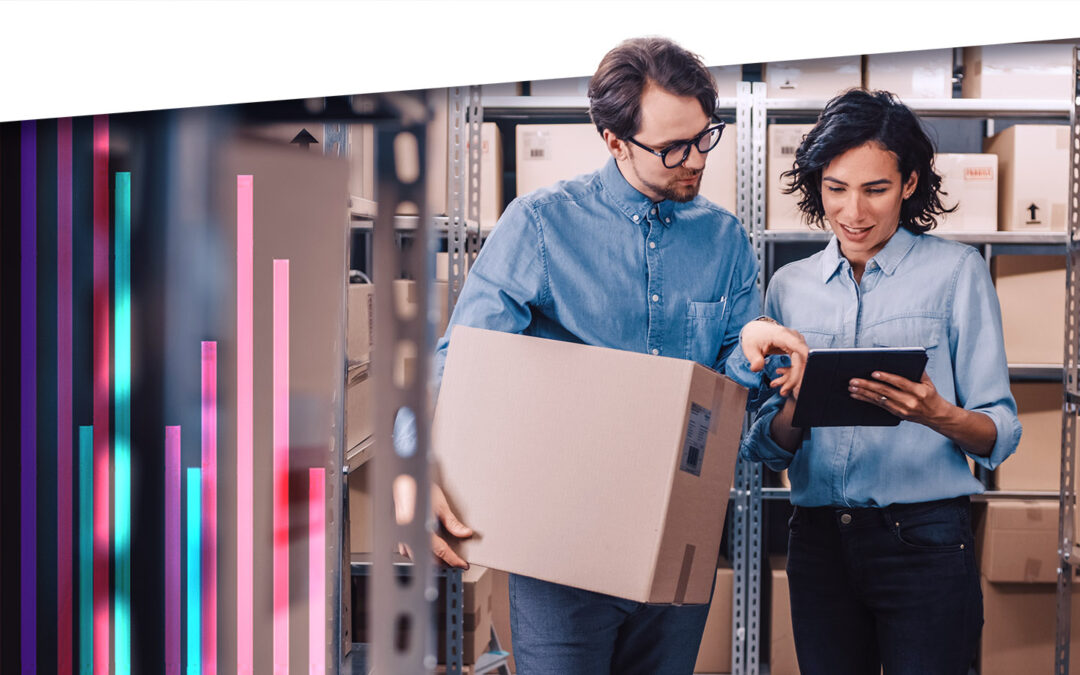
Forecast-Based Inventory Management for Better Planning
Forecast-based inventory management, or MRP (Material Requirements Planning) logic, is a forward-planning method that helps businesses meet demand without overstocking or understocking. By anticipating demand and adjusting inventory levels, it maintains a balance between meeting customer needs and minimizing excess inventory costs. This approach optimizes operations, reduces waste, and enhances customer satisfaction.
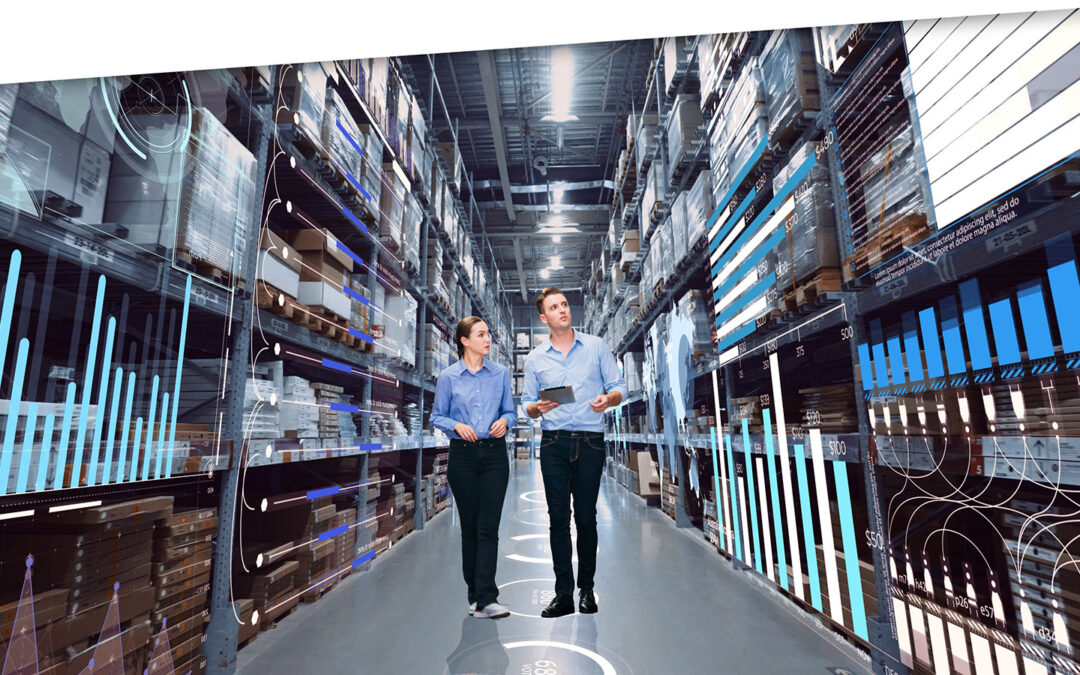
Make AI-Driven Inventory Optimization an Ally for Your Organization
In this blog, we will explore how organizations can achieve exceptional efficiency and accuracy with AI-driven inventory optimization. Traditional inventory management methods often fall short due to their reactive nature and reliance on manual processes. Maintaining optimal inventory levels is fundamental for meeting customer demand while minimizing costs. The introduction of AI-driven inventory optimization can significantly reduce the burden of manual processes, providing relief to supply chain managers from tedious tasks.
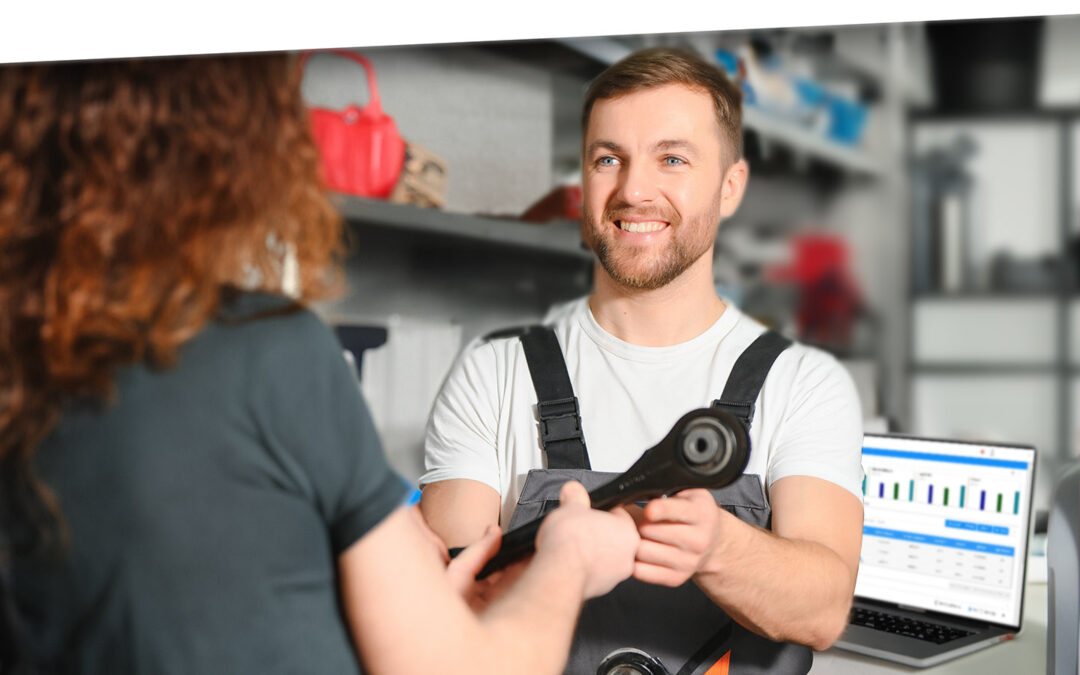
The Importance of Clear Service Level Definitions in Inventory Management
Inventory optimization software that supports what-if analysis will expose the tradeoff of stockouts vs. excess costs of varying service level targets. But first it is important to identify how “service levels” is interpreted, measured, and reported. This will avoid miscommunication and the false sense of security that can develop when less stringent definitions are used. Clearly defining how service level is calculated puts all stakeholders on the same page. This facilitates better decision-making.