Inventory planning parameters, such as safety stock levels, reorder points, Min/Max settings, lead times, order quantities, and DDMRP buffers directly impact inventory spending and ability to meet customer demand. Based on these parameter settings, your ERP system makes daily purchase order suggestions.
Ensuring that these inputs are understood and optimized regularly will substantially reduce wasteful inventory spending and dramatically improve customer service levels.
Given the importance of getting these planning parameters right, we spend a lot of time during our consultations asking (1) how these parameter values are calculated and (2) how often they are updated. Most often the methods for calculating the parameter values are rule of thumb. You can read about why using rule of thumb approaches is so problematic here – Beware of Simple Rules of Thumb for Managing Inventory.
This blog will focus on the frequency of updates. When we interview companies and ask them how often they update planning parameters, the answer we nearly always hear is “every day!” A follow up question or two most often reveals that this just isn’t true. What “every day” actually means in practice is this: Every day, the ERP system suggests dozens to hundreds of purchase orders and/or production jobs. The planner, let’s call him Peter, reviews these orders daily and decides whether to release, modify, or cancel them. If the order suggestion doesn’t “feel right”, Peter reviews the planning inputs and modifies the order if necessary. For example, Peter may feel there is already enough inventory on hand. To “fix” the issue, he will reduce the reorder point and cancel the order. Or if he feels that the order should have been placed weeks ago, Peter may expedite the order and increase the reorder point and order quantity to ensure there will be plenty of stock the next time.
The principal flaws with this approach are that it is reactive and incomplete. Here is why:
Reactive
It only assesses the handful of items marked for replenishment on any given day but not others. The trigger for reviewing an item is when the ERP suggests an order, and that will only happen when the reorder point or Min is breached. If the Min is too high and breaches earlier than it should have, an unneeded order will be placed unless caught by the planner. If the Min is too low, well, it is too late to fix the error. No matter how large the order suggestion is, you still have to wait to be resupplied and since the order was suggested late, a stockout during the replenishment period is highly probable. Where is the “planning” in such a process? As one customer put it, “Our former process was, in hindsight, spent managing the outputs and not the inputs.”
Incomplete
What about the thousands of other items that have a Min/Max, safety Stock, Reorder Point, or other parameters that isn’t being reassessed given the updated demand and supply data. The planner isn’t reviewing any of these items which means problems aren’t being identified in advance. Compounding the problem is that when Peter does make a change he doesn’t have any tools to assess the quality of his changes. If he modifies the min/max settings he doesn’t know the specific impact this will have on inventory value, ordering costs, holding costs, stock outs, and service levels. He only knows that an increase in inventory will likely improve service and increase costs. He doesn’t know for example whether his inventory has reached a point of diminishing returns. When inventory decisions are made with only a very rough understanding of the trade offs it creates more problems downstream. You wouldn’t want your carpenter making rough estimates of their measurements yet it’s commonplace for inventory planning professionals to do so with millions of dollars in inventory spend at stake.
How Often Do Most Companies Update Parameters?
So how often do most companies make system-wide updates to their planning parameters such as reorder points, safety stocks, Min/Max settings, lead times, and order quantities? Typically, mass updates occur quarterly, annually, and in some cases never – the only times changes are made are when an order is triggered by ERP. Not exactly agile.
The biggest reason given for not intervening more often is that it takes too much time. Most companies set these key parameters using very unwieldy Excel programs or ERP applications that simply aren’t designed to conduct systemic inventory planning. This is where inventory optimization software can help.
Using inventory optimization software and probability forecasting to update key planning parameters frequently, say every week or month instead of quarterly or annually, enables you quickly respond to changes in your business. You can seize on cost saving opportunities, as when demand turns down and you can reduce reorder points and/or order quantities and possibly cancel outstanding orders. Or you can respond to problems, as when demand increases threaten your service level commitments to customers, or supplier lead times increase and require re-computation of reorder points.
How to do it Right
The key is establishing an agreed upon set of performance and inventory value metrics and letting the software monitor the state of play in the background and alert you to exceptional situations. This is simply one more way of saying that, once systems have been established, you want to go forward using management by exception. You can set ranges within which things can bubble along as they normally do, but once a critical parameter like “stock out risk exceeds a pre-defined level” or “inventory value or costs exceeds a pre-defined level,” the software can provide a daily alert and can also recommend a response, such as raising a reorder point. With this level of automated assistance, it becomes possible to keep your finger on the pulse of the inventory without being overwhelmed by the sheer volume of data.
For example, you may choose an initial set of inventory parameters as the policy because you could see from the software that it meets your service level goals within your inventory budget. You may let the system prescribe service level targets for you and be comfortable with the settings because inventory value is within the budget. However, if demand gets less predictable than historically, you won’t be able to achieve the same level of service without an increase in inventory. An exception report will identify this and enable you to make an informed decision on what to do. You can decide to modify the policy or keep it the same. If you keep it the same, you now know the additional risks and change in inventory costs. This can be communicated to all stake holders so that there aren’t any surprises.
Plan Don’t React
Rather than being constantly in reactive mode, you can handle what really needs to be handled and still have some time to do forward thinking. For instance, you can do “what if” analyses on such issues as which supplier lead times would yield the biggest payoff if reduced, or whether service level targets should be adjusted to account for shifts in customer criticality, or similar policy issues. After all, it’s not as if you are not going to end up with a full daily agenda, it’s just a question of whether you can elevate that agenda to a more strategic level. So if you are spending all of your “planning” time managing the outputs of your ERP instead of constructively reviewing and optimizing the inputs, it is time to reassess your inventory planning process.
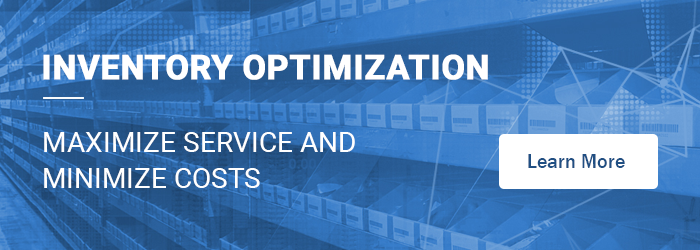