Taiichi Ohno of Toyota is credited with inventing Just-In-Time (JIT) manufacturing in the 1950s. JIT ensures that a manufacturer produces only what is needed, only when required, and only in the necessary amount. That innovation has since had major impacts, some good, some less so.
A recent New York Times article “How the World Ran out of Everything” describes some of the “less so” impacts. For example, JIT has kept inventory costs very low improving return on assets. This in turn is rewarded by Wall Street, so many companies have spent the last few decades reducing their inventories dramatically. Focused as they were on financials, many companies ignored the risks inherent in reducing inventories to the point that “lean” began to border on “emaciated.” Combined with increased globalization and new risks of supply interruption, stock-outs have abounded.
Some industries have gone too far, leaving them exposed to disruption. In a competition to get to the lowest cost, companies have inadvertently concentrated their risk, been interrupted by shortages of raw materials or components, and sometimes forced to halt assembly lines. Wall Street does not look kindly on production halts.
We all know that random events have added to the problem. First among them has been the Covid pandemic. As the pandemic has hindered factory operations and spread disarray in global shipping, many economies worldwide have been tormented by shortages of an immense range of goods — from computer chips to lumber to clothing.
The damage is compounded when more unexpected things go wrong. The Suez Canal Blockage is a prime example, obstructing the main trade route between Europe and Asia. Recently, cyberattacks have added another layer of disruption.
The reaction creates its own problems, just as the cyberattack on the Colonial Pipeline created gas shortages through panic buying. Suppliers start filling orders more slowly than usual. Manufacturers and distributors reverse course and increase inventories and diversify their suppliers to avoid future stockouts. Simply expanding warehouses may not deliver the solution, and the need to determine how much inventory to keep is more urgent every day.
So how can you execute a real-world plan for JIT inventory amidst all this risk and uncertainty? The foundation of your response is your corporate data. Uncertainty has two sources: supply and demand. You need the facts for both.
On the supply side, exploit the data you have on recent supplier lead times, which reflect the current turbulence. Don’t use average values when you can use probability distributions that reflect the full range of contingencies. Consider this comparison. Supplier A is now reliably filling orders in exactly 10 days. Supplier B also averages 10 days but does with a 78%/22% mix of 7 and 21 days. Both A and B have an average replenishment delay of 10 days, but the operational results they provide will be very different. You can only recognize this if you use probability models of inventory performance.
On the demand side, similar considerations apply. First, recognize that there may have been a major shift in the character of item demand (statisticians call this a “regime change”), so purge from your analysis any data that represent the “good old days.” Then, again, stop thinking in terms of averages. While the average demand is important, it is not a sufficient descriptor of the problem you face. Equally important is the volatility of demand. Volatility is the reason you keep inventory in the first place. If demand were completely predictable, you would have neither stockouts nor excess inventory. Just as you need to estimate the full probability distribution of replenishment lead times, you need the full distribution of demand values.
Once you understand the range of variability in both supply and demand, probabilistic forecasting will allow you to account for disruptions and unusual events. Software will convert your data on demand and lead times into huge numbers of scenarios representing how your next planning period might play out. Given those scenarios, the software can determine how best to meet your goals for such metrics as inventory costs and stockout rates. Using solutions such as Smart Inventory Optimization , you will confidently plan based on your targeted stockout risk with minimal inventory carrying cost. You may also consider letting the solution prescribe optimal service level targets by assessing the costs of additional inventory vs. stockout cost.
In inventory planning, as in science, we cannot escape the reality of uncertainty and the impact of unusual events. We must plan accordingly: using inventory optimization software helps you identify the least-cost service level. This creates a coherent, company-wide effort that combines visibility into current operations with mathematically correct assessments of future risks and conditions.
Inventory planning has become more “interesting” and requires a greater degree of risk awareness and agility. The right software can help.
Related Posts
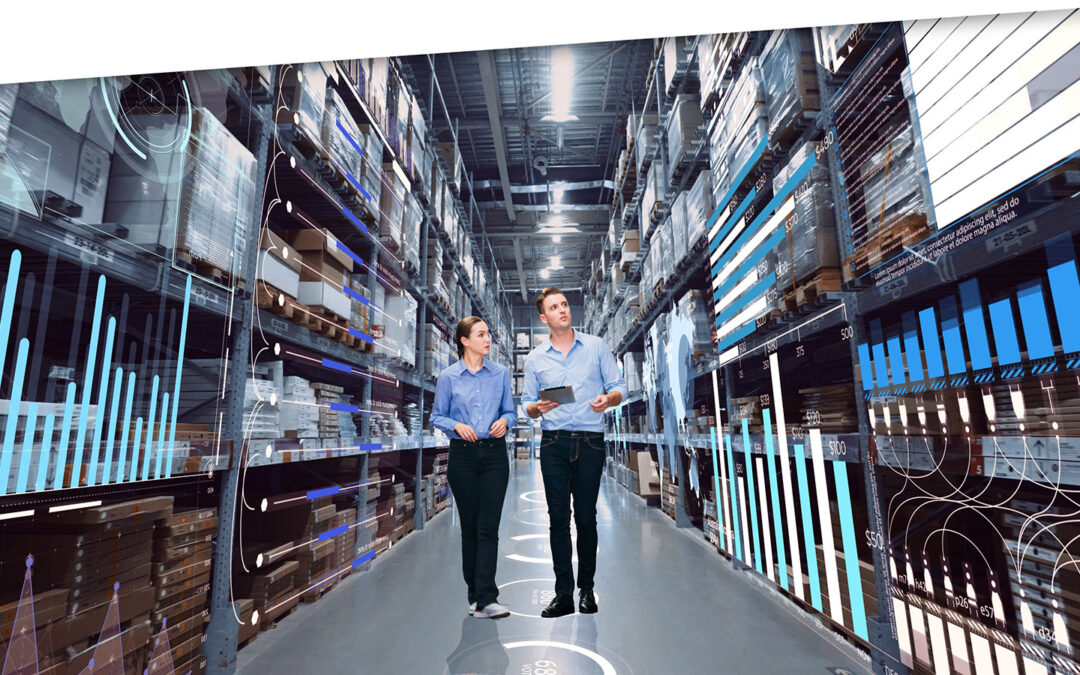
Make AI-Driven Inventory Optimization an Ally for Your Organization
In this blog, we will explore how organizations can achieve exceptional efficiency and accuracy with AI-driven inventory optimization. Traditional inventory management methods often fall short due to their reactive nature and reliance on manual processes. Maintaining optimal inventory levels is fundamental for meeting customer demand while minimizing costs. The introduction of AI-driven inventory optimization can significantly reduce the burden of manual processes, providing relief to supply chain managers from tedious tasks.
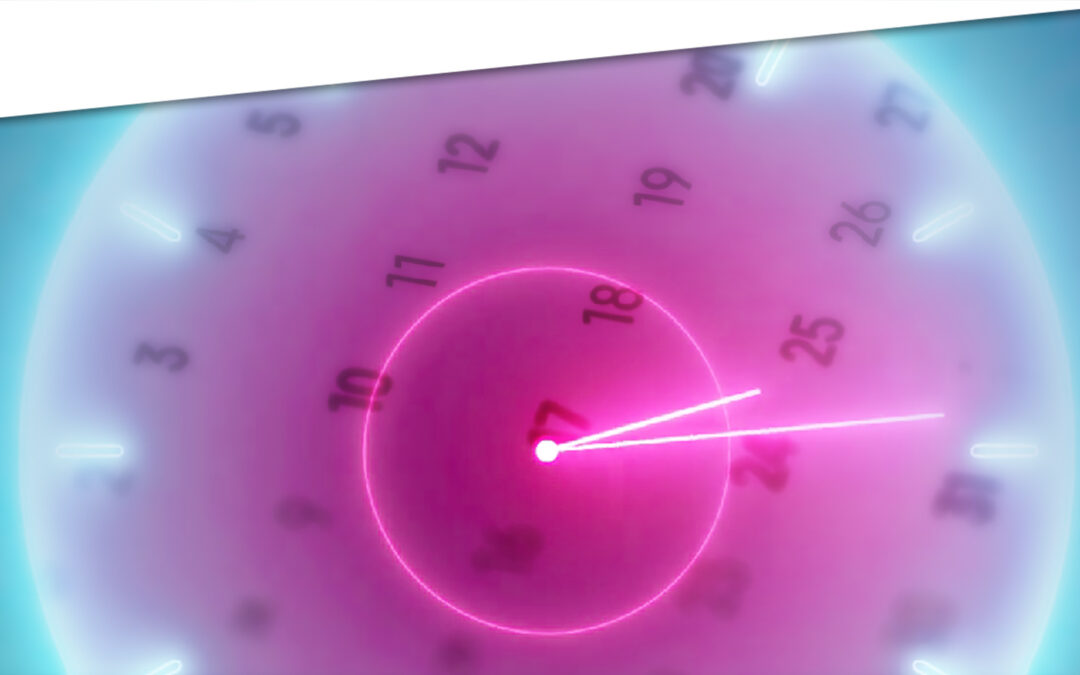
Daily Demand Scenarios
In this Videoblog, we will explain how time series forecasting has emerged as a pivotal tool, particularly at the daily level, which Smart Software has been pioneering since its inception over forty years ago. The evolution of business practices from annual to more refined temporal increments like monthly and now daily data analysis illustrates a significant shift in operational strategies.
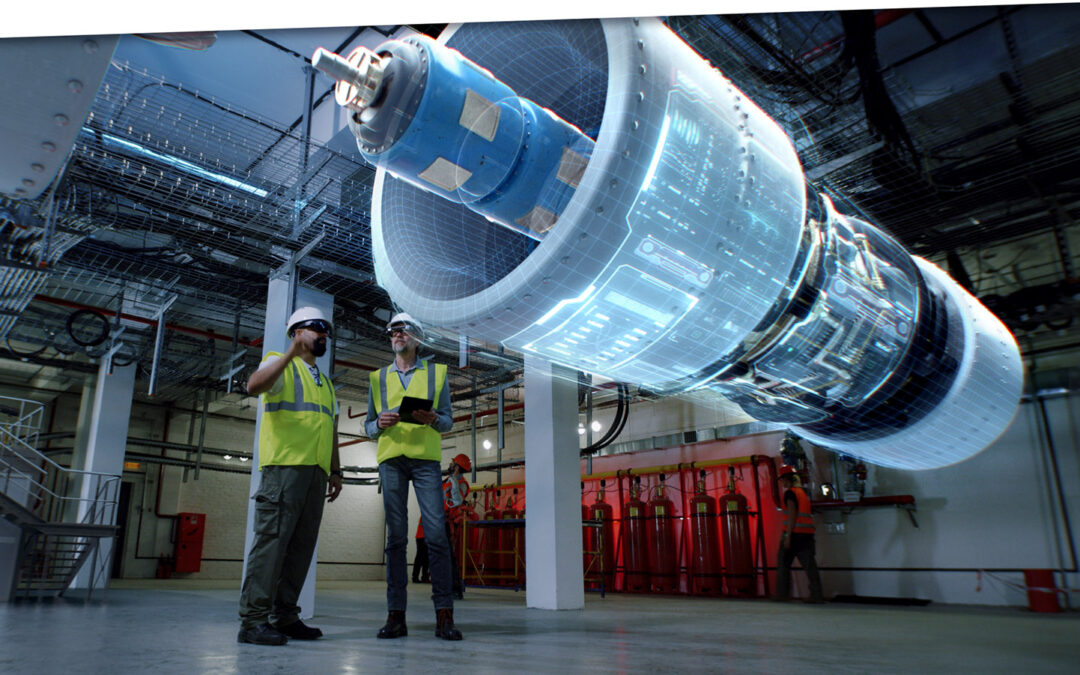
Constructive Play with Digital Twins
Those of you who track hot topics will be familiar with the term “digital twin.” Those who have been too busy with work may want to read on and catch up. While there are several definitions of digital twin, here’s one that works well: A digital twin is a dynamic virtual copy of a physical asset, process, system, or environment that looks like and behaves identically to its real-world counterpart. A digital twin ingests data and replicates processes so you can predict possible performance outcomes and issues that the real-world product might undergo.