The Covid19 pandemic has placed unusual stress on public transit agencies. This stress forces agencies to look again at their spare parts planning processes, which is a key driver up ensuring uptime and balancing service parts inventory costs.
This blog focuses on bus systems and their practices for spare parts management and planning. However, there are lessons here for other types of public transit, including rail and light rail.
Back in 1995, the Transportation Research Board (TRB) of the National Research Council published a report that still has relevance. System-Specific Spare Bus Ratios: A Synthesis of Transit Practice stated
The purpose of this study was to document and examine the critical site-specific variables that affect the number of spare vehicles that bus systems need to maintain maximum service requirements. … Although transit managers generally acknowledged that right-sizing the fleet actually improves operations and lowers cost, many reported difficulties in achieving and consistently maintaining a 20 percent spare ratio as recommended by FTA… The respondents to the survey advocated that more emphasis be placed on developing improved and innovative bus maintenance techniques, which would assist them in minimizing downtime and improving vehicle availability, ultimately leading to reduced spare vehicles and labor and material costs.
Grossly simplified guidelines like “keep 20% spare buses” are easy to understand and measure but grossly mask more detailed tactics that can provide more tailored policies that better steward taxpayer dollars spent on spare parts while ensuring the highest levels of availability. If operational reliability can be improved for each bus, then fewer spares are needed.
One way to keep each bus up and running more often is to improve the management of inventories of spare parts – specifically by forecasting service parts usage and the required replenishment policies more accurately. Here is where modern supply chain management can make a significant contribution. The TRB noted this in their report:
Many agencies have been successful in limiting reliance on excess spare vehicles. Those transit officials agree that several factors and initiatives have led to their success and are critical to the success of any program [including] … Effective use of advanced technology to manage critical maintenance functions, including the orderly and timely replacement of parts… Failure to have available service parts and other components when they are needed will adversely affect any maintenance program.
As long as managers are cognizant of the issues and vigilant about what tools are available to them, the probability of buses [being] ‘out for no stock’ will greatly diminish.”
Effective spare parts inventory management requires a balance between “having enough” and “having too much.” What modern service parts planning software can do is make visible the tradeoff between these two goals so that transit managers can make fact-based decisions about spare parts inventories.
There are enough complications in finding the right balance to require moving beyond simple rules of thumb such as “keep ten days’ worth of demand on hand” or “reorder when you are down to five units in stock.” Factors that drive these decisions include both the average demand for a part, the volatility of that demand, the average replenishment lead time (which can be a problem when the part arrives by slow boat from Germany), the variability in lead time, and several cost factors: holding costs, ordering costs, and shortage costs (e.g., lost fares, loss of public goodwill).
Innovative supply chain analytics and spare parts planning software uses advanced probabilistic forecasting and stochastic optimization methods to manage these complexities and provide greater parts availability at lower cost. For instance, Minnesota’s Metro Transit documented a 4x increase in return on investment in the first six months of implementing a new system. To read more about how public transit agencies are exploiting innovative supply chain analytics, see:
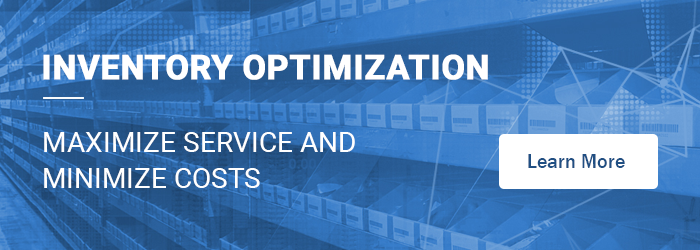