Intermittent, lumpy or uneven demand —particularly for low-demand items like service and spare parts — is especially difficult to predict with any accuracy. Smart Software’s proprietary probabilistic forecasting dramatically improves service level accuracy. If any of these scenarios apply to your company then probabilistic forecasting will help improve your bottom line.
- Do you have intermittent or lumpy demand with large, infrequent spikes that are many times the average demand?
- Is it hard to obtain business information about when demand is likely to spike again?
- Do you miss out on business opportunities because you can’t accurately forecast demand and estimate inventory requirements for certain unpredictable products?
- Are you required to hold inventory on many items even if they are infrequently demanded in order to differentiate vs. the competition by providing high service levels?
- Do you have to make unnecessarily large investments in inventory to cover unexpected orders and materials requirements?
- Do you have to deliver to customers right away despite long supplier lead times?
If you’ve answered yes to some or all of the questions above, you aren’t alone. Intermittent demand —also known as irregular, sporadic, lumpy, or slow-moving demand — affects industries of all types and sizes: capital goods and equipment sectors, automotive, aviation, public transit, industrial tools, specialty chemicals, utilities and high tech, to name just a few. And it makes demand forecasting and planning extremely difficult. It can be much more than a headache; it can be a multi-million-dollar problem, especially for MRO businesses and others who manage and distribute spare and service parts.
Identifying intermittent demand data isn’t hard. It typically contains a large percentage of zero values, with non-zero values mixed in randomly. But few forecasting solutions have yielded satisfactory results even in this era of Big Data Analysis, Predictive Analytics, Machine Learning, and Artificial Intelligence.
DOWNLOAD THE ARTICLE
Traditional Approaches and their Reliance on an Assumed Demand Distribution
Traditional statistical forecasting methods, like exponential smoothing and moving averages, work well when product demand data is normal, or smooth, but it doesn’t give accurate results with intermittent data. Many automated forecasting tools fail because they work by identifying patterns in demand history data, such as trend and seasonality. But with intermittent demand data, patterns are especially difficult to recognize. These methods also tend to ignore the special role of zero values in analyzing and forecasting demand.Even so, some conventional statistical forecasting methods can produce credible forecasts of the average demand per period. However, when demand is intermittent, a forecast of the average demand is not nearly sufficient for inventory planning. Accurate estimates of the entire distribution (i.e., complete set) of all possible lead-time demand values is needed. Without this, these methods produce misleading inputs to inventory control models — with costly consequences.
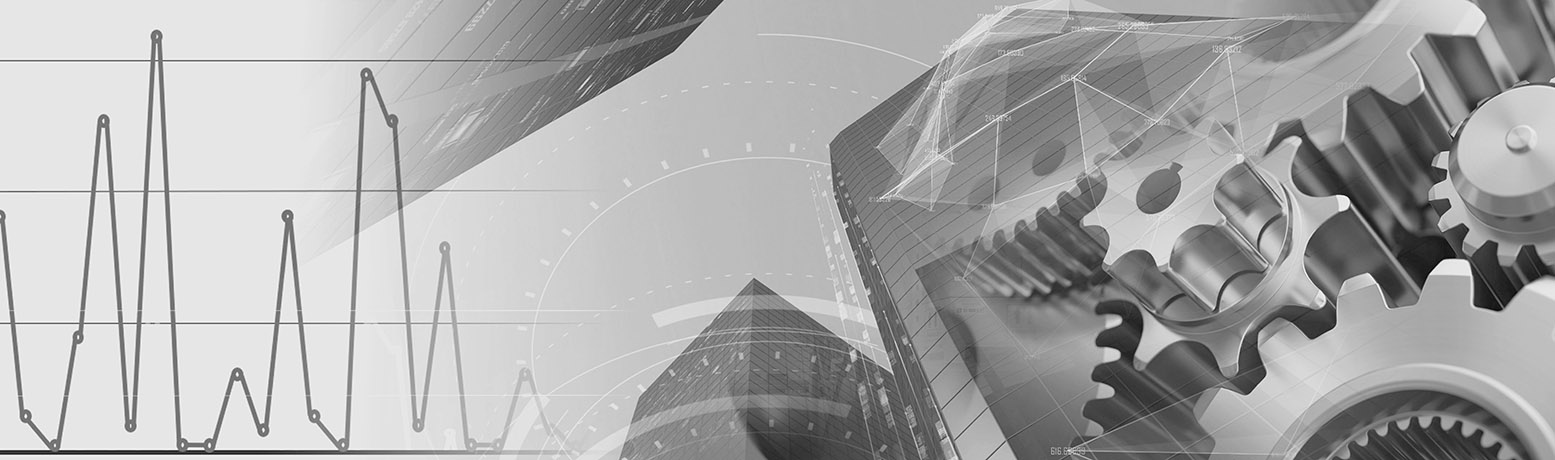
To produce reorder points, order-up-to levels, and safety stocks for inventory planning, many forecasting approaches rely on assumptions about the demand and lead time distribution. Some assume that the probability distribution of total demand for a particular product item over a lead time (lead-time demand) will resemble a normal, classic bell-shaped curve. Other approaches might rely on a Poisson distribution or some other textbook distribution. With intermittent demand, a one-sized fits all approach is problematic because the actual distribution will often not match the assumed distribution. When this occurs, estimates of the buffer stock will be wrong. This is especially the case when managing spare parts (Table 1).
For each intermittently demanded item, the importance of having an accurate forecast of the entire distribution of all possible lead time demand values — not just one number representing the average or most likely demand per period — cannot be overstated. These forecasts are key inputs to the inventory control models that recommend correct procedures for the timing and size of replenishment orders (reorder points and order quantities). They are particularly essential in spare parts environments, where they are needed to accurately estimate customer service level inventory requirements (e.g., a 95 or 99 percent likelihood of not stocking out of an item) for satisfying total demand over a lead time. Inventory planning departments must be confident that when they target a desired service level that they will achieve that target. If the forecasting model consistently yields a different service level than targeted, inventory will be mismanaged and confidence in the system will erode.
Faced with this challenge, many organizations rely on applying rule of thumb based approaches to determine stocking levels or will apply judgmental adjustments to their statistical forecasts, which they hope will more accurately predict future activity based on past business experience. But there are several problems with these approaches, as well.
Rule of thumb approaches ignore variability in demand and lead time. They also do not update for changes in demand patterns and don’t provide critical trade-off information about the relationship between service levels and inventory costs.
Judgmental forecasting is not feasible when dealing with large numbers (thousands and tens of thousands) of items. Furthermore, most judgmental forecasts provide a single-number estimate instead of a forecast of the full distribution of lead-time demand values. Finally, it is easy to inadvertently but incorrectly predict a downward (or upward) trend in demand, based on expectations, resulting in understocking (or over-stocking) inventory.
How does Probabilistic Demand Forecasting Work in Practice?
Although the full architecture of this technology includes additional proprietary features, a simple example of the approach demonstrates the usefulness of the technique. See Table 1.
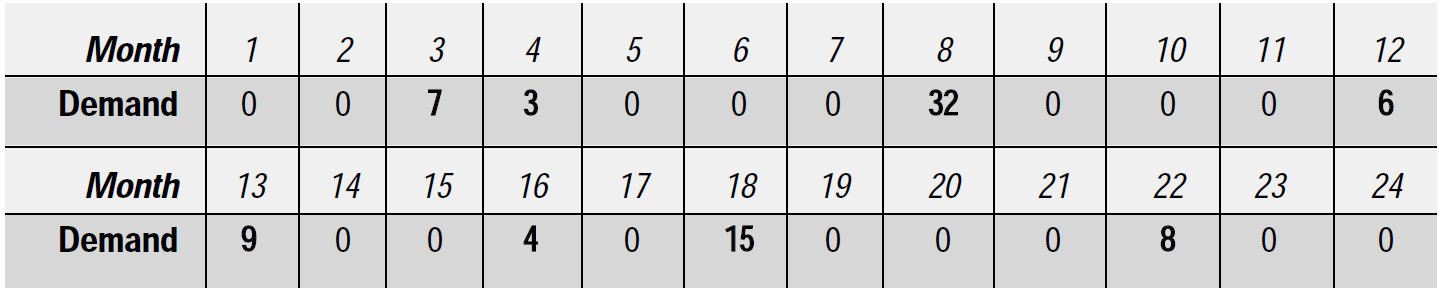
Table 1. Monthly demand values for a service part item.
The 24 monthly demand values for a service part itemare typical of intermittent demand. Let’s say you need forecasts of total demand for this item over the next three months because your parts supplier needs three months to fill an order to replenish inventory. The probabilistic approach is to sample from the 24 monthly values, with replacement, three times, creating a scenario of total demand over the three-month lead time.

Figure 1. The results of 25,000 scenarios.
You might randomly select months 6, 12 and 4, which gives you demand values of 0, 6 and 3, respectively, for a total lead-time demand (in units) of 0 + 6 + 3 = 9. You then repeat this process, perhaps randomly selecting months 19, 8 and 14, which gives a lead-time demand of 0 + 32 + 0 = 32 units. Continuing this process, you can build a statistically rigorous picture of the entire distribution of possible lead-time demand values for this item. Figure 1 shows the results of 25,000 such scenarios, indicating (in this example) that the most likely value for lead-time demand is zero but that lead-time demand could be as great as 70 or more units. It also reflects the real-life possibility that nonzero demand values for the part item occurring in the future could differ from those that have occurred in the past.
With the high-speed computational resources available in the cloud today, probabilistic forecasting methods can provide fast and realistic forecasts of total lead-time demand for thousands or tens of thousands of intermittently demanded product items. These forecasts can then be entered directly into inventory control models to insure that enough inventory is available to satisfy customer demand. This also ensures that no more inventory than necessary is maintained, minimizing costs.
A Field Proven Method That Works
Customers that have implemented the technology have found that it increases customer service level accuracy and significantly reduces inventory costs.
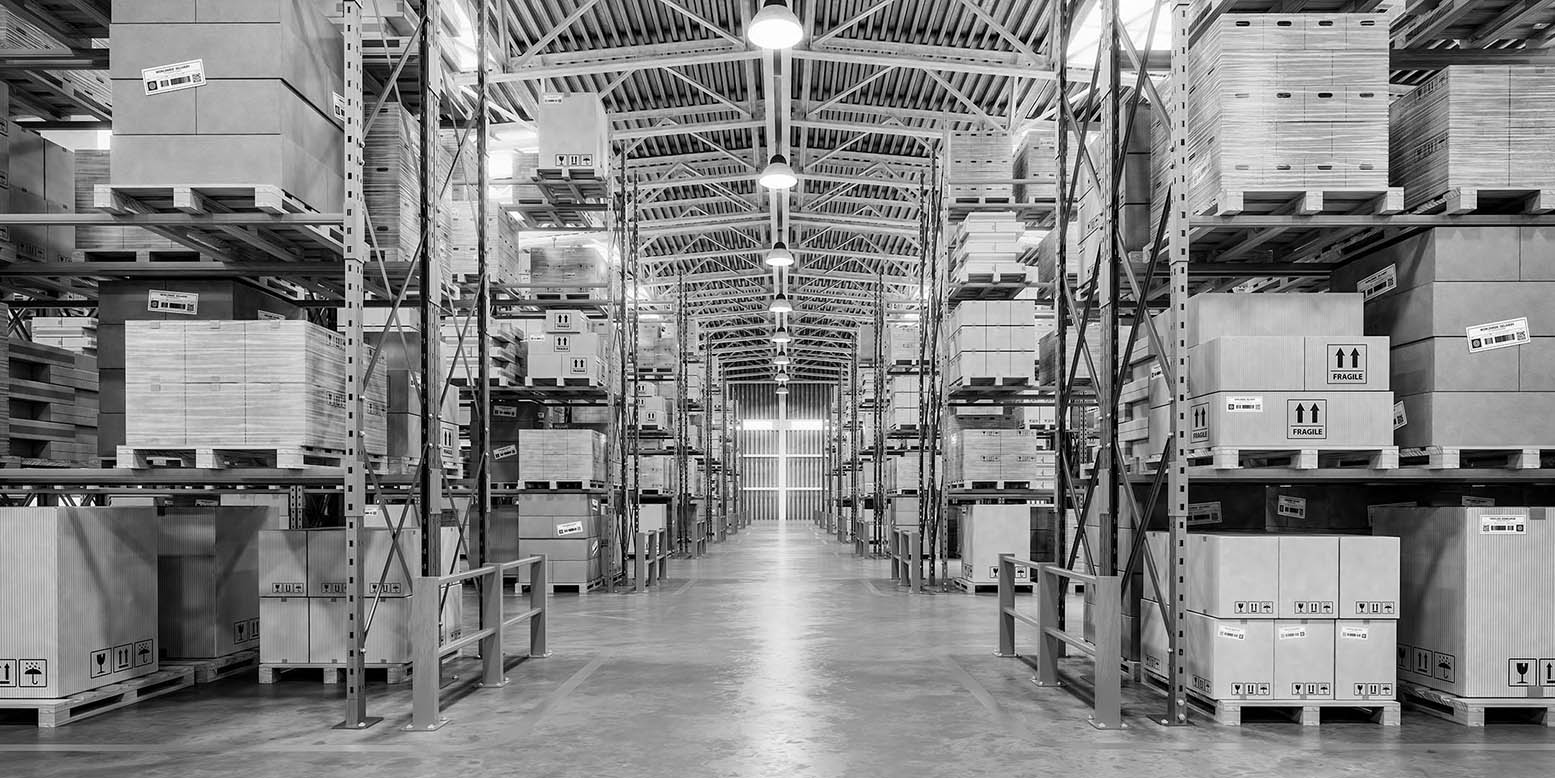
A nationwide hardware retailer’s warehousing operation forecasted inventory requirements for 12,000 intermittently demanded SKUs at 95 and 99 percent service levels. The forecast results were almost 100 percent accurate. At the 95 percent service level, 95.23 percent of the items did not stock out (95 percent would have been perfect). At the 99 percent service level, 98.66 percent of the items did not stock out (99 percent would have been perfect).
The aircraft maintenance operation of a global company got similar service level forecasting results with 6,000 SKUs. Potential annual savings in inventory carrying costs were estimated at $3 million. The aftermarket business unit of an automotive industry supplier, two-thirds of whose 7,000 SKUs demonstrate highly intermittent demand, also projected $3 million in annual cost savings.
That the challenge of forecasting intermittent product demand has indeed been met is good news for manufacturers, distributors, and spare parts/MRO businesses. With cloud computing, Smart Software’s field-proven probabilistic method is now accessible to the non-statistician and can be applied at scale to tens of thousands of parts. Demand data that was once un-forecastable no longer poses an obstacle to achieving the highest customer service levels with the lowest possible investment in inventory.
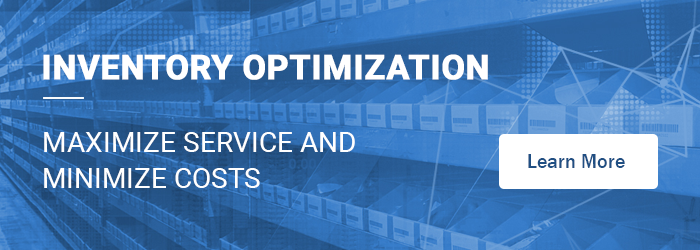
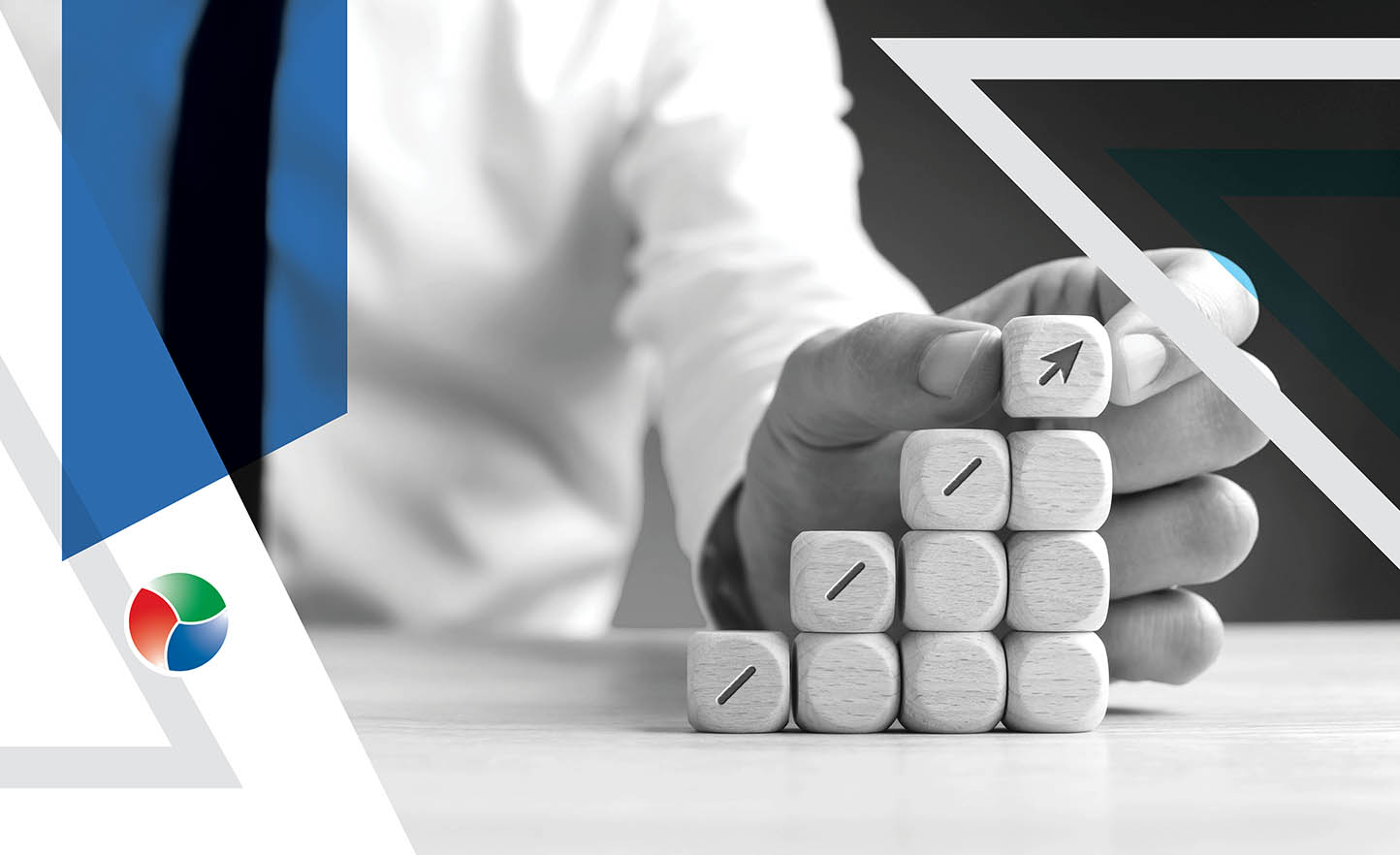
DOWNLOAD THE ARTICLE