Summary
Setting a target service level or fill rate is a strategic decision about inventory risk management. Choosing service levels can be difficult. Relevant factors include current service levels, replenishment lead times, cost constraints, the pain inflicted by shortages on you and your customers, and your competitive position. Target setting is often best approached as a collaboration among operations, sales and finance. Inventory optimization software is an essential tool in the process.
Service Level Choices
Service level is the probability that no shortages occur between when you order more stock and when it arrives on the shelf. The reasonable range of service levels is from about 70% to 99%. Levels below 70% may signal that you don’t care about or can’t handle your customers. Levels of 100% are almost never appropriate and usually indicate a hugely bloated inventory.
Factors Influencing Choice of Service Level
Several factors influence the choice of service level for an inventory item. Here are some of the more important.
Current service levels:
A reasonable place to start is to find out what your current service levels are for each item and overall. If you are already in good shape, then the job becomes the easier one of tweaking an already-good solution. If you are in bad shape now, then setting service levels can be more difficult. Surprisingly few companies have data on this important metric across their whole fleet of inventory items. What often happens is that reorder points grow willy-nilly from choices made in corporate pre-history and are rarely, sometimes never, systematically reviewed and updated. Since reorder points are a major determinant of service levels, it follows that service levels “just happen”. Inventory optimization software can convert your current reorder points and lead times into solid estimates of your current service levels. This analysis often reveals subset of items with service levels either too high or too low, in which case you have guidance about which items to adjust down or up, respectively.
Replenishment lead times:
Some companies adjust service levels to match replenishment lead times. If it takes a long time to make or buy an item, then it takes a long time to recover from a shortage. Accordingly, they bump up service levels on long-lead-time items and reduce them on items for which backlogs will be brief.
Cost constraints:
Inventory optimization software can find the lowest-cost ways to hit high service level targets, but aggressive targets inevitably imply higher costs. You may find that costs constrain your choice of service level targets. Costs come in various flavors. “Inventory investment” is the dollar value of inventory. “Operating costs” include both holding costs and ordering costs. Constraints on inventory investment are often imposed on inventory executives and always imply ceilings on service level targets; software can make these relationships explicit but not take away the necessity of choice. It is less common to hear of ceilings on operating costs, but they are always at least a secondary factor arguing for lower service levels.
Shortage costs:
Shortage costs depend on whether your shortage policy calls for backorders or lost sales. In either case, shortage costs work counter to inventory investment and operating costs by arguing for higher service levels. These costs may not always be expressed in dollar terms, as in the case of medical/surgical supplies, where shortage costs are denominated in morbidity and mortality.
Competition:
The closer your company is to dominating its market, the more you can ease back on service levels to save money. However, easing back too far carries risks: It encourages potential customers to look elsewhere, and it encourages competitors. Conversely, high product availability can go far to bolstering the position of a minor player.
Collaborative Targeting
Inventory executives may be the ones tasked with setting service level targets, but it may be best to collaborate with other functions when making these calls. Finance can share any “red lines” early in the process, and they should be tasked with estimating holding and ordering costs. Sales can help with estimating shortage costs by explaining likely customer reactions to backlogs or lost sales.
The Role of Inventory Optimization and Planning Software
Without inventory optimization software, setting service level targets is pure guesswork: It is impossible to know how any given target will play out in terms of inventory investment, operating costs, shortage costs. The software can compute the detailed, quantitative tradeoff curves required to make informed choices or even recommend the target service level that results in the lowest overall cost considering holding costs, ordering costs, and stock out costs. However, not all software solutions are created equal. You might enter a user defined 99% service level into your inventory planning system or the system could recommend a target service – but it doesn’t mean you will actually hit that stated service level. In fact, you might not even come close to hitting it and achieve a much lower service level. We’ve observed situations where a targeted service level of 99% actually achieved a service level of just 82%! Any decisions made as a result of the target will result in unintended misallocation of inventory, very costly consequences, and lots of explaining to do.So be sure to check out our blog article on how to measure the accuracy of your service level forecast so you don’t make this costly mistake.
Related Posts

Innovating the OEM Aftermarket with AI-Driven Inventory Optimization
The aftermarket sector provides OEMs with a decisive advantage by offering a steady revenue stream and fostering customer loyalty through the reliable and timely delivery of service parts. However, managing inventory and forecasting demand in the aftermarket is fraught with challenges, including unpredictable demand patterns, vast product ranges, and the necessity for quick turnarounds. Traditional methods often fall short due to the complexity and variability of demand in the aftermarket. The latest technologies can analyze large datasets to predict future demand more accurately and optimize inventory levels, leading to better service and lower costs.
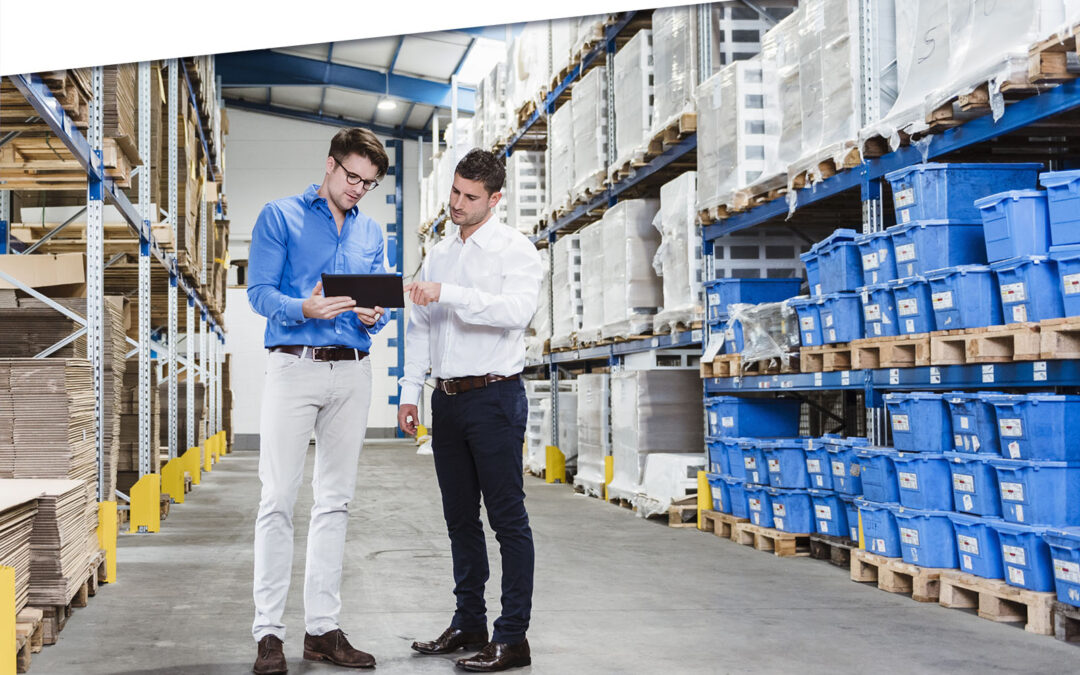
Forecast-Based Inventory Management for Better Planning
Forecast-based inventory management, or MRP (Material Requirements Planning) logic, is a forward-planning method that helps businesses meet demand without overstocking or understocking. By anticipating demand and adjusting inventory levels, it maintains a balance between meeting customer needs and minimizing excess inventory costs. This approach optimizes operations, reduces waste, and enhances customer satisfaction.
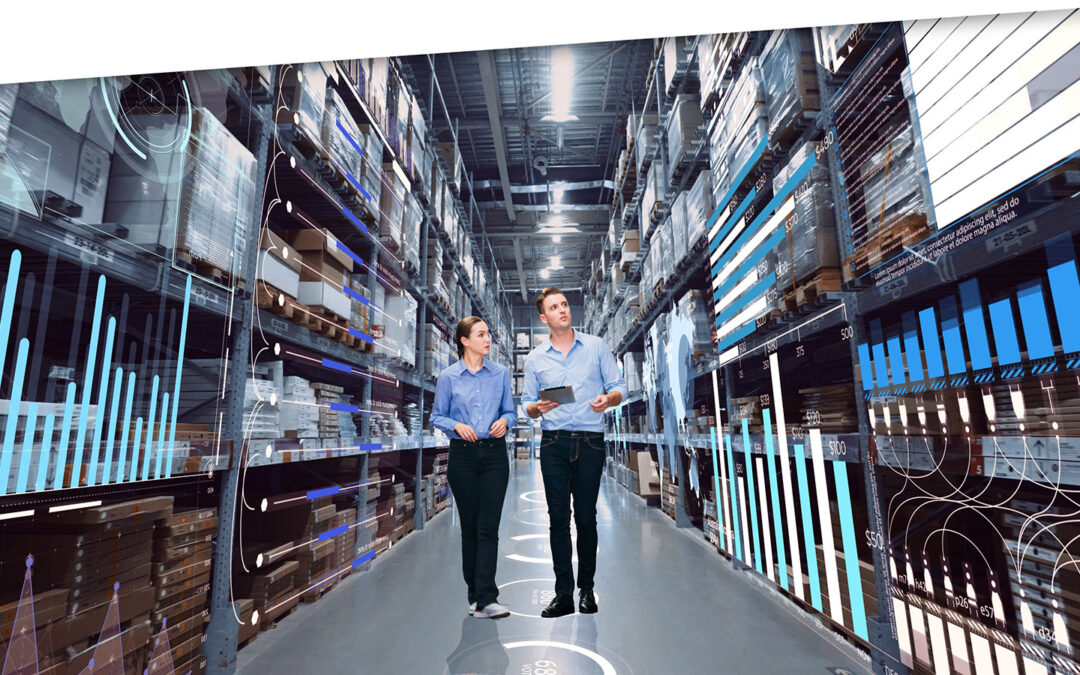
Make AI-Driven Inventory Optimization an Ally for Your Organization
In this blog, we will explore how organizations can achieve exceptional efficiency and accuracy with AI-driven inventory optimization. Traditional inventory management methods often fall short due to their reactive nature and reliance on manual processes. Maintaining optimal inventory levels is fundamental for meeting customer demand while minimizing costs. The introduction of AI-driven inventory optimization can significantly reduce the burden of manual processes, providing relief to supply chain managers from tedious tasks.