Chemical Manufacturer, Bedoukian Research, Uses SmartForecasts to Transform its Supply Chain Planning
Bedoukian Research, Inc., located in Danbury, Connecticut, is a specialized process manufacturer producing high quality ingredients used in flavors and fragrances for customers worldwide. Bedoukian makes 350 specialty chemicals, in small batches, from 2000 raw materials. In addition, the company manufactures fifty insect pheromones used to attract and control insect pests, and resells 100 other products. Two-thirds of its products have hard-to-forecast, intermittent demand.
A Smart Software customer since 1987, Bedoukian Research not only uses SmartForecasts to forecast products with normal demand, but became an early adopter of SmartForecasts intermittent demand forecasting technology.
The Challenge
Many of Bedoukian’s raw materials are sourced in Asia, and are shipped by sea. Lead times can run 2-3 months and affect equipment usage and the company’s ability to meet the company’s high customer service level expectations. Many of the company’s products are built-to-order, and the same raw material might be a component in numerous products. When an ingredient is out-of-stock, it can lead to expensive emergency shipments or lost sales. In addition, Bedoukian’s planning process must account for product shelf lives and changes in commodity pricing.
To achieve high customer service goals, the company needed a solution that would provide accurate stocking level estimates for all of its products, including those with intermittent demand.
The Solution
Bedoukian uses SmartForecasts integrated with Chameleon, an ERP system specifically designed for chemical manufacturers.
Each month, SmartForecasts forecasts the demand for every finished goods item four months into the future, and estimates optimal inventory stocking levels for its raw materials too. The company plans to be one of the first users of Smart Software’s “Bill-of-Materials” forecasting capabilities that should simplify the planning process across product lines, while ensuring that its standard costs keep pace with the escalating costs of raw materials.
The Results
“The intermittent demand forecasting capability has been very useful,” claims Leona Eggleston, who leads the forecasting process. “We’ve gone from forecasting our slow-moving items by hand with poor results to automatically generating highly accurate stocking level estimates.”
In addition, SmartForecasts helps the company see the patterns in its product demand and better track sales performance. When buying patterns change, salespeople can swiftly take remedial action and avoid losing a customer’s business.
In the past five years, Bedoukian has been able to support increased sales with less inventory. While its sales increased 15%, finished goods inventory increased only 4% and raw materials inventory 5%. Additionally, it has improved its customer service by reducing late shipments to customers due to insufficient stock from 16% to 3%.
Improved planning has also enabled Bedoukian to consolidate ocean shipments for almost every raw material which decreases total freight expenses, and cuts down on emergency airfreight costs which saves over $1,000 for every drum.
Bob Bedoukian, president of the company, is more than satisfied and claims, “The more we use SmartForecasts, the more important it becomes for our business and the more efficiently our business runs.”
Driving Better Auto Aftermarket Parts Distribution at Prevost Car with Smart Software
Smart Software’s (SmartForecast®) forecasting solutions increase parts availability and reduce inventory costs
Prevost Car, Inc. is a leading Canadian manufacturer of intercity buses and coach shells for high-end motor home and specialty conversion. Prevost Parts, a division of Prevost Car, serves the North American auto aftermarket distributing original coach and urban bus parts for Prevost Car and Nova Bus, as well as replacement parts for other models. To serve its market, the company maintains two distribution centers, one in Canada and one in the US; five service centers; and over 25,000 active parts. 70 percent of those parts have an intermittent, irregular demand profile, which makes them very hard to forecast and manage.
The Challenge
At the beginning, Prevost Parts’ management started a comprehensive program to improve the company’s parts distribution system. Prevost needed inventories at its warehouses to more accurately reflect demand at those locations, and required more accurate forecasting inputs to its production planning processes. 25 percent of its orders were not being shipped from the distribution point closest to the customer or were backlogged. This situation caused increased transportation costs, delivery delays, and unacceptable customer service levels. In addition, because Prevost’s SAP Min/Max system didn’t compensate for seasonality or trends, the company had too much stock in the off-season and too little when the need was greatest.
To respond to these issues, Prevost’s management conducted a formal evaluation of six demand planning and forecasting systems, including SAP’s demand planning module, to find a solution that would overcome the limitations of the Min/Max system and enable it to use the full potential of SAP’s distribution resources planning (DRP) module. Because the DRP system wasn’t in sync with the demand forecast, product orders weren’t being issued in a timely and accurate manner.
In addition, Prevost Parts was lacking effective demand planning within its multiple site/multiple level distribution network. To accomplish this, the company needed a forecasting solution that could accurately forecast demand for all of its products and deliver accurate safety stock estimates at the lowest level in the network. It also required a system that could provide the flexibility of cumulative lead time measurements, isolate and identify extreme values, recognize seasonal patterns, and provide top-down and bottom-up product group forecasts.
The Solution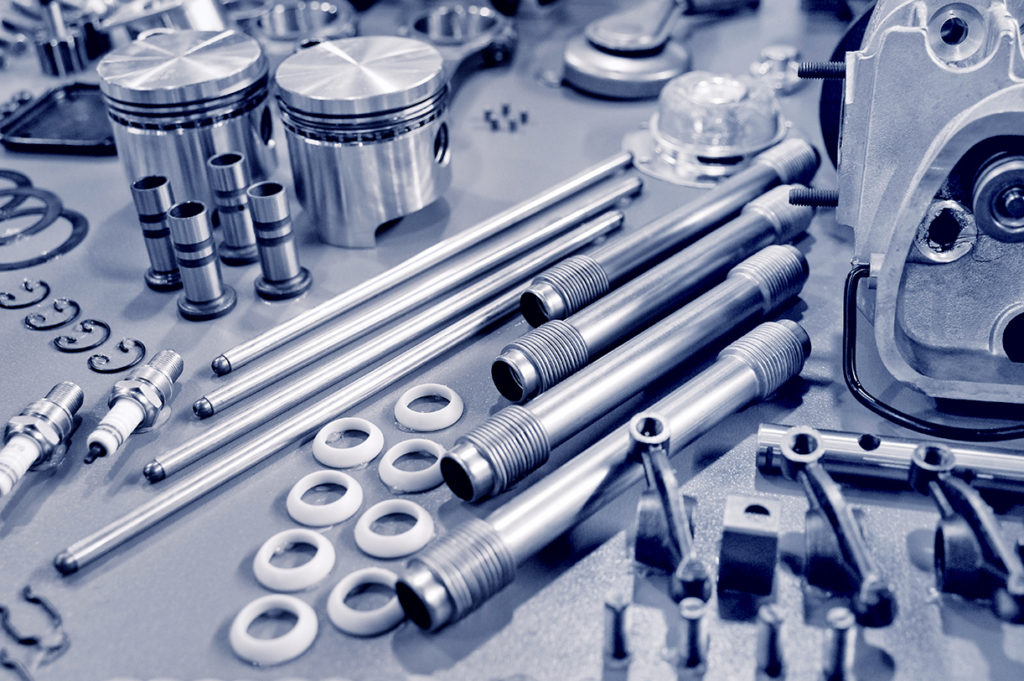
Of the six applications considered, Prevost Parts selected SmartForecasts Enterprise from Smart Software, Inc. SmartForecasts scored highest in the evaluation of more than eight functional criteria. The key deciding factor, however, was SmartForecasts’ ability to generate accurate sales forecasts and safety stock requirements for intermittently demand products. Products of this type are very difficult to forecast because of the slow-moving, irregular nature of their demand patterns.
As Dave Gilbert, logistics director at Prevost Parts, noted, “With most of our parts having intermittent demand, the ability to solve that problem was very important to us, and SmartForecasts’ unique solution in that area was a major advantage.”
In addition, the test results showed that SmartForecasts’ inventory stocking recommendations could reduce required safety stock levels as much as eighteen percent more than the next best application. There were other factors that also weighed in the decision, including SmartForecasts’ ability to interface easily with SAP’s DRP system and simplify the process of managing safety stocks.
The Results
The first year, SmartForecasts was installed at corporate headquarters in Ste. Claire, Quebec, where the software is directly linked to an Oracle database used by Prevost Part’s SAP system to store data and forecasting results. Since implementation, the company’s demand planners have used the system to make a number of planning changes, and those changes have begun to pay off. Backorders of the company’s most frequently demanded parts have been reduced 65%, lost sales are down 59%, and fill rates increased from 93% to 96% in just 3 months.
But the implementation of these changes required Prevost Parts to creatively adjust the way it operates. The company’s strategy for improving its distribution activities required a major shift in the way it forecasted demand. Rather than simply forecasting overall demand, the company needed to forecast demand for each product item at each of its distribution and service centers. This would give a more accurate picture of local demand and enable the company to better align its inventory where it was needed most. Local forecasts could then be rolled up into a company-wide forecast for planning purposes.
At the beginning of every month, Prevost Parts transfers the past month’s consumption data directly from SAP tables in the Oracle database into a Demand History table maintained by SmartForecasts in the same Oracle database. Using SmartForecasts, Prevost automatically produces a forecast of demand and safety stock requirements for all products at each of its distribution and service centers using thirty-six months of history. These forecasts are validated by a demand planner and branch parts managers using audit reports and graphical adjustment facilities in SmartForecasts and then passed to the SAP tables for direct use by the SAP DRP program.
Based on these results, Prevost Parts started stocking its warehouses on a monthly basis, but management quickly found that monthly shipments weren’t meeting its replenishment needs. For this reason, demand is now broken down into weekly buckets, resulting in a Just-in-Time ordering process that has lowered stocking levels at its warehouses.
Prevost plans to continue to measure its progress and savings, and fully expects that it will continue to see major improvements in reducing costs, increasing customer service, and effectively deploying its production and distribution assets. According to Gilbert, “We need to have the right parts in the right place to support our customers. SmartForecasts helps us to not only improve our inventory allocation but also significantly reduce transportation and inventory costs.”
Minnesota’s Metro Transit Improves Parts Inventory planning with Smart Software
SmartForecasts to accurately forecast future parts usage at 14 inventory stocking locations
Belmont, Mass., August 6, 2014 – Smart Software, Inc., leading provider of service level-driven demand planning, today announced that, in a public bidding process, Minnesota’s Metro Transit purchased its flagship product, SmartForecasts®. Smart’s solution has a unique technology for accurately forecasting intermittent demand, solving a critical parts planning challenge for transit systems. In addition to software, Smart Software will provide Metro Transit with consulting, training, and ongoing support services.
The Materials Management Department at Metro Transit will use the software to improve the planning and purchasing of service parts for its bus and rail operations. Many of the company’s parts exhibit hard-to-forecast intermittent demand. The erratic nature of its parts consumption requires an inventory planning system that is easy to use, accurately forecasts future parts usage, and provides reliable inputs into its replenishment process.
Metro Transit is the public transportation system for the Greater Minneapolis/St. Paul, metropolitan area in Minnesota. In 2013, Metro Transit provided 81.4 million bus, commuter rail, and light rail rides on over 128 routes. The company stocks 24,000 parts valued at approximately $42 million which support over 1,000 vehicles. Repair operations are supported by a central warehouse and a network of 13 stocking locations spread throughout the region.
Using service-level driven demand planning techniques enabled by SmartForecasts, Metro Transit’s material planners will know the proper amount of inventory to carry for all parts in all warehouses to meet its challenging service levels.This will be especially important for intermittently demanded items which cannot be forecasted using traditional planning methods. Expected benefits include more effective and less costly resource allocation and increased parts availability to sustain ongoing operations. SmartForecasts will interface with Metro Transit’s Fleetworks ERP system, which handles the parts purchasing function.
“Metro Transit’s ridership has increased by over 5 million rides in the last 4 years. Ensuring a high level of customer service has never been more important,”said Greg Hartunian, president of Smart Software. “Using SmartForecasts to help accurately forecast parts inventory requirements and better understand service vs. financial tradeoffs will help Metro Transit continue to maximize service at a minimum cost.”
Metro Transit joins a number of leading transportation systems in its decision to implement SmartForecasts, including Metro North Railroad, Montreal Transit, and New Jersey Transit.
About Smart Software, Inc.
Founded in 1981, Smart Software, Inc. is a leading provider of enterprise-wide demand forecasting, planning and inventory optimization solutions. Smart Software’s flagship product, SmartForecasts, has thousands of users worldwide, including customers at mid-market enterprises and Fortune 500 companies, such as Abbott Laboratories, Metro-North Railroad, Siemens, Disney, Nestle, Nikon, GE and The Coca-Cola Company. Smart Software is headquartered in Belmont, Massachusetts and can be found online at www.smartsoftware.wpengine.com .
SmartForecasts is a registered trademark of Smart Software, Inc. All other trademarks are the property of their respective owners.
For more information, please contact Smart Software, Inc., Four Hill Road, Belmont, MA 02478.
Phone: 1-800-SMART-99 (800-762-7899); FAX: 1-617-489-2748; E-mail: info@smartsoftware.wpengine.com
SmartForecasts 9.0 Adds Big Data Functionality
Smart Software enhances forecast accuracy and planner productivity
Belmont, Mass., September 27, 2013 – Smart Software, Inc., provider of industry-leading demand forecasting, planning, and inventory optimization solutions, today announced a major upgrade to its flagship product, SmartForecasts®, with enterprise-class productivity and performance enhancements. Release 9.0 is the first SmartForecasts release available both as a perpetual license and through Smart Software’s recently announced SFCloud software as a service solution.
The new release enables planners to work more effectively with very large databases, adds features to improve forecasting for complex bills of material, and improves forecast accuracy by 15% or more. Major capabilities include:
Working with Large Databases
New forecast scheduling capabilities improve productivity by automating functions and enabling them to run unattended as background tasks. This is extremely useful when forecasting a very large number of items, and simplifies and speeds operations such as database saving and hierarchy reconciliation. The new capabilities will save planners working with large data sets considerable time, hours per week, while eliminating manual steps that can introduce human error.
A related productivity-enhancing feature is enhancements to the exception reporting features. SmartForecasts users can now choose to extract data for only those items whose values are outside specified norms. Importing only this data from the database saves time and simplifies the process of forecast adjustment and database reconciliation.
SmartForecasts has also expanded the number of options for file exports in our export module. Users can export data in several additional output formats making it easier to provide results in formats required for ERP import.
Bill of Material Forecasting
Planners can now forecast demand at finished good levels and automatically derive the component demand history and forecasts. Many manufacturers add safety stock to their finished good forecasts in order to ensure a ready supply of components. This can lead to overstocking, since finished good demand is less predictable than the component demand. Using SmartForecasts, planners can now automatically derive an accurate usage history for each component, create service level-driven forecasts, and determine required component safety stock and reorder point levels to ensure adequate supply.
Forecast Accuracy
In version 9.0, the forecasting algorithms in SmartForecasts have been given a tune-up. Tests have confirmed that the new version reduces forecast error by 15% over previous versions. Additionally these enhancements have improved the way that SmartForecasts identifies and handles seasonality, intermittent, and lumpy demand.
Enhancements to SmartInterface
SmartInterface, Smart Software’s database import tool, has been enhanced to enable users to import forecast results into existing forecast projects. Users can now automatically import planned demand, budget forecasts, or known future orders into the forecast tables. It can also be used to import forecast adjustments or new item forecasts from Excel files. This capability provides an exceptionally simple and effective vehicle for incorporating collaborative inputs from sales, product specialists and others who will help fine-tune the forecast.
“SmartForecasts continues to evolve with the market delivering the enterprise-class solution our customers are asking for,” said Nelson Hartunian, president and CEO of Smart Software. “SmartForecasts version 9.0 marks the beginning of a transformation that will broaden the scope of Smart Software’s offerings in the demand planning space and answers the need for comprehensive best-in-class solutions that complement the requirements of corporate information systems.”
SmartForecasts 9.0 will be demonstrated at Booth 1716 at the 2013 APICS International Conference and Expo, in Orlando, Florida, September 29 – 30.
About Smart Software, Inc.
Founded in 1981, Smart Software, Inc. is a leading provider of enterprise-wide demand forecasting, planning and inventory optimization solutions. Smart Software’s flagship product, SmartForecasts, has thousands of users worldwide, including customers at mid-market enterprises and Fortune 500 companies, such as Abbott Laboratories, Metro-North Railroad, Siemens, Disney, Nestle, Nikon, GE and The Coca-Cola Company. Smart Software is headquartered in Belmont, Massachusetts and can be found online at www.smartsoftware.wpengine.com .
SmartForecasts is a registered trademark of Smart Software, Inc. All other trademarks are the property of their respective owners.
For more information, please contact Smart Software, Inc., Four Hill Road, Belmont, MA 02478.
Phone: 1-800-SMART-99 (800-762-7899); FAX: 1-617-489-2748; E-mail: info@smartsoftware.wpengine.com
Flexible SaaS Demand Forecasting Implementation: Smart Software Announces SFCloud
Full-featured cloud-based implementation of enterprise-class SmartForecasts provides additional demand planning options
Belmont, Mass., September 24, 2013 – In a move that broadens the market for its flagship product, SmartForecasts®, Smart Software, Inc., provider of industry-leading demand forecasting, planning, and inventory optimization solutions, today announced SFCloud. SFCloud is a full-featured version of SmartForecasts now available as a software-as-a-service solution. It gives organizations more flexibility in how they deploy SmartForecasts in widely dispersed organizations. The inaugural version of SFCloud features SmartForecasts 9.0.
The SaaS model makes powerful demand planning capabilities available to large and small companies, eliminating much of the complexity associated with sophisticated enterprise applications. With SFCloud, Smart Software installs upgrades and fixes automatically, manages the infrastructure for the customer, and provides much more rigorous security than most company IT organizations are able to deliver.
Companies that prefer a ‘pay as you go’ operating expenditure over the capital purchase of a perpetual license will appreciate the financial flexibility SFCloud affords. While all the functionality of SmartForecasts is available with SFCloud, customers can choose to use the features that they need, for the number of users they need, when they need them. Pricing for the software as a service option is based on the features selected and the number of simultaneous users.
“SFCloud is a significant move for us as we continue to add value to our customers’ demand planning operations,” said Nelson Hartunian, president and CEO of Smart Software. “It gives customers additional implementation options, and opens a market for us with new customers needing a robust enterprise-class demand forecasting solution, accurate intermittent demand forecasting, and more, but don’t have the budget or infrastructure to implement it.”
SFCloud helps demand planners handle large data sets, sales seasonality, promotions, new and aging products, multi-dimensional hierarchies, bills of materials, and intermittently demanded service parts and capital goods items. It also provides inventory managers with accurate estimates of the optimal inventory and safety stock required to meet future orders and achieve desired service levels. SFCloud integrates with virtually any ERP or supply chain planning system including solutions from SAP, Oracle, Microsoft, Infor, Sage and Epicor.
SmartForecasts 9.0 will be demonstrated at Booth 1716 at the 2013 APICS International Conference and Expo, in Orlando, Florida, September 29 and 30.
About Smart Software, Inc.
Founded in 1981, Smart Software, Inc. is a leading provider of enterprise-wide demand forecasting, planning and inventory optimization solutions. Smart Software’s flagship product, SmartForecasts, has thousands of users worldwide, including customers at mid-market enterprises and Fortune 500 companies, such as Abbott Laboratories, Metro-North Railroad, Siemens, Disney, Nestle, Nikon, GE and The Coca-Cola Company. Smart Software is headquartered in Belmont, Massachusetts and can be found online at www.smartsoftware.wpengine.com .
SmartForecasts is a registered trademark of Smart Software, Inc. All other trademarks are the property of their respective owners.
For more information, please contact Smart Software, Inc., Four Hill Road, Belmont, MA 02478.
Phone: 1-800-SMART-99 (800-762-7899); FAX: 1-617-489-2748; E-mail: info@smartsoftware.wpengine.com