As we approach the midpoint in 2013, there is still a lot of economic uncertainty complicating your supply chain planning processes. Some look at this shaky economy and postpone needed investments that can position their organizations for a strong future.
However, this is not the time to retreat from your supply chain improvement initiatives. Rather, it’s a time to double-down on your efforts to prepare for the inevitable business opportunities that lie ahead.
Economic recovery is a time of sales opportunities. You want to make sure that you’re prepared to take advantage of them. Good demand and inventory planning can help.With the right software and planning processes, you can achieve a sound statistical basis for decision-making going forward while making informed adjustments as circumstances dictate. You can improve your ability to read demand signals, spot trends, model future events, and bring your inventory into balance with demand.
Here are six areas of demand and inventory planning where changes you make now can lead to big payoffs when new opportunities arise:
1. Optimize your inventories
When the customer calls, you want to be able to ship. At the same time, you want to control your costs. The surest way to meet that goal is to find the inventory “sweet spot.” That’s where you have the minimum amount of inventory required to satisfy product demand over a specified lead time and at a desired service level.
The ability to accurately set safety stock and inventory levels can set you apart from the competition, and make a difference in your bottom line. However, getting to that point requires a shift in your planning focus from just forecasting future demand to optimizing stocking levels to fill future orders.
If you’d like to know more about achieving the “sweet spot,” you can find a good article published in APICS Magazine here.
2. Implement intermittent demand forecasting solutions
Companies in the service parts, auto aftermarket, and capital goods industries commonly experience intermittent, “slow moving” demand for a large percentage of their inventory items. Accurately forecasting demand and estimating safety stock levels for these types of items is probably the toughest challenge demand planners face. If you can accurately forecast your intermittently demanded parts and products, and have the correct amount of inventory and safety stock on the shelf, you’ve got most of the competition beat!
The reason for this is that items that have intermittent demand do not have normal demand patterns or distributions, making them difficult to forecast using traditional forecasting methods (see the diagram below).
Bar chart illustrating intermittent demand
So, if you have an accurate means of forecasting intermittent demand and estimating safety stock requirements, you’ll be ahead of your competitors that don’t.
If you’d like to know more about forecasting and planning items with intermittent demand, you can find an informative white paper here.
3. Improve lead times
The economic downturn has forced companies to rethink their sourcing strategies because of uncertain demand back home, long lead times to obtain their goods, rising labor costs abroad, and increasing transportation costs. Shortening replenishment lead times can reduce the time required to get the products you need and helps make your supply chain more efficient. It also makes it easier to react to changes in demand when recovery comes.
4. Prioritize service levels
Prioritizing service levels for your products can help insure that the items important to your sales are given the attention they need. For items that are highly demanded, consider setting service levels higher than for those with less demand. Also try doing a revenue-based ABC analysis of your company’s stock-keeping units (SKUs) and set service levels accordingly in your software planning solution.
For example, you might set the service levels for your “bread and butter” items at 95-99% or higher, while setting service levels much lower (at 70-80% or even less) for other items. In this way, you may find that you need much less stock for some of your SKUs and more stock for others to effectively achieve your overall service level goals.
5. Use more recent demand history in creating your forecasts
Because the economy has been changing so fast, it may be time to shorten the demand history used in generating your forecasts so more emphasis is placed on recent trends and demand patterns—reflecting the “new normal”—rather than those contained in outdated history from 3 or 4 years ago. This, of course, should be done in consultation with your management team and preferably as part of an organized S&OP process that thoroughly evaluates both the risks and benefits of adopting this strategy.
6. Invest in technologies and resources that help you capitalize on opportunities
Investing in the right tools and processes increases your competitive advantage. If you aren’t doing so already, here are some valuable things to consider:
• Start an S&OP process, or fine tune your current process, to include key stakeholders in the supply chain and also ensure that demand forecasting and inventory planning provide key inputs in that planning process.
• If your forecasting software is not good at picking up trends, or cannot handle the portion of your inventory with intermittent demand, find software that’s up to the task.
• Find software that will take your forecast results and generate accurate inventory stocking levels to satisfy demand for your products, components or raw materials over specified lead times and at service levels you desire.
• Look for software solutions that are scalable, yet have a relatively low total cost of ownership, fast payback and high ROI.
• Finally, don’t scrimp on training; get all the training and consulting you need to get the “biggest bang” from your software investments.
Do you have anything to add? What are you doing to prepare for the economic recovery? Please leave a comment.
Charles Smart is the founding President of Smart Software. He currently serves as Vice Chairman, on Smart Software’s Board of Directors, as a company spokesman and in development of strategic business relationships. Prior to founding Smart Software, he was a management consultant at the Stanford Research Institute (SRI International) and Policy Analysis, Inc., and served as a Lieutenant in the U.S. Navy.
Related Posts

Innovating the OEM Aftermarket with AI-Driven Inventory Optimization
The aftermarket sector provides OEMs with a decisive advantage by offering a steady revenue stream and fostering customer loyalty through the reliable and timely delivery of service parts. However, managing inventory and forecasting demand in the aftermarket is fraught with challenges, including unpredictable demand patterns, vast product ranges, and the necessity for quick turnarounds. Traditional methods often fall short due to the complexity and variability of demand in the aftermarket. The latest technologies can analyze large datasets to predict future demand more accurately and optimize inventory levels, leading to better service and lower costs.
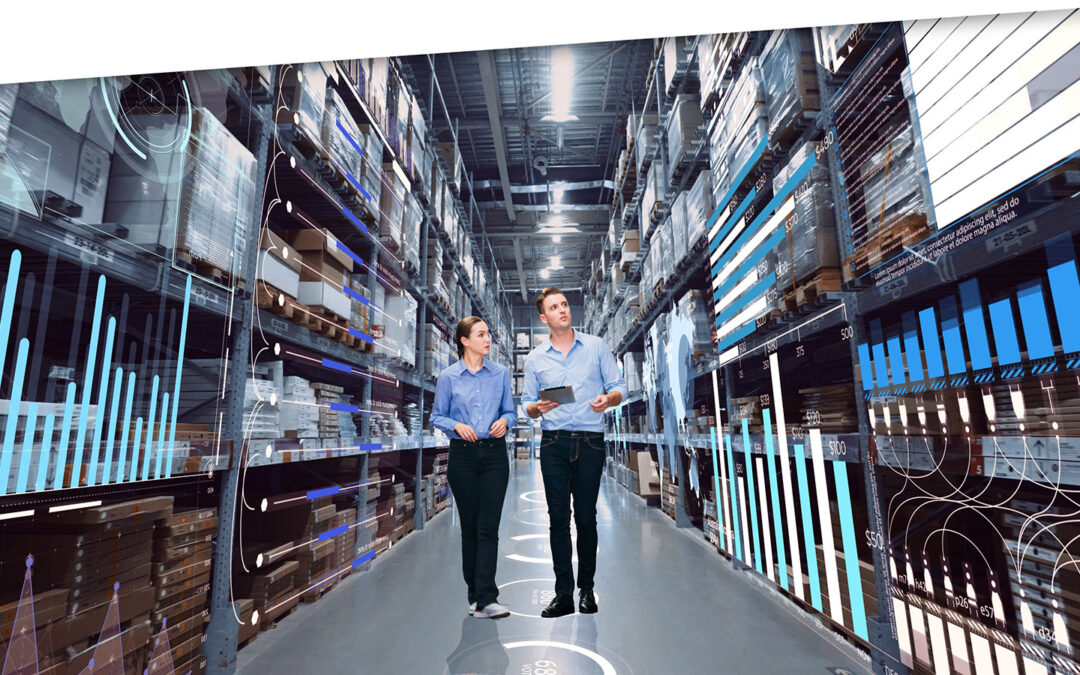
Make AI-Driven Inventory Optimization an Ally for Your Organization
In this blog, we will explore how organizations can achieve exceptional efficiency and accuracy with AI-driven inventory optimization. Traditional inventory management methods often fall short due to their reactive nature and reliance on manual processes. Maintaining optimal inventory levels is fundamental for meeting customer demand while minimizing costs. The introduction of AI-driven inventory optimization can significantly reduce the burden of manual processes, providing relief to supply chain managers from tedious tasks.

Future-Proofing Utilities: Advanced Analytics for Supply Chain Optimization
Utilities in the electrical, natural gas, urban water, and telecommunications fields are all asset-intensive and reliant on physical infrastructure that must be properly maintained, updated, and upgraded over time. Maximizing asset uptime and the reliability of physical infrastructure demands effective inventory management, spare parts forecasting, and supplier management. A utility that executes these processes effectively will outperform its peers, provide better returns for its investors and higher service levels for its customers, while reducing its environmental impact.