Most statistical forecasting works in one direct flow from past data to forecast. Forecasting with leading indicators works a different way. A leading indicator is a second variable that may influence the one being forecasted. Applying testable human knowledge about the predictive power in the relationship between these different sets of data will sometimes provide superior accuracy.
Most of the time, a forecast is based solely on the past history of the item being forecast. Let’s assume that the forecaster’s problem is to predict future unit sales of an important product. The process begins with gathering data on the product’s past sales. (Gregory Hartunian shares some practical advice on choosing the best available data in a previous post to the Smart Forecaster.) This data flows into forecasting software, which analyzes the sales record to measure the level of random variability and exploit any predictable aspects, such as trend or regular patterns of seasonal variability. The forecast is based entirely on the past behavior of the item being forecasted. Nothing that might have caused the wiggles and jiggles in the product’s sales graph is explicitly accounted for. This approach is fast, simple, self-contained and scalable, because software can zip through a huge number of forecasts automatically.
But sometimes the forecaster can do better, at the cost of more work. If the forecaster can peer through the fog of randomness and identify a second variable that influences the one being forecasted, a leading indicator, more accurate predictions are possible.
For example, suppose the product is window glass for houses. It may well be that increases or decreases in the number of construction permits for new houses will be reflected in corresponding increases or decreases in the number of sheets of glass ordered several months later. If the forecaster can distill this “lagged” or delayed relationship into an equation, that equation can be used to forecast glass sales several months hence using known values of the leading indicator. This equation is called a “regression equation” and has a form something like:
Sales of glass in 3 months = 210.9 + 26.7 × Number of housing starts this month.
Forecasting software can take the housing start and glass sales data and convert them into such a regression equation.
Graph displaying a relationship between example figures for time-shifted building permits and demand for glass
Leading indicators demonstrated
However, unlike automatic statistical forecasting based on a product’s past sales, forecasting with a leading indicator faces the same problem as the proverbial recipe for rabbit stew: “First catch a rabbit”. Here the forecaster’s subject matter expertise is critical to success. The forecaster must be able to nominate one or more candidates for the job of leading indicator. After this crucial step, based on the forecaster’s knowledge, experience and intuition, then software can be used to verify that there really is a predictive, time-delayed relationship between the candidate leading indicator and the variable to be forecasted.
This verification step is done using a “cross-correlation” analysis. The software essentially takes as input a sequence of values of the variable to be forecasted and another sequence of values of the supposed leading indicator. Then it slides the data from the forecast variable ahead by, successively, one, two, three, etc. time periods. At each slip in time (called a “lag”, because the leading indicator is lagging further and further behind the forecast variable), the software checks for a pattern of association between the two variables. If it finds a pattern that is too strong to be explained as a statistical accident, the forecaster’s hunch is confirmed.
Obviously, forecasting with leading indicators is more work than forecasting using only an item’s own past values. The forecaster has to identify a leading indicator, starting with a list suggested by the forecaster’s subject matter expertise. This is a “hand-crafting” process that is not suited to mass production of forecasts. But it can be a successful approach for a smaller number of important items that are worth the extra effort. The role of forecasting software, such as our SmartForecasts system, is to help the forecaster authenticate the leading indicator and then exploit it.
Thomas Willemain, PhD, co-founded Smart Software and currently serves as Senior Vice President for Research. Dr. Willemain also serves as Professor Emeritus of Industrial and Systems Engineering at Rensselaer Polytechnic Institute and as a member of the research staff at the Center for Computing Sciences, Institute for Defense Analyses.
Related Posts
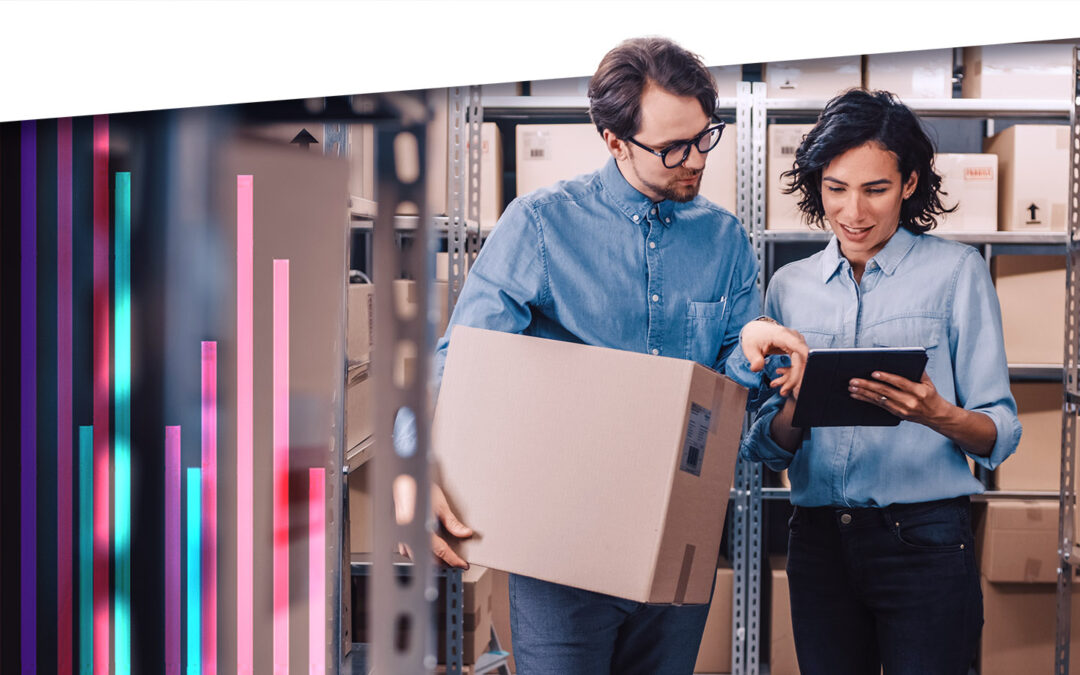
Forecast-Based Inventory Management for Better Planning
Forecast-based inventory management, or MRP (Material Requirements Planning) logic, is a forward-planning method that helps businesses meet demand without overstocking or understocking. By anticipating demand and adjusting inventory levels, it maintains a balance between meeting customer needs and minimizing excess inventory costs. This approach optimizes operations, reduces waste, and enhances customer satisfaction.
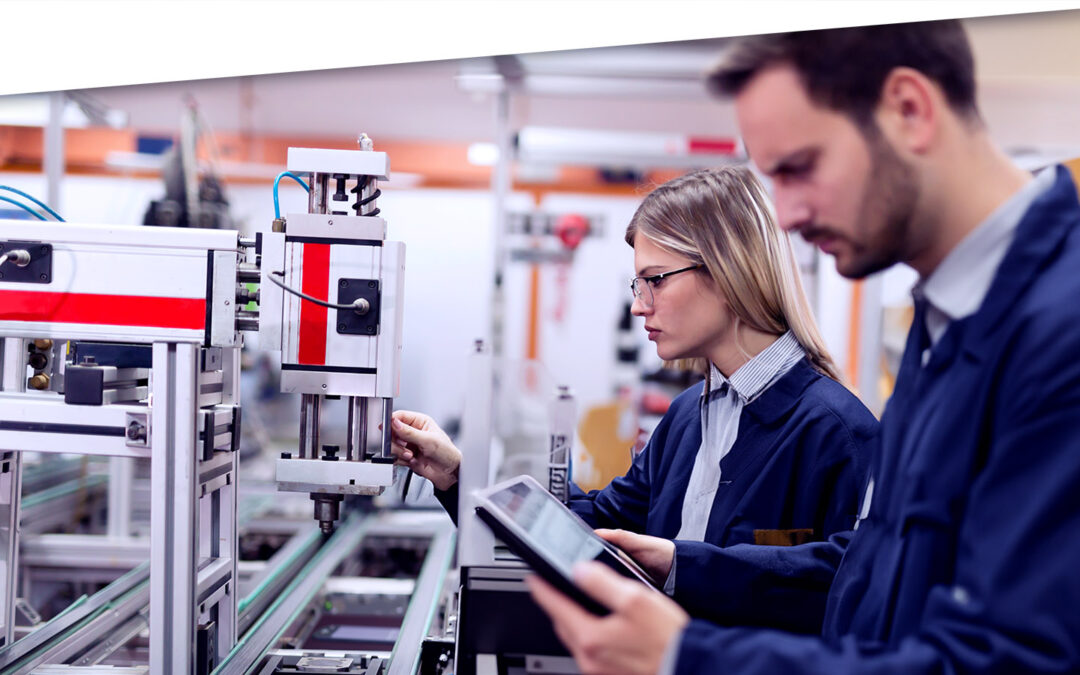
Leveraging Epicor Kinetic Planning BOMs with Smart IP&O to Forecast Accurately
In this blog, we explore how leveraging Epicor Kinetic Planning BOMs with Smart IP&O can transform your approach to forecasting in a highly configurable manufacturing environment. Discover how Smart, a cutting-edge AI-driven demand planning and inventory optimization solution, can simplify the complexities of predicting finished goods demand, especially when dealing with interchangeable components. Learn how Planning BOMs and advanced forecasting techniques enable businesses to anticipate customer needs more accurately, ensuring operational efficiency and staying ahead in a competitive market.
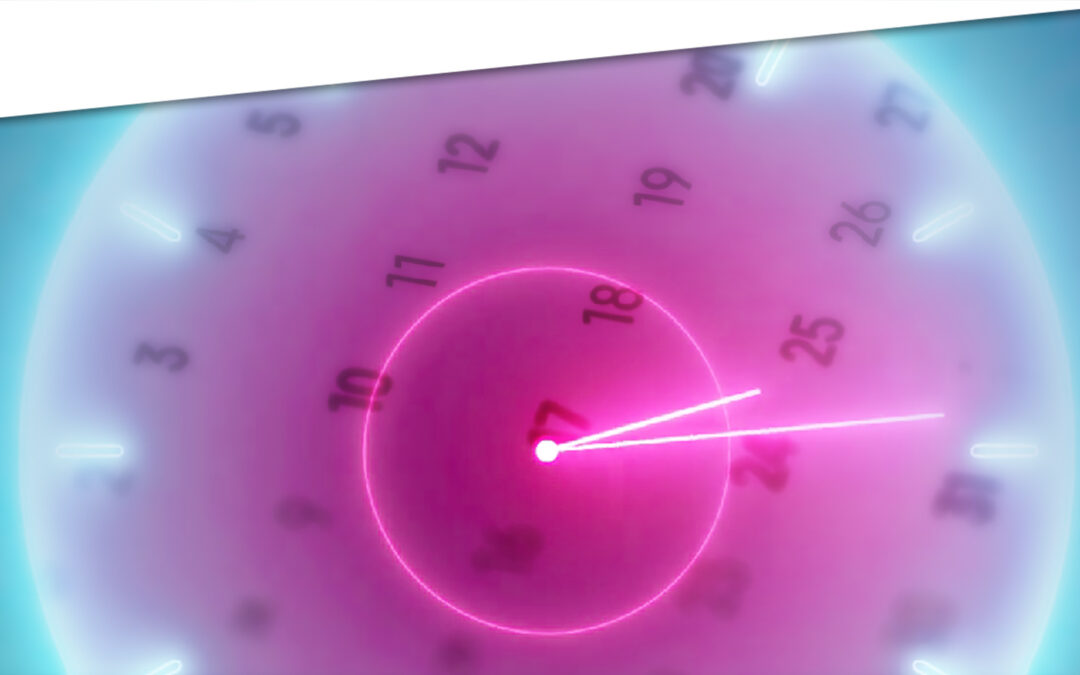
Daily Demand Scenarios
In this Videoblog, we will explain how time series forecasting has emerged as a pivotal tool, particularly at the daily level, which Smart Software has been pioneering since its inception over forty years ago. The evolution of business practices from annual to more refined temporal increments like monthly and now daily data analysis illustrates a significant shift in operational strategies.