Smart Software Launches Smart Inventory Optimization and Demand Planning for Prophet 21
Smart Software, a leader in enterprise demand planning, consensus forecasting, and inventory optimization solutions announces the release of Smart Inventory Planning and Optimization (Smart IP&O) for Prophet 21 (P21). The company will demonstrate the solution at the Connect 2022, P21’s Annual User Group Conference August 29th – August 31st. With Smart IP&O, Prophet 21 users will now be able to:
- Conduct Global What if Scenarios across thousands of parts that compare Smart prescribed, user defined, and P21 calculated stocking policies across Key Performance Predictions of Service Levels, Fill Rates, Shortage Costs, Inventory Value, and more.
- Leverage Smart’s prescribed stocking policies and service level recommendations that will optimally yield the most profitable outcomes for each part considering predicted holding costs, ordering costs, and shortage costs.
- Accurately forecast all demand patterns including intermittent demand that is highly prevalent with distribution businesses. Smart’s patented probabilistic modeling engine generates thousands of future demand scenarios that more accurately predict demand and stocking policies.
- Develop consensus forecasts comparing statistical, P21 generated forecasts, sales, and customer forecasts. Smart’s Demand Planning workbench enables graphical and tabular visualizations of all forecasts considered and supports automated consensus forecasting and accuracy measurement.
- Leverage Smart IP&O’s bi-directional integration to P21 that continually updates Smart’s common data model with planning data and writes back forecasts and stocking policies on demand.
“Smart IP&O extends an already feature rich P21 with difference making forecasting and inventory optimization technology. Our joint customers will now be able to more effectively wield inventory to build a competitive moat around their business, maximize sales, and outperform the competition,” said Greg Hartunian, Smart Software CEO. “Today’s supply chains need far better capabilities to contend with the extreme demand and supply variability businesses are facing today. We look forward to equipping our Epicor P21 customers with the tools to do this effectively, accurately, and at scale.”
About Smart Software, Inc.
Founded in 1981, Smart Software, Inc. is an Epicor Platinum Partner and leading provider of demand planning, forecasting, inventory optimization, and analytics solutions. Our web platform, Smart IP&O, leverages probabilistic forecast modeling, machine learning, and collaborative demand planning to optimize inventory levels and increase forecast accuracy. Smart Software is headquartered in Belmont, Massachusetts. To learn more, visit www.smartcorp.com.
Smart Software to Present at Epicor Insights 2022
Smart Software President and CEO to present Epicor Insights 2022 Sessions on Creating Competitive Advantage with Smart Inventory Planning and Optimization
Belmont, MA, May, 2022 – Smart Software, Inc., provider of industry-leading demand forecasting, planning, and inventory optimization solutions, today announced that it will present at Epicor Insights 2022.
Greg Hartunian, CEO of Smart Software, will present two sessions and will explain Epicor Smart Inventory Planning and Optimization at this year’s Epicor Insights event in Nashville, TN. Greg will show how to empower planning teams to reduce inventory, improve service levels, and increase operational efficiency.
- The Prophet 21 presentation is scheduled for Wed May 25th, 11:30 am -12:15 pm (CST)
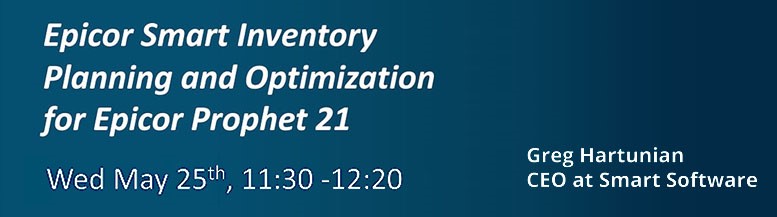
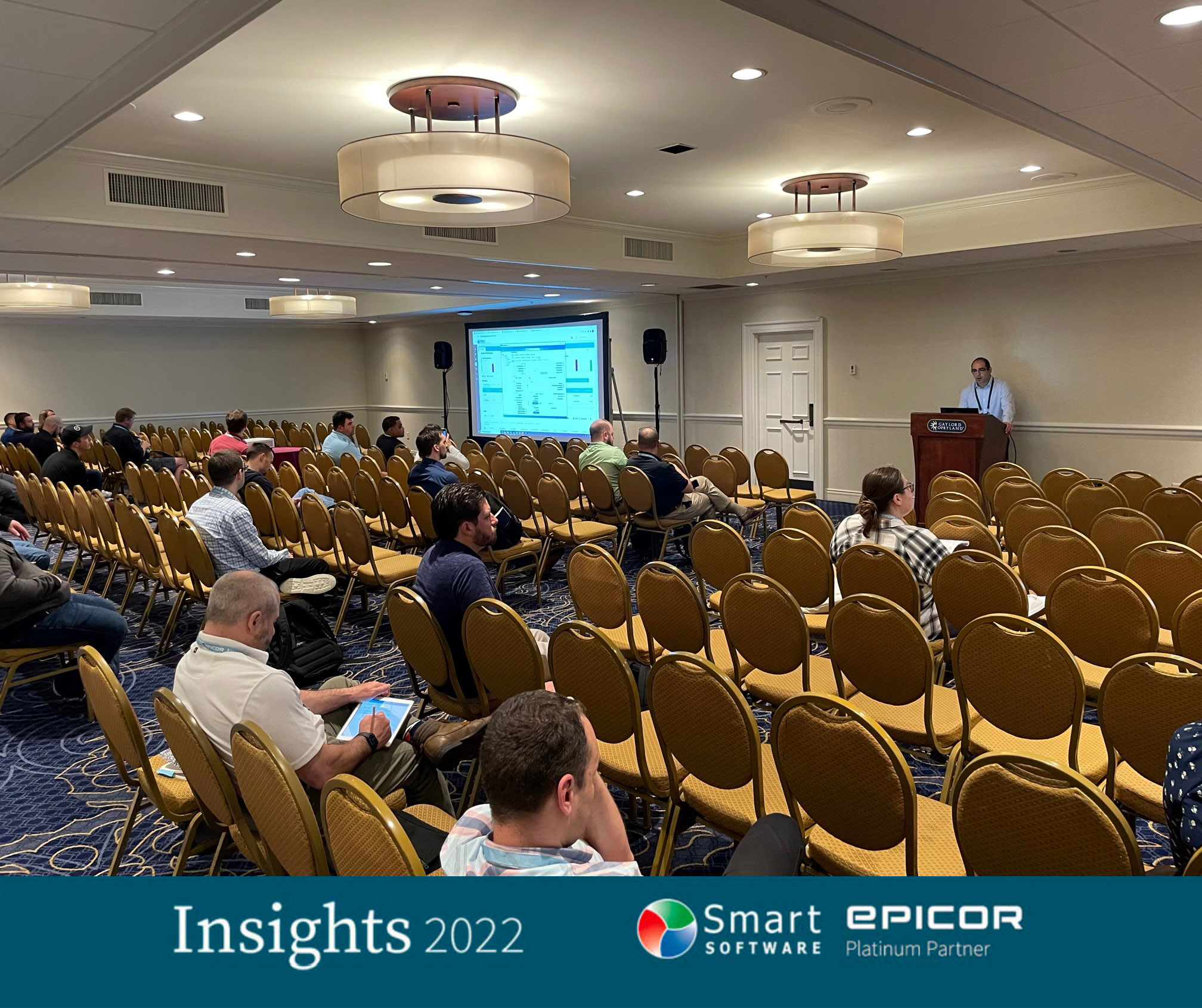
- The Kinetic presentation is scheduled for Wed May 25th, 2:30 pm – 3:20 pm (CST)
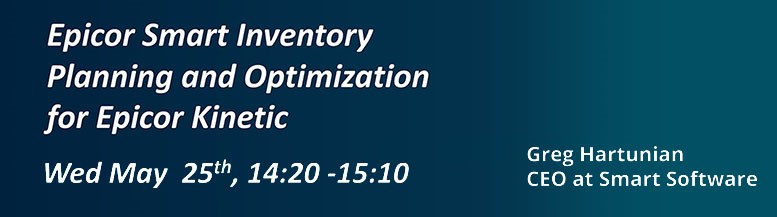
If you plan to attend this year, please join us at either session below and learn more about Smart Inventory Planning and Optimization as we highlight valuable features in our solutions. Epicor Insights 2022 will bring together more than 2,000 users of Epicor’s industry-specific ERP solutions for the manufacturing, distribution, and service industries. To learn more, visit INSIGHTS 2022.
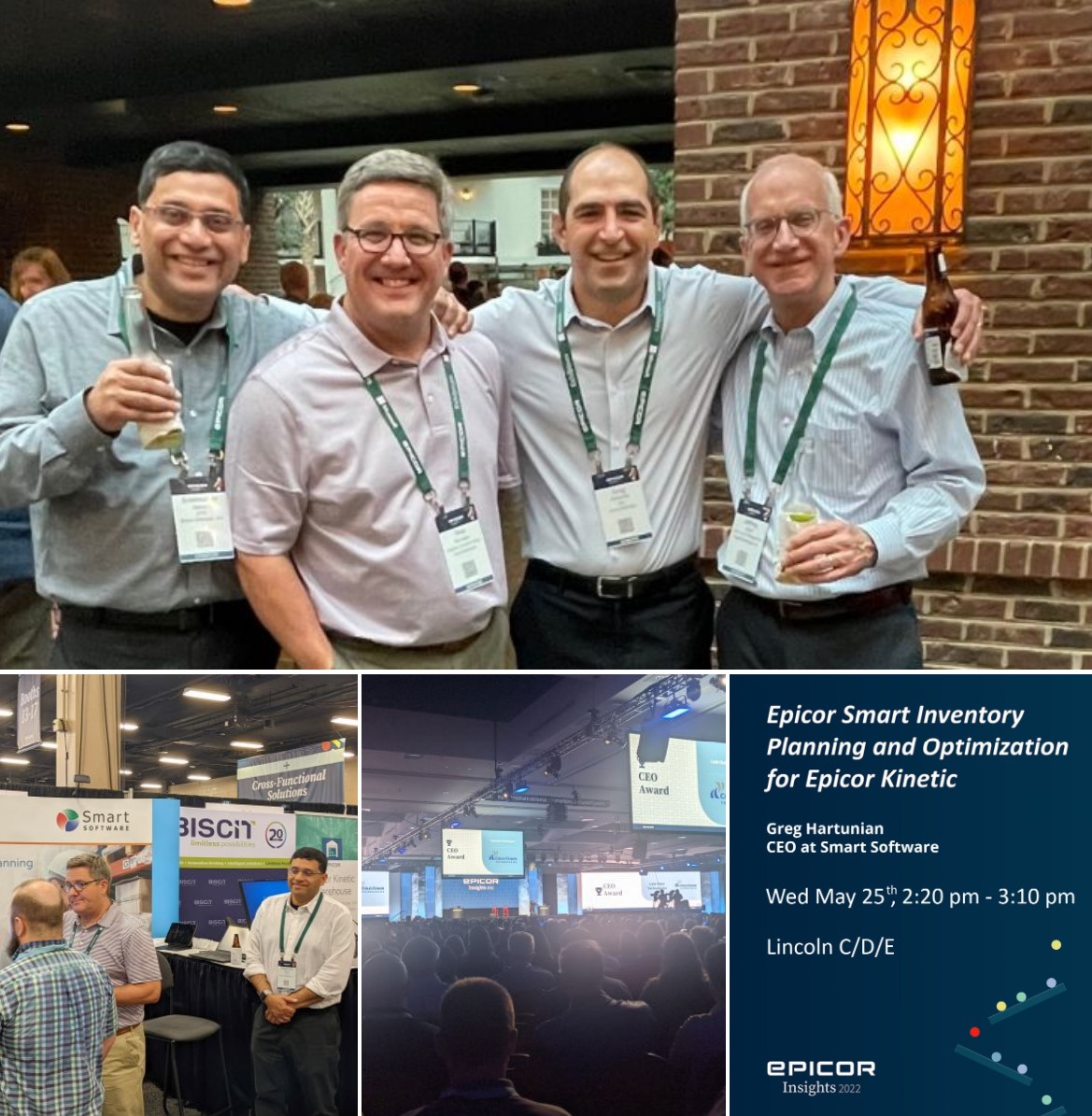
Smart Software is an Epicor Platinum Partner and leading provider of demand planning, forecasting, inventory optimization, and analytics solutions. Our web platform, Smart IP&O, leverages probabilistic forecast modeling, machine learning, and collaborative demand planning to optimize inventory levels and increase forecast accuracy. You’ll use Smart IP&O to create accurate forecasts and optimal stocking policies that drive automated ordering in Epicor. The platform includes bi-directional integrations to both Epicor ERP and Prophet 21.
About Smart Software, Inc.
Founded in 1981, Smart Software, Inc. is a leader in providing businesses with enterprise-wide demand forecasting, planning and inventory optimization solutions. Smart Software’s demand forecasting and inventory optimization solutions have helped thousands of users worldwide, including customers at mid-market enterprises and Fortune 500 companies, such as Disney, Arizona Public Service, and Ameren. Smart Inventory Planning & Optimization gives demand planners the tools to handle sales seasonality, promotions, new and aging products, multi-dimensional hierarchies, and intermittently demanded service parts and capital goods items. It also provides inventory managers with accurate estimates of the optimal inventory and safety stock required to meet future orders and achieve desired service levels. Smart Software is headquartered in Belmont, Massachusetts and can be found on the World Wide Web at www.smartcorp.com.
For more information, please contact Smart Software, Inc., Four Hill Road, Belmont, MA 02478.
Phone: 1-800-SMART-99 (800-762-7899); FAX: 1-617-489-2748; E-mail: info@smartcorp.com
Smart Software to Present at Epicor Insights 2021
Smart Software President and CEO to present Epicor Insights 2021 Breakout Session on Creating Competitive Advantage with Smart Inventory Planning and Optimization
Belmont, MA, June, 2021 – Smart Software, Inc., provider of industry-leading demand forecasting, planning, and inventory optimization solutions, today announced that it will present at Epicor Insights 2021.
Greg Hartunian, CEO of Smart Software, will present “Creating Competitive Advantage with Smart Inventory Planning and Optimization.” Greg will explain how to empower planning teams to reduce inventory, improve service levels, and increase operational efficiency. Most inventory planning teams rely upon traditional forecasting approaches, rule of thumb methods, and sales feedback on demand. Our Breakout Session at Epicor Insights discusses these approaches, why they often fail, and how new probabilistic forecasting and optimization methods can make a big difference to your bottom line.
- The presentation is scheduled for Wed July 14th 10:25 -11:15 AM (PST)

Epicor Insights 2021 will bring together more than 2,000 users of Epicor’s industry-specific ERP solutions for the manufacturing, distribution, and service industries. To learn more, visit INSIGHTS 2021.
Join us at Mandalay Bay in Las Vegas, at the Solution Pavilion, Booth #1.


Smart Software is an Epicor Platinum Partner and leading provider of demand planning, forecasting, inventory optimization, and analytics solutions. Our web platform, Smart IP&O, leverages probabilistic forecast modeling, machine learning, and collaborative demand planning to optimize inventory levels and increase forecast accuracy. You’ll use Smart IP&O to create accurate forecasts and optimal stocking policies that drive automated ordering in Epicor. The platform includes bi-directional integrations to both Epicor ERP and Prophet 21.
About Smart Software, Inc.
Founded in 1981, Smart Software, Inc. is a leader in providing businesses with enterprise-wide demand forecasting, planning and inventory optimization solutions. Smart Software’s demand forecasting and inventory optimization solutions have helped thousands of users worldwide, including customers at mid-market enterprises and Fortune 500 companies, such as Mitsubishi, Siemens, Disney, FedEx, MARS, and The Home Depot. Smart Inventory Planning & Optimization gives demand planners the tools to handle sales seasonality, promotions, new and aging products, multi-dimensional hierarchies, and intermittently demanded service parts and capital goods items. It also provides inventory managers with accurate estimates of the optimal inventory and safety stock required to meet future orders and achieve desired service levels. Smart Software is headquartered in Belmont, Massachusetts and can be found on the World Wide Web at www.smartcorp.com.
For more information, please contact Smart Software, Inc., Four Hill Road, Belmont, MA 02478.
Phone: 1-800-SMART-99 (800-762-7899); FAX: 1-617-489-2748; E-mail: info@smartcorp.com
Why pick arbitrary Service Level Targets?
Why pick arbitrary Service Level Targets? Learn how to select automatically the optimal Targets @scale minimizing total costs for your business.
There are unavoidable tradeoffs between inventory cost and item availability. The Smart Inventory Optimization (SIO) app calculates all the key metrics to expose those tradeoffs. You can try “what-if” experiments such as “What happens to shortage cost if we raise the reorder point from 5 to 10?”. Better yet, you can let SIO find the optimal operating policy, e.g., the lowest cost combination of reorder point and order quantity that guarantees a 95% service level.
In this blog, we’ll explore several effective strategies for managing spare parts inventory, emphasizing the importance of optimizing stock levels, maintaining service levels, and using smart tools to aid in decision-making. Managing spare parts inventory is a critical component for businesses that depend on equipment uptime and service reliability. Unlike regular inventory items, spare parts often have unpredictable demand patterns, making them more challenging to manage effectively. An efficient spare parts inventory management system helps prevent stockouts that can lead to operational downtime and costly delays while also avoiding overstocking that unnecessarily ties up capital and increases holding costs.
Managing inventory effectively is critical for maintaining a healthy balance sheet and ensuring that resources are optimally allocated. Here is an in-depth exploration of the main causes of overstocking, their implications, and possible solutions.
Effective supply chain and inventory management are essential for achieving operational efficiency and customer satisfaction. This blog provides clear and concise answers to some basic and other common questions from our Smart IP&O customers, offering practical insights to overcome typical challenges and enhance your inventory management practices. Focusing on these key areas, we help you transform complex inventory issues into strategic, manageable actions that reduce costs and improve overall performance with Smart IP&O.
Backing into Safety Stock is the Safe Play
We frequently encounter confusion about the process of setting safety stock levels. This blog hopes to clarify the issue.
Safety stock is a critical component in any system of inventory management. Indeed, some inventory software treats safety stock as the key decision variable in the quest to balance inventory cost against item availability. Unfortunately, that approach is not the best way to strike the balance.
First, realize that safety stock is part of a general equation:
Inventory Target = Average Lead Time Demand + Safety Stock.
Average Lead Time Demand is defined as the average units demanded multiplied by the average replenishment lead time. Example: If daily demand averages 2 units and the average lead time is 7 days, then the average lead time demand is 2 x 7= 14 units. Keeping 14 units on hand suffices to handle typical demand.
But we all know that demand is random, so keeping enough stock on hand to cover the average lead time demand invites stockouts. As we like to say, “The average is not the answer.” The smart answer is to add in some safety stock to accommodate any random spikes in demand. But how much?
There’s the problem. If you try to guesstimate a number for the safety stock, you are on thin ice. How do you know what the “right” number is? You may think that you don’t have to worry about that because you have a good-enough answer now, but that answer has a sell-by date. Lead times change. So do demand patterns. So do company priorities. That means today’s good answer may become tomorrow’s blunder.
Some companies try to wing it using a crude rule of thumb approach. For instance, they may say something like “Set safety stock at an additional two weeks of average demand.” This approach is seductive: It only needs simple math, and it is clear. But for the reasons listed in the previous paragraph, it’s foolish. Better to get a good answer than a convenient answer.
You need a principled, objective way to answer the question that takes account of the mathematics of randomness. More than that, you need an answer that is linked to the key performance indicators (KPI’s) of the system: inventory cost and item availability.
Simple logic gives you some sense of the answer, but it doesn’t provide the number you need. You know that more safety stock increases both cost and availability, while less safety stock decreases both. But without knowing how much those metrics will change if you change the safety stock, you have no way to align the safety stock decision with management’s intent for striking the balance between cost and availability.
Rather than flying blind, you can back into the choice of safety stock by first finding the right choice for inventory target. Once you’ve done that, the safety stock pops out by a simple subtraction:
Safety Stock = Inventory Target – Average Lead Time Demand.
Often times, companies will state that they don’t carry safety stock because the safety stock field in their ERP system is blank. Nearly always, safety stock is built into the targeted inventory level they have established. So, using the above formula to “back out” how much safety stock you are building into the plan is quite helpful. The key is not just to know how much safety stock you are carrying but the link between your inventory target, safety stocks, and its corresponding KPI’s.
For instance, suppose you can tolerate only a 5% chance of stocking out while waiting for replenishment (inventory texts call this interval the “period of risk.”). Software can examine the demand history of each item and work out the odds of stockout based on the thousands of different demand scenarios that can occur during the lead time. Then the right answer for the inventory target is the choice that leads to no more than a 5% stockout risk. Given that target and knowing the average lead time demand, the appropriate safety stock value falls right out by subtraction. You also get to know the average holding, ordering and shortage costs.
That’s what we mean by “backing into the safety stock.” Start with company objectives, determine the appropriate inventory target, then derive the safety stock as the last step. Don’t start with a guess about safety stock and hope for the best.
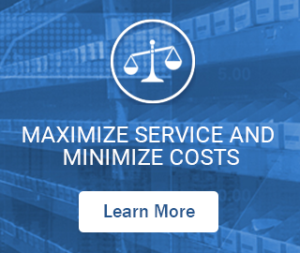
In this blog, we’ll explore several effective strategies for managing spare parts inventory, emphasizing the importance of optimizing stock levels, maintaining service levels, and using smart tools to aid in decision-making. Managing spare parts inventory is a critical component for businesses that depend on equipment uptime and service reliability. Unlike regular inventory items, spare parts often have unpredictable demand patterns, making them more challenging to manage effectively. An efficient spare parts inventory management system helps prevent stockouts that can lead to operational downtime and costly delays while also avoiding overstocking that unnecessarily ties up capital and increases holding costs.
Managing inventory effectively is critical for maintaining a healthy balance sheet and ensuring that resources are optimally allocated. Here is an in-depth exploration of the main causes of overstocking, their implications, and possible solutions.
Effective supply chain and inventory management are essential for achieving operational efficiency and customer satisfaction. This blog provides clear and concise answers to some basic and other common questions from our Smart IP&O customers, offering practical insights to overcome typical challenges and enhance your inventory management practices. Focusing on these key areas, we help you transform complex inventory issues into strategic, manageable actions that reduce costs and improve overall performance with Smart IP&O.