Managing Demand Variability
Anybody doing the job knows that managing inventory can be stressful. Common stressors include: Customers with “special” requests, IT departments with other priorities, balky ERP systems running on inaccurate data, raw material shortages, suppliers with long lead times in far-away countries where production often stops for various reasons and more. This note will address one particular and ever-present source of stress: demand variability.
Everybody Has a Forecasting Problem
Suppose you manage a large fleet of spare parts. These might be surgical equipment for your hospital, or repair parts for your power station. Your mission is to maximize up time. Your enemy is down time. But because breakdowns hit at random, you are constantly in reactive mode. You might hope for rescue from forecasting technologies. But forecasts are inevitably imperfect to some degree: the element of surprise is always present. You might wait for Internet of Things (IOT) tech to be deployed on your equipment to monitor and detect impending failures, helping you schedule repairs well in advance. But you know you can’t meter up the thousands of small things that can fail and disable a big thing.
So, you decide to combine forecasting with inventory management and build buffers or safety stock to protect against surprise spikes in demand. Now you have to work out how much safety stock to maintain, knowing that too little means vulnerability and too much means bloat.
Suppose you handle finished goods inventories for a make-to-stock company. Your problem is essentially the same as in managing service parts: You have external customers and uncertain demand. But you may also have additional problems in terms of synchronizing multiple suppliers of components that you assemble into finished goods. The suppliers want you to tell them how much of their stuff to make so you can make your stuff, but you don’t know how much of your own stuff you’ll need to make.
Finally, suppose you handle finished goods in a build-to-order company. You might think that you no longer have a forecasting problem, since you don’t build until you are paid to build. But you do have a forecasting problem. Since your finished goods might be assembled from a mixture of components and sub-assemblies, you have to translate some forecast of finished goods demand to work out a forecast of those components. Otherwise, you will go to make your finished goods and discover that you don’t have a required component and have to wait until you can re-actively assemble everything you need. And your customers might not be willing to wait.
So, everybody has a forecasting problem.
What Makes Forecasting Difficult
Forecasting can be quick, easy and dead accurate – as long as the world is simple. If demand for your product is 10 units every week, month after month, you can make very accurate forecasts. But life is not quite like that. If you’re lucky and life is almost like that – maybe weekly demand is more like {10, 9, 10, 8, 12, 10, 10…} — you can still make very accurate forecast and just make minor adjustments around the edges. But if life is as it more often is – maybe weekly demand looks like {0, 0, 7, 0, 0, 0, 23, 0 …} – demand forecasting is difficult indeed. The key distinction is demand variability: it’s the zigging and zagging that creates the pain.
Safety Stock Takes Over Where Forecasting Leaves Off
Statistical forecasting methods are an important part of the solution. They let you squeeze as much advantage as possible from the historical patterns of demand your company has recorded for each item. The job of forecasts is to describe what is typical, which provides the base on which to cope with randomness in demand. Statistical forecasting techniques work by finding “big picture” features in demand records, such as trend and seasonality, then projecting those into the future. They all implicitly assume that whatever patterns exist now will persist, so 5% growth will continue, and July demand will always be 20% higher than February demand. To get to that point, statistical forecasting methods use some form of averaging to smother the “noise” in the demand history.
But then the rest of the job falls on inventory management, because the atypical, random component of future demand will still be a hassle in the future. This inevitable level of uncertainty has to be handled by the “shock-absorber” called safety stock.
The same methods that produce forecasts of trend and/or seasonality can be used to estimate the amount of forecast error. This has to be done carefully using a method called “holdout analysis”. It works like this. Suppose you have 365 observations of daily demand for Item X, which has a replenishment lead time of 10 days. You want to know how many units will be demanded over some future 10-day period. You might input the first 305 days of demand history into the forecasting technique and get forecasts for the next 10 days, days 306-315.
The answer gives you one estimate of the 10-day total demand. Importantly, it also gives you one estimate of the variability around that forecast, i.e., the forecast error, the difference between what actually happened in days 306-315 and what was forecasted. Now you can repeat the process, this time using the first 306 days to forecast the next 10, the first 307 days to forecast the next 10, etc. You end up with 52 honest estimates of the variability of total demand over a 10-day lead time. Suppose 95% of those estimates are less than 28 units. Then 28 units would be a pretty safe safety stock to add to the forecast, since you will run into shortages only 5% of the time.
Modern statistical software does these calculations automatically. It can ease at least one of the chronic headaches of inventory management by helping you cope with demand variability.
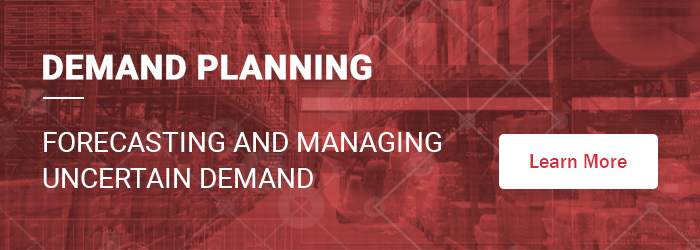
Smart Software is pleased to announce that our article “Managing Inventory amid Regime Change” has won 1st place in the Forecasting category of the 2022 Supply Chain Brief MVP Awards.
Smart Software’s Channel Sales Director and Enterprise Solution Engineer, to present three sessions at this year’s Microsoft Dynamics Community Summit North America event in Orlando, FL.
.
Smart Software, will lead a 30-minute webinar as part of the WERC Solutions Partner Program. The presentation will focus on how a leading Electric Utility implemented Smart Inventory Planning and Optimization (Smart IP&O) as part of the company’s strategic supply chain optimization (SCO) initiative.
V-LINE marks anniversary with conference and Smart keynote.
During the “User Conference: Spare Parts Inventory Planning and Optimization,” topics like vested outsourcing and digital MRO supply chain orchestration were discussed with the participation of Jeff Scott, our vice president of business development at Smart Software.
Jeff discussed the practical process of optimizing spares inventory policies, particularly the challenge of addressing seemingly unforecastable intermittent demand. He reviewed common approaches, their failings, and the value of taking a different approach with probabilistic modeling and improved statistical methods. If you would like to learn more, a good place to start is Smart Software’s recent webinar on Intermittent Demand –
click here to view the replay.

To the right Jeff Scott vice president of business development at Smart Software.
About Smart Software, Inc.
Founded in 1981, Smart Software, Inc. is a leader in providing businesses with enterprise-wide demand forecasting, planning and inventory optimization solutions. Smart Software’s demand forecasting and inventory optimization solutions have helped thousands of users worldwide, including customers at mid-market enterprises and Fortune 500 companies, such as Mitsubishi, Siemens, Disney, FedEx, MARS, and The Home Depot. Smart Inventory Planning & Optimization gives demand planners the tools to handle sales seasonality, promotions, new and aging products, multi-dimensional hierarchies, and intermittently demanded service parts and capital goods items. It also provides inventory managers with accurate estimates of the optimal inventory and safety stock required to meet future orders and achieve desired service levels. Smart Software is headquartered in Belmont, Massachusetts and can be found on the World Wide Web at
www.smartcorp.com.
SmartForecasts and Smart IP&O are registered trademarks of Smart Software, Inc. All other trademarks are the property of their respective owners.
For more information, please contact Smart Software, Inc., Four Hill Road, Belmont, MA 02478.
Phone:
1-800-SMART-99 (800-762-7899); FAX: 1-617-489-2748; E-mail: info@smartcorp.com
Smart Software President and CEO to Present at Microsoft Dynamics NAV 2019
Smart Software to lead Microsoft Dynamics NAV Summit Session on Inventory Optimization and Intermittent Demand
Belmont, Mass., October, 2019 – Smart Software, Inc., provider of industry-leading demand forecasting, inventory planning, and inventory optimization solutions, today announced that CEO Greg Hartunian, will present at the Microsoft Dynamics NAV Summit from October 15-18 in Kissimmee, FL.
Greg Hartunian and Bruce Kennedy, Senior Consultant at ArcherPoint will present “Inventory Optimization and Intermittent Demand – Why Forecasting Isn’t Enough.” The session details how to plan optimal inventory levels for thousands of items when demand is intermittent. Seemingly random, sporadic demand is the worst case scenario for accurately forecasting demand and inventory requirements. Typical planning approaches such as reliance on sales forecasts and rules of thumb methods, why they often fail, and how probabilistic forecasting methods can make a big difference to the bottom line will be discussed. They will demonstrate practical examples, working through a service level-driven methodology to manage risk and find the optimal balance between inventory investment and availability, and then send corresponding replenishment drivers to Business Central 365/NAV to make it so.
The presentation is scheduled for Oct. 16, 1-2 PM. Smart Software will be also exhibiting at the conference showcasing Smart Inventory Planning & Optimization and bi-directional integrations to Microsoft Dynamics NAV, Microsoft Dynamics 365 Business Central, and Microsoft Dynamics AX.

About Smart Software, Inc.
Founded in 1981, Smart Software, Inc. is Microsoft Dynamics Gold Partner and full-service provider for Dynamics NAV and Dynamics 365, a leader in providing demand forecasting, planning and inventory optimization solutions. Smart Software’s demand forecasting and inventory optimization solutions have helped thousands of users worldwide, including customers at mid-market enterprises and Fortune 500 companies, such as Mitsubishi, Siemens, Disney, FedEx, MARS, and The Home Depot. Smart Inventory Planning & Optimization gives demand planners the tools to handle sales seasonality, promotions, new and aging products, multi-dimensional hierarchies, and intermittently demanded service parts and capital goods items. It also provides inventory managers with accurate estimates of the optimal inventory and safety stock required to meet future orders and achieve desired service levels. Smart Software is headquartered in Belmont, Massachusetts and can be found on the World Wide Web at www.smartcorp.com.
SmartForecasts and Smart IP&O are registered trademarks of Smart Software, Inc. All other trademarks are the property of their respective owners.
For more information, please contact Smart Software, Inc., Four Hill Road, Belmont, MA 02478.
Phone: 1-800-SMART-99 (800-762-7899); FAX: 1-617-489-2748; E-mail: info@smartcorp.com

Smart Software to Present at NESCON 2019
Smart Software to lead NESCON keynote address on Planning for the “Un-Plannable”.
Belmont, Mass., July 8, 2019 – Smart Software, Inc., provider of industry-leading demand forecasting, planning, and inventory optimization solutions, today announced that it will present at the NESCON 2019, New England Supply Chain Conference & Exhibition Keynote in Malborough, MA. The presentation is scheduled for Oct. 7, 12:15-1:30 PM.
Greg Hartunian, CEO of Smart Software, under the tittle “Planning for the Un-Plannable”, will present how to plan optimal inventory levels and purchase quantities for thousands of items, when demand is intermittent, constantly changing, or affected by unexpected events. Random, sporadic demand is the worst case scenario for planning and procurement, and leads to excess inventory levels, and costly stock outs. Greg will discuss traditional inventory planning and forecasting approaches, present practical examples of how they can fail, and share how probabilistic modeling methods can make a big difference to your bottom line. The Keynote is a good opportunity to learn how to reduce stock outs and inventory costs, by leveraging data driven decisions that identify the financial trade-offs associated with changes in demand, lead times, service level targets, and costs.

About Smart Software, Inc.
Founded in 1981, Smart Software, Inc. is a leader in providing businesses with enterprise-wide demand forecasting, planning and inventory optimization solutions. Smart Software’s demand forecasting and inventory optimization solutions have helped thousands of users worldwide, including customers at mid-market enterprises and Fortune 500 companies, such as Mitsubishi, Siemens, Disney, FedEx, MARS, and The Home Depot. Smart Inventory Planning & Optimization gives demand planners the tools to handle sales seasonality, promotions, new and aging products, multi-dimensional hierarchies, and intermittently demanded service parts and capital goods items. It also provides inventory managers with accurate estimates of the optimal inventory and safety stock required to meet future orders and achieve desired service levels. Smart Software is headquartered in Belmont, Massachusetts and can be found on the World Wide Web at www.smartcorp.com.
SmartForecasts and Smart IP&O are registered trademarks of Smart Software, Inc. All other trademarks are the property of their respective owners.
For more information, please contact Smart Software, Inc., Four Hill Road, Belmont, MA 02478.
Phone: 1-800-SMART-99 (800-762-7899); FAX: 1-617-489-2748; E-mail: info@smartcorp.com
Webinar: 10 Questions That Reveal Your Company’s True Inventory Policy
Do you know how your organization sets its inventory planning policies and the degree to which you actually apply them? And that they’re doing the job? Demand planning, forecasting, and inventory planning need to be well-defined processes that are understood and accepted by everybody involved. There should be zero mystery.
Please join our webinar featuring Greg Hartunian, CEO of Smart Software, who will review the top 10 questions you should ask to reveal your company’s true planning policy. Doing so will demystify your planning process and help you identify major opportunities for financial savings and process improvement.
We are offering this webinar due to the popularity of our blog
“Reveal your Real Inventory Planning and Forecasting Process by asking these 10 questions.” Greg will explain the importance of each question and describe how to interpret the variety of answers you will likely receive. Armed with this information, you’ll be able to document your process more clearly and identify opportunities for financial savings and process improvement. We will allow time for questions and answers and look forward to a robust discussion.
Please register to attend the webinar. If you are interested but not cannot attend, please register anyway – we will record our session and will send you a link to the replay.
We hope you will be able to join us!
SmartForecasts and Smart IP&O are registered trademarks of Smart Software, Inc. All other trademarks are the property of their respective owners.
For more information, please contact Smart Software, Inc., Four Hill Road, Belmont, MA 02478.
Phone: 1-800-SMART-99 (800-762-7899); FAX: 1-617-489-2748; E-mail: info@smartcorp.com