Improve Forecast Accuracy, Eliminate Excess Inventory, & Maximize Service Levels
In this Video Dr. Thomas Willemain, co–Founder and SVP Research, talks about forecast-based inventory management policy, also known as MRP logic. This is the fourth in our series on major approaches to managing inventory. We begin by looking at some very simple and then more robust models of inventory dynamics that help us determine how much to order or manufacture and when. We then consider how to calculate lead time and account for lead time variability. Tom concludes by describing the importance of safety stock, it’s role in properly buffering against demand and supply uncertainty, and how best to calculate it.
RECENT POSTS
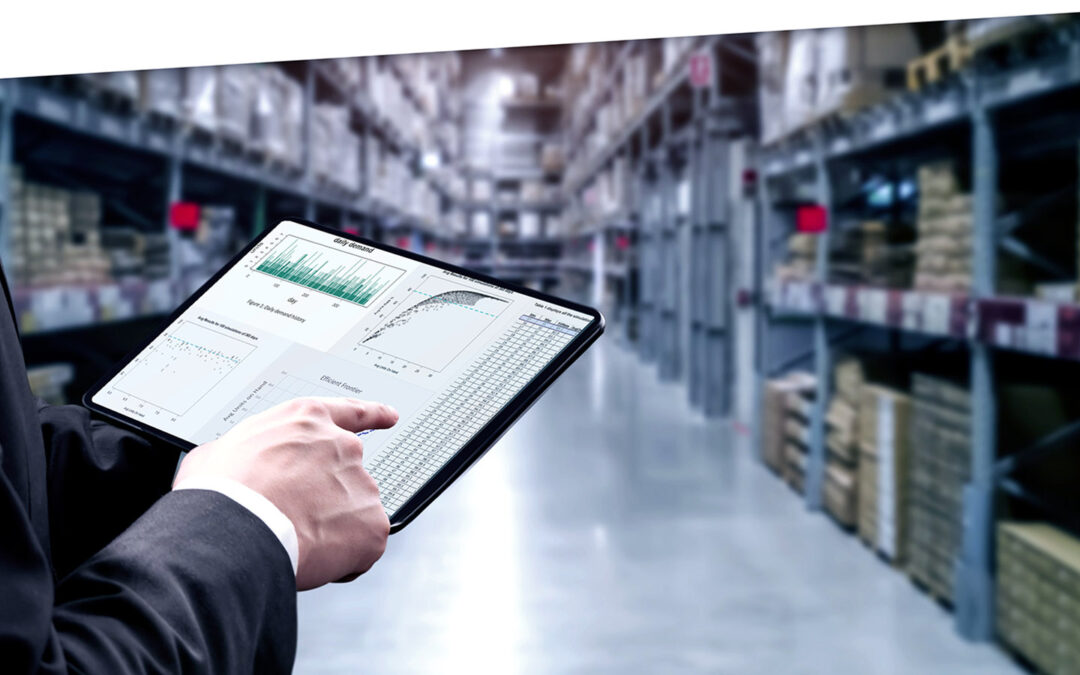
Are You Playing the Inventory Guessing Game?
Some companies invest in software to help them manage their inventory, whether it’s spare parts or finished goods. But a surprising number of others play the Inventory Guessing Game every day, trusting to an imagined “Golden Gut” or to plain luck to set their inventory control parameters. But what kind of results do you expect with that approach?
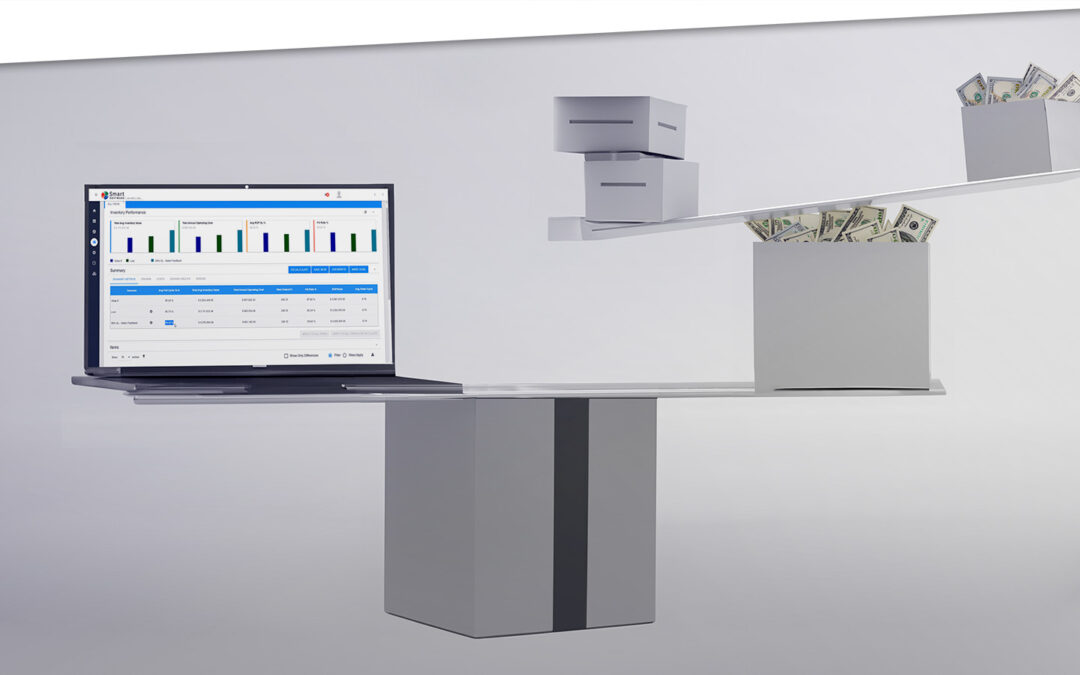
Finding Your Spot on the Tradeoff Curve
Managing inventory, like managing anything, involves balancing competing priorities. Do you want a lean inventory? Yes! Do you want to be able to say “It’s in stock” when a customer wants to buy something? Yes!
But can you have it both ways? Only to a degree. If you lean into leaning your inventory too aggressively, you risk stockouts. If you stamp out stockouts, you create inventory bloat. You are forced to find a satisfactory balance between the two competing goals of lean inventory and high item availability.
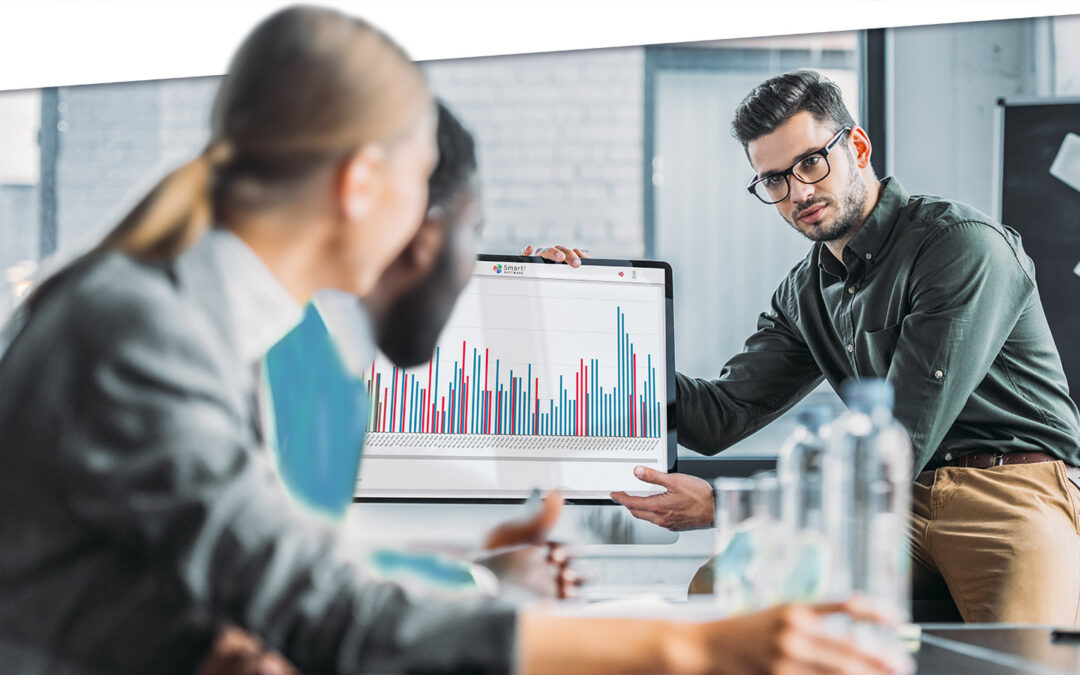
Direct to the Brain of the Boss – Inventory Analytics and Reporting
In this blog, the spotlight is cast on the software that creates reports for management, the silent hero that translates the beauty of furious calculations into actionable reports. Watch as the calculations, intricately guided by planners utilizing our software, seamlessly converge into Smart Operational Analytics (SOA) reports, dividing five key areas: inventory analysis, inventory performance, inventory trending, supplier performance, and demand anomalies.