Service Level Driven Planning (SLDP) is an approach to inventory planning. It prescribes optimal service level targets continually identifies and communicates trade-offs between service and cost that are at the root of all wise inventory decisions. When an organization understands this relationship, they can communicate where they are at risk, where they are not, and effectively wield their inventory assets. SLDP helps expose inventory imbalances and enables informed decisions on how best to correct them. To implement SLDP, you’ll need to look beyond traditional planning approaches such as arbitrary service level targeting (all of my A items should get 99% service level, B items 95%, C items 80%, etc.) and demand forecasting that unrealistically attempts to predict exactly what will happen and when. SLDP unfolds in 4 steps: Benchmark, Collaborate, Plan, and Track.
Step 1. Benchmark Performance
All participants in the inventory planning and investment process must hold a common understanding of how current policy is performing across an agreed upon set of inventory metrics. Metrics should include historically achieved service levels and fill rates, delivery time to customers, supplier lead time performance, inventory turns, and inventory investment. Once these metrics have been benchmarked and can be reported on daily, the organization will have the information it needs to begin prioritize planning efforts. For example, if inventory has increased but service levels have not, this would indicate that the inventory is not being properly allocated across SKUs. Reports should be generated within mouse-clicks enabling planners to focus on analysis instead of time intensive report generation. Past performance isn’t a guarantee of future performance since demand variability, costs, priorities, and lead times are always changing. So SLDP enables predictive benchmarking that estimates what performance is likely to be in the future. Inventory optimization software utilizing probability forecasting can be used to estimate a realistic range of potential demands and replenishment cycles stress testing your planning parameters helping uncover how often and which items to expect stockouts and excess.
Step 2. “What if” Planning & Collaboration
“What if” inventory modeling and collaboration is at the heart of SLDP. The historical and predictive benchmarks should first be shared with all relevant stakeholders including sales, finance, and operations. Efforts should be placed on answering the following questions:
– Are both the current performance and investment acceptable?
– If not, how should they be improved?
– Which SKUs are likely to be demanded next and in what quantities?
– Where are we willing to take more stock out risk?
– Where must stock-out risk be minimized?
– What are the specific stock out costs?
– What business rules and constraints must we adhere to (customer service level agreements, inventory thresholds, etc.)
Once the above questions are answered, new inventory planning policies can be developed. Inventory Optimization software can reconcile all costs associated with managing inventory including stockout costs to generate the right set of planning parameters (min/max, safety stock, reorder points, etc.) and prescribed service levels. The optimal policy can be compared to the current policy and modified based on constraints and business rules. For example, certain items might be targeted at a target service level in order to conform to a customer service level agreement. Various “what if” inventory planning scenarios can be developed and shared with key stakeholders. For example, you might model how shorter lead times impacts inventory costs. Once consensus has been achieved and the risks and costs are clearly communicated, the modified policies can be uploaded to the ERP system to drive inventory replenishment.
Step 3. Continually Plan and Manage by Exception
SLDP continually reforecasts optimized planning parameters based on changing demands, lead times, costs, and other factors. This means that service levels and inventory value have the potential to change. For example, the prescribed service level target of 95% might increase to 99% the next planning period if the stock-out costs on that item increased suddenly. This is also true if opting to arbitrarily target a given service level or fix planning parameters to a specific unit quantity. For example, a target service level of 95% might require $1,000 in inventory today but $2,000 next month if lead times spiked. Similarly, a reorder point of 10 units might get 95% service today and only 85% service next month in response to increased demand variability. Inventory Optimization software will identify which items are forecasted to have significant changes in service level and/or inventory value and which items aren’t being ordered according to the consensus plan. Exception lists are automatically produced making it easy for you to review these items and decide how to manage them moving forward. Prescriptive Analytics can help identify whether the root cause of the change is a demand anomaly, change in overall demand variability, change in lead time, or change in cost helping you fine tune the policy accordingly.
Step 4. Track Ongoing Performance
SLDP processes regularly measure historical and current operational performance. Results must be monitored to ensure that service levels are improving and inventory levels are decreasing when compared to the historical benchmarks determined in Step 1. Track metrics such as turns, aggregate and item specific service levels, fill rates, out-of-stocks, and supplier lead time performance. Share results across the organization and identify root causes to operational inefficiencies. SLDP processes makes performance tracking easy by providing tools that automatically generate the necessary reports rather than placing this burden on planners to manage in Excel. Doing so enables the organization to uncover operational issues impacting performance and provide feedback on what is working and what should be improved.
Conclusion
The SLDP framework is a way to rationalize the inventory planning process and generate a significant economic return. Its organizing principle is that customer service levels and inventory costs associated with the chosen policy should be understood, tracked, and continually refined. Utilizing inventory optimization software helps ensure that you are able to identify the least-cost service level. This creates a coherent, company-wide effort that combines visibility into current operations with scientific assessments of future risks and conditions. It is realized by a combination of executive vision, staff subject matter expertise, and the power of modern inventory planning and optimization software.
See how Smart Inventory Optimization Supports Service Level Driven Planning and download the product sheet here: https://smartcorp.com/inventory-optimization/
Related Posts
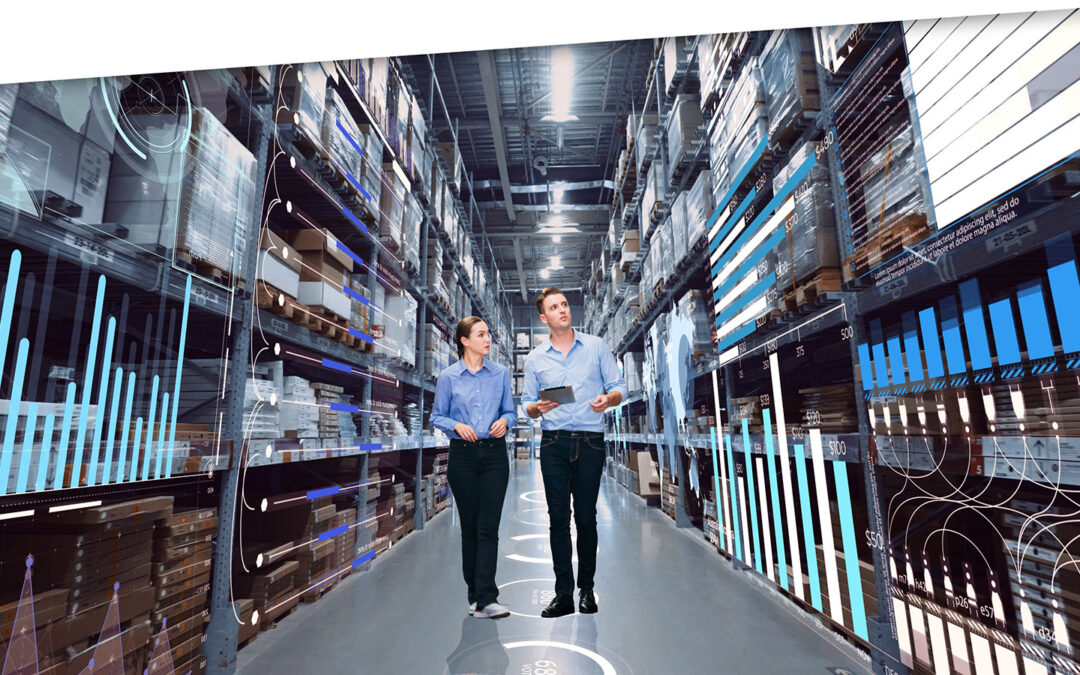
Make AI-Driven Inventory Optimization an Ally for Your Organization
In this blog, we will explore how organizations can achieve exceptional efficiency and accuracy with AI-driven inventory optimization. Traditional inventory management methods often fall short due to their reactive nature and reliance on manual processes. Maintaining optimal inventory levels is fundamental for meeting customer demand while minimizing costs. The introduction of AI-driven inventory optimization can significantly reduce the burden of manual processes, providing relief to supply chain managers from tedious tasks.
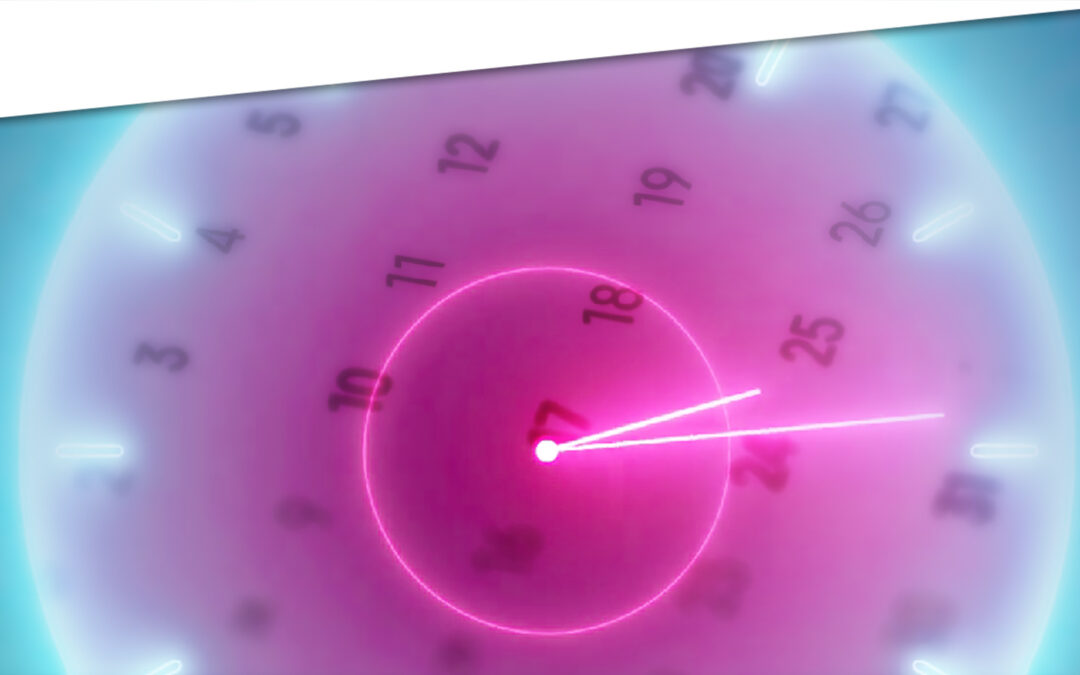
Daily Demand Scenarios
In this Videoblog, we will explain how time series forecasting has emerged as a pivotal tool, particularly at the daily level, which Smart Software has been pioneering since its inception over forty years ago. The evolution of business practices from annual to more refined temporal increments like monthly and now daily data analysis illustrates a significant shift in operational strategies.
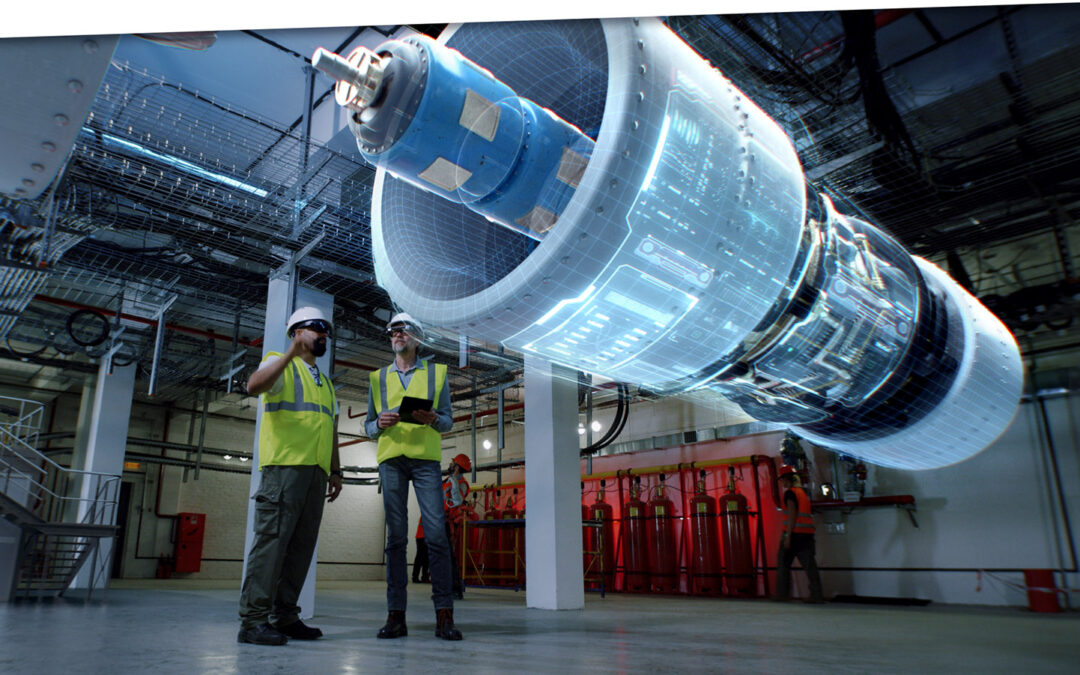
Constructive Play with Digital Twins
Those of you who track hot topics will be familiar with the term “digital twin.” Those who have been too busy with work may want to read on and catch up. While there are several definitions of digital twin, here’s one that works well: A digital twin is a dynamic virtual copy of a physical asset, process, system, or environment that looks like and behaves identically to its real-world counterpart. A digital twin ingests data and replicates processes so you can predict possible performance outcomes and issues that the real-world product might undergo.