Service Parts Planning Problem
Service parts and spare parts have intermittent demand patterns that make them all but impossible to forecast with traditional forecasting methods. Up to 90% of spare parts have intermittent demand – also known as lumpy or “anything but normally distributed” demand. The result is widely inaccurate estimates of demand forecasts, reorder points, and safety stock estimates that cause stockouts and inventory excess. Compounding the problem is an unpredictable repair and return cycles for repairable service parts & equipment that must regularly rotate in and out of service. Planners don’t know whether to buy more spares or wait for out-of-service spares to be repaired and returned to service. It’s a guessing game that wastes millions annually in unneeded capital investments and weeks to months of avoidable equipment downtime.
Service Parts Planning Solution
Smart Inventory Optimization (SIO™) uses a unique empirical probabilistic forecasting approach that is engineered for planning intermittent demand commonly observed with spare parts and service parts. Our patented and APICS award-winning method rapidly generates tens of thousands of possible scenarios of future demand sequences without relying on the assumptions commonly made about the nature of service parts demand distributions by traditional forecasting methods. The result is a highly accurate estimate of safety stock, reorder points, and service levels, leading to higher service levels and lower inventory costs. Smart’s Repair and Return module accurately simulate the inflow and outflow of repairable spare parts. It predicts downtime, service levels, and inventory costs associated with the current rotating service parts spare pool. Planners will know whether to wait for repairs to be completed or to purchase additional service spares from suppliers avoiding unnecessary buying and equipment downtime.
White Paper: What you Need to know about Forecasting and Planning Service Parts
This paper describes Smart Software’s patented methodology for forecasting demand, safety stocks, and reorder points on items such as service parts and components with intermittent demand, and provides several examples of customer success.
Intermittent Demand Problem
Some product items have an intermittent demand pattern that makes them all but impossible to forecast with traditional, smoothing-based forecasting methods. Items with intermittent demand – also known as lumpy, volatile, variable or unpredictable demand – have many zero or low volume values interspersed with random spikes of demand that are often many times larger than the average. This problem is especially prevalent in companies that manage large inventories of service and spare parts in industries such as aviation, aerospace, automotive, high tech, and electronics, as well as in MRO (Maintenance, Repair and Overhaul).
Intermittent demand
In these businesses, as much as 80% of the parts and product items may have intermittent or lumpy demand. Intermittent demand makes it difficult to accurately estimate the safety stock and service level inventory requirements needed for successful supply chain planning. Because forecasts of intermittent and lumpy demand have been so unreliable, most companies forecast inventory requirements relying primarily on subjective business knowledge, forecast only a fraction of their higher volume inventory, use simple “rule of thumb” estimates, or traditional statistical forecasting that incorrectly assumes a particular type demand distribution for inventory control. The result is that billions of dollars are wasted every year because of either excess inventory costs or poor customer service due to stock-outs.
Intermittent demand – also known as lumpy, volatile, variable or unpredictable demand.
The Smart Solution
SmartForecasts and Smart Inventory Optimization use a unique empirical probabilistic forecasting approach that results in accurate forecasts of inventory requirements where demand is intermittent. The solution works particularly well whenever demand does not conform to a simple normal distribution. Our patented, APICS award-winning “bootstrapping” technology rapidly generates tens of thousands of possible scenarios of future demand sequences and cumulative demand values over an item’s lead time. These scenarios are statistically similar to the item’s observed data, and they capture the relevant details of intermittent demand without relying on the assumptions commonly made about the nature of demand distributions by traditional forecasting methods. The result is a highly accurate forecast of the entire distribution of cumulative demand over an item’s full lead time. With the information these demand distributions provide, you can easily plan your company’s safety stock and service level inventory requirements for thousands of intermittently demanded items with nearly 100% accuracy.
The Benefits
Companies using our powerful intermittent demand forecasting and planning solution typically reduce standing inventory by 20% in the first year, increase parts availability 10-20%, and reduce the need for and associated costs of emergency transshipment to close gaps in their supply chain. Repair and service parts inventories are truly optimized, leading to more efficient operations, improvements in customer service, and significantly less cash tied up in inventory.
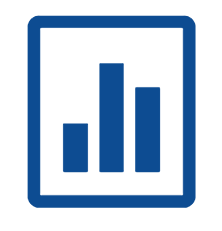
Optimal Inventory Levels
Reduce excess stock
Improve service levels
Minimize buyer transactions
Maximize return on assets

Organizational Consensus
Balance service levels
Identify stockout risk
Identify overstocks
No finger-pointing
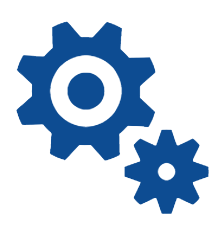
Operational Connectivity
Align process with strategic objectives
Empower team to “make it so”
Optimize as conditions change
Pass results to ERP
Who is Inventory Optimization for?
Smart Inventory Optimization is for executives and business savvy planners who seek to:
- Yield maximum returns from inventory assets.
- Address the problem of highly variable or intermittent demand.
- Broker the service vs. cost tradeoffs between different departments.
- Develop a repeatable and efficient inventory planning process.
- Empower the team to ensure operational plan is aligned with strategic plan.
What questions can Inventory Optimization answer?
- What is the best service level achievable with the inventory budget?
- What service levels will yield the maximum return?
- If lead times increased, what would it cost to maintain service?
- If I reduce inventory, what will the impact on service be?
- If order quantity increases, what will the impact on service and costs be?
- What is the order quantity that balances holding and ordering costs?
Inventory forecasting for the inventory executive
Smart Inventory Optimization empowers you to:
- Predict service performance and inventory costs.
- Assess business impact of “what-if” inventory policies.
- Align inventory policy with corporate strategy.
- Establish an operational framework that guides the planning team.
- Reduce inventory and improve service.