Optimizing Parts Management at BC Transit
Introduction
BC Transit’s vision statement is to be Your Best Transportation Solution. BC Transit accomplishes this by transporting 57 million annual passenger trips in over 130 communities across British Columbia. Transit is becoming a key part of the solution for many of the complex challenges that communities face across the province, such as climate change, affordability and congestion, and as a result transit service is expanding quickly (9 per cent growth in the past five years). Delivery of this service in a safe and timely manner is paramount. BC Transit’s fleet of 1,185 buses require regular maintenance and rapid repairs to ensure they are as effective and efficient as possible. Having the right part in the right place at the right time is essential. Eric Nelson, Director of Supply Services, discussed the challenges of meeting this responsibility and how their use of Smart Software technology is helping make BC Transit the best transportation solution.
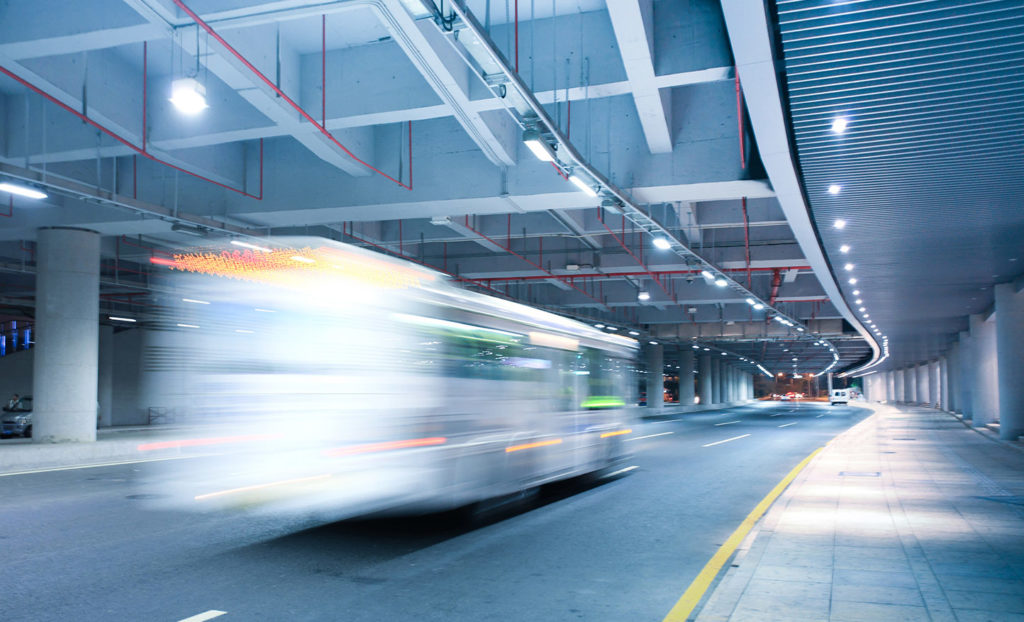
The Challenge:
BC Transit was preparing to centralize warehouse operations around a new central distribution center, just as the organization was preparing to upgrade to a new version of its JD Edwards Enterprise Resource Planning (ERP) system. They needed to determine the right stocking levels to serve the entire BC Transit network with 35 active branch plants under an aggressive timeline. In a matter of weeks, the transition would begin to their new ERP and wholesale system updates would be barred.
This was no small matter as BC Transit manages 30,000 discrete skus. Space in the new consolidated Provincial Distribution Centre would be at a premium, and parts planning was a highly manual, qualitative process. Reorder points were set manually, based on weekly requisitions and the buyers’ knowledge and judgement. The move to the new CDC model would require setting optimal reorder points for all stocked parts. The existing process would not be able to do this – there were just too many parts.
Compounding the challenge was the highly intermittent nature of BC Transit parts demand. Rather than following a routine, easily forecastable pattern, service parts often experience highly sporadic, seemingly random demand. Qualitative methods and intuition would not ensure the 95% service level that BC Transit required. The organization needed a better solution.
The Solution:
BC Transit turned to Smart Software. Nelson was aware of Smart’s work with other transit systems and was drawn to Smart Inventory Planning & Optimization for a number of reasons:
- Service level-driven planning methodology with probabilistic modeling, enabling ‘what if’ scenario development. and cost vs. performance trade-offs;
- Proven ability to plan for intermittent demand, demonstrated across multiple transit customers;
- Cloud-based suite of web applications, providing anywhere access and eliminating the need for IT infrastructure; and
- Automated data integration and analytics, providing the continuous flow of data from and the return of optimal Min/Max drivers to JD Edwards to drive replenishment.
Smart and BC Transit worked through an accelerated implementation process to get their initial system up and running within two months. BC Transit was able to establish stocking policies to get the new warehouse and central distribution system up and running. Once initial policies were set, they used the first year of operations to monitor and refine reorder points.
“The big change,” says Nelson, “was to shift from the qualitative, manual establishment of reorder points to a highly automated system of setting Min/Max values for all active parts.”
Year 1 focused on getting the process working and relating the new capabilities to overall supply chain operations. The experience established confidence in the system. Their enhanced planning process now treats new items manually until they experience three incidents of demand. At that point the demanded parts transition into production planning and are included in the routine, monthly automated process. Plans are now underway to push Min/Max planning out to the 28 regional transportation systems and all 35 stocking locations.
Results:
“We could not have consolidated central distribution into one facility without Smart,” says Nelson. “During the transition we discovered a need for 3,000 additional SKUs. There just wouldn’t have been room. It is difficult to put a monetary value on this.”
Using Smart IP&O, BC Transit was able to internalize the impact of centralizing all external shipments. They were able to consolidate demand for all regional transit systems and foresee required stocking levels. Nelson added, “we did not see any instance of incorrect forecasts. And we were able to set policies effectively for parts with exceptionally sparse demand.”
BC Transit values its newfound ability to forecast the financial impact of stocking decisions. They are able to balance capacity against criticality and the cost of inventory. They have been able to reduce the number of orders, determine optimal order quantities, and deal with variability of lead time – especially long lead times. “Smart IP&O has enabled us to utilize service level as a driving KPI, essentially risk adjusting our inventory to address the criticality of not running out, and to deal with the thorny challenges of seasonal and intermittent demand. It is helping us keep our buses on the road, so we can be the best transportation solution for our partners across British Columbia.”
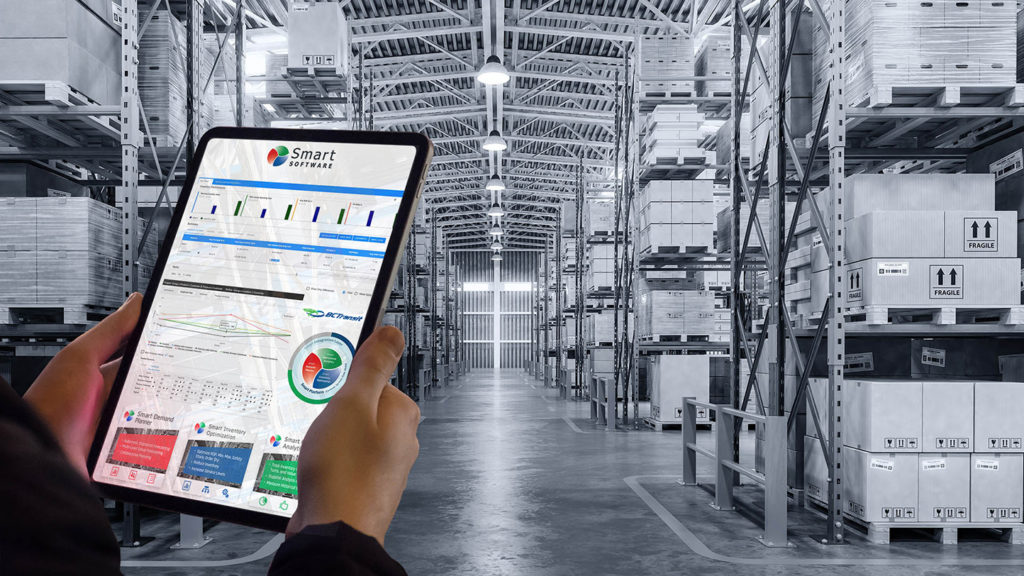
Draped in Success – Inventory Planning at Rose Brand
Introduction
Rose Brand is North America’s largest provider of theatrical fabrics, fabrications and production supplies for the entertainment, event and display industries. If you’ve been to a play or musical, you’ve probably seen their products. Product availability is crucial to the company’s success, and the company strives to achieve same day shipping from its east and west coast distribution centers. This is a tall order when offering thousands of discrete items. Doug Harvey, Director of Operations, sat down with us to explain how Rose Brand delivers, and how Smart Software helps.
The Challenge:
“Having the product in stock is everything,” explains Harvey. “Rose Brand customers know what they want and usually want it now. If a requested item is not in stock, there is a good chance Rose Brand will lose that order and several more, and the customer may not come back.” The array of products is wide and complex – over 10,000 skus, many offered in 5, 10, even 30 colors. And it’s gotten more complex. The company recently acquired a manufacturer of curtain tracks and motors. Lots more parts.
Accelerating growth strained a procurement process that relied heavily on buyers’ domain knowledge and gut feel. Many of their stocked items experience highly sporadic, intermittent demand that staff were ill-equipped to plan. Determining when to order was based on rudimentary spreadsheet models that required extensive manual adjustment, so much so that most items – particularly the thousands of slow movers – were not actively planned. The lack of a methodical planning process, combined with the criticality that they not stock out, resulted in overstocks, stockouts, and strained limited warehouse space.
The Solution:
Rose Brand selected demand and inventory planning software from Smart Software as the foundation for a methodical planning process. This enabled them to effectively implement Min/Max inventory planning, setting optimal Minimum On-Hand values and order quantities. Two capabilities in particular made a big difference. First, the ability to conduct service level-driven planning made it possible to risk adjust inventory. Some critical items cannot be allowed to stock out, and so are be run at very high service levels. A 1% risk of stocking out might be acceptable. Others that are less critical can tolerate lower service levels. This risk adjustment of inventory, and achieving required service levels, reduces inventory and improves service levels.
Second, the software included Smart’s unique methodology for planning intermittent demand. This method, invented and patented by Smart, probabilistically models lead time demand and establishes the requisite Min or reorder point corresponding to the desired service level. Items with this sort of demand profile can now be effectively planned. Way better than knee-jerk or wild guess adjustments to random stockouts.
In addition to providing effective inventory policy drivers, SmartForecasts enabled staff to consider and model what-if scenarios. For example, Rose Brand purchases 1.5 containers from a vendor every 4 weeks. If their supplier could deliver in 3 weeks, how much inventory – and warehouse space – would that save? Half a container. A lot.
Results:
Rose Brand reduced inventory at the outset, and as its business grew, managed slow inventory growth as sales increased 50%. A crucial factor in that growth has been the company’s ability to respond to customers’ increasing insistence on immediate availability. SmartForecasts has enabled the company to effectively plan all of its thousands of stocked products, and has provided the planning framework for the company’s growing infrastructure. This included the addition of its West Coast warehouse, and the inclusion of a newly acquired division in 2018.
“Rose Brand has undergone tremendous change and growth since its founding in 1921,” says Harvey. “Smart Software has brought capabilities that help us meet accelerating demand and expectations, and we look forward to pushing this envelope together in coming years.”
Caught in a Perfect Storm, SmartForecasts Helps Rev-A-Shelf Weather the Crisis
The Smart Forecaster
Pursuing best practices in demand planning, forecasting and inventory optimization
Does your extended supply chain suffer from extreme seasonal variability? Does this situation challenge your ability to meet service level commitments to your customers? I have grappled with this at Rev-A-Shelf, addressing unusual conditions created by Chinese New Year and other global events, and would like to share the experience and a few things I learned along the way.
First, let me explain our situation. We import 60% of the parts we use to build our kitchen and bath accessories from China and Europe. Most of the year we were able to plan our inventory needs using a spreadsheet-based min/max approach. But not during Chinese New Year, which drives the planet’s greatest annual population migration. Chinese New Year shuts down production for up to two months, creating significant supply risk as we strive to meet our three day order fulfillment commitment.
We solved our problem, introducing statistical demand forecasting with the flexibility to extend lead times when necessary, the ability to reliably establish safety stocks that achieve our required service levels and a continuous reporting system that lets everyone know exactly where we stand. However, success required much more than a new piece of software. We needed to change the way we view future demand, supply risk and safety stock. Here are a few key things we did that made all the difference.
Stakeholder education and buy-in
Regardless of the project, it’s always best to enlist the buy-in of all stakeholders. We knew we had to do something to solve our problem, but there was bound to be resistance. Senior managers, for example, had developed a healthy distrust of software and wondered whether demand forecasting software could help. Our buyers had developed their own perspectives and procurement methods, and felt personally at risk as we considered new approaches.
People came around as they developed a common understanding of the problem and how we would address it. Education was a big part of the solution. We explained how forecasting works and key factors we should all understand: how to analyze trends, how to use “what if” scenarios, impact of shifting lead times, how to relate service levels to supply risk and safety stock and key performance indicators like inventory turns. Going through this process together, we all became stakeholders in the solution.
Use the Right software
When you have lots of part numbers and any sort of supply or demand variability, you just cannot forecast effectively with a spreadsheet. With our min/max forecasting system, we were planning to an average, and it wasn’t working. Average usage has inherent flaws for planning purposes—it’s always looking backward!
You need software that looks ahead, recognizes seasonal patterns and enables you to determine how much stock you’ll need to meet required service levels over varying lead times.
Fine-tune processes
When the old ways don’t work, you need to be open to adjusting your assumptions. Think less about where you’ve been, and more about where you want to be. Take a look at your lead times and plan to your desired service level. Last year’s history may not be the best predictor of this year’s demand. The same forecast horizon may not be appropriate for all products or certain time of the year.
Make the Forecast Actionable
It’s not enough to produce an accurate forecast and estimated inventory stocking levels. You’ve got to develop a way to make the information actionable for those tasked with using it. We developed a set of reports that enabled buyers to leverage better forecast and safety stock information. Now, at the end of every month, we produce a forecast report that provides a clear picture of current inventory, safety stock, past usage, forecasted usage, incoming deliveries (PO’s) and recommended order quantities.
Validate Results
You can, and we did, test our new methods against our own demand history. Still, an authoritative outsider can make acceptance easier. We commissioned a study by a professor at Louisville University’s College of Business who set one of her graduate students to the task. Through them we were able to reinforce what we saw happening from our results, and feel comfortable that we were on a good path.
All of these factors helped Rev-A-Shelf transform its demand planning process, to great effect. Today we are exceeding our service level targets, and our fill rate, based on a three day ship cycle, is showing steady improvement, and trending up. Overall, units-in-stock have stayed flat while supporting a 13% increase in sales
John Engelhardt is currently Director of Purchasing and Asian Operations for Rev-a-Shelf, LLC in Louisville, KY. He has held a variety of management positions both in private business and public organizations. At Rev-A-Shelf he held the position of International Sales Manager and Director of Sales Support before assuming his current position. He can be reached at johne at rev-a-shelf dot com.

The aftermarket sector provides OEMs with a decisive advantage by offering a steady revenue stream and fostering customer loyalty through the reliable and timely delivery of service parts. However, managing inventory and forecasting demand in the aftermarket is fraught with challenges, including unpredictable demand patterns, vast product ranges, and the necessity for quick turnarounds. Traditional methods often fall short due to the complexity and variability of demand in the aftermarket. The latest technologies can analyze large datasets to predict future demand more accurately and optimize inventory levels, leading to better service and lower costs.
Forecast-based inventory management, or MRP (Material Requirements Planning) logic, is a forward-planning method that helps businesses meet demand without overstocking or understocking. By anticipating demand and adjusting inventory levels, it maintains a balance between meeting customer needs and minimizing excess inventory costs. This approach optimizes operations, reduces waste, and enhances customer satisfaction.
In this blog, we will explore how organizations can achieve exceptional efficiency and accuracy with AI-driven inventory optimization. Traditional inventory management methods often fall short due to their reactive nature and reliance on manual processes. Maintaining optimal inventory levels is fundamental for meeting customer demand while minimizing costs. The introduction of AI-driven inventory optimization can significantly reduce the burden of manual processes, providing relief to supply chain managers from tedious tasks.
Forum Energy Streamlines Demand Planning, Improves Market Responsiveness with SmartForecasts
Forum Energy Technologies is a $1.7 billion global oilfield products company, serving the oil and natural gas industry. With over 3,500 employees, Forum is headquartered in Houston, TX and has manufacturing and distribution facilities strategically located around the globe. Forum’s Valve Solutions Division in Stafford, Texas, uses SmartForecasts in combination with its Epicor ERP system for planning at the finished goods and component levels.
The Challenge
Forum faced a complex demand planning challenge. Its business, highly cyclical and sensitive to market changes, required a responsive planning process. This was complicated by the fact that the majority of its stocked items exhibit sporadic, seemingly unforecastable intermittent demand. This is characterized by many zero or low volume values interspersed with random spikes that are often many times larger than average demand.
Forum relied upon a cumbersome excel-based forecasting process that generated estimates of average demand but did not provide guidance on appropriate levels of stock. Determining stock levels was mostly guesswork, based on intuition. The large number of items and lack of effective tools resulted in an inefficient planning process where only a small portion of items could be reviewed on a regular basis. It was not unusual for items to be forecast once per quarter.
Given six to ten month lead times for imported items and a cyclical business climate, Forum needed to forecast more frequently in order to react faster to changing market conditions. This would require a data-driven solution that could determine appropriate stock levels to reduce stockout risk while keeping inventory at an affordable level.
The Solution
Forum Energy purchased SmartForecasts for its abilities to automatically apply appropriate forecasting methodologies to specific items, handle intermittent demand, and interface with its Epicor ERP.
SmartForecasts enabled Forum to make several changes to the way it managed its inventory:
• automate forecasting, increasing efficiency to the extent that planners could forecast products on a monthly basis and have the time and ability to review exceptions;
• forecast at both the finished goods and component levels, using SmartForecasts intermittent demand forecasting for all components;
• perform a meaningful S&OP process spanning supply chain management and sales; and,
• model different inventory policy and service level scenarios to better allocate inventory investment and react more quickly to market changes.
The Results
Like other companies in the oil and gas industry, Forum has experienced a slowdown in its business. SmartForecasts enabled Forum to quickly adjust its inventories by running what-if scenarios and evaluating the risks involved with different actions. While it has only recently started to use Smart’s “Service Level Demand Planning” methodology, according to Rod Cardenas, purchasing manager, “the service level planning method has led to productive conversations between sales and supply chain and given us a platform or common ground from which we base our discussions.”
Forum now does intermittent demand forecasting for all of its components. That capability has been an important factor in increasing confidence in forecasting results. According to Cardenas, “SmartForecasts gives us good information to work with. People are feeling comfortable with numbers, and through our S&OP process we’ve been able to create buy-in across the company.”
Over four years Forum experienced revenue growth of 15-20% per year, and was able to do so without increasing inventory. Using SmartForecasts it has also been able to increase inventory turns from 1.8 times to an estimated 3.0 times this year.
Recently Forum began a vendor-managed inventory (VMI) program for its fasteners. SmartForecasts is being used to help vendors manage their bin sizes. Shifting inventory risk to its vendors, Forum has been able to reduce in-house inventory from 700,000 units to 100,000, and is expected that it will be able to turn its in-house inventory 12 times.
“We’re just scratching the surface of taking advantage of SmartForecasts’ capabilities, added Cardenas. “There’s a lot more we can do.”Smart Software ( SmartForecasts®) Helps Metro-North Railroad Keep the Trains Running On-Time
Introduction
Metro-North Railroad (MNR) is part of the New York Metropolitan Transit Authority, and services commuters and other travelers in the New York metropolitan area. It’s the second largest commuter railroad in the U.S. serving 300,000 passengers each weekday, while operating 1,266 engines and rail cars over 775 miles of track.
The Material Management division is charged with stocking spare parts inventory. It maintains 37,500 parts valued at $107 million. More than 80% of its inventory has extremely volatile and hard-to-forecast intermittent demand.
Challenge: Safety Stock for Long-Lived Assets
MNR’s prime objective is to move people in a timely manner. For service outages, it must have the right items in stock to fix the problem.
Service level is MNR’s most important key performance indicator. At the beginning, it found itself with too much expensive inventory sitting idle and an unacceptably low 95.8% service level.
To remedy this situation, Material Management needed to be able to analyze all of MNR’s inventory, including items with intermittent demand, and then optimize them while simultaneously increasing service levels. MNR did not have appropriate planning tools to do the job.
MNR also faced several other challenges: ridership was increasing, and the agency was expanding its fleets, retiring old trains, and introducing new ones. With a five-year planning horizon, MNR needed to maintain adequate safety stock for an asset service life of 20 years or more, and replacement lead times, for some parts, of more than a year.
Solution: SmartForecasts
After a thorough evaluation process, MNR selected Smart Software’s SmartForecasts®. Smart’s solution uses patented bootstrapping technology that accurately forecasts intermittent demand. It also provides inventory managers with accurate estimates of the optimal inventory and safety stock required to meet future orders and achieve desired service levels.
MNR realized a payback after only 9 months. SmartForecasts was used to identify overstocked items, many of which had pending orders. By putting holds on some orders, and canceling others, MNR realized immediate improvements in cash flows. Management was also able to identify items at risk of stocking out and re-deployed resources that buoyed immediate service level improvements.
Results:Accurate Intermittent Demand Forecasts
MNR’s multi-year project continues to provide improving results. Recently, some of the company’s notable successes and approaches for utilizing SmartForecasts, were cited in Material Management’s yearly report to its Board of Directors on previous year operations:
- Parts Inventory to support its equipment has declined 8% from $128 million.
- In the second year, following a continuing trend, customer service levels reached a record high 98.7%. This was accomplished with a new fleet growth of over 2%
- SmartForecasts was instrumental in reducing inventory growth for new equipment from a projected 10% to only 6%.
- MNR uses SmartForecasts to identify multi-year service part needs for long-term contracts. By contracting with suppliers on a multi-year agreements, administrative lead times were greatly reduced. This enabled further reductions in stock without compromising service.
- Smart Forecast was critical in the formulation of a stock reduction plan for MNR’s retiring fleet, and helped identify inventory retirement reserves, enabling MNR to maximize disposal benefits and warehouse bin space reclamation.
- MNR identified $1.6 million in inactive inventory for final disposal, and provided availability of excess parts to Long Island Railroad, thus potentially minimizing additional MTA inventory investments.

According to Rich Price, Chief Material Officer at MNR, “SmartForecasts does the job. It’s the only solution out there I’m aware of that has really licked the intermittent demand modeling challenge. It gives us accurate information and more importantly at the lowest dollar. That’s the bottom line we’re really interested in. Without SmartForecasts, I think we would have seen a continued growth in our inventory and not necessarily gotten any greater benefit for service.”
SmartForecasts helps Vicor Increases Service Levels 10 Percentage Points and Reduces Inventory 20 Percent
Vicor Corporation, a publicly traded, $200 million company with headquarters in Andover, Massachusetts, is a build-to-order manufacturer of power conversion products for the electronics OEM market. Vicor produces 30,000 product items grouped into fifteen product families. The items are made from 10-15,000 components. As a build-to-order manufacturer, Vicor does both assembly and fabrication. It also tries to run a lean operation, keeping a very low backlog of finished good items and only ordering component parts on an as-needed basis. This strategy tends to lower inventory costs but also heightens the company’s risk of stocking out of key items.
The Challenge
While a few hundred of Vicor’s products are sold on a regular basis, some are ordered as little as every two years-a factor that makes demand forecasting and inventory planning more difficult. Yet Vicor’s business success depends critically on having the right component in stock when it’s needed to make a product item. So, having an accurate forecasting process in place is a major contributor to the company’s smooth operations.
As CIO of Vicor Corporation, Doug Richardson was charged with helping the company achieve two strategic objectives: improve on-time delivery of the company’s products and reduce inventory levels.
The Solution
Starting in 1999, Richardson led a team that replaced Vicor’s old manufacturing systems and a homegrown forecasting system with the PeopleSoft ERP system and SmartForecasts Enterprise. In May 2002, Vicor completed a tight integration of SmartForecasts with PeopleSoft’s Production Planning module, and by July 2002, the company started seeing positive results. Mark Vernaglia, senior operations planner at Vicor, makes the point that the ability to interactively adjust the statistical forecast results and understand seasonality were two big selling points in SmartForecasts’ favor.
Vicor has a two-phase demand forecasting process that combines both sales force and statistical forecasting techniques. In the first phase, the sales force obtains judgmental predictions directly from Vicor’s largest customers regarding their demand for each of the company’s product items. These customers account for about 40 to 50 percent of Vicor’s shipment volume. In the second phase, the shipment history for these customers is excluded, and SmartForecasts’ Automatic Forecasting capabilities are used to forecast statistically the product demand expected from all of the other customers. By summing these two sets of results, Vicor generates the total production forecast for each product item.
Because Vicor needs to assign future revenue goals for its product families as part of its sales and operations planning (S&OP), the company also makes use of SmartForecasts’ top-down modeling capabilities. It uses SmartForecasts to impose the build plan for each family and to intelligently distribute that goal among the items in the family.
The Results
In less than a year following integration with the PeopleSoft system, SmartForecasts uncovered a critical upward trend in Vicor’s business. “At first we thought something was wrong,” stated Richardson. So Vicor did the forecast again with more demand history as input. Sure enough, SmartForecasts had spotted a trend that began in late 2001.
“The SmartForecasts results provided evidence that the post-9/11 business downturn had hit bottom,” Richardson continued. “If SmartForecasts hadn’t uncovered the upward trend, we wouldn’t have had enough inventory on hand to meet demand.”
The system has continued to deliver substantial results that put the company well on the road to achieving its strategic objectives. According to Richardson, on-time delivery performance (customer service level) has increased by 10 percentage points and, at the same time, inventories are down by 20 percent. The improvements are the results of hard work by a team focused on improving order fulfillment, a key element of which is the company’s ability to better forecast inventory needs and understand demand patterns with SmartForecasts Enterprise.
The forecasting process has been greatly enhanced since the integration of SmartForecasts Enterprise with Vicor’s PeopleSoft system. Before the implementation, Vicor only forecasted about twenty percent of its products, in part because the old homegrown forecasting system was cumbersome to use and didn’t have the necessary horsepower or data capacity. Because of the speed of SmartForecasts and its ease of use, the company can now forecast more than eighty percent of its items. The ability to forecast more products has been a big factor in reducing Vicor’s inventory requirements and improving service levels.
Mark Vernaglia feels very comfortable using SmartForecasts and claims that he was able to be proficient with little training. “We’re getting great results,” stated Vernaglia, “and I haven’t even started taxing the software’s capabilities.”
The results have made Vernaglia more confident in his job. “With SmartForecasts we’ve been able to be much more aggressive with our inventory planning,” he continued. “You’ve got to have confidence in your forecast, and we now have the confidence to stock certain component parts that we didn’t have before.”
In the future, Vernaglia plans to expand the forecasting process to the component level and to start using SmartForecasts’ patented intermittent demand forecasting capabilities. He’s confident that these unique capabilities will help Vicor improve its ability to set stocking levels appropriately for slow-moving items.
Vicor looks forward to continuing improvements. “I’m willing to bet that our numbers will continue to go in opposite directions-inventory down and service levels up,” wagered Vernaglia. These are the kinds of changes that continue to help Vicor’s management achieve its strategic goals.