What is to blame for having too much of the stuff you don’t need and not enough of the stuff you do need? Demand and supply variability are often blamed. These problems are significant and seems impossible to overcome leaving many organizations to simply accept misallocated stock as a cost of doing business. However, the real problem it isn’t simply late supplier deliveries and unpredictable demand. These are supply chain planning “facts of life” and it’s how your company addresses them that counts. Watch Greg Hartunian’s vlog to hear his thoughts and what you can do about it.
Smart Inventory Planning and Optimization automatically calculates the stocking policy that yields the best return for your business considering holding costs, ordering costs, and stock outs. To see it in action, register below to watch a 12 minute demonstration.
Related Posts
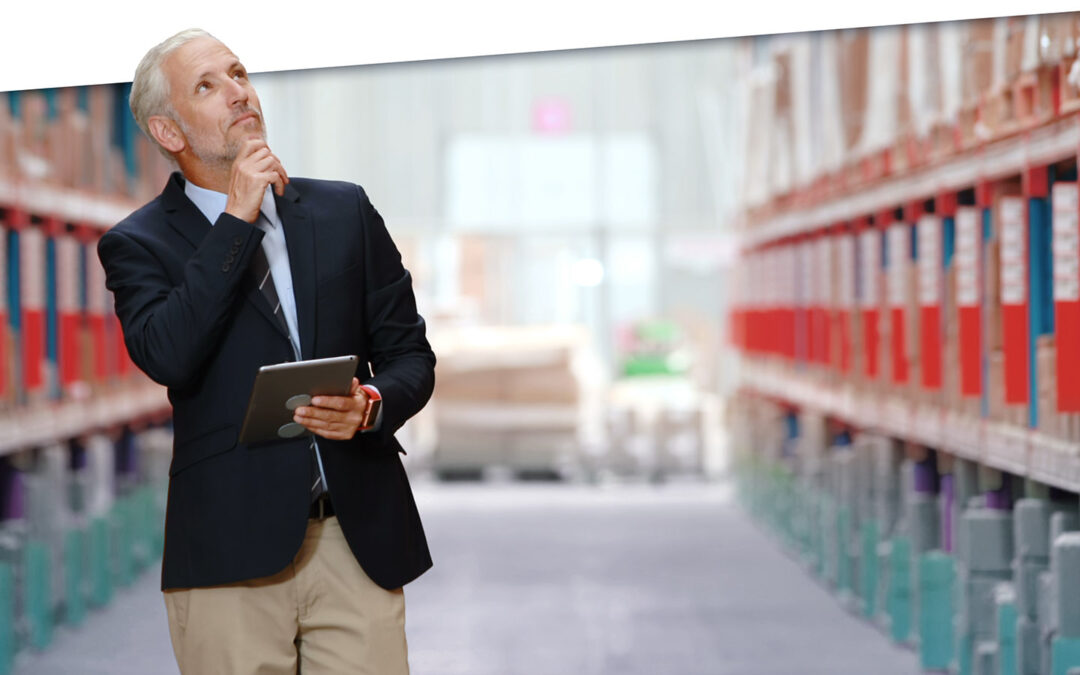
Why Inventory Planning Shouldn’t Rely Exclusively on Simple Rules of Thumb
For too many companies, a critical piece of data fact-finding ― the measurement of demand uncertainty ― is handled by simple but inaccurate rules of thumb. For example, demand planners will often compute safety stock by a user-defined multiple of the forecast or historical average. Or they may configure their ERP to order more when on hand inventory gets to 2 x the average demand over the lead time for important items and 1.5 x for less important ones. This is a huge mistake with costly consequences.
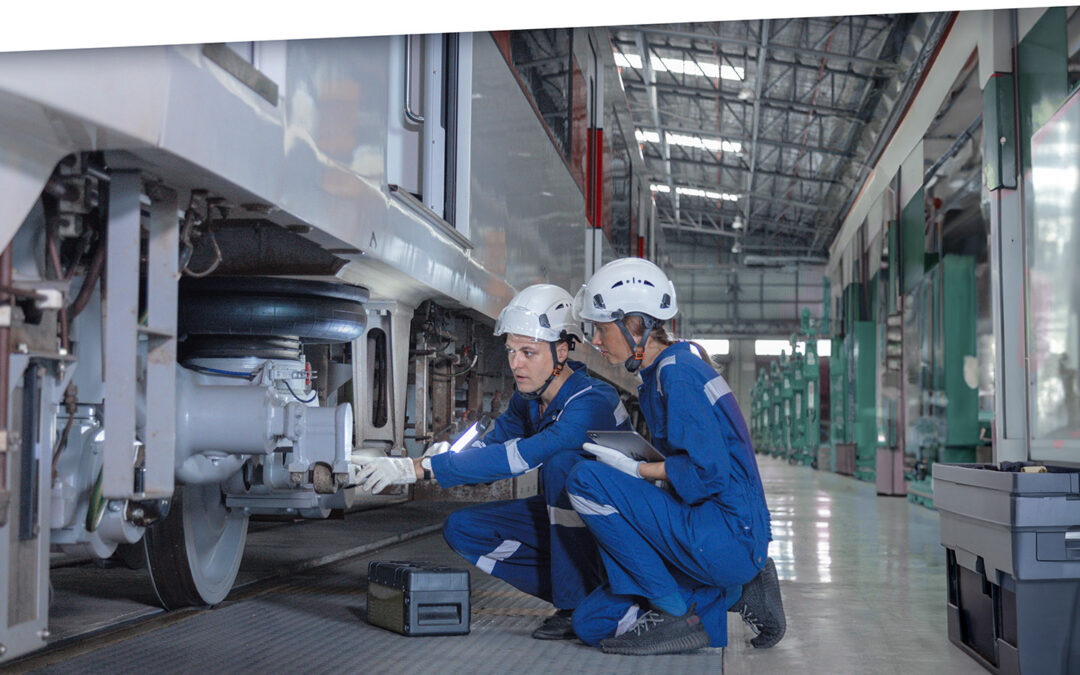
Why MRO Businesses Should Care About Excess Inventory
Do MRO companies genuinely prioritize reducing excess spare parts inventory? From an organizational standpoint, our experience suggests not necessarily. Boardroom discussions typically revolve around expanding fleets, acquiring new customers, meeting service level agreements (SLAs), modernizing infrastructure, and maximizing uptime. In industries where assets supported by spare parts cost hundreds of millions or generate significant revenue (e.g., mining or oil & gas), the value of the inventory just doesn’t raise any eyebrows, and organizations tend to overlook massive amounts of excessive inventory.
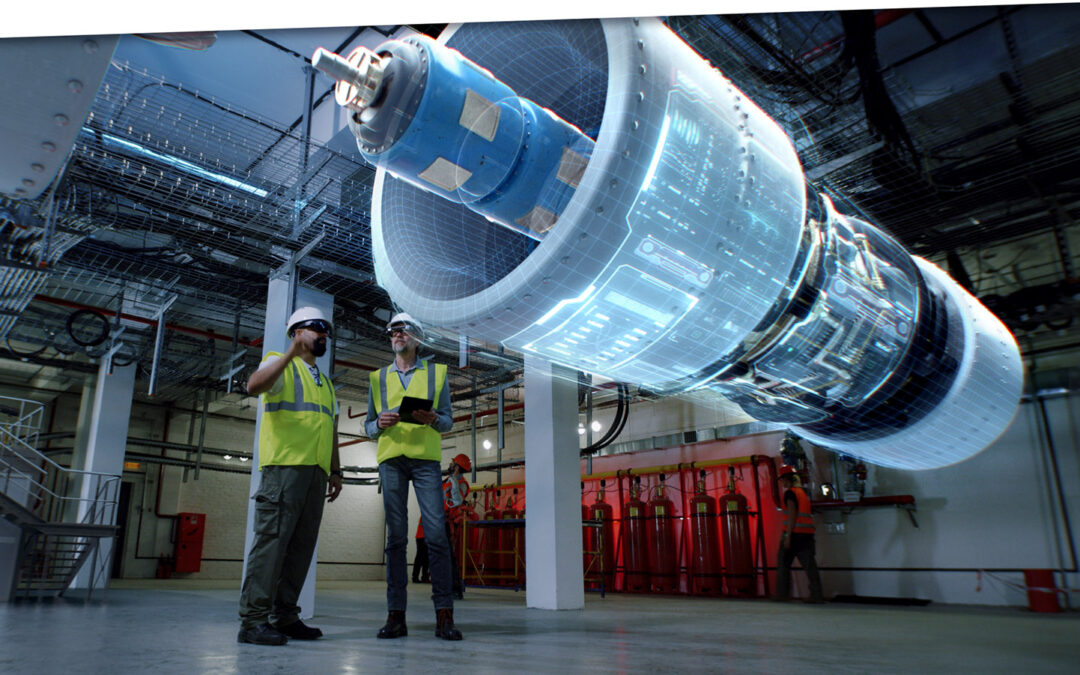
Constructive Play with Digital Twins
Those of you who track hot topics will be familiar with the term “digital twin.” Those who have been too busy with work may want to read on and catch up. While there are several definitions of digital twin, here’s one that works well: A digital twin is a dynamic virtual copy of a physical asset, process, system, or environment that looks like and behaves identically to its real-world counterpart. A digital twin ingests data and replicates processes so you can predict possible performance outcomes and issues that the real-world product might undergo.