Problem
Poor part availability erodes the reputation of MRO based businesses through unplanned downtime, scheduled maintenance delays, and violations of contracted SLAs. Having the right parts at exactly the right time eliminates these risks. However, that ideal is nearly impossible to achieve because of the prevalence of intermittent demand. Traditional planning solutions don’t effectively address intermittency, resulting in widely inaccurate estimates of demand forecasts, reorder points, and safety stock. Compounding the problem are extremely long supplier lead times on consumable parts and unpredictable repair/return cycles for expensive repairable parts. All this uncertainty causes planning to devolve into a reactive and manual guessing game. This wastes tens of millions annually in unneeded parts purchasing, expedites, countless hours of avoidable equipment downtime, and lost revenue.
Solution
The Smart IP&O software suite includes mission critical forecasting, supply planning, and inventory optimization solutions coupled with accelerator add-ons designed to address the unique challenges facing MRO and Aftermarket Spare Parts businesses. The inventory optimization workbench drives what if scenarios leveraging Smart’s patented probabilistic forecasting that yields optimal Min/Max and safety stock recommendations. Smart’s Repair and Return functionality accurately simulates the inflow and outflow of expensive repairable spare parts recommending if planners should wait for repairs to be completed or to purchase additional spares from suppliers. Capital budgeting and project-based planning nets accurate order schedules by reconciling available supply with planned and unplanned demand to ensure the parts are purchased when needed.
White Paper: What you Need to know about Forecasting and Planning Spare Parts
This paper describes Smart Software’s patented methodology for forecasting demand, safety stocks, and reorder points on items such as spare parts and components with intermittent demand, and provides several examples of customer success.
Smart Spare Parts Planning and Inventory Optimization
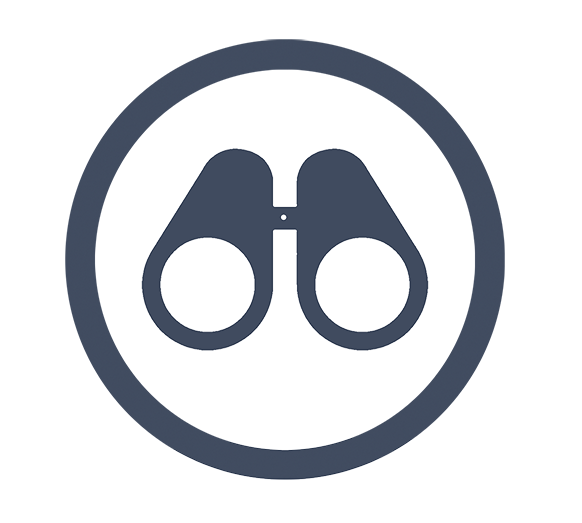
Predict Service Levels
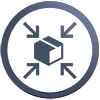
Optimize Reorder Points
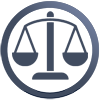
Balance Network Inventory
Intermittent Demand Problem
Some product items have an intermittent demand pattern that makes them all but impossible to forecast with traditional, smoothing-based forecasting methods. Items with intermittent demand – also known as lumpy, volatile, variable or unpredictable demand – have many zero or low volume values interspersed with random spikes of demand that are often many times larger than the average. This problem is especially prevalent in companies that manage large inventories of service and spare parts in industries such as aviation, aerospace, automotive, high tech, and electronics, as well as in MRO (Maintenance, Repair and Overhaul).
Intermittent demand
In these businesses, as much as 80% of the parts and product items may have intermittent or lumpy demand. Intermittent demand makes it difficult to accurately estimate the safety stock and service level inventory requirements needed for successful supply chain planning. Because forecasts of intermittent and lumpy demand have been so unreliable, most companies forecast inventory requirements relying primarily on subjective business knowledge, forecast only a fraction of their higher volume inventory, use simple “rule of thumb” estimates, or traditional statistical forecasting that incorrectly assumes a particular type demand distribution for inventory control. The result is that billions of dollars are wasted every year because of either excess inventory costs or poor customer service due to stock-outs.
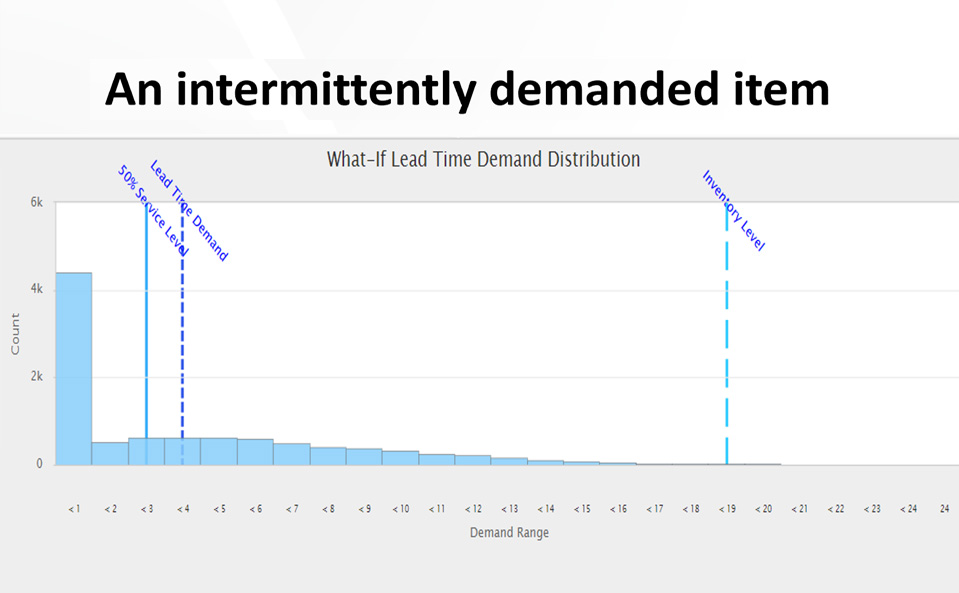
Intermittent demand – also known as lumpy, volatile, variable or unpredictable demand.
The Smart Solution
SmartForecasts and Smart Inventory Optimization use a unique empirical probabilistic forecasting approach that results in accurate forecasts of inventory requirements where demand is intermittent. The solution works particularly well whenever demand does not conform to a simple normal distribution. Our patented, APICS award-winning “bootstrapping” technology rapidly generates tens of thousands of possible scenarios of future demand sequences and cumulative demand values over an item’s lead time. These scenarios are statistically similar to the item’s observed data, and they capture the relevant details of intermittent demand without relying on the assumptions commonly made about the nature of demand distributions by traditional forecasting methods. The result is a highly accurate forecast of the entire distribution of cumulative demand over an item’s full lead time. With the information these demand distributions provide, you can easily plan your company’s safety stock and service level inventory requirements for thousands of intermittently demanded items with nearly 100% accuracy.
The Benefits
Companies using our powerful intermittent demand forecasting and planning solution typically reduce standing inventory by 20% in the first year, increase parts availability 10-20%, and reduce the need for and associated costs of emergency transshipment to close gaps in their supply chain. Repair and service parts inventories are truly optimized, leading to more efficient operations, improvements in customer service, and significantly less cash tied up in inventory.
Who is Inventory Optimization for?
Smart Inventory Optimization is for executives and business savvy planners who seek to:
- Yield maximum returns from inventory assets.
- Address the problem of highly variable or intermittent demand.
- Broker the service vs. cost tradeoffs between different departments.
- Develop a repeatable and efficient inventory planning process.
- Empower the team to ensure operational plan is aligned with strategic plan.
What questions can Inventory Optimization answer?
- What is the best service level achievable with the inventory budget?
- What service levels will yield the maximum return?
- If lead times increased, what would it cost to maintain service?
- If I reduce inventory, what will the impact on service be?
- If order quantity increases, what will the impact on service and costs be?
- What is the order quantity that balances holding and ordering costs?
Inventory forecasting for the inventory executive
Smart Inventory Optimization empowers you to:
- Predict service performance and inventory costs.
- Assess business impact of “what-if” inventory policies.
- Align inventory policy with corporate strategy.
- Establish an operational framework that guides the planning team.
- Reduce inventory and improve service.