Managing spare parts presents numerous challenges, such as unexpected breakdowns, changing schedules, and inconsistent demand patterns. Traditional forecasting methods and manual approaches are ineffective in dealing with these complexities. To overcome these challenges, this blog outlines key strategies that prioritize service levels, utilize probabilistic methods to calculate reorder points, regularly adjust stocking policies, and implement a dedicated planning process to avoid excessive inventory. Explore these strategies to optimize spare parts inventory and improve operational efficiency.
Bottom Line Upfront
1.Inventory Management is Risk Management.
2.Can’t manage risk well or at scale with subjective planning – Need to know service vs. cost.
3.It’s not supply & demand variability that are the problem – it’s how you handle it.
4.Spare parts have intermittent demand so traditional methods don’t work.
5.Rule of thumb approaches don’t account for demand variability and misallocate stock.
6.Use Service Level Driven Planning (service vs. cost tradeoffs) to drive stock decisions.
7.Probabilistic approaches such as bootstrapping yield accurate estimates of reorder points.
8.Classify parts and assign service level targets by class.
9.Recalibrate often – thousands of parts have old, stale reorder points.
10.Repairable parts require special treatment.
Do Focus on the Real Root Causes
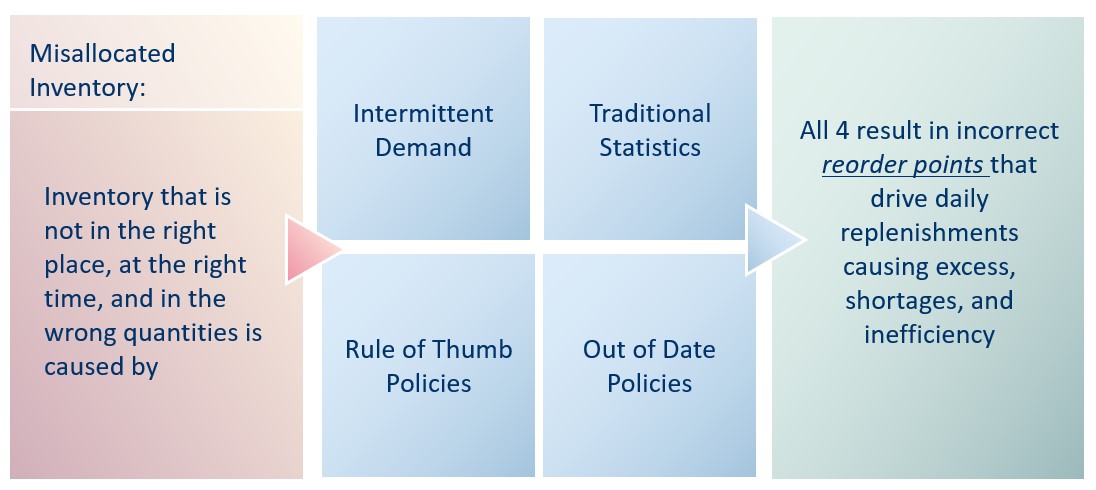
Intermittent Demand

- Slow moving, irregular or sporadic with a large percentage of zero values.
- Non-zero values are mixed in randomly – spikes are large and varied.
- Isn’t bell shaped (demand is not Normally distributed around the average.)
- At least 70% of a typical Utility’s parts are intermittently demanded.
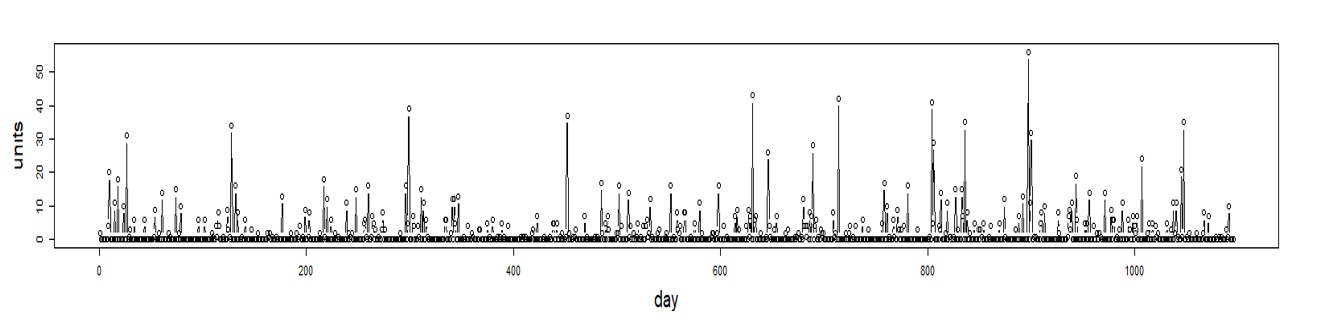
Normal Demand

- Very few periods of zero demand (exception is seasonal parts.)
- Often exhibits trend, seasonal, or cyclical patterns.
- Lower levels of demand variability.
- Is bell-shaped (demand is Normally distributed around the average.)
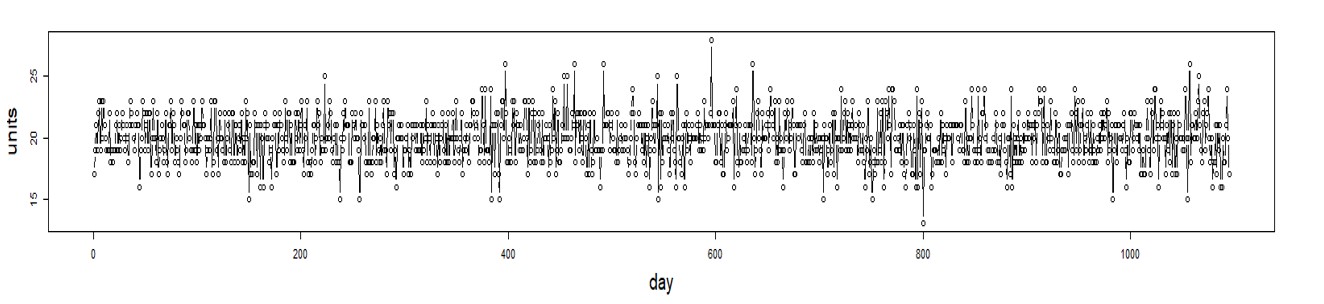
Don’t rely on averages
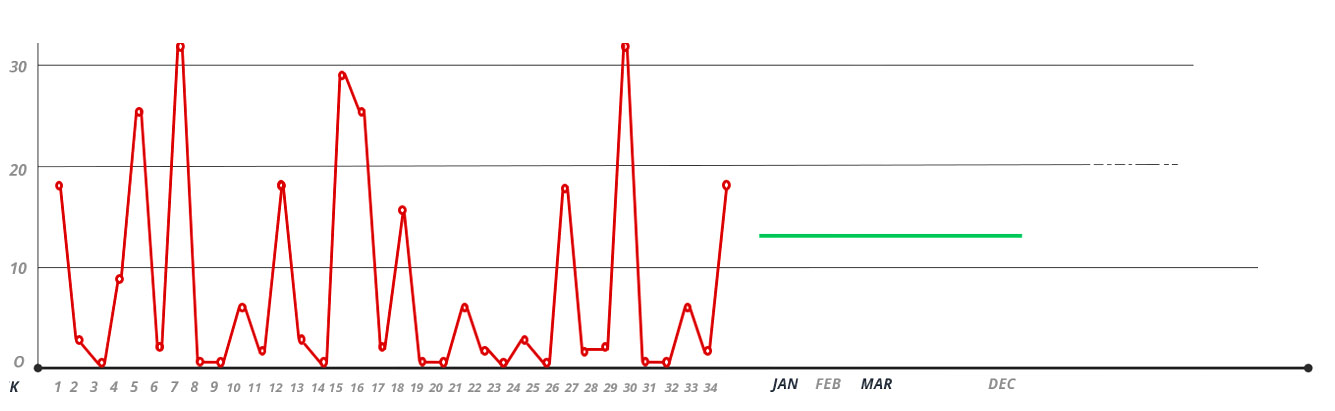
- OK for determining typical usage over longer periods of time.
- Often forecasts more “accurately” than some advanced methods.
- But…insufficient for determining what to stock.
Don’t Buffer with Multiples of Averages
Example: Two equally important parts so let’s treat them the same.
We’ll order more when On Hand Inventory ≤ 2 x Avg Lead Time Demand.
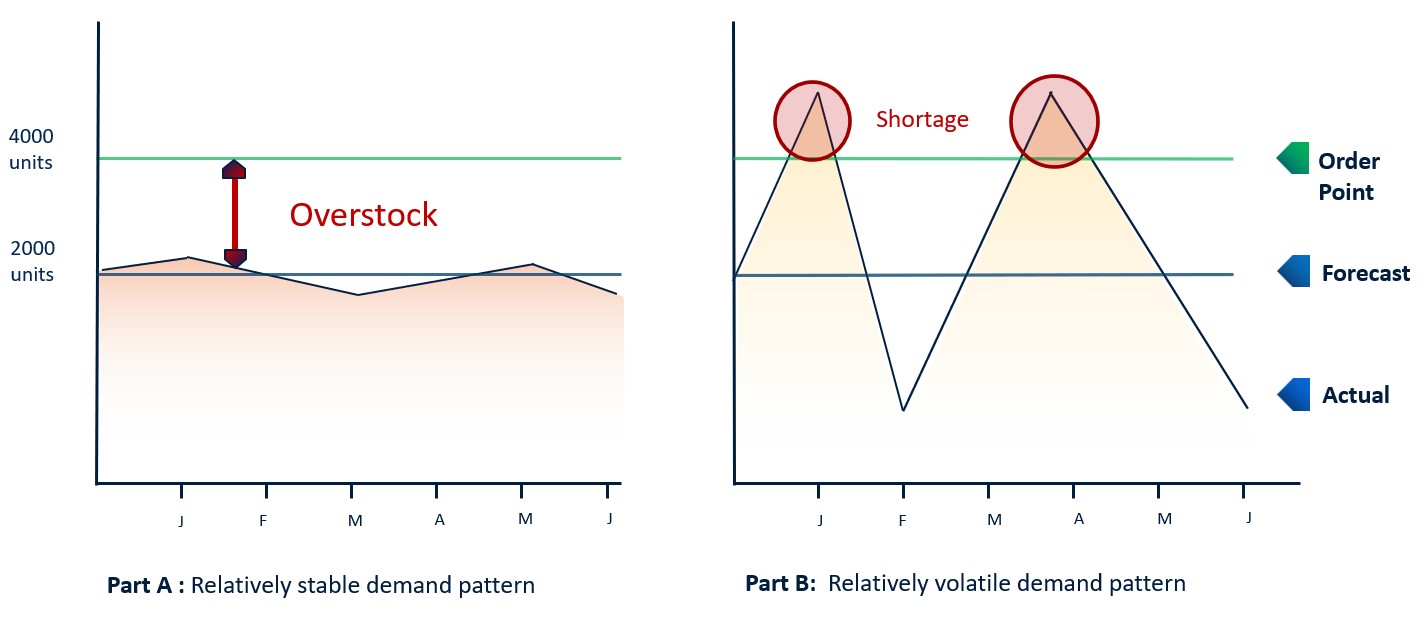
Do use Service Level tradeoff curves to compute safety stock
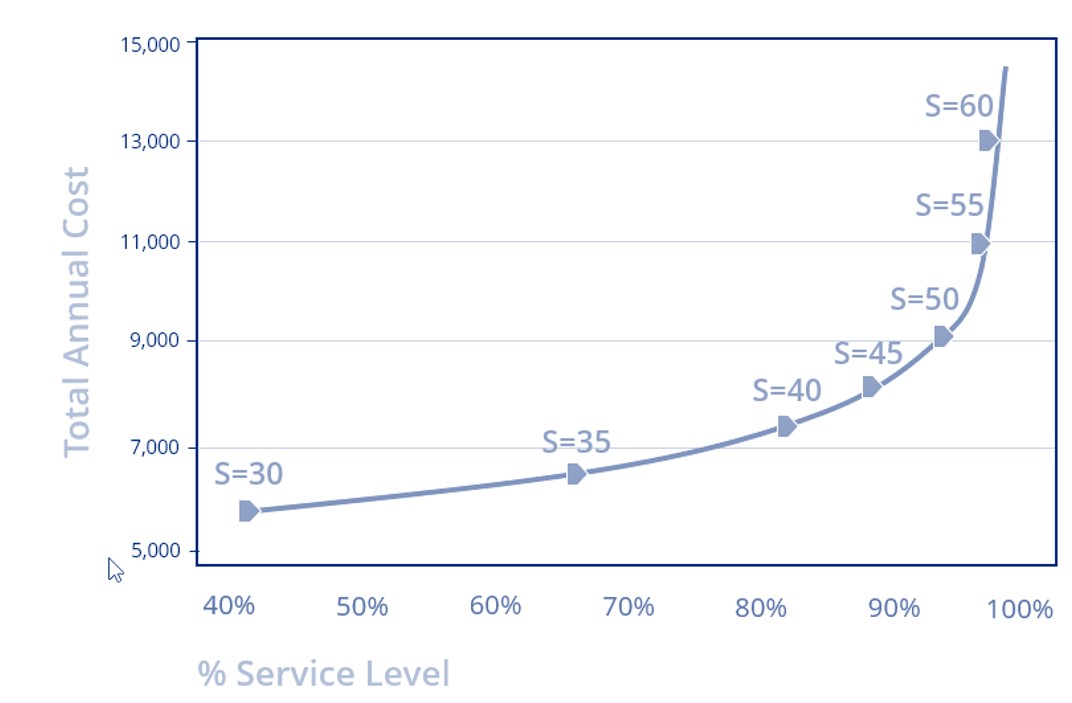
Standard Normal Probabilities
OK for normal demand. Doesn’t work with intermittent demand!
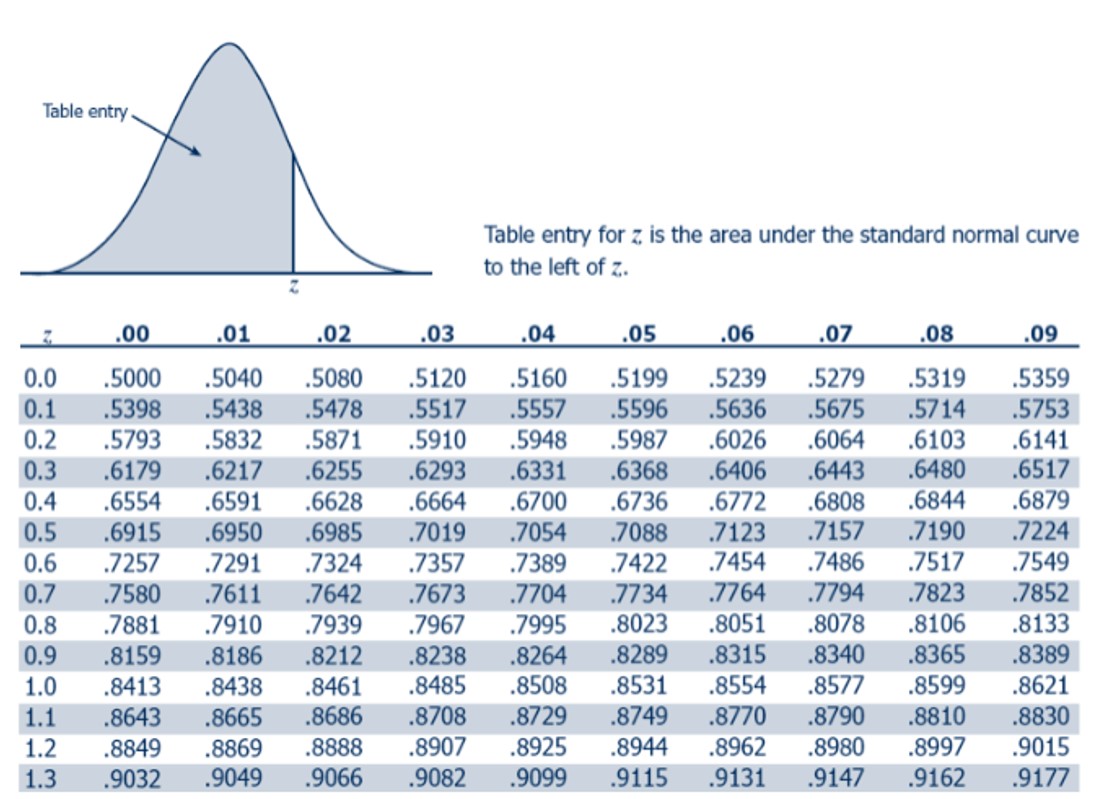
Don’t use Normal (Bell Shaped) Distributions
- You’ll get the tradeoff curve wrong:
– e.g., You’ll target 95% but achieve 85%.
– e.g., You’ll target 99% but achieve 91%.
- This is a huge miss with costly implications:
– You’ll stock out more often than expected.
– You’ll start to add subjective buffers to compensate and then overstock.
– Lack of trust/second-guessing of outputs paralyzes planning.
Why Traditional Methods Fail on Intermittent Demand:
Traditional Methods are not designed to address core issues in spare parts management.
Need: Probability distribution (not bell-shaped) of demand over variable lead time.
- Get: Prediction of average demand in each month, not a total over lead time.
- Get: Bolted-on model of variability, usually the Normal model, usually wrong.
Need: Exposure of tradeoffs between item availability and cost of inventory.
- Get: None of this; instead, get a lot of inconsistent, ad-hoc decisions.
Do use Statistical Bootstrapping to Predict the Distribution:
Then exploit the distribution to optimize stocking policies.
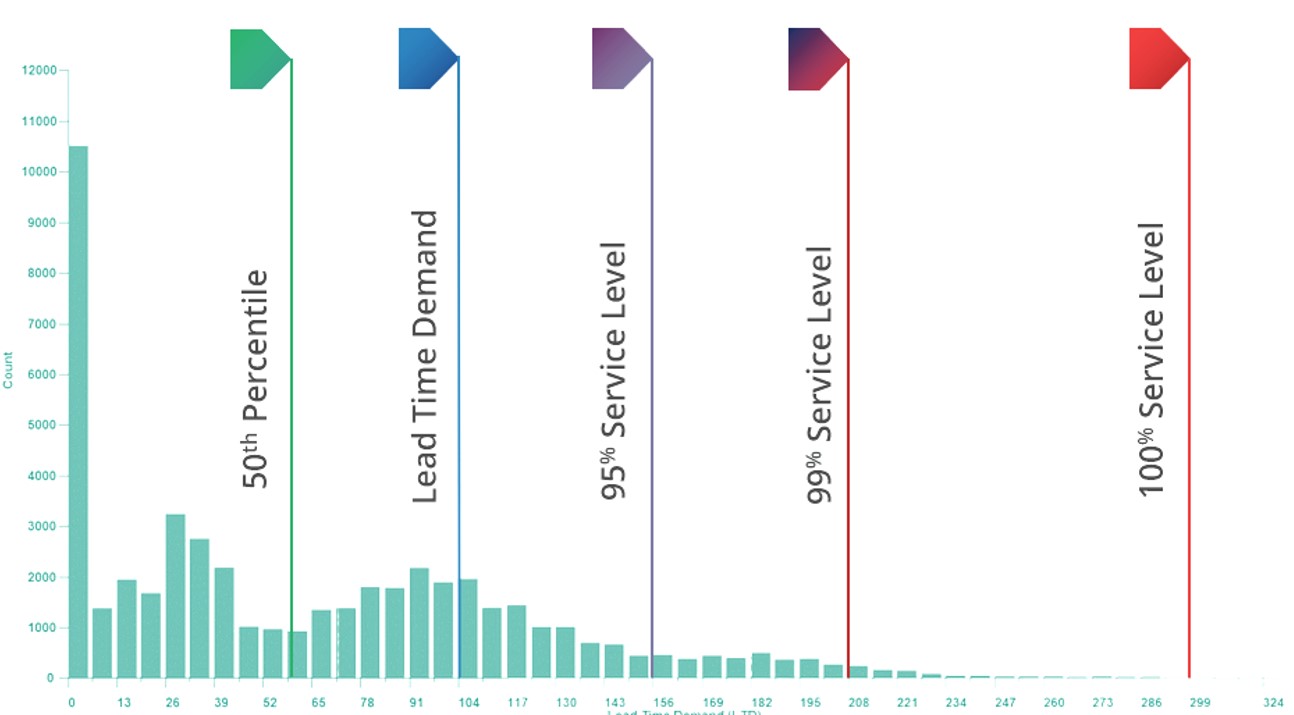
How does Bootstrapping Work?
24 Months of Historical Demand Data.

Bootstrap Scenarios for a 3-month Lead Time.
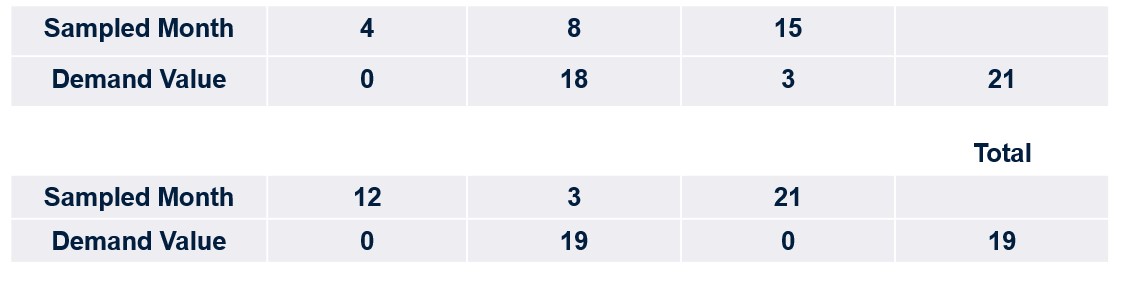
Bootstrapping Hits the Service Level Target with nearly 100% Accuracy!
- National Warehousing Operation.
Task: Forecast inventory stocking levels for 12,000 intermittently demanded SKUs at 95% & 99% service levels
Results:
At 95% service level, 95.23% did not stock out.
At 99% service level, 98.66% did not stock out.
This means you can rely on output to set expectations and confidently make targeted stock adjustments that lower inventory and increase service.
Set Target Service Levels According to Order Frequency & Size
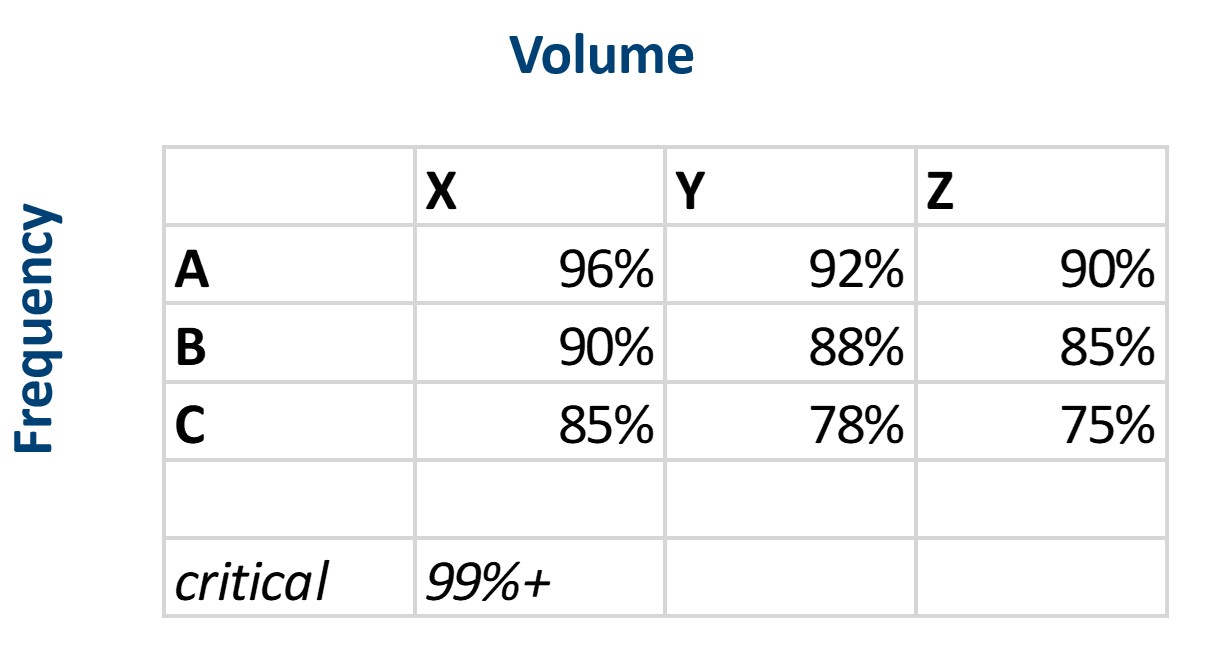
Recalibrate Reorder Points Frequently
- Static ROPs cause excess and shortages.
- As lead time increases, so should the ROP and vice versa.
- As usage decreases, so should the ROP and vice versa.
- Longer you wait to recalibrate, the greater the imbalance.
- Mountains of parts ordered too soon or too late.
- Wastes buyers’ time placing the wrong orders.
- Breeds distrust in systems and forces data silos.
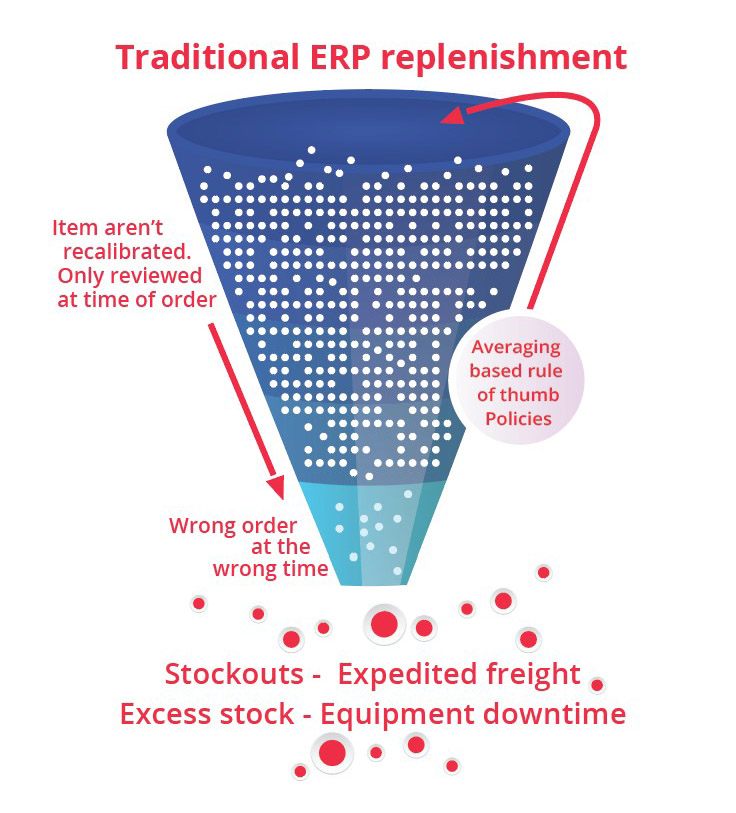
Do Plan Rotables (Repair Parts) Differently
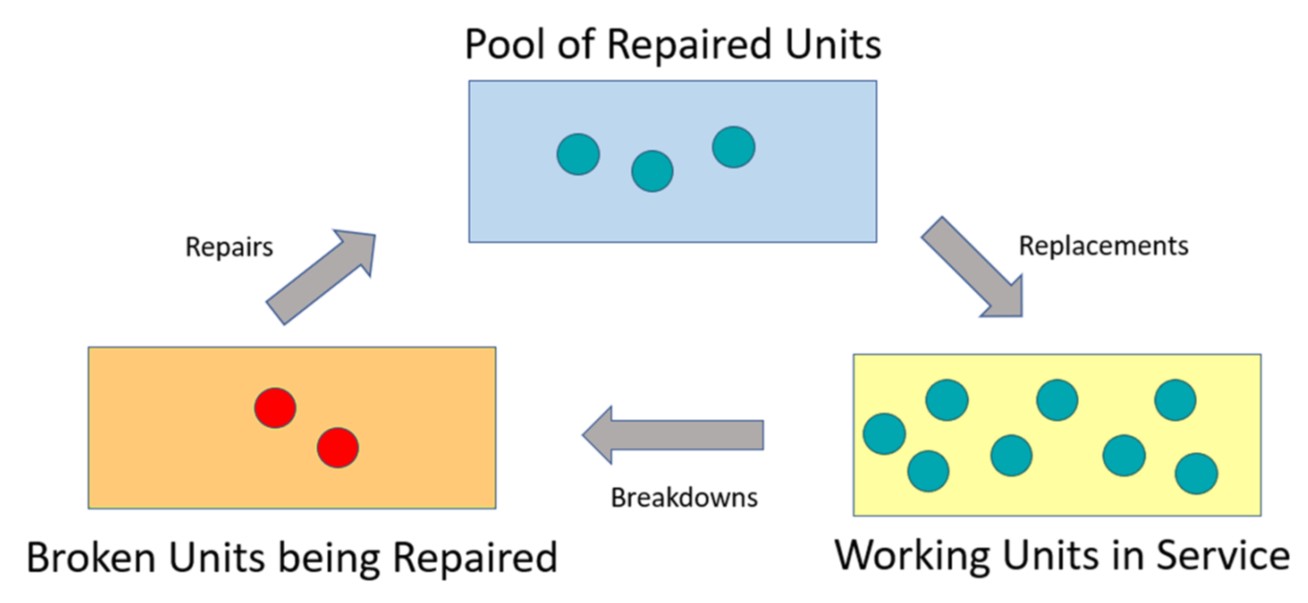
Summary
1.Inventory Management is Risk Management.
2.Can’t manage risk well or at scale with subjective planning – Need to know service vs. cost.
3.It’s not supply & demand variability that are the problem – it’s how you handle it.
4.Spare parts have intermittent demand so traditional methods don’t work.
5.Rule of thumb approaches don’t account demand variability and misallocate stock.
6.Use Service Level Driven Planning (service vs. cost tradeoffs) to drive stock decisions.
7.Probabilistic approaches such as bootstrapping yield accurate estimates of reorder points.
8.Classify parts and assign service level targets by class.
9.Recalibrate often – thousands of parts have old, stale reorder points.
10.Repairable parts require special treatment.