MAX-MIN O ROP – ROQ
por Philip Slater
El autor de este blog invitado es Philip Slater, fundador de SparePartsKNowHow.com, el principal recurso educativo para la gestión de piezas de repuesto. El Sr. Slater es un líder mundial y consultor en gestión de materiales y, específicamente, en gestión y optimización de inventario de repuestos de ingeniería. En 2012 Philip fue honrado con un premio nacional Premio al Liderazgo en Educación Logística. Para ver la publicación original del blog, haga clic en aquí.
Básicamente, hay dos formas en que las empresas expresan sus configuraciones de control de inventario: ya sea como MAX-MIN (a veces MIN-MAX) o ROP-ROQ.
Algunas personas dirán que realmente no importa cuál use, siempre y cuando comprenda las definiciones y los pros y los contras. Sin embargo, en mi experiencia, sí importa y este es un aspecto de la gestión del inventario de piezas de repuesto que realmente necesita para hacerlo bien.
Comencemos con las definiciones de MIN, MAX, ROP y ROQ
MIN = abreviatura de mínimo
Hay, de manera confusa, dos escuelas de pensamiento sobre lo que se entiende por MIN. Por lo general, este es el punto en el que se desencadena la necesidad de pedir más existencias. A veces, sin embargo, el MIN se considera la cantidad mínima que se puede mantener de manera segura para cubrir las necesidades previstas. En este caso se establece la necesidad de pedir más stock para que el punto de pedido sea uno menos que el valor MIN. Es decir. MÍN -1.
La clave para administrar cuando se utiliza una configuración MIN es comprender la configuración del sistema informático que utiliza, ya que las diferentes definiciones cambiarán el nivel de espera resultante, el punto de pedido y quizás incluso el stock de reserva o de seguridad real.
MAX = abreviatura de máximo
Este valor suele ser las existencias máximas específicas del artículo. Por lo general, en un sistema MAX-MIN, donde MIN es el punto de reorden, la cantidad reordenada después de alcanzar MIN es la cantidad requerida para volver a MAX. Por ejemplo, si el MAX-MIN es 5-2, cuando la cantidad en el almacén llegue a 2, el departamento de compras deberá pedir 3 para volver al MAX.
ROP = Punto de pedido
Como sugiere el nombre, simplemente, este es el nivel de existencias en el que se desencadena la necesidad de reordenar. Esto se calcula determinando el nivel de existencias de seguridad y las existencias requeridas para las necesidades de servicio durante el tiempo de entrega del nuevo pedido.
ROQ = Cantidad de nuevo pedido
Una vez más, como sugiere el nombre, esta es la cantidad que se volverá a pedir cuando se alcance el ROP. Esta no es la EOQ sino la cantidad que tiene sentido económico y está comercialmente disponible.
Las diferencias son significativas e importantes
Es esencial que cada gerente de inventario comprenda que los enfoques MAX-MIN y ROP-ROQ no son simplemente intercambiables.
Por ejemplo, en términos generales:
MIN se puede equiparar con la ROP, excepto si tiene un sistema configurado para reordenar en un punto de MIN-1. En ese caso, no hay equivalencia.
Para artículos de movimiento lento, el MAX puede, en algunas circunstancias, ser igual a la ROP + ROQ. Esto se debe a que, para los artículos de movimiento lento, es posible que no haya una demanda adicional antes de que los artículos recién pedidos lleguen a las existencias.
Sin embargo, con todos los demás artículos, es POCO PROBABLE que el MAX sea igual a la ROP + ROQ, ya que los artículos pueden emitirse entre el momento en que se alcanza el MIN y la llegada de los artículos recién pedidos. De hecho, existe una lógica que dice que el MAX nunca se alcanzaría.
¿Importan estas diferencias? Creo que lo hacen.
Por ejemplo, ¿qué sucede si cambia los sistemas de TI? Si pasa de un tipo de sistema MAX-MIN a otro pero definen el MIN de manera diferente, entonces no puede simplemente migrar sus datos. Esto puede no parecer obvio si todos usan el lenguaje de MAX-MIN, pero es una trampa clásica donde las palabras se usan de diferentes maneras.
De manera similar, si está comparando sus niveles de participación con otra empresa o sitio, entonces debe conocer las diferentes definiciones y los resultados que lograría cada enfoque. De lo contrario, está comparando 'manzanas con peras'.
O qué pasa cuando un nuevo miembro del equipo llega a su empresa y su empresa anterior usaba los términos MAX-MIN pero con parámetros o significados diferentes a los que usa su empresa. Es probable que se suponga que los términos se usan de la misma manera y esto podría dar lugar a escasez o exceso de existencias, según las diferencias en las definiciones.
Para agregar más confusión, algunos sistemas de software usan el término 'Stock de seguridad' para representar el nivel mínimo de retención, a pesar de que esta no es la definición universal de stock de seguridad. Esta nomenclatura diferente lleva a algunas personas a suponer que tener menos del llamado "stock de seguridad" según su sistema de TI es "inseguro" o riesgoso, cuando en realidad puede no serlo en absoluto. Incluso pueden tener un nivel excesivo de existencias porque no aplican correctamente el término "existencias de seguridad". Llamarlo inventario de seguridad no lo convierte en tal.
Pros y contras
MÁXIMO MINIMO
Ventajas:
• Conceptualmente simple de entender.
Contras:
• Los términos pueden ser engañosos en términos de existencias de seguridad y máximos reales.
• Los términos se utilizan de diferentes maneras, por lo que se requiere precaución para garantizar una comprensión común.
• Los valores a menudo se establecen utilizando la 'experiencia' o la intuición.
• A menudo conduce a un exceso de existencias mientras se informan datos de exceso de existencias engañosos
ROP-ROQ
Ventajas:
• El significado de cada término es claro y consistente.
• Valores establecidos mediante lógica auditable.
• Valores de stock de seguridad claramente establecidos.
• Es más probable que las tenencias reflejen las necesidades reales y las limitaciones comerciales.
Contras:
• Requiere más trabajo para determinar los valores apropiados.
Necesitas hacer esto bien
Las diferencias entre MAX-MIN y ROP-ROQ no son triviales y los términos ciertamente no son intercambiables. En mi experiencia, el enfoque ROP-ROQ produce mayor transparencia y es más fácil de manejar porque no hay confusión sobre el significado de los términos. Este enfoque también produce un nivel de inventario más apropiado y auditable.
Esto sugiere que si la gestión del inventario de repuestos es importante para usted, entonces realmente necesita hacerlo bien.
Artículos Relacionados
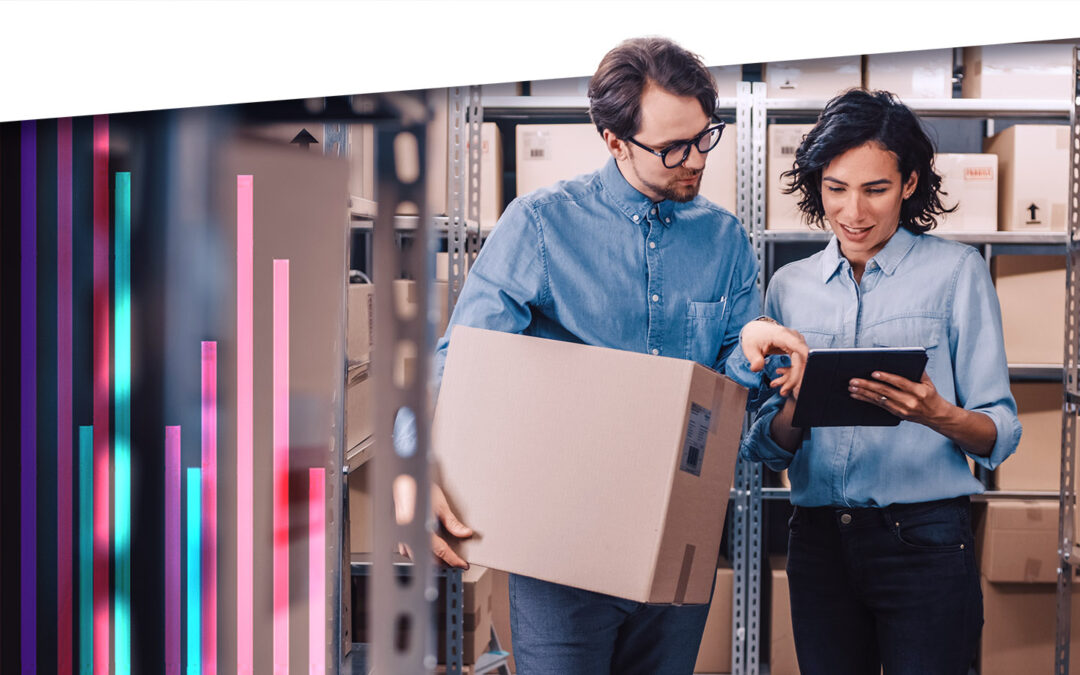
Gestión de inventario basada en pronósticos para una mejor planificación
Forecast-based inventory management, or MRP (Material Requirements Planning) logic, is a forward-planning method that helps businesses meet demand without overstocking or understocking. By anticipating demand and adjusting inventory levels, it maintains a balance between meeting customer needs and minimizing excess inventory costs. This approach optimizes operations, reduces waste, and enhances customer satisfaction.
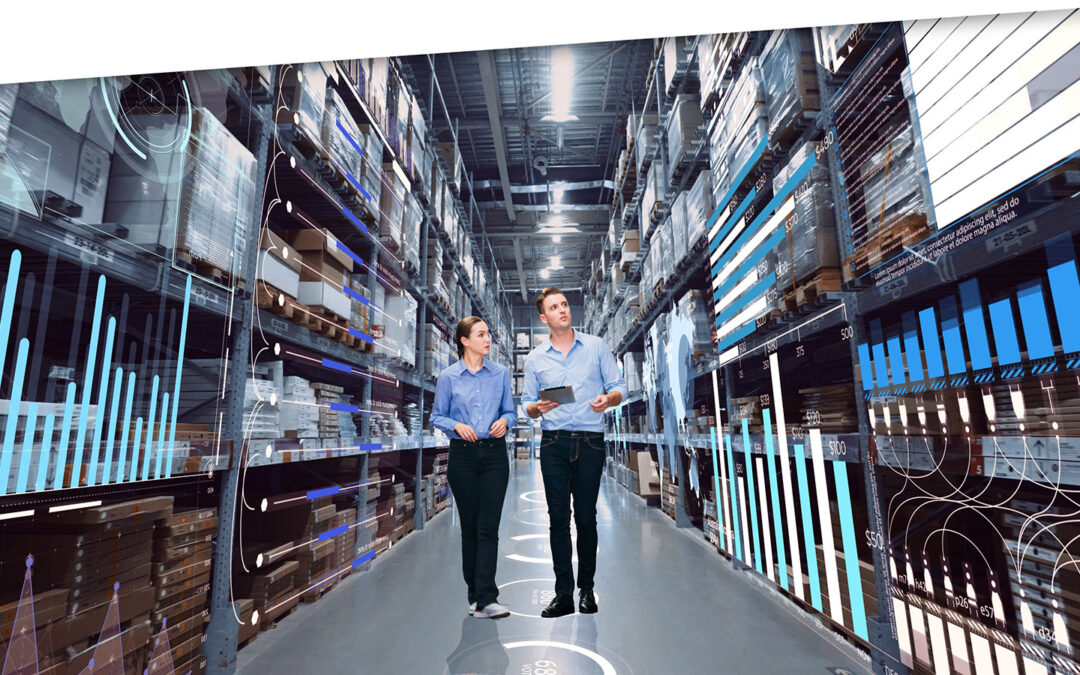
Haga de la optimización de inventario impulsada por IA un aliado para su organización
En este blog, exploraremos cómo las organizaciones pueden lograr una eficiencia y precisión excepcionales con la optimización del inventario impulsada por la IA. Los métodos tradicionales de gestión de inventario a menudo resultan insuficientes debido a su naturaleza reactiva y su dependencia de procesos manuales. Mantener niveles óptimos de inventario es fundamental para satisfacer la demanda de los clientes y minimizar los costos. La introducción de la optimización del inventario impulsada por la IA puede reducir significativamente la carga de los procesos manuales, brindando alivio a los gerentes de la cadena de suministro de tareas tediosas.
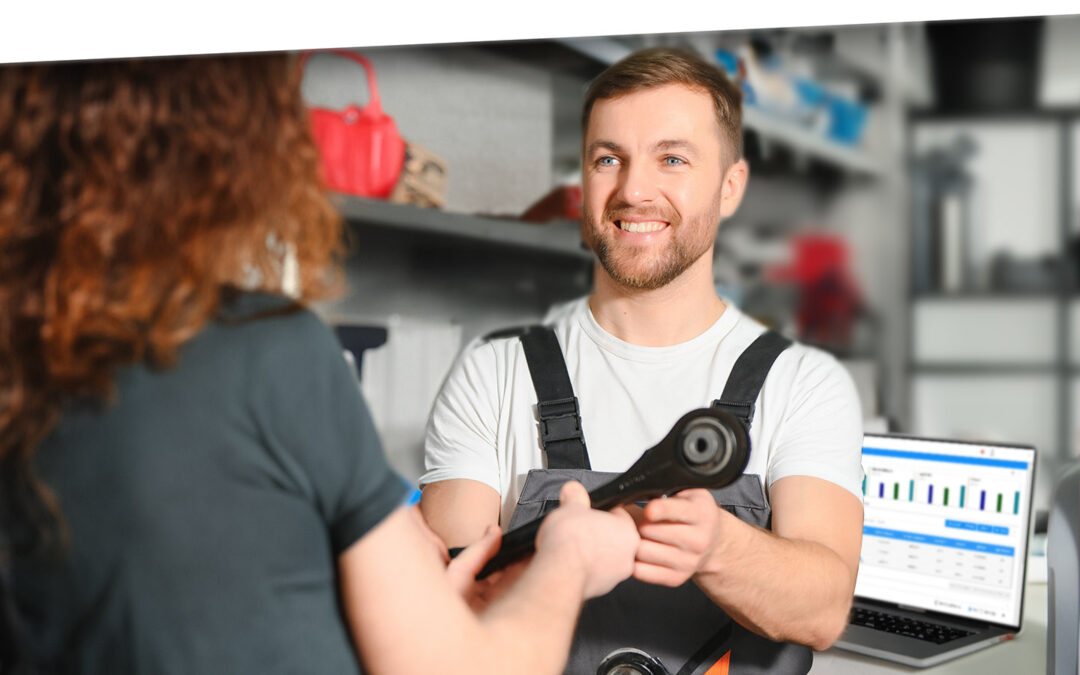
La importancia de definiciones claras de niveles de servicio en la gestión de inventario
El software de optimización de inventario que respalda el análisis hipotético expondrá el equilibrio entre los desabastecimientos y los costos excesivos de los distintos objetivos de nivel de servicio. Pero primero es importante identificar cómo se interpretan, miden y reportan los “niveles de servicio”. Esto evitará la falta de comunicación y la falsa sensación de seguridad que puede desarrollarse cuando se utilizan definiciones menos estrictas. Definir claramente cómo se calcula el nivel de servicio pone a todas las partes interesadas en la misma página. Esto facilita una mejor toma de decisiones.