Las empresas de servicios públicos tienen requisitos únicos de optimización de la cadena de suministro, principalmente garantizando un alto tiempo de actividad al mantener todas las máquinas críticas en funcionamiento continuo. Lograr esto implica mantener una alta disponibilidad de repuestos para garantizar un suministro consistente, confiable y seguro. Además, como entidades reguladas, las empresas de servicios públicos también deben gestionar y controlar cuidadosamente los costos.
Gestionar las cadenas de suministro de manera eficiente
Para mantener un suministro eléctrico fiable a 99.99%+ Para niveles de servicio, por ejemplo, las empresas de servicios públicos deben poder responder rápidamente a los cambios en la demanda en el corto plazo y anticipar con precisión la demanda futura. Para ello, deben tener una cadena de suministro bien organizada que les permita comprar los equipos, materiales y servicios necesarios de los proveedores adecuados en el momento adecuado, en las cantidades adecuadas y al precio adecuado.
Hacerlo se ha vuelto cada vez más desafiante en los últimos 3 años.
- Los requisitos de seguridad, confiabilidad y prestación de servicios son más estrictos.
- Las interrupciones en la cadena de suministro, los plazos de entrega impredecibles de los proveedores y los picos intermitentes en el uso de piezas siempre han sido problemáticos, pero ahora son más la regla que la excepción.
- La desregulación a principios de la década de 2000 eliminó las piezas de repuesto de la lista de artículos reembolsados directamente, lo que obligó a las empresas de servicios públicos a pagar las piezas de repuesto directamente con los ingresos.[1]
- La necesidad constante de capital combinada con tasas de interés que aumentan agresivamente significa que los costos se examinan más que nunca.
Como resultado, la optimización de la cadena de suministro (SCO) se ha convertido en una práctica empresarial cada vez más crítica para las empresas de servicios públicos. Para hacer frente a estos desafíos, las empresas de servicios públicos ya no pueden simplemente gestionar su cadena de suministro: deben optimizarla. Y para ello, serán necesarias inversiones en nuevos procesos y sistemas.
[1] Scala et al. “Inventario de Riesgos y Repuestos en Empresas Eléctricas”. Actas de la Conferencia de Investigación de Ingeniería Industrial.
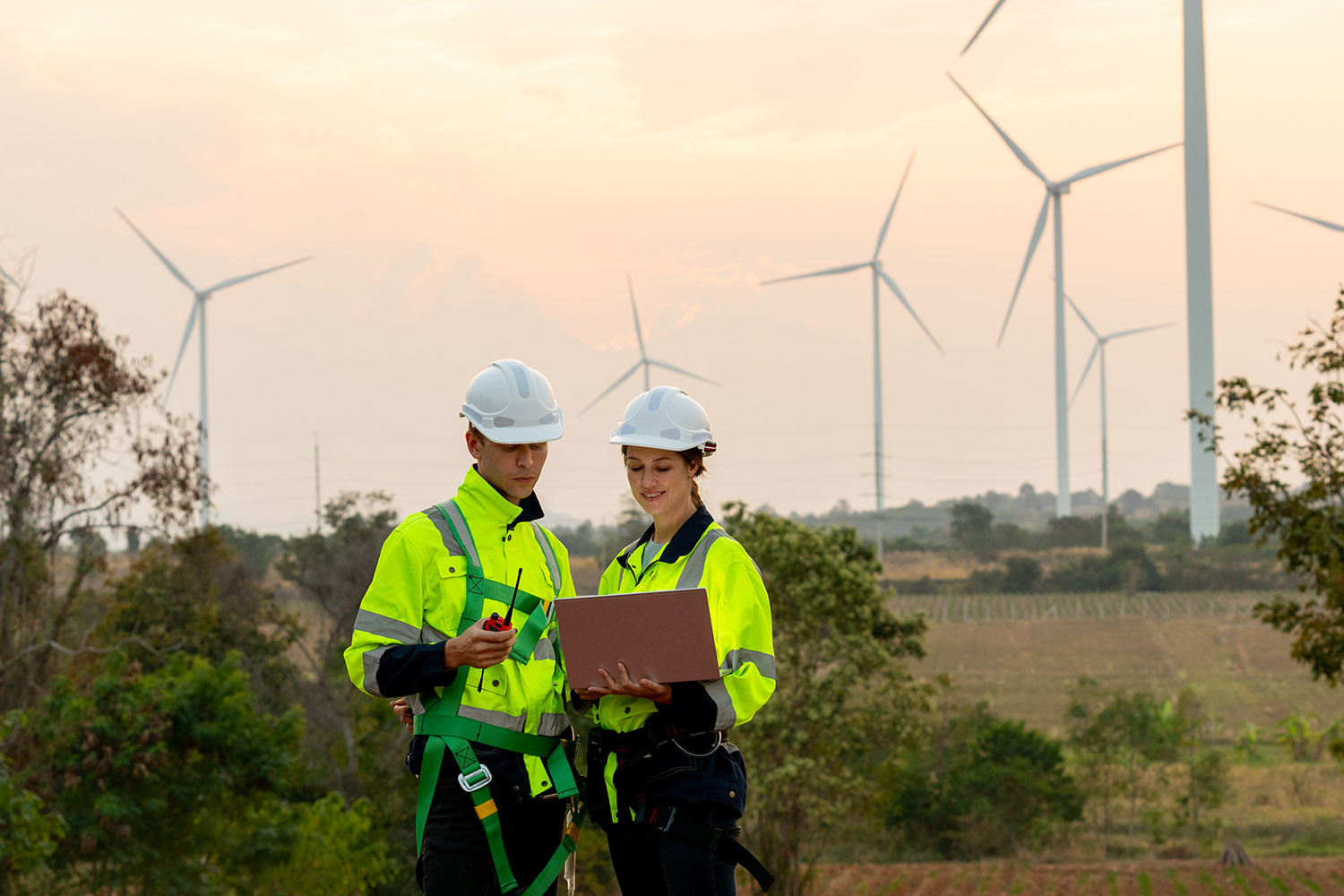
Planificación y optimización de inventario
Las inversiones específicas en tecnología de optimización de inventario ofrecen un camino a seguir para cada empresa de servicios públicos. Las soluciones de optimización de inventario deben priorizarse porque:
- Puede implementarse en una fracción del tiempo requerido para iniciativas en otras áreas, como la gestión de almacenes, el diseño de la cadena de suministro y las consolidaciones de compras. No es raro comenzar a generar beneficios después de 90 días y tener una implementación de software completa en menos de 180 días.
- Puede generar un ROI masivo, con rendimientos 20x y beneficios financieros de siete cifras al año. Al pronosticar mejor el uso de piezas, las empresas de servicios públicos reducirán los costos al comprar solo el inventario necesario mientras controlan el riesgo de desabastecimiento que conduce a tiempos de inactividad y niveles de servicio deficientes.
- Proporcionar apoyo fundamental para otras iniciativas. Una cadena de suministro sólida se basa en pronósticos de uso sólidos y planes de compra de inventario.
Utilizando análisis predictivos y algoritmos avanzados, la optimización de inventario ayuda a las empresas de servicios públicos a maximizar los niveles de servicio y reducir los costos operativos mediante la optimización de los niveles de inventario de piezas de repuesto. Por ejemplo, una empresa de servicios eléctricos podría usar pronósticos estadísticos para predecir el uso futuro de piezas, realizar auditorías de inventario para identificar el exceso de inventario y aprovechar los resultados analíticos para identificar dónde deben enfocarse primero los esfuerzos de optimización del inventario. Al hacer esto, la empresa de servicios públicos puede garantizar que las máquinas funcionen a niveles óptimos y reducir el riesgo de demoras costosas debido a la falta de repuestos.
Mediante el uso de análisis y datos, puede identificar qué repuestos y equipos es más probable que se necesiten y pedir solo los artículos necesarios. Esto ayuda a garantizar que el equipo tenga un alto tiempo de actividad. Recompensa el monitoreo y el ajuste regulares de los niveles de inventario para que cuando cambien las condiciones operativas, pueda detectar el cambio y ajustarlo en consecuencia. Esto implica que los ciclos de planificación deben operar a un ritmo lo suficientemente alto como para mantenerse al día con las condiciones cambiantes. apalancamiento de pronóstico probabilístico recalibrar las políticas de almacenamiento de repuestos para cada ciclo de planificación garantiza que las políticas de almacenamiento (como los niveles mínimos/máximos) estén siempre actualizadas y reflejen el uso de piezas y los plazos de entrega de los proveedores más recientes.
Niveles de servicio y la curva de compensación
El nivel de servicio Curva de compensación relaciona la inversión en inventario con la disponibilidad de artículos medida por el nivel de servicio. El nivel de servicio es la probabilidad de que no ocurra escasez entre el momento en que solicita más existencias y cuando llega al estante. Sorprendentemente, pocas empresas tienen datos sobre esta importante métrica en toda su flota de repuestos.
La curva de compensación del nivel de servicio expone el vínculo entre los costos asociados con los diferentes niveles de servicio y los requisitos de inventario necesarios para alcanzarlos. Saber qué componentes son importantes para mantener altos niveles de servicio es clave para el proceso de optimización y está determinado por varios factores, incluida la estandarización de artículos del inventario, la criticidad, el uso histórico y las órdenes de reparación futuras conocidas. Al comprender esta relación, las empresas de servicios públicos pueden asignar mejor los recursos, como cuando se usan las curvas para identificar áreas donde se pueden reducir los costos sin afectar la confiabilidad del sistema.
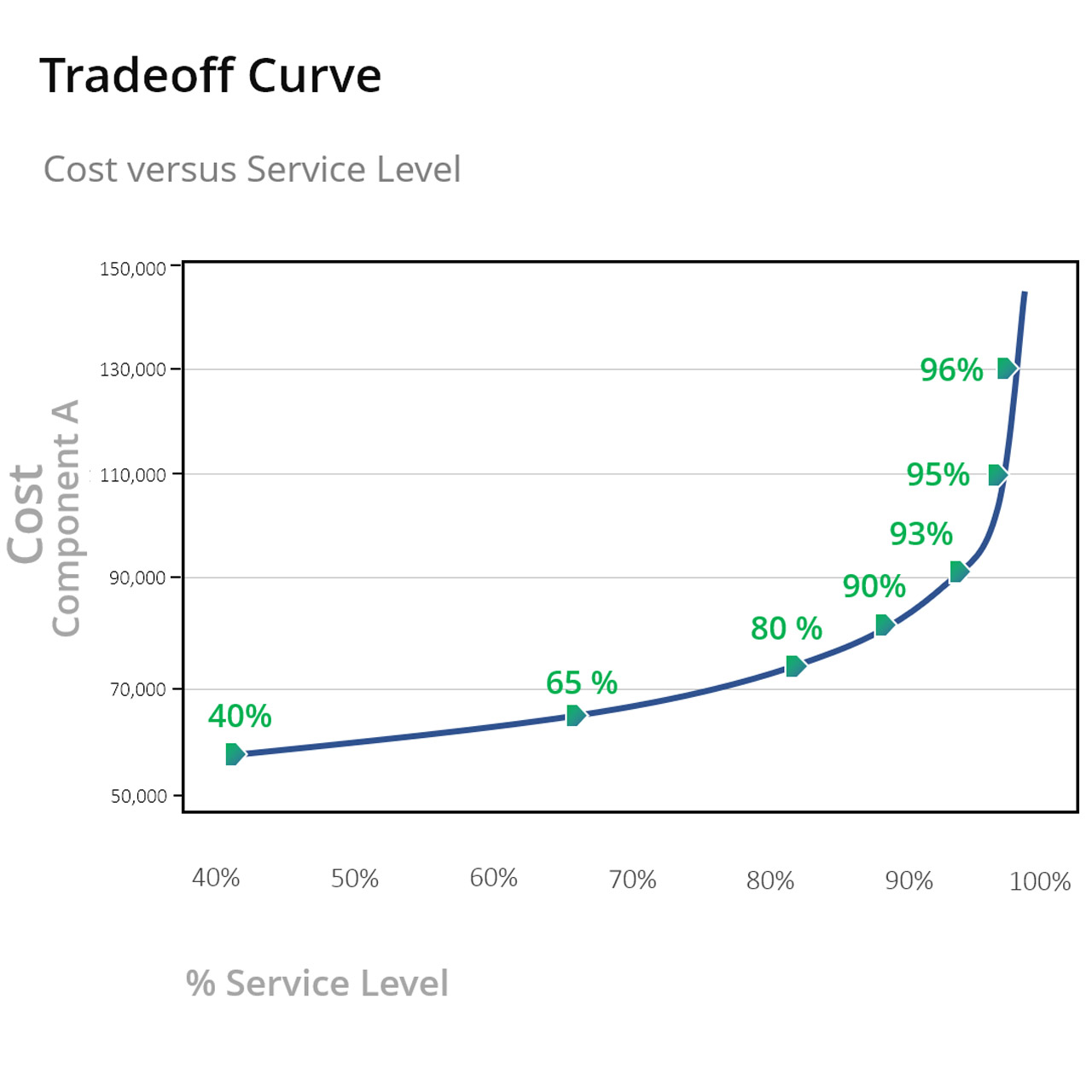
Con el software de optimización de inventario, establecer políticas de almacenamiento es pura conjetura: es posible saber cómo cualquier aumento o disminución afectará los niveles de servicio, además de las estimaciones aproximadas. Nadie sabe realmente cómo se desarrollarán los cambios en términos de inversión en inventarios, costos operativos y costos de escasez. La mayoría de los servicios públicos dependen de métodos de regla general y ajustar arbitrariamente las políticas de almacenamiento de manera reactiva después de que algo haya salido mal, como una gran falta de existencias o una pérdida de inventario. Cuando los ajustes se realizan de esta manera, no hay un análisis basado en hechos que detalle cómo se espera que este cambio afecte las métricas que importan: niveles de servicio y valores de inventario.
El software de optimización de inventario puede calcular las curvas de compensación cuantitativas y detalladas requeridas para tomar decisiones informadas sobre políticas de inventario o incluso recomendar el nivel de servicio objetivo que resulte en el costo operativo general más bajo (la suma de los costos de mantenimiento, pedido y desabastecimiento). Usando este análisis, los grandes aumentos en los niveles de existencias pueden justificarse matemáticamente cuando la reducción prevista en los costos de escasez supera el aumento en la inversión en inventario y los costos de mantenimiento asociados. Al establecer niveles de servicio apropiados y recalibrar las políticas en todas las partes activas una vez en cada ciclo de planificación (al menos una vez al mes), las empresas de servicios públicos pueden minimizar el riesgo de interrupciones mientras controlan los gastos.
Quizás los aspectos más críticos de la respuesta a la avería del equipo son los relacionados con el logro de una arreglo por primera vez lo más rápido posible. Tener los repuestos adecuados disponibles puede ser la diferencia entre completar un solo viaje y aumentar el tiempo medio de reparación, asumir los costos asociados con varias visitas y hacer que las relaciones con los clientes se deterioren.
Con un software moderno, puede comparar el rendimiento anterior y aprovechar los métodos de pronóstico probabilístico para simular el rendimiento futuro. Al someter a prueba sus políticas actuales de almacenamiento de inventario frente a todos los escenarios plausibles de uso futuro de piezas, sabrá de antemano cómo es probable que funcionen las políticas de almacenamiento actuales y propuestas. Cecha un vistazo a nuestra publicación de blog sobre cómo medir la precisión de su pronóstico de nivel de servicio para ayudarlo a evaluar la precisión de las recomendaciones de inventario que los proveedores de software pretenden proporcionar beneficios.
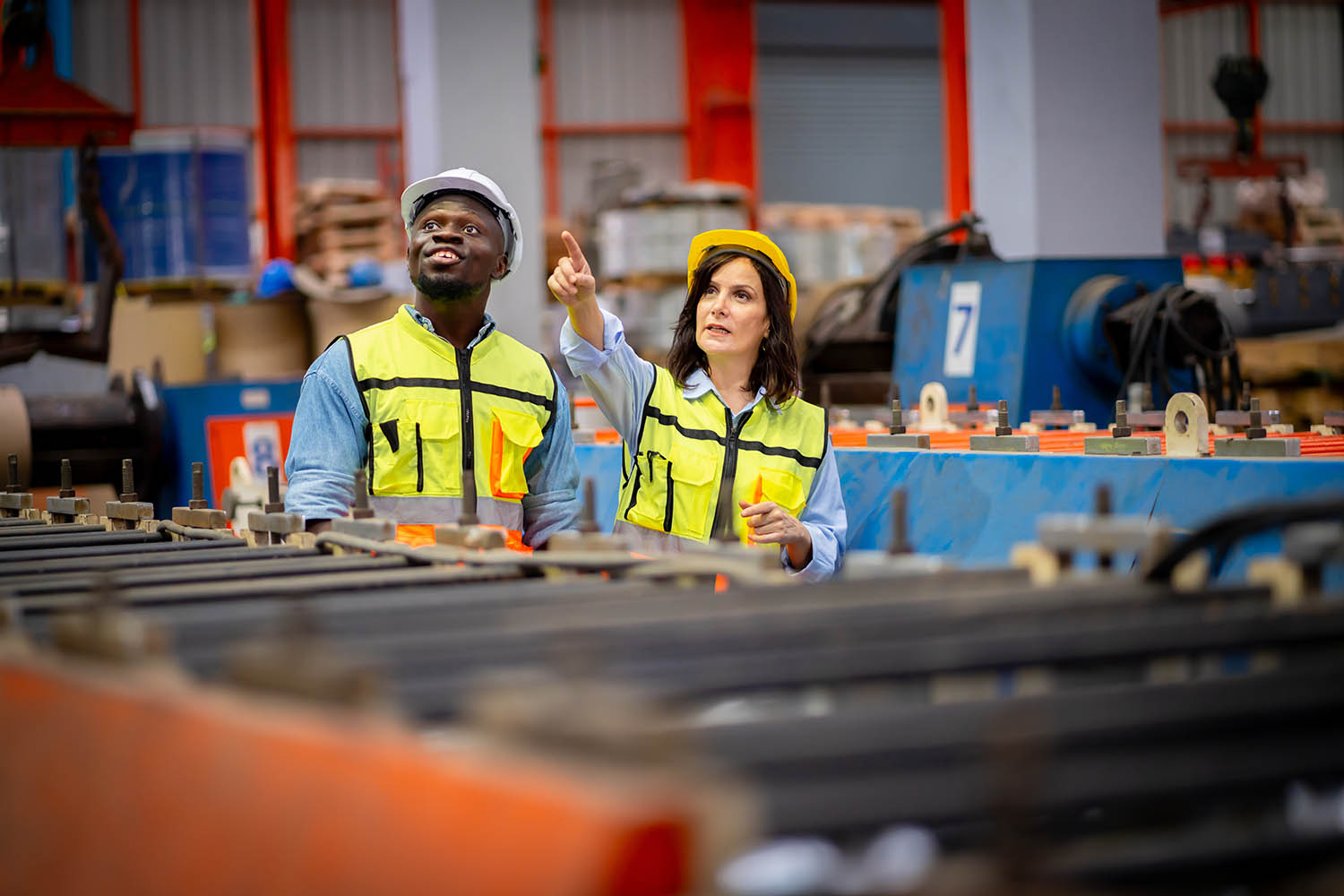
Aprovechando el análisis avanzado y la IA
Al introducir la automatización, cada empresa de servicios públicos tiene sus propios objetivos que perseguir, pero se debe comenzar evaluando las operaciones actuales para identificar áreas que pueden volverse más efectivas. Algunas empresas pueden priorizar las cuestiones financieras, pero otras pueden priorizar las exigencias regulatorias, como el gasto en energía limpia o cambios en toda la industria, como las redes inteligentes. Las dificultades de cada empresa son únicas, pero el software moderno puede señalar el camino hacia un sistema de gestión de inventario más eficaz que minimice el exceso de inventario y coloque los componentes correctos en los lugares correctos y en el momento adecuado.
En general, las iniciativas de optimización de la cadena de suministro son esenciales para las empresas de servicios públicos que buscan maximizar su eficiencia y reducir sus costos. La tecnología nos permite hacer que el proceso de integración sea perfecto y no es necesario que reemplace su sistema ERP o EAM actual para hacerlo. Solo necesita hacer un mejor uso de los datos que ya tiene.
Por ejemplo, una gran empresa de servicios públicos lanzó una iniciativa estratégica de optimización de la cadena de suministro (SCO) y agregó las mejores capacidades de su clase a través de la selección e integración de aplicaciones comerciales listas para usar. El principal de ellos fue el sistema inteligente de planificación y optimización de inventario (Smart IP&O), que comprende la funcionalidad de previsión de piezas/planificación de demanda y optimización de inventario. En solo 90 días, el sistema de software estaba listo y funcionando, y pronto redujo el inventario en $9,000,000 mientras mantenía la disponibilidad de repuestos a un alto nivel. Puedes leer el caso de estudio aquí La empresa de servicios eléctricos opta por Smart IP&O.
Las empresas de servicios públicos pueden asegurarse de poder gestionar sus suministros de repuestos de una manera eficiente y rentable, preparándolas mejor para el futuro. Con el tiempo, este equilibrio entre oferta y demanda se traduce en una ventaja significativa. Comprender la curva de compensación del nivel de servicio ayuda a comprender los costos asociados con los diferentes niveles de servicio y los requisitos de inventario necesarios para lograrlos. Esto conduce a costos operativos reducidos, inventario optimizado y garantía de que puede satisfacer las necesidades de sus clientes.