En este artículo, revisaremos la funcionalidad de pedidos de inventario en Epicor P21, explicaremos sus limitaciones y resumiremos cómo Smart Inventory Planning & Optimization (Smart IP&O) puede ayudar a reducir el inventario, minimizar los desabastecimientos y restaurar la confianza de su organización en su ERP. También veremos como generar un robusto análisis predictivo, pronóstico basado en consenso y planificación de escenarios hipotéticos.
Funciones de planificación de reabastecimiento dentro de Epicor Prophet 21
Epicor P21 puede administrar el reabastecimiento al sugerir qué ordenar y cuándo a través de políticas de inventario basadas en puntos de reorden o basadas en pronósticos. Los usuarios pueden calcular estas políticas externamente o generarlas dinámicamente dentro de P21. Una vez que se hayan especificado las políticas y los pronósticos, el Generador de requisitos de órdenes de compra (PORG) de P21 creará sugerencias de pedidos automatizadas de qué reponer y cuándo reconciliar el suministro entrante, la demanda actual disponible, las políticas de almacenamiento y los pronósticos de demanda.
Epicor P21 tiene 4 métodos de reposición
En la pantalla de mantenimiento de artículos de Epicor P21, los usuarios pueden elegir uno de los cuatro métodos de reabastecimiento para cada artículo en existencia.
- Mínimo máximo
- Punto de pedido/Cantidad de pedido
- EOQ
- ”Hasta” una cantidad
Hay ajustes y configuraciones adicionales para determinar los plazos de entrega y contabilizar los modificadores de pedidos, como las cantidades mínimas y máximas de pedido impuestas por el proveedor. Mín./Máx. y Punto de pedido/Cantidad de pedido se consideran políticas "estáticas". EOQ y ”Hasta” se consideran políticas "dinámicas" y se calculan dentro de P21.
Mínimo máximo
El punto de reorden es igual al Min. Cada vez que el inventario disponible cae por debajo del mínimo (punto de pedido), el informe PORG creará una sugerencia de pedido hasta el máximo (por ejemplo, si el inventario disponible después de la infracción es de 20 unidades y el máximo es 100, entonces la cantidad del pedido será 80) . Min/Max se considera una política estática y una vez ingresada en P21 permanecerá sin cambios a menos que el usuario la anule. Los usuarios suelen ejecutar hojas de cálculo para calcular los valores mínimos y máximos y actualizarlos de vez en cuando.
Punto de pedido/Cantidad de pedido
Esto es lo mismo que la política Mín./Máx. excepto que en lugar de pedir hasta el Máx., se sugerirá un pedido para una cantidad fija definida por el usuario (por ejemplo, pida siempre 100 unidades cuando se incumpla el punto de pedido). OP/OQ se considera una política estática y permanecerá sin cambios a menos que el usuario la anule. Los usuarios a menudo ejecutan hojas de cálculo para calcular los valores OP/OQ y actualizarlos de vez en cuando.
EOQ
La política de EOQ es un método basado en puntos de reorden. El punto de pedido se genera dinámicamente en función del pronóstico de demanda de P21 durante el tiempo de entrega + la demanda durante el período de revisión + el stock de seguridad. La cantidad de la orden se basa en un cálculo de la Cantidad económica de la orden que considera los costos de mantenimiento y los costos de la orden e intenta recomendar un tamaño de orden que minimice el costo total. Cuando el inventario disponible supera el punto de pedido, el informe PORG generará un pedido igual al EOQ calculado.
”Hasta” una cantidad
El método Up To es otra política dinámica que se basa en un punto de pedido. Se calcula de la misma manera que el método EOQ utilizando la demanda pronosticada de P21 durante el tiempo de entrega + la demanda durante el período de revisión + el inventario de seguridad. La sugerencia de cantidad de pedido se basa en lo que sea necesario para reabastecer el stock "hasta" el punto de pedido. Esto tiende a equivaler a una cantidad de pedido que es consistente con la demanda del tiempo de entrega porque a medida que la demanda impulsa el stock por debajo del punto de reorden, se sugerirán pedidos "hasta" el punto de reorden.
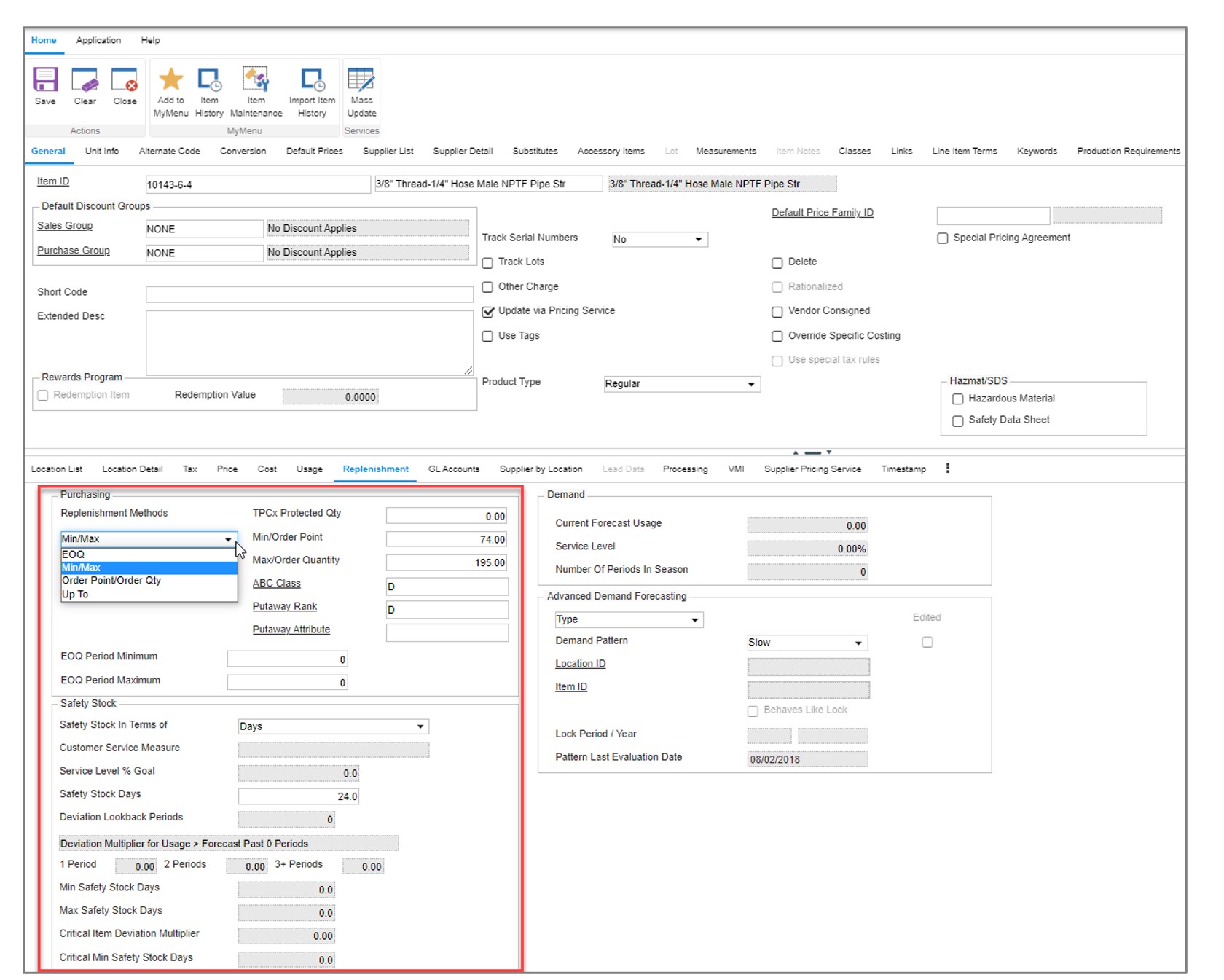
Pantalla de mantenimiento de artículos de P21, donde los usuarios pueden especificar la política de inventario deseada y configurar otros ajustes, como stock de seguridad y modificadores de pedidos.
Limitaciones
Métodos de pronóstico
Hay dos modos de pronóstico en P21: Básico y Avanzado. Cada uno usa una serie de métodos de promedio y requiere configuraciones manuales y reglas de clasificación determinadas por el usuario para generar un pronóstico de demanda. Ninguno de los modos está diseñado con un sistema experto listo para usar que genera automáticamente pronósticos que dan cuenta de los patrones subyacentes, como la tendencia o la estacionalidad. Se requiere mucha configuración que tiende a inhibir la adopción por parte del usuario y la modificación de las reglas de pronóstico asumidas definidas en la implementación inicial que pueden ya no ser relevantes. No existe una manera de comparar fácilmente la precisión del pronóstico de diferentes configuraciones. Por ejemplo, ¿es mejor usar 24 meses de historial o 18 meses? ¿Es más exacto suponer que se debe aplicar una tendencia cuando un artículo crece 2% por mes o debería ser 10%? ¿Es mejor asumir que el artículo es estacional si 80% o más de su demanda ocurre en 6 meses del año o 4 meses del año? Como resultado, es común que las reglas de clasificación sean demasiado amplias o específicas, lo que genera problemas como la aplicación de un modelo de pronóstico incorrecto, el uso de demasiado o muy poco historial, o la sobreestimación o subestimación de la tendencia y la estacionalidad. Para obtener más información sobre cómo funciona esto, consulte esta publicación de blog (próximamente)
Gestión de pronósticos y planificación por consenso
P21 carece de funciones de gestión de pronósticos que permitan a las organizaciones planificar en múltiples niveles de jerarquía, como familia de productos, región o por cliente. Los pronósticos deben crearse en el nivel más bajo de granularidad (producto por ubicación) donde la demanda suele ser demasiado intermitente para obtener un buen pronóstico. No hay forma de compartir pronósticos, colaborar, revisar o crear pronósticos en niveles agregados y acordar el plan de consenso. Es difícil incorporar conocimiento comercial, evaluar pronósticos en niveles más altos de agregación y rastrear si las anulaciones mejoran o perjudican la precisión del pronóstico. Esto hace que la previsión sea demasiado unidimensional y dependa de las configuraciones matemáticas iniciales.
Demanda intermitente
Muchos clientes de P21 confían en métodos estáticos (mín./máx. y OP/OQ) debido al predominio de la demanda intermitente. También conocida como "érratica", la demanda intermitente se caracteriza por ventas esporádicas, grandes picos en la demanda y muchos períodos sin demanda. Cuando la demanda es intermitente, los métodos tradicionales de previsión y existencias de seguridad simplemente no funcionan. Dado que los distribuidores no pueden darse el lujo de abastecerse únicamente de productos de alta rotación con una demanda constante, necesitan soluciones especializadas que estén diseñadas para planificar de manera eficaz los artículos con demanda intermitente. 80% o más de las piezas de un distribuidor tendrán una demanda intermitente. Las políticas de almacenamiento que se generan utilizando métodos tradicionales, como los disponibles en P21 y otras aplicaciones de planificación, darán como resultado estimaciones incorrectas de qué almacenar para lograr el nivel de servicio objetivo. Como se ilustra en el gráfico a continuación, no es posible pronosticar los picos de manera constante. Está atascado con un pronóstico que es efectivamente un promedio de los períodos anteriores.
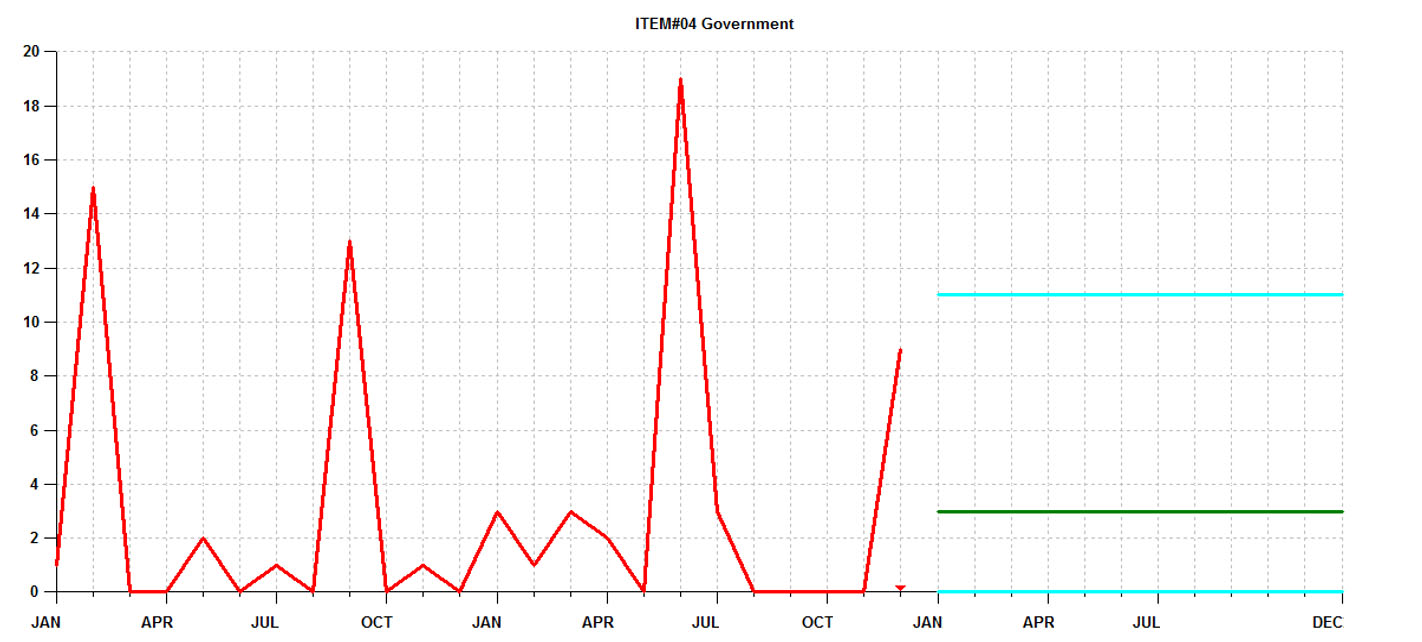
Los pronósticos de demanda intermitente no pueden predecir los picos y requieren reservas de existencias de seguridad para protegerse contra los desabastecimientos.
En segundo lugar, los métodos de inventario de seguridad de P21 le permiten establecer un nivel de servicio objetivo, pero la lógica subyacente supone erróneamente que la demanda esta Normalmente distribuida. Con la demanda intermitente, la demanda no es “normal” y por lo tanto la estimación del stock de seguridad será incorrecta. Esto es lo que significa incorrecto: al establecer un nivel de servicio de, por ejemplo, 98%, la expectativa es que 98% del tiempo que el stock disponible llene 100% de lo que el cliente necesita del estante. El uso de una distribución normal para calcular las existencias de seguridad dará como resultado grandes desviaciones entre el nivel de servicio objetivo y el nivel de servicio real logrado. No es raro ver situaciones en las que el nivel de servicio real no alcance el objetivo por 10% o más (es decir, se apuntó a 95% pero solo alcanzó 85%).
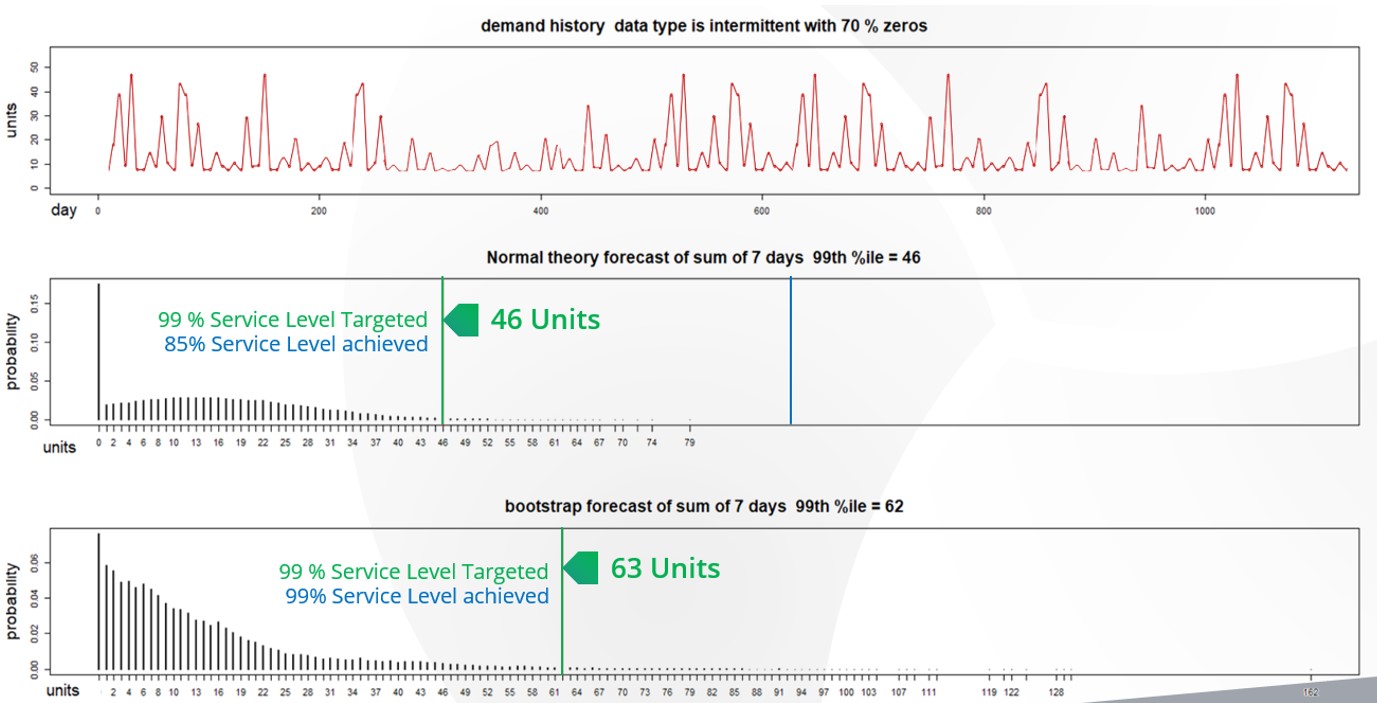
En esta figura puede ver el historial de demanda de una pieza demandada intermitentemente y dos distribuciones basadas en este historial de demanda. La primera distribución se generó utilizando la misma “distribución normal: lógica empleada por P21. La segunda es una distribución simulada basada en el pronóstico probabilístico de Smart Software. La distribución P21 "normal" recomienda que se necesitan 46 unidades para alcanzar el nivel de servicio 99%, pero en comparación con los valores reales, se necesitaba mucho más inventario. Smart predijo con precisión que se requerían 63 unidades para alcanzar el nivel de servicio.
Este Blog explica cómo puede probar la precisión del nivel de servicio de su sistema.
Confianza en hojas de cálculo y planificación reactiva
Los clientes de P21 nos dicen que dependen en gran medida del uso de hojas de cálculo para gestionar las políticas de almacenamiento y las previsiones. Las hojas de cálculo no están diseñadas específicamente para la previsión y la optimización del inventario. Los usuarios a menudo seguirán sus propias regla de oro inventadas por el usuario, métodos que a menudo hacen más daño que bien. Una vez calculado, los usuarios deben ingresar la información nuevamente en P21 a través de la importación manual de archivos o incluso la entrada manual. La naturaleza lenta del proceso lleva a las empresas a calcular sus políticas de inventario con poca frecuencia. Pasan muchos meses y, en ocasiones, años entre actualizaciones masivas que conducen a un enfoque reactivo de "configúrelo y olvídese", y el momento del pedidoe se convierte en el único momento en que un comprador/planificador revisa la política de inventario. Cuando las políticas se revisan después de que el punto de pedido ya se ha incumplido, es demasiado tarde. Cuando el punto de pedido se considera demasiado alto, se requiere una modificación manual para revisar el historial, calcular pronósticos, evaluar las posiciones del búfer y recalibrar. El gran volumen de pedidos significa que los compradores simplemente liberarán los pedidos en lugar de tomarse el arduo tiempo de revisar todo, lo que generará un exceso significativo de existencias. Si el punto de pedido es demasiado bajo, ya es demasiado tarde. Ahora se requerirá una aceleración que aumente los costos e incluso entonces, aún perderá ventas si el cliente se va a otro lado.
Planificación limitada de What If
Dado que las funciones para modificar los puntos de pedido y las cantidades de pedido están integradas en P21, no es posible realizar cambios generales en grupos de artículos y evaluar los resultados previstos antes de decidir comprometerse. Esto obliga a los usuarios a adoptar un proceso de "esperar y ver" cuando se trata de modificar parámetros. Los planificadores harán un cambio y luego monitorearán los datos reales hasta que estén seguros de que el cambio mejoró las cosas. Administrar esto a escala (muchos planificadores manejan decenas de miles de artículos) consume mucho tiempo y el resultado final es una recalibración poco frecuente de la política de inventario. Esto también contribuye a la planificación reactiva por lo que los planificadores solo revisarán la configuración después de que haya ocurrido un problema.
Epicor es más inteligente
Epicor se asoció con Smart Software y ofrece Smart IP&O como un complemento multiplataforma para Prophet 21 completo con una integración bidireccional basada en API. Esto permite que los clientes de Epicor aprovechen las mejores aplicaciones de pronóstico y optimización de inventario creadas especialmente. Con Epicor Smart IP&O puede generar pronósticos que capturan la tendencia y la estacionalidad sin tener que aplicar configuraciones manuales primero. Podrá volver a calibrar automáticamente las políticas en cada ciclo de planificación utilizando modelos estadísticos y probabilísticos de vanguardia probados en el campo que fueron diseñados para planificar con precisión de la demanda intermitente. Las existencias de seguridad tendrán en cuenta con precisión la variabilidad de la oferta y la demanda, las condiciones comerciales y las prioridades. Puedes aprovechar la planificación impulsada por el nivel de servicio para que tenga suficiente stock o activar métodos de optimización que prescriben las políticas de almacenamiento más rentables y los niveles de servicio que consideran el costo real de mantener el inventario. Puede crear pronósticos de demanda consensuados que combinen el conocimiento comercial con las estadísticas, evaluar mejor los pronósticos de venta y de los clientes, y cargar con confianza pronósticos y políticas de existencias en Epicor con unos pocos clics del mouse.
Los clientes de Smart IP&O generalmente obtienen ganancias anuales de 7 cifras a partir de rápidas reducciones, mayores ventas y menos exceso de existencias, al mismo tiempo que obtienen una ventaja competitiva al diferenciarse en un mejor servicio al cliente. Regístrese aquí para ver un seminario web grabado y organizado por el Grupo de usuarios de Epicor que perfila la plataforma de optimización de inventario y planificación de la demanda de Smart. https://smartcorp.com/epicor-smart-inventory-planning-optimization/