FONDO
La mayoría de los blogs, seminarios web y documentos técnicos de Smart Software describen el uso de nuestro software en "operaciones normales". Este trata sobre “operaciones irregulares”. Smart Software está en el proceso de adaptar nuestros productos para ayudarle a afrontar sus propias operaciones irregulares. Esto es una vista previa.
Escuché por primera vez el término “operaciones irregulares” cuando cumplía un período sabático en la Administración Federal de Aviación de Estados Unidos en Washington, DC. La FAA abrevia el término "IROPS" y lo utiliza para describir situaciones en las que el clima, problemas mecánicos u otros problemas interrumpen el flujo normal de la aeronave.
Smart Inventory Optimization® (“SIO”) actualmente trabaja para proporcionar lo que se conoce como políticas de “estado estable” para administrar artículos de inventario. Eso significa, por ejemplo, que SIO calcula automáticamente los valores de los puntos de reorden (ROP) y las cantidades de pedido (OQ) que deben durar en el futuro previsible. Calcula estos valores basándose en simulaciones de operaciones diarias que se extienden años en el futuro. Si sucede lo imprevisible, nuestra Cambio de regimén El método de detección reacciona eliminando datos obsoletos y permitiendo volver a calcular los ROP y OQ.
A menudo observamos la creciente velocidad de los negocios, lo que acorta la duración del “futuro previsible”. Algunos de nuestros clientes ahora están adoptando horizontes de planificación más cortos, como pasar de planes trimestrales a mensuales. Un efecto secundario de este cambio es que las IROPS se han vuelto más importantes. Si un plan se basa en tres años simulados de demanda diaria, un evento extraño, como un gran pedido sorpresa, no importa mucho en el gran esquema de las cosas. Pero si el horizonte de planificación es muy corto, una gran demanda sorpresa puede tener un efecto importante en los indicadores clave de desempeño (KPI) calculados en un intervalo más corto: no hay tiempo para “promediar”. El planificador puede verse obligado a realizar una orden de reabastecimiento de emergencia para hacer frente a la interrupción. ¿Cuándo se debe realizar el pedido para hacer el mayor bien? ¿Qué tan grande debería ser?
ESCENARIO: OPS NORMALES
Para concretar esto, considere el siguiente escenario. Tom's Spares, Inc. proporciona piezas de servicio críticas a sus clientes, incluido SKU723, una placa de circuito de repuesto vendida con el nombre comercial WIDGET. La demanda de WIDGET es intermitente, con menos de una unidad por día. Tom's Spares realiza pedidos de WIDGET a Acme Products, quienes tardan entre 7 y 10 días en cumplir con los pedidos de reabastecimiento.
Tom's Spares opera con un horizonte de planificación de inventario corto de 28 días. La empresa opera en un entorno competitivo con clientes impacientes que sólo aceptan de mala gana los pedidos pendientes. La política de Tom es establecer ROP y OQ para mantener el inventario reducido y al mismo tiempo mantener una tasa de cumplimiento de al menos 90%. La gerencia monitorea los KPI mensualmente. En el caso de WIDGETS, estos objetivos de KPI se cumplen actualmente utilizando un ROP=3 y un OQ=4, lo que da como resultado un promedio disponible de aproximadamente 4 unidades y una tasa de cumplimiento promedio de 96%. Tom's Spares tiene algo bastante bueno con los WIDGETS.
La Figura 1 muestra dos meses de información WIDGET. El panel superior izquierdo muestra la demanda unitaria diaria. La parte superior derecha muestra las unidades diarias disponibles. El panel inferior izquierdo muestra el momento y el tamaño de los pedidos de reabastecimiento a Acme Products. La parte inferior derecha muestra las unidades pendientes de pedido debido a desabastecimientos. En esta simulación, la demanda diaria era 0 o 1, con una demanda de 2 unidades. Las unidades disponibles comenzaron el mes en 7 y nunca cayeron por debajo de 1, aunque en el mes siguiente hubo un desabastecimiento que resultó en una sola unidad en espera. Durante los dos meses, se enviaron a Acme 4 pedidos de reabastecimiento de 4 unidades cada uno, y todos llegaron durante el período de simulación de dos meses.
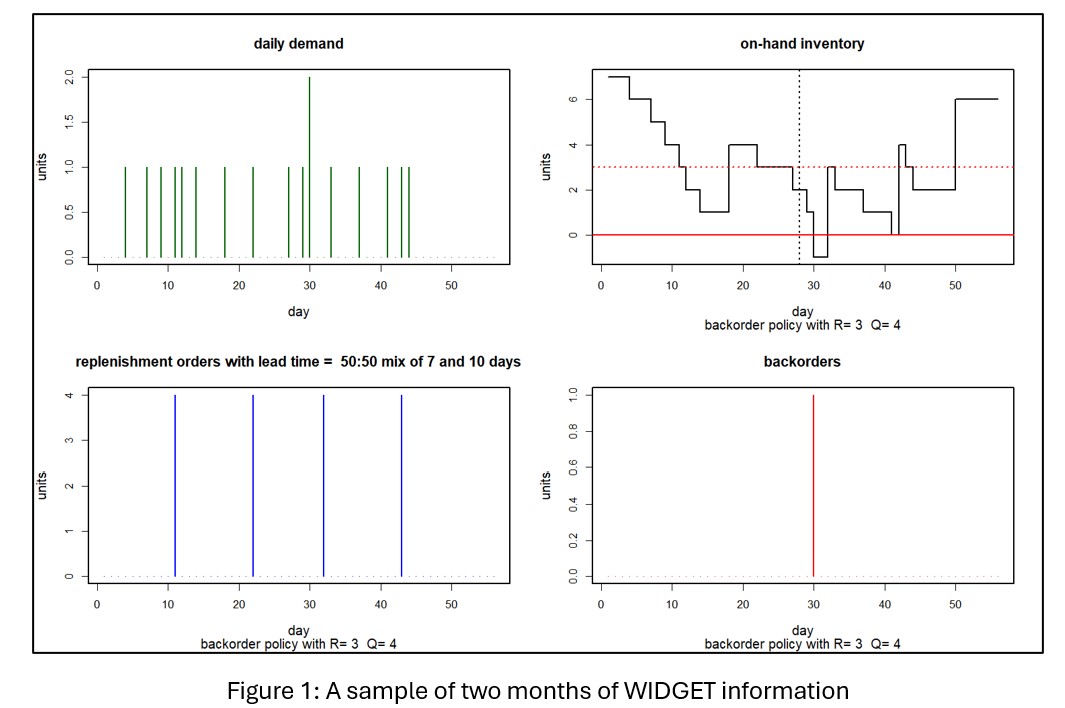
UN BUEN PROBLEMA INTERRUMPE LAS OPERACIONES NORMALES
Ahora agregamos algunos “buenos problemas” al escenario: surge un pedido inusualmente grande a mitad del período de planificación. Es “bueno” porque más demanda implica más ingresos. Pero es un “problema” porque los parámetros normales de control de inventario de operaciones (ROP=3, OQ=4) no fueron elegidos para hacer frente a esta situación. El aumento de la demanda podría ser tan grande, y en un momento tan desventajoso, como para abrumar el sistema de inventario, creando desabastecimientos y los consiguientes pedidos pendientes. El informe de KPI a la gerencia para un mes así no sería agradable.
La Figura 2 muestra un escenario en el que se produce un pico de demanda de 10 unidades en el tercer día del período de planificación. En este caso, el pico pone el inventario bajo agua durante el resto del mes y crea una cascada de pedidos pendientes que se extiende hasta el mes siguiente. Con un promedio de más de 1000 simulaciones, los KPI del mes 1 muestran un promedio disponible de 0,6 unidades y una miserable tasa de llenado de 44%.

LUCHA CONTRA CON OPERACIONES IRREGULARES
Tom's Spares puede responder a una situación irregular con un movimiento irregular creando una orden de reabastecimiento de emergencia. Para hacerlo bien, tienen que pensar en (a) cuándo realizar el pedido (b) qué tan grande debe ser el pedido y (c) si deben acelerar el pedido.
La cuestión del momento parece obvia: reaccionar tan pronto como llegue la orden. Sin embargo, si el cliente avisara con antelación, Tom's Spares podría realizar el pedido con antelación y estar en mejor posición para limitar las interrupciones provocadas por el pico. Sin embargo, si la comunicación entre Tom's y el cliente que realiza el pedido grande es irregular, entonces el cliente podría avisar a Tom's más tarde o no avisarle en absoluto.
El tamaño del pedido especial también parece obvio: haga un pedido anticipado del número de unidades requerido. Pero eso funciona mejor si Tom's Spares sabe cuándo se producirá el pico de demanda. De lo contrario, podría ser una buena idea realizar pedidos adicionales para limitar la duración de los pedidos pendientes. En general, cuanto menos alerta temprana se proporcione, mayor será el pedido que Tom's deberá realizar. Por supuesto, esta relación podría explorarse mediante simulación.
La llegada del pedido de reposición podría dejarse a la operación habitual de Acme Products. En las simulaciones anteriores, Acme tenía las mismas probabilidades de responder en 7 o 14 días. Para un horizonte de planificación de 28 días, correr el riesgo de obtener una respuesta de 14 días podría generar problemas, por lo que puede ser especialmente valioso para Tom's pagarle a Acme por el envío acelerado. Quizás de la noche a la mañana, pero posiblemente algo más barato pero relativamente rápido.
Exploramos algunos escenarios más mediante simulación. La tabla 1 muestra los resultados. Los escenarios 1 a 4 suponen que llega una demanda adicional sorpresa de 10 unidades el día 3, lo que desencadena un pedido inmediato de reabastecimiento adicional. El tamaño y el plazo de entrega del pedido de reabastecimiento varían.
El escenario 0 muestra que no hacer nada en respuesta a la demanda sorpresa conduce a una tasa de llenado abismal de 41% para ese mes; Lo que no se muestra es que este resultado establece que el próximo mes continuará con un desempeño deficiente. Las operaciones regulares no funcionarán bien. El planificador debe hacer algo para responder a la demanda anómala.
Hacer algo en respuesta implica realizar un pedido de reabastecimiento de emergencia por única vez. El planificador debe elegir el tamaño y el momento de ese pedido. Los escenarios 1 y 3 representan reposiciones “de tamaño medio”. Los escenarios 1 y 2 representan reabastecimientos al día siguiente, mientras que los escenarios 3 y 4 representan una respuesta garantizada en una semana.
Los resultados dejan claro que la respuesta inmediata es más importante que el tamaño de la orden de reabastecimiento para restaurar la tasa de cumplimiento. El reabastecimiento nocturno produce tasas de llenado en el rango 70%, mientras que el tiempo de reabastecimiento de una semana reduce la tasa de llenado al rango medio de 50% a medio 60%.

CONCLUSIONES
El software de gestión de inventario se está expandiendo desde su enfoque tradicional en operaciones normales a un enfoque adicional en operaciones irregulares (IROPS). Esta evolución ha sido posible gracias al desarrollo de nuevos métodos estadísticos para generar escenarios de demanda a nivel diario.
Consideramos una situación IROPS: la llegada sorpresa de una demanda anormalmente grande. Las simulaciones diarias proporcionaron orientación sobre el momento y el tamaño de una orden de reabastecimiento de emergencia. Los resultados de dicho análisis brindan a los planificadores de inventarios un respaldo crítico al estimar los resultados de intervenciones alternativas que les sugiere su experiencia.