Mientras el mundo contiene la respiración para ver cómo se desarrollará el nuevo coronavirus (2019-nCOV), cruzamos los dedos por todos aquellos que actualmente están en cuarentena o bajo tratamiento y rezamos para que las autoridades sanitarias de todo el mundo pronto tomen la delantera. .
Esta breve nota trata sobre una forma en que su empresa puede desarrollar un plan para adaptarse a una de las posibles consecuencias del virus: aumentos repentinos en el tiempo que lleva obtener la reposición de inventario de los proveedores. Las cadenas de suministro en todo el mundo están siendo interrumpidas. Si esto te sucede, ¿cómo puedes reaccionar de manera sistemática?
Reacción a plazos de entrega más largos
Este es un problema que se puede resolver utilizando análisis avanzados de la cadena de suministro. Presumiblemente, es posible que ya haya utilizado esta tecnología para tomar buenas decisiones para los parámetros de control utilizados en la gestión de todos sus artículos de inventario, por ejemplo, valores para Min y Max o Punto de pedido y Cantidad de pedido. La pregunta técnica específica que se aborda aquí es cómo convertir un aumento en el tiempo de reabastecimiento en cambios en esos parámetros de control.
En general, los plazos de entrega más largos requieren inventarios más amplios si desea mantener un alto nivel de servicio al cliente. Esta regla general se traduce en valores mayores de Min y/o Max. Cuánto más grande depende críticamente de qué nuevos valores de tiempo de entrega más largos aparecerán y sus probabilidades de ocurrir.
Si bien muchos sistemas de software de planificación asumen un tiempo de entrega fijo, la realidad es que casi todos los tiempos de entrega tienen cierto grado de aleatoriedad. Por lo general, ignorar que la aleatoriedad aumenta el riesgo de desabastecimiento, por lo que es importante tener una buena estimación de la distribución de probabilidad de los tiempos de entrega. En tiempos normales, sus datos transaccionales se pueden usar para estimar esa relación. Pero las interrupciones repentinas como 2019-nCOV crean situaciones sin precedentes en las que debe hacer conjeturas informadas sobre qué nuevos retrasos verá y qué tan probables son. Supondremos aquí que puede imaginar algunos de estos escenarios y desea descubrir cómo responder mejor a ellos.
Un ejemplo utilizando software avanzado
Para ilustrar este tipo de planificación prospectiva, considere un ejemplo hipotético. Un artículo, una pieza de repuesto, tiene un patrón establecido de plazos de reposición, con retrasos de 5, 10 y 15 días con probabilidades de 15%, 70% y 15%, respectivamente. Dada esta distribución y una demanda aleatoria con un promedio de una unidad cada 5 días, los valores de Min = 5 y Max = 10 hacen un buen trabajo. La Figura 1 muestra una simulación de 10 años de operación diaria bajo este escenario. La tasa de llenado y el nivel de servicio son altos y los desabastecimientos son poco frecuentes.
Ahora suponga que las interrupciones en la cadena de suministro crean una distribución menos favorable del tiempo de entrega, con una combinación 50:50 de 15 y 30 días. La Figura 2 muestra el mal desempeño de los valores actuales de Min y Max en este nuevo escenario. La tasa de llenado y el nivel de servicio se desploman debido a los frecuentes desabastecimientos. Costos operativos más del triple debido a penalizaciones por pedidos atrasados. Solo la inversión en inventario (el valor promedio en dólares de las existencias en el estante) parece mejorar, pero esto sucede solo porque con mucha frecuencia hay pedidos pendientes y no queda nada en el estante. El cambio a plazos de entrega más largos requiere claramente nuevos valores más altos de Min y Max.
La Figura 3 muestra cómo funciona el sistema cuando el Min aumenta de 5 a 10 y el Max de 10 a 15. Este cambio compensa los plazos de entrega más largos, restaurando los altos niveles anteriores de tasa de llenado y nivel de servicio. La inversión en inventario es necesariamente mayor, pero los costos operativos en realidad son más bajos que antes.
Resumen
Los cambios en las condiciones normales de operación requieren ajustes en la forma en que se administran los artículos del inventario. Uno de esos cambios que se avecina en esta fecha es el impacto potencial del virus Corona 2019-nCOV en las cadenas de suministro, con aumentos anticipados en los plazos de reposición.
Los cambios en los plazos de entrega requieren cambios en los parámetros de control de inventario, como Min's y Max's. Estos cambios son difíciles de hacer con confianza utilizando puras conjeturas. Pero con alguna estimación del aumento en los plazos de entrega, puede usar un software avanzado para aprender cómo hacer estos ajustes con cierta confianza.
Esta nota ilustra este punto usando simulaciones de la operación diaria de un sistema de control de inventario.
Figura 1 Simulación de operaciones normales utilizando los plazos de reabastecimiento actuales, mínimo y máximo
Figura 2 Simulación de operaciones anómalas utilizando plazos de entrega más largos y Mín. y Máx. actuales
Figura 3 Simulación de operaciones anormales utilizando plazos de entrega más largos y Min y Max revisados
Artículos Relacionados

Innovando en el mercado de repuestos OEM con optimización de inventario impulsada por IA
El sector de posventa ofrece a los fabricantes de equipos originales una ventaja decisiva al ofrecer un flujo de ingresos constante y fomentar la lealtad del cliente mediante la entrega confiable y oportuna de piezas de repuesto. Sin embargo, la gestión del inventario y la previsión de la demanda en el mercado de posventa está plagada de desafíos, incluidos patrones de demanda impredecibles, amplias gamas de productos y la necesidad de entregas rápidas. Los métodos tradicionales a menudo no son suficientes debido a la complejidad y variabilidad de la demanda en el mercado de posventa. Las últimas tecnologías pueden analizar grandes conjuntos de datos para predecir la demanda futura con mayor precisión y optimizar los niveles de inventario, lo que conduce a un mejor servicio y menores costos.
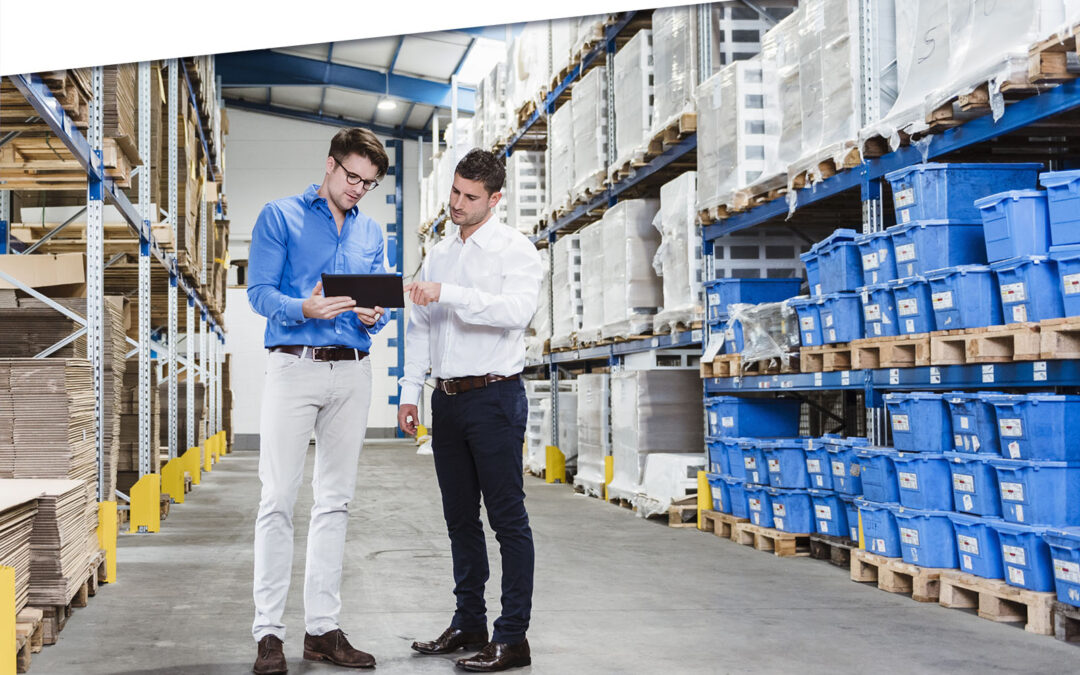
Gestión de inventario basada en pronósticos para una mejor planificación
La gestión de inventario basada en pronósticos, o lógica MRP (planificación de requisitos de materiales), es un método de planificación anticipada que ayuda a las empresas a satisfacer la demanda sin exceso o falta de existencias. Al anticipar la demanda y ajustar los niveles de inventario, mantiene un equilibrio entre satisfacer las necesidades de los clientes y minimizar los costos excesivos de inventario. Este enfoque optimiza las operaciones, reduce el desperdicio y mejora la satisfacción del cliente.
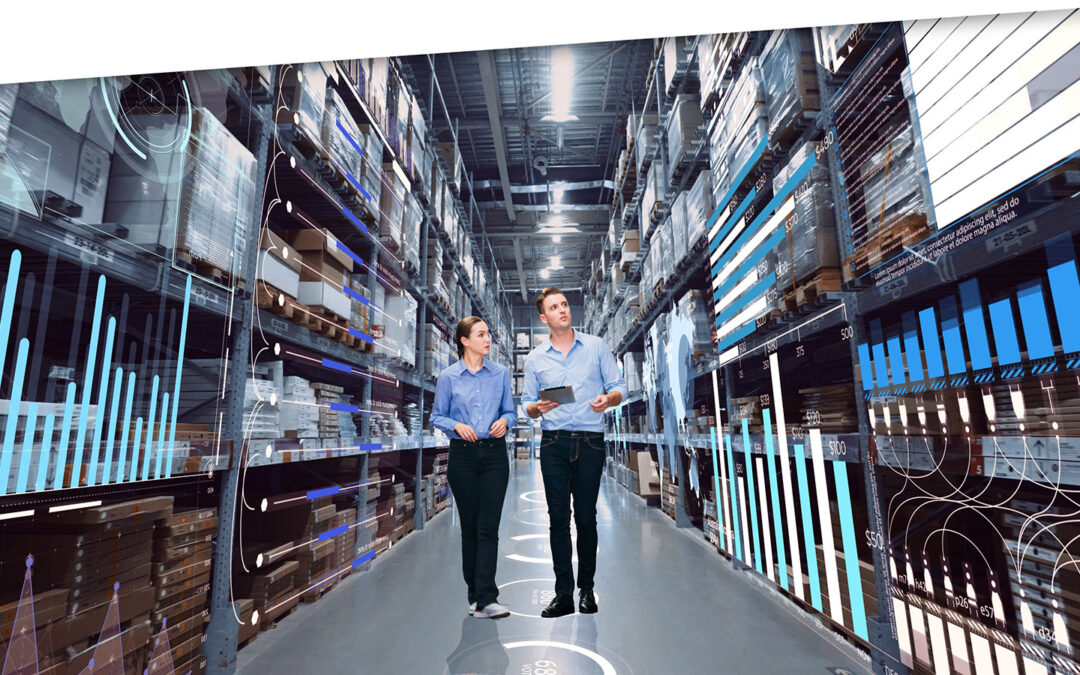
Haga de la optimización de inventario impulsada por IA un aliado para su organización
En este blog, exploraremos cómo las organizaciones pueden lograr una eficiencia y precisión excepcionales con la optimización del inventario impulsada por la IA. Los métodos tradicionales de gestión de inventario a menudo resultan insuficientes debido a su naturaleza reactiva y su dependencia de procesos manuales. Mantener niveles óptimos de inventario es fundamental para satisfacer la demanda de los clientes y minimizar los costos. La introducción de la optimización del inventario impulsada por la IA puede reducir significativamente la carga de los procesos manuales, brindando alivio a los gerentes de la cadena de suministro de tareas tediosas.