¿Se considera el stock de seguridad como repuestos de emergencia o como un amortiguador diario contra picos en la demanda? Conocer la diferencia y configurar su ERP correctamente marcará una gran diferencia en sus resultados.
Él Stock de seguridad campo en tu ERP sistema puede significar cosas muy diferentes dependiendo de la configuración. No comprender estas diferencias y cómo afectan sus resultados es un problema común que hemos visto surgir en las implementaciones de nuestro software.
La implementación del software de optimización de inventario comienza cuando los nuevos clientes completan la implementación técnica para que los datos fluyan. Luego reciben capacitación de usuarios y pasan semanas configurando cuidadosamente sus existencias de seguridad iniciales, niveles de reorden y pronósticos de demanda de consenso con Smart IP&O. El equipo se siente cómodo con las predicciones de rendimiento clave (KPP) de Smart para los niveles de servicio, los costos de pedido y el inventario disponible, todo lo cual se pronostica utilizando las nuevas políticas de almacenamiento.
Pero cuando guardan las políticas y los pronósticos en su sistema de prueba ERP, a veces los pedidos sugeridos son mucho más grandes y más frecuentes de lo que esperaban, lo que aumenta los costos de inventario proyectados.
Cuando esto sucede, el principal culpable es cómo está configurado el ERP para tratar el stock de seguridad. Estar al tanto de estos ajustes de configuración ayudará a los equipos de planificación a establecer mejor las expectativas y lograr los resultados esperados con menos esfuerzo (¡y motivo de alarma!).
Estos son los tres ejemplos comunes de configuraciones de inventario de seguridad de ERP:
Configuración 1. El inventario de seguridad se trata como stock de emergencia que no se puede consumir. Si se pronostica un incumplimiento del stock de seguridad, el sistema ERP forzará una aceleración sin importar el costo para que el inventario disponible nunca caiga por debajo del stock de seguridad, incluso si ya se ha pedido un recibo programado y está programado para llegar pronto.
Configuración 2. El inventario de seguridad se trata como Reserva de estabilización que está diseñado para ser consumido. El sistema ERP colocará un pedido cuando se pronostique un incumplimiento del stock de seguridad, pero se permitirá que el inventario disponible caiga por debajo del stock de seguridad. La reserva de reserva protege contra el desabastecimiento durante el período de reabastecimiento (es decir, el tiempo de entrega).
Configuración 3. El sistema ignora el inventario de seguridad y lo trata como un indicador visual. ayuda de planificación o regla empírica. Los cálculos de planificación de suministro lo ignoran, pero el planificador lo utiliza para ayudar a realizar evaluaciones manuales de cuándo hacer un pedido.
Nota: Nunca recomendamos usar el campo de inventario de seguridad como se describe en la Configuración 3. En la mayoría de los casos, estas configuraciones no fueron intencionadas sino que son el resultado de años de improvisación que han llevado a usar el ERP de una manera no estándar. En general, estos campos se diseñaron para influir mediante programación en los cálculos de reposición. Entonces, el foco de nuestra conversación estará en las Configuraciones 1 y 2.
Los sistemas de optimización de inventario y pronóstico están diseñados para calcular pronósticos que anticiparán la reducción del inventario y luego calcularán las existencias de seguridad suficientes para proteger contra la variabilidad en la demanda y el suministro. Esto significa que el stock de seguridad está destinado a ser utilizado como tampón protector (Configuración 2) y no como emergencia escasa (Configuración 3). También es importante entender que, por diseño, el inventario de seguridad será consumido aproximadamente 50% de la época.
¿Por qué 50%? Porque los pedidos reales superarán un pronóstico imparcial la mitad de las veces. Vea el gráfico a continuación que ilustra esto. Un pronóstico "bueno" debe arrojar el valor que se acercará más al real con mayor frecuencia, de modo que la demanda real sea mayor o menor sin sesgo en ninguna dirección.
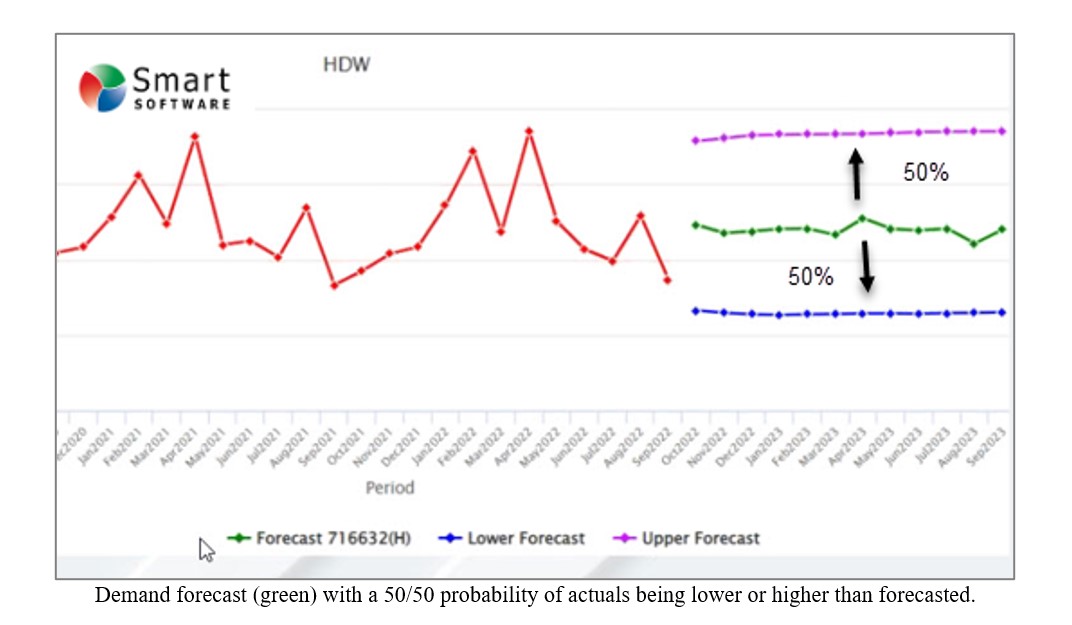
Si configuró su sistema ERP para permitir correctamente el consumo de existencias de seguridad, entonces el inventario disponible podría verse como el gráfico a continuación. Tenga en cuenta que se consume algo de stock de seguridad, pero se evita un desabastecimiento. El nivel de servicio al que se dirige al calcular el stock de seguridad determinará la frecuencia con la que se agota el stock antes de que llegue la orden de reposición. El inventario promedio es de aproximadamente 60 unidades durante el horizonte de tiempo en este escenario.

Si su sistema ERP está configurado para no permita el consumo de existencias de seguridad y trate la cantidad ingresada en el campo de existencias de seguridad más como repuestos de emergencia, ¡entonces tendrá un exceso de existencias masivo! Su inventario disponible se vería como el gráfico a continuación con pedidos acelerados tan pronto como se espera una violación del stock de seguridad. El inventario promedio es de aproximadamente 90 unidades, un aumento de 50% en comparación con cuando permitió que se consumiera el stock de seguridad.
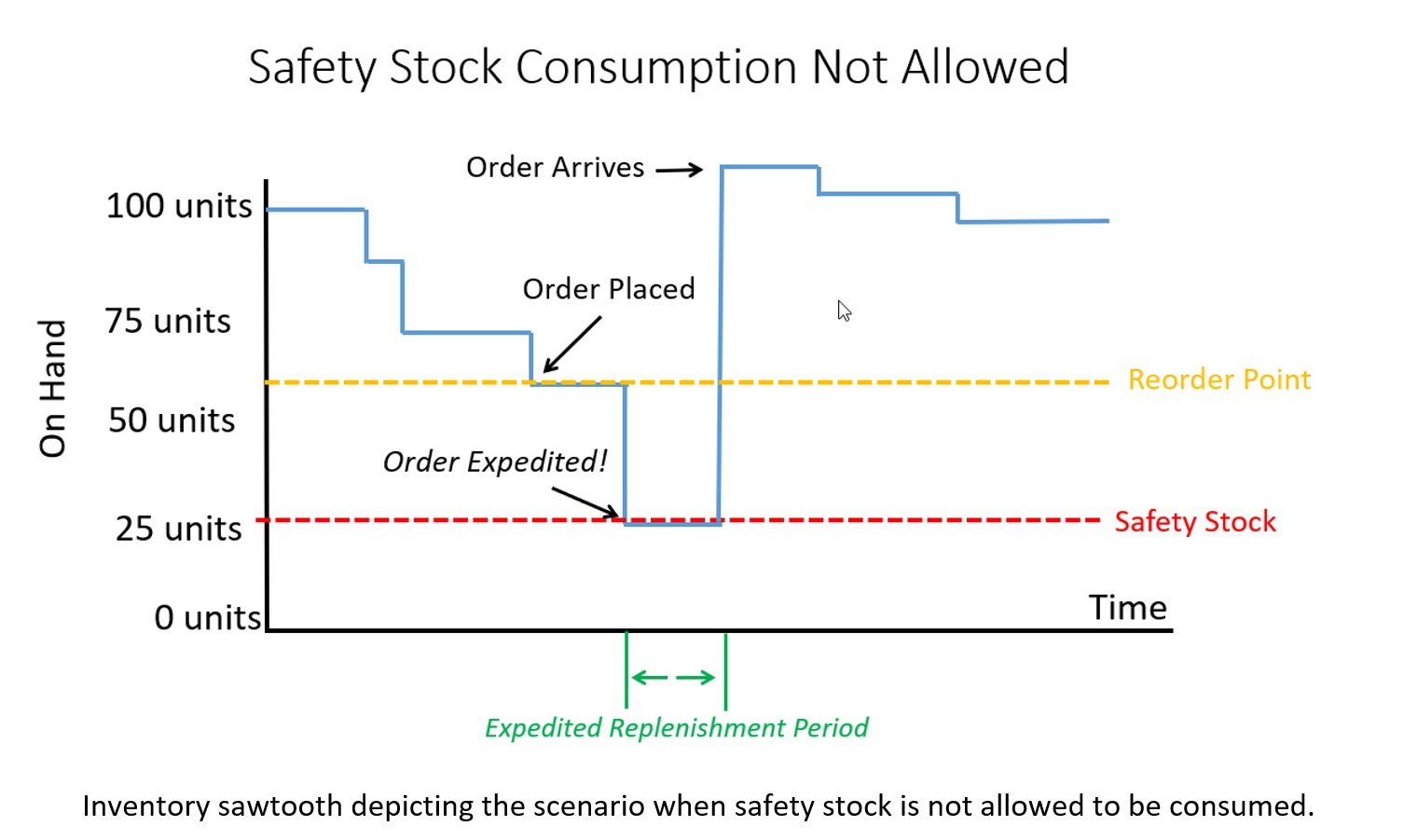