Para la mayoría de los pequeños y medianos fabricantes y distribuidores, la optimización del inventario de un solo nivel o de un solo escalón está a la vanguardia de la práctica logística. La optimización de inventario de niveles múltiples ("MEIO") implica jugar el juego a un nivel aún más alto y, por lo tanto, es mucho menos común. Este blog es el primero de dos. Su objetivo es explicar qué es MEIO, por qué fallan las teorías estándar de MEIO y cómo el modelado probabilístico a través de la simulación de escenarios puede restaurar la realidad del proceso MEIO. El segundo blog mostrará un ejemplo particular.
Definición de optimización de inventario
Un sistema de inventario se basa en un conjunto de opciones de diseño.
La primera opción es la política para responder a los desabastecimientos: ¿simplemente pierde la venta ante un competidor o puede convencer al cliente para que acepte un pedido pendiente? Lo primero es más común con los distribuidores que con los fabricantes, pero esto puede no ser una gran elección ya que los clientes pueden dictar la respuesta.
La segunda opción es la política de inventario. Estas se dividen en políticas de “revisión continua” y “revisión periódica”, con varias opciones dentro de cada tipo. Puede enlazar a un video tutorial que describe varias políticas de inventario comunes aquí. Quizás el más eficiente sea conocido por los profesionales como "Min/Max" y por los académicos como (s, s) o “pequeña S, gran S”. Utilizamos esta política en las siguientes simulaciones de escenarios. Funciona de la siguiente manera: cuando el inventario disponible cae por debajo del mínimo (s), se realiza un pedido de reposición. El tamaño del pedido es la brecha entre el inventario disponible y el Max (S), por lo que si Min es 10, Max es 25 y disponible es 8, es hora de hacer un pedido de 25-8 = 17 unidades.
La tercera opción es decidir sobre los mejores valores de los "parámetros" de la política de inventario, por ejemplo, los valores que se utilizarán para Min y Max. Antes de asignar números a Min y Max, necesita claridad sobre lo que significa "mejor" para usted. Por lo general, lo mejor significa opciones que minimizan los costos operativos de inventario sujetos a un piso en la disponibilidad del artículo, expresado como Nivel de servicio o Tasa de llenado. En términos matemáticos, este es un "problema de optimización de enteros con restricciones bidimensional". "Bidimensional" porque tienes que elegir dos números: Min y Max. "Entero" porque Min y Max tienen que ser números enteros. "Restringido" porque debe elegir valores mínimos y máximos que brinden un nivel lo suficientemente alto de disponibilidad de artículos, como niveles de servicio y tasas de llenado. “Optimización” porque desea llegar allí con el costo operativo más bajo (el costo operativo combina los costos de mantenimiento, pedido y escasez).
Sistemas de inventario de varios niveles
El problema de optimización se vuelve más difícil en sistemas de múltiples escalones. En un sistema de un solo escalón, cada elemento del inventario se puede analizar de forma aislada: un par de valores Mín./Máx. por SKU. Debido a que hay más partes en un sistema de varios niveles, existe un problema computacional mayor.
La Figura 1 muestra un sistema simple de dos niveles para administrar un solo SKU. En el nivel inferior, las demandas llegan a varios almacenes. Cuando están en peligro de agotarse, se reabastecen desde un centro de distribución (DC). Cuando el propio DC está en peligro de agotarse, lo suministra una fuente externa, como el fabricante del artículo.
El problema de diseño aquí es multidimensional: necesitamos valores mínimos y máximos para 4 almacenes y para el CD, por lo que la optimización ocurre en 4×2+1×2=10 dimensiones. El análisis debe tener en cuenta una multitud de factores contextuales:
- El nivel promedio y la volatilidad de la demanda que ingresa a cada almacén.
- El promedio y la variabilidad de los plazos de reabastecimiento del centro de distribución.
- El promedio y la variabilidad de los plazos de reabastecimiento desde la fuente.
- El nivel de servicio mínimo exigido en los almacenes.
- El nivel de servicio mínimo requerido en el CD.
- Los costos de mantenimiento, pedido y escasez en cada almacén.
- Los costos de mantenimiento, pedido y escasez en el centro de distribución.
Como era de esperar, las conjeturas en el asiento de los pantalones no funcionarán bien en esta situación. Tampoco intentar simplificar el problema analizando cada escalón por separado. Por ejemplo, los desabastecimientos en el centro de distribución aumentan el riesgo de desabastecimiento a nivel de almacén y viceversa.
Obviamente, este problema es demasiado complicado para tratar de resolverlo sin la ayuda de algún tipo de modelo informático.
Por qué la teoría del inventario estándar es mala matemática
Con un poco de búsqueda, puede encontrar modelos, artículos de revistas y libros sobre MEIO. Estas son fuentes valiosas de información y conocimiento, incluso números. Pero la mayoría de ellos confían en el recurso de simplificar demasiado el problema para que sea posible escribir y resolver ecuaciones. Esta es la “Fantasía” a la que se refiere el título.
Hacerlo es una maniobra clásica de modelado y no es necesariamente una mala idea. Cuando era estudiante de posgrado en el MIT, me enseñaron el valor de tener dos modelos: un modelo pequeño y aproximado para servir como una especie de visor y un modelo más grande y preciso para producir números confiables. El modelo más pequeño está basado en ecuaciones y teorías; el modelo más grande está basado en procedimientos y datos, es decir, una simulación detallada del sistema. Los modelos basados en teorías y ecuaciones simples pueden producir malas estimaciones numéricas e incluso pasar por alto fenómenos completos. Por el contrario, los modelos basados en procedimientos (p. ej., "pedir hasta el máximo cuando supere el mínimo") y hechos (p. ej., los últimos 3 años de demanda diaria de artículos) requerirán mucha más computación pero darán respuestas más realistas. Afortunadamente, gracias a la nube, tenemos mucha potencia informática al alcance de la mano.
Quizás el mayor "pecado" de modelado en la literatura de MEIO es la suposición de que las demandas en todos los escalones se pueden modelar como procesos de Poisson puramente aleatorios. Incluso si fuera cierto a nivel de almacén, estaría lejos de ser cierto a nivel de CD. El proceso de Poisson es la "rata blanca del modelado de demanda" porque es simple y permite una mayor manipulación de ecuaciones con lápiz y papel. Dado que no todas las demandas tienen forma de Poisson, esto da como resultado recomendaciones poco realistas.
Optimización de simulación basada en escenarios
Para obtener realismo, debemos profundizar en los detalles de cómo funcionan los sistemas de inventario en cada escalón. Con pocos límites, excepto los impuestos por el hardware, como el tamaño de la memoria, los programas de computadora pueden mantener cualquier nivel de complejidad. Por ejemplo, no hay necesidad de suponer que cada uno de los almacenes enfrenta flujos de demanda idénticos o tiene los mismos costos que todos los demás.
Una simulación por computadora funciona de la siguiente manera.
- El historial de demanda del mundo real y el historial de tiempo de entrega se recopilan para cada SKU en cada ubicación.
- Los valores de los parámetros de inventario (p. ej., Min y Max) se seleccionan para la prueba.
- Los historiales de demanda y reposición se utilizan para crear escenarios que representan las entradas al programa de computadora que codifica las reglas de operación del sistema.
- Las entradas se utilizan para impulsar la operación de un modelo informático del sistema con los valores de los parámetros elegidos durante un largo período, digamos un año.
- Los indicadores clave de rendimiento (KPI) se calculan para el año simulado.
- Los pasos 2 a 5 se repiten muchas veces y los resultados se promedian para vincular las opciones de parámetros con el rendimiento del sistema.
-
La optimización del inventario agrega otro "bucle externo" a los cálculos mediante la búsqueda sistemática de los posibles valores de Min y Max. Entre esos pares de parámetros que satisfacen la restricción de disponibilidad de artículos, la búsqueda adicional identifica los valores Mín. y Máx. que dan como resultado el costo operativo más bajo.
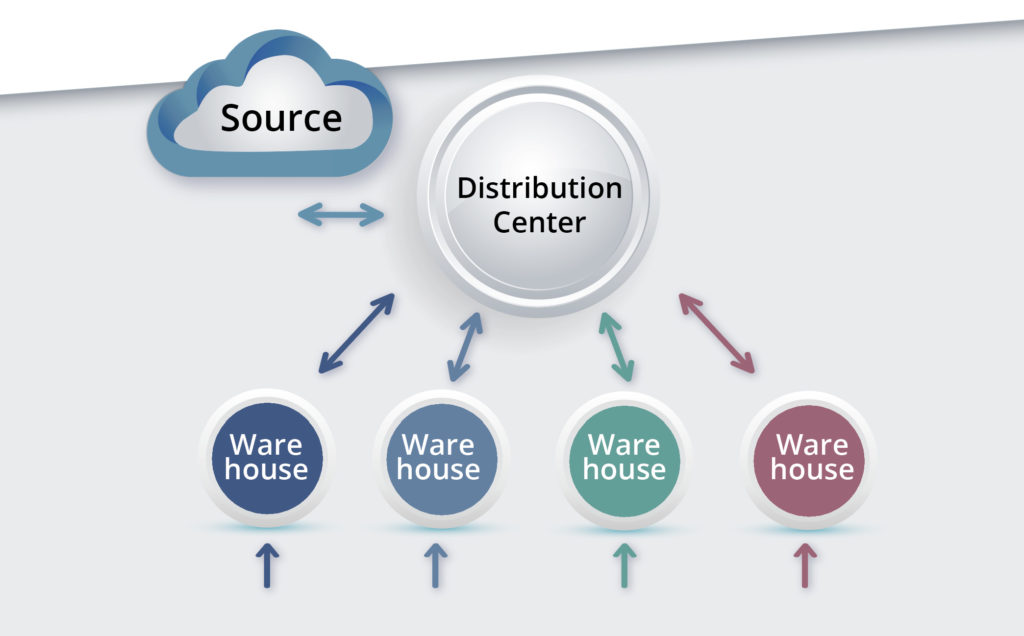
Figura 1: Estructura general de un tipo de sistema de inventario de dos niveles
Estén atentos a nuestro próximo blog
PRÓXIMAMENTE, EN BREVE, PRONTO. Para ver un ejemplo de una simulación del sistema en la Figura 1, lea el segundo blog sobre este tema
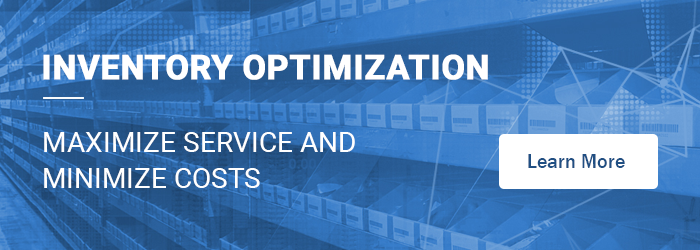